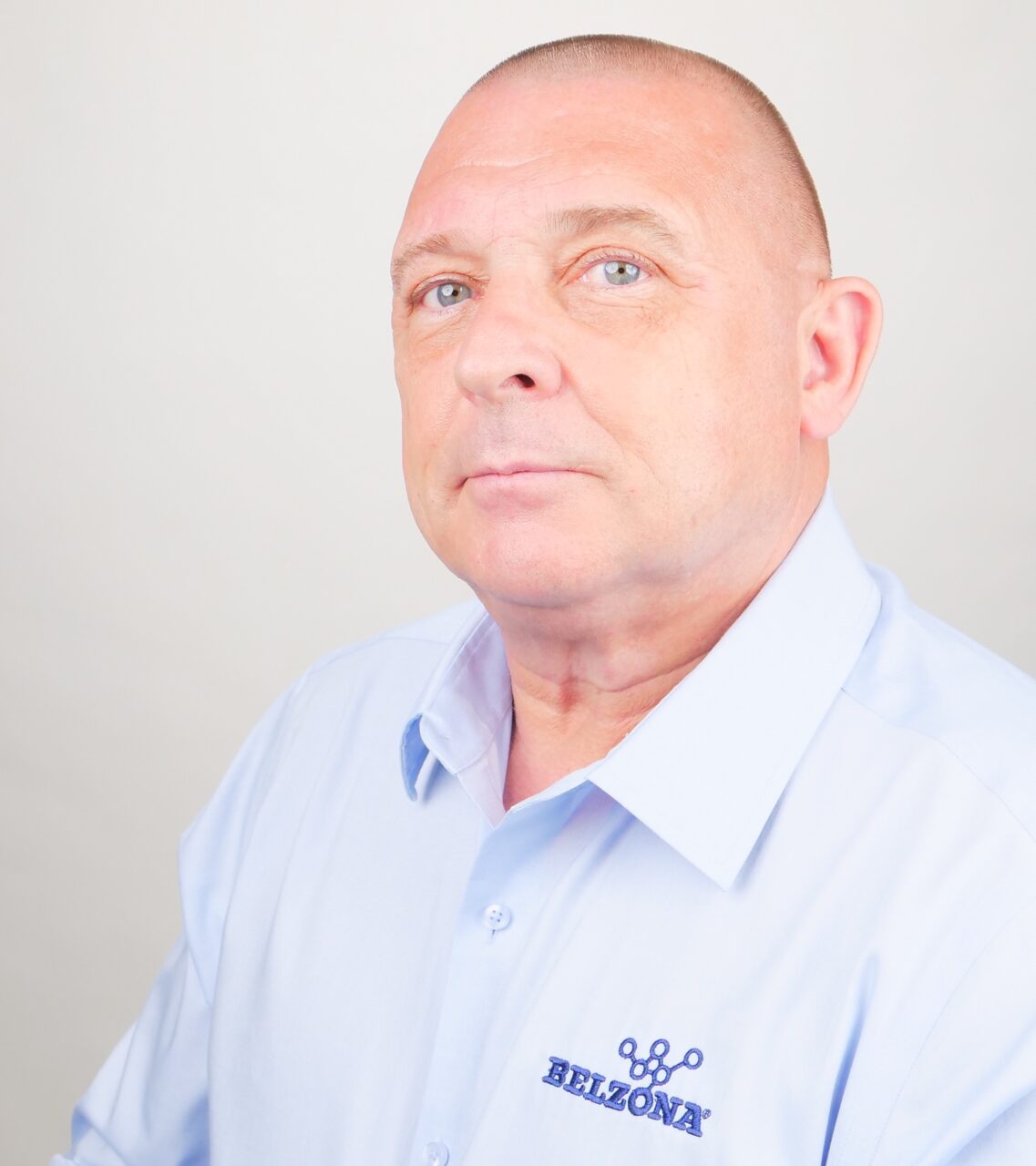
Simon Latty, Senior Technical Services Engineer based in Thailand, first became associated with Belzona in 1979. It has been over forty years since he started his Belzona journey.
Equipped with field experience and product knowledge as well as excellent application techniques, he is one of the trainers for product training sessions at the Belzona Asia Pacific office. Simon also designs and develops exhibition pieces. In addition, he also provides product demonstrations for Belzona’s how-to videos.
Let’s Get to Know Simon
Can you please tell us about how you started your Belzona journey and what tasks are you currently involved in at work on a day-to-day basis?
