Often, the idea of static charge conjures innocent memories of rubbing balloons and hair standing on end. However, in an industrial setting, static charge is regarded far less fondly. In fact, unwanted static charge can be extremely hazardous, leading to potentially life-threatening incidents in environments involving chemical containment, or the presence of highly flammable materials. This Blog post aims to shed light on this industry hazard, by looking at the generation and control of static electricity, including the theory behind static dissipative technology available to industry e.g. Belzona 4351.
Generation of static charge
It can sometimes be the hidden dangers that pose the most significant challenge. This is particularly true in relation to the common processes associated with chemical storage and containment areas, including pumping and pouring, all of which cause movement of chemical products and liquids. The flow of product against other materials and surfaces can easily generate friction and consequently can lead to the generation of static electric charge. Defined as an electric charge that has built up on an insulated body, static electricity is a major industry hazard, with the potential to cause fires and explosions. There are numerous chemical containment examples, as well as general industry cases, where static electricity igniting fluid or dust has been the root cause of serious incidents. According to the National Fire Protection Association and the UK’s Institution of Chemical Engineers, static electricity is the prime culprit for at least two serious fires or explosions in industry worldwide every day of the year. Therefore, plant operators are responsible for excluding the risk of explosions, whether that is through avoiding explosive mixtures or eliminating the chances of static charge as an ignition source.
There are three conditions that must be in place for static electricity to become a hazard and potentially cause a fire or explosion:
Safety conditions and regulations aim to eliminate, or at the very least safeguard against, one or more of these elements; however, there are some that can be controlled more easily than others. Treating the flammable material as a constant, that therefore determines controlling the accumulation of static electricity as the essential goal.
Dissipating the threat
As highlighted earlier, friction between two materials causes a transfer of energy. This is known as triboelectric charge, a term given to the transfer of charge to a certain material after coming into contact with another material. This can occur when fluid is flowing or agitated, separating positive and negative charges, which can accumulate in the fluid or on the surface of chemical containment areas such as bunds and fuel tanks. Worryingly, a spark of 0.25 millijoules provides sufficient energy to ignite most flammable vapours with potentially catastrophic consequences and a brush discharge in lined equipment can have energy of 2,000 millijoules. Grounding or earthing areas that are susceptible to the hazardous build-up of static charge is commonplace; however, this does not always eliminate the problem. Often there are still further measurements that must be taken, in terms of the health and safety and industry standards; this can include adding a static dissipative coating.
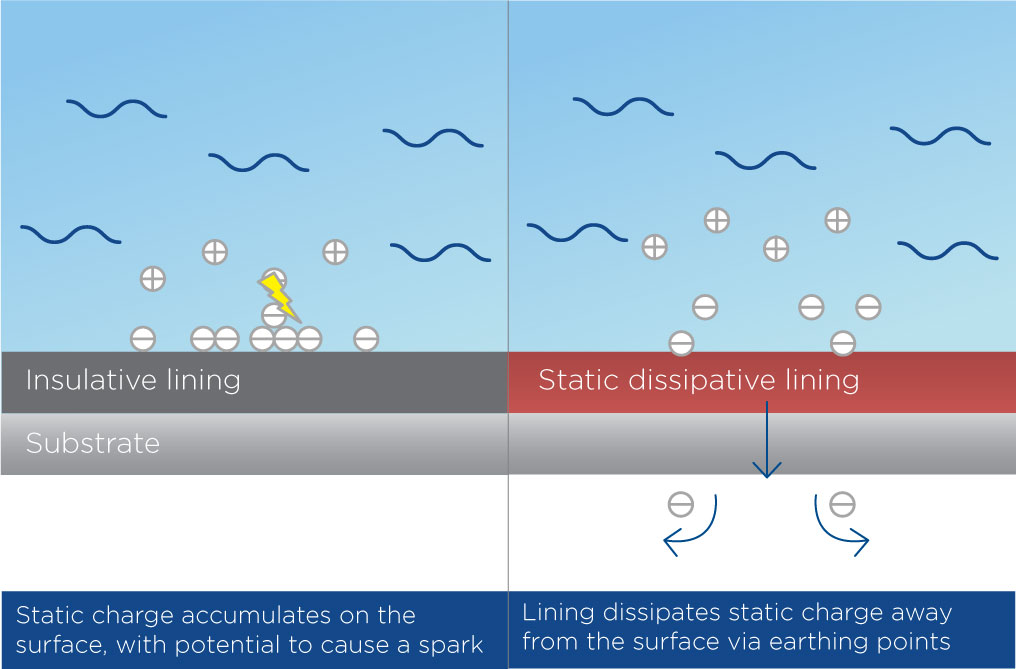
Static dissipative coatings, as their name suggests, stop static charge from accumulating on the material’s surface and instead dissipate this charge away to the grounding point. Importantly, static dissipative should not be misinterpreted for anti-static, terminology that is quite often misused. So, what is the difference between an anti-static and static dissipative coating? Significantly, the difference is attributed to the coating’s resistivity and as you can see from Figure 1, it is possible to measure the flow of current across the surface of any material. At one end of the scale there are metals which have the lowest surface resistivity of all materials due to their highly conductive nature and measure between 10-1 and 10-5 Ohm per square. Conversely, there are insulating materials, including plastics, which measure at 1012 Ohm per square and above. Many plastics are used as insulative coatings, including bund coatings; however, they still do not alleviate any potential build-up of static charge. Evidently, static dissipative (106 to 1012) and anti-static materials (1010 to 1012) differ in their levels of surface resistivity, yet they do have a crossover along the spectrum. Both antistatic and static dissipative materials will reduce the risk of generating a spark, yet only the latter can dissipate any accumulated charge.
Extinguishing the spark
Static dissipative solutions ideally lend themselves to agitated fluids, commonly associated with fluid processes, such as pumping and piping and filtration systems, linked to fuel storage tanks and chemical containment areas. Yet, static charge can develop in many different environments, some of which don’t contain any fluids. Application scenarios can vary to include refineries and grain silos, where dust particles are highly susceptible to ignition from static charge accumulation.
A note of significance in all environments is that static dissipative linings work in conjunction with the mandatory safety guidelines of grounding all equipment and is not a replacement for these existing precautions. Simply, it can dissipate the static charge away from the surface via earthing points located either in the substrate itself or connected to an external area.
For more information on Belzona’s static dissipative solutions, visit: http://www.belzona.com/en/products/4000/4351.aspx