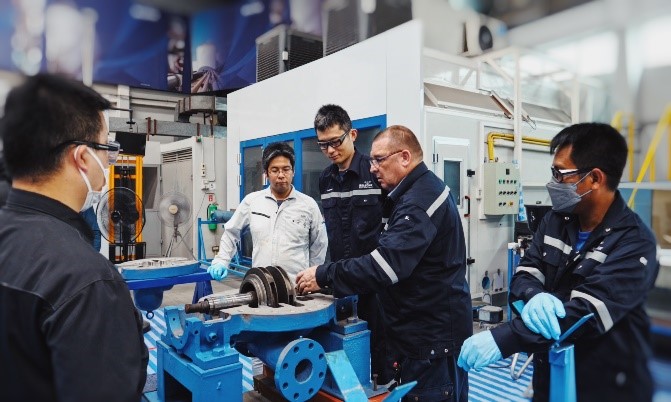
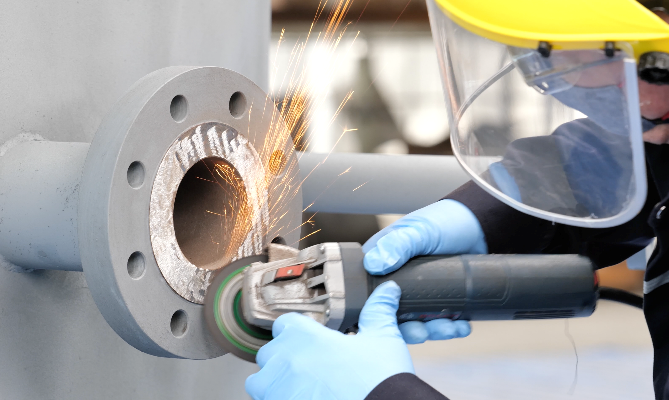
My role has always been in the practical side of things. In fact, my first role at Belzona was making sales aids. Before joining the company, I knew nothing about the industry but the fact that I have always enjoyed fixing and making things helped me settle in very quickly.
In the early 90s, I started to have opportunities in the field supporting our Distributors and Consultants in the UK. I think those opportunities contributed to my sailing through a NACE level 3 certification, the AMPP Senior Certified Coatings Inspector.
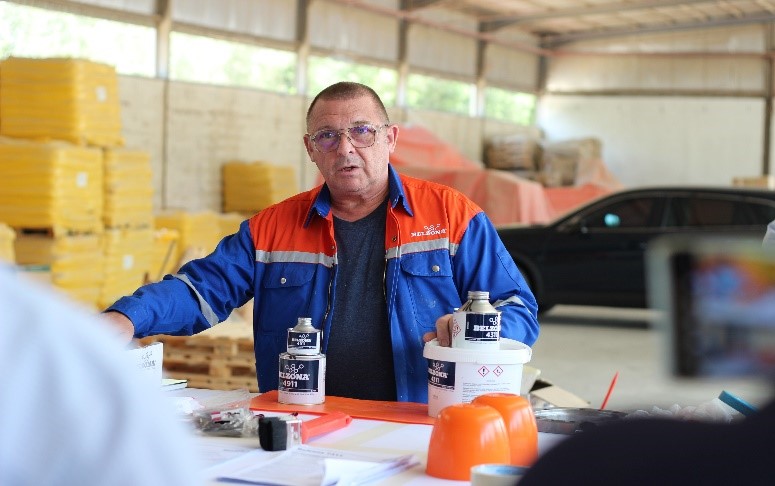
As a Senior Technical Services Engineer, I often lead practical training sessions in our BAP facility. I am heavily involved in producing a range of exhibition pieces that demonstrate the benefits of Belzona solutions. I also spend a considerable amount of time visiting our Distributors and Consultants in Asia, the Pacific, and the Middle East and helping our network with various application projects.
Changes in the Industry
Are there any changes in the industry that you have seen and what impact has this had on your job role?
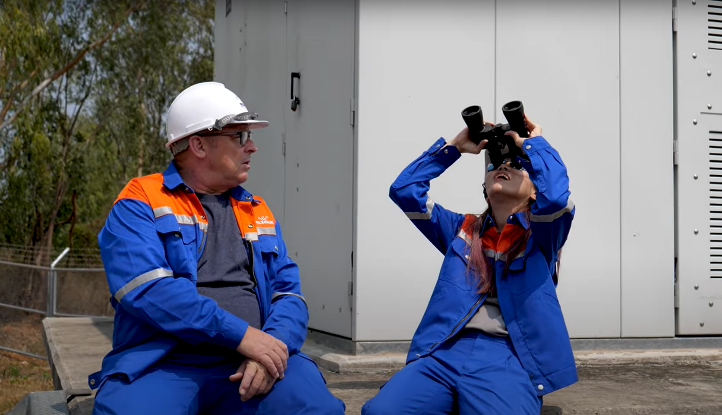
In recent years, to support the shift towards renewable energy, we’ve been targeting industrial maintenance problems within renewable energy industries, such as wind power. As our products are designed to repair equipment rather than replace it, this supports the shift towards renewable energy. For example, I recently had the opportunity to support our customer on-site on a wind farm in Thailand for a leading-edge protection application.
In the Field
Were there any specific projects that you remember and that you can share with us?
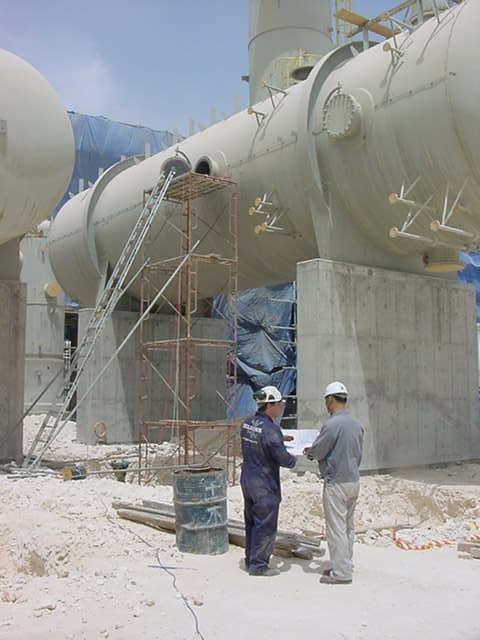
There are so many stories to tell. I still remember those days travelling to Nigeria, Yemen, and Sudan for various different projects. There was one project in the Middle East that many people in Belzona might relate to. It was probably still one of the biggest projects, with well over 100 vessels all lined with Belzona products. As one of the lead engineers in this project, I got to travel to seven different countries within the span of several months.
Another project had me spending three and a half months in South Korea. It was for the application of four metric tonnes of Belzona 1591 into nine huge vessels which were fabricated in South Korea.
After the fabrication, I followed the vessels to an oilfield in the Sirte desert in Libya to observe their installation at the construction site. Those on-site applications were a great experience. I met great people in the field and built a good rapport and I remember that we were always welcomed with generous hospitality.
Put it to the Test!
Are there any testing tools or devices you can introduce to us? How do they help in the testing process?
Since the pandemic, we have constructed a number of test devices in-house. All of them have been built by our fabricators and engineers.
We have built two abrasion testing machines in-house. The first one is an abrasion wheel, which conforms to ASTM standard, ASTM G65. We have so far tested 21 Belzona products from the 1000, 2000, 4000, and 5000 Series.
The other one is an abrasion drum that simulates realistic conditions for testing abrasion-resistant products working in a harsh and wet slurry environment. We have used this equipment to test all of our 1800 series including Belzona 1818 before its first launch.
Countdown to More Findings
We have built our own three-channel atlas cell driver. This is a long-term cold wall effect simulator. We have run an initial commissioning test to confirm everything works as expected. We are looking forward to more testing and working with the Research and Development Department (R&D) to validate the capability of the device.
Solutions in Action
Are there any specific initiatives or projects that the Company is currently focusing on?
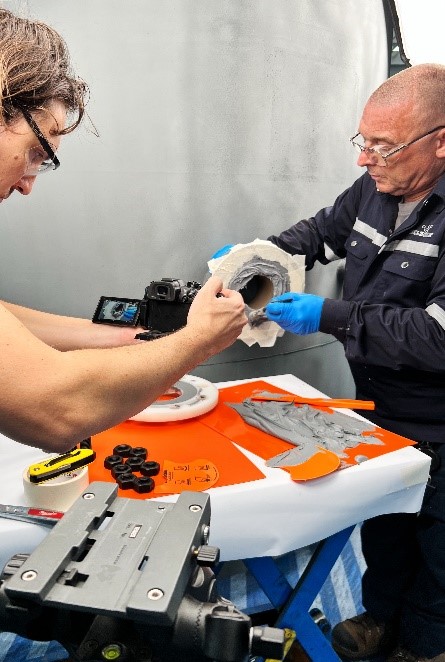
We are lucky enough to have the resources to do things on a bigger scale, not restricted to benchtops or small-footprint rigs. We have the benefit of significant space in our state-of-the-art facility where we can recreate realistic working environments. This has been an advantage when producing the growing series of how-to videos.
In recent months, we have been busy producing those videos, some new, some to replace outdated videos. With the resources we have, and the skill set of our staff, we are able to show the audience how the products and applications work in a lifelike environment, closer to the real work environment. These videos are fun to make, and we have received some very good feedback from YouTube viewers—I am looking forward to doing more of those !
Interested in a Career at Belzona?
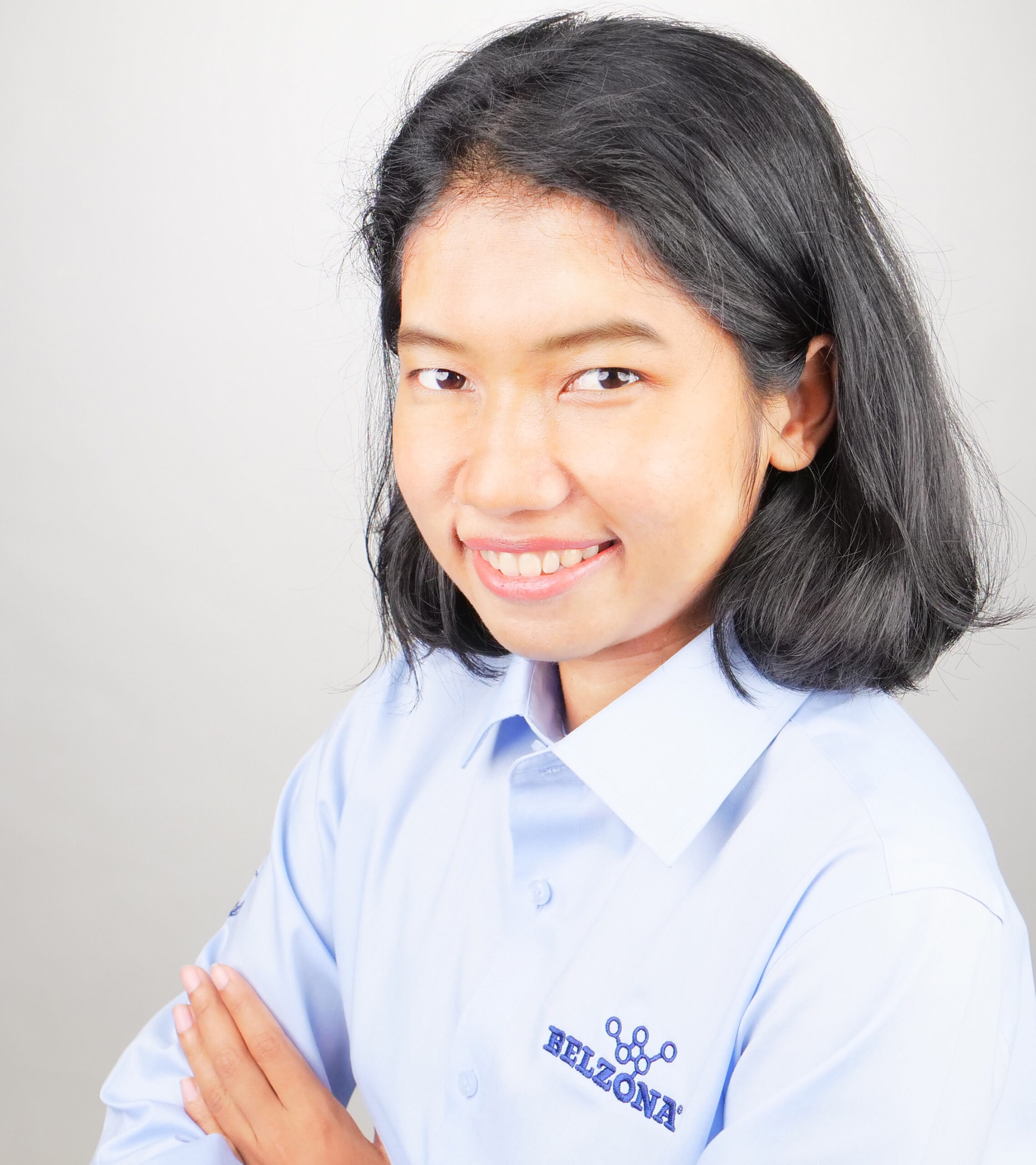
Marketing and Distributor Support Coordinator at Belzona Limited, based in Bangkok, Thailand