Please find below the recording and transcript of the Belzona webinar “Cold Applied Solutions for Storage Tanks” first recorded on the 15th of July, 2019.
Cold Applied Solutions for Storage Tanks Webinar Recording
This blog post will be covering some of the areas where tanks typically experience damage and deterioration, and how you can use different solutions to repair, protect and improve them. Including:
- Tank base sealing
- Nozzles and flanges
- Cold bonding methods
- Internal linings for storage tanks
Tank Base Sealing
Common problems and different solutions to repair them
Frequent problems and their conventional solutions
Some of the key common problems areas with tank bases are: corrosion of the tank wall and chine angle, deterioration of the seal and also corrosion of the tank base.
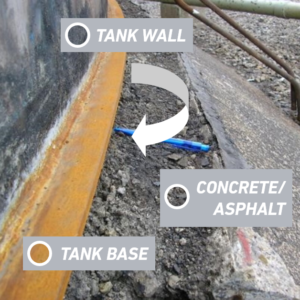
Illustrated here is a steel tank wall and concrete base, which has deteriorated and broken up over time. Now water will no longer flow away from the chine angle, it instead sits here at the interface. The tank naturally expands and contracts, drawing water in at this joint by capillary action. This then causes further corrosion at the base of the tank.
Mastics and bitumen can degrade easily due to UV exposure and, as the tank naturally moves, they crack and lose their seal.Bonded rubber rapidly degrades from the effects of UV and weathering, leading to costly, regular replacement of this system.
To solve these common problems, three of the most conventional repair methods include:
Bitumen and Mastics
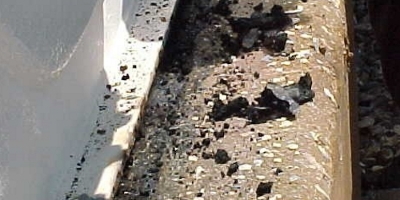
Mastics and bitumen can degrade easily due to UV exposure and, as the tank naturally moves, they crack and lose their seal.
Steel Skirting
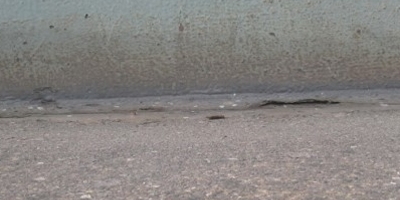
Steel skirting installation involves hot work and if the newly welded steel isn’t protected, over time it will start to corrode again.
Bonded Rubber
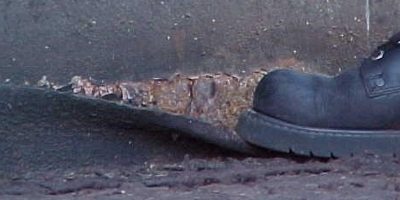
Bonded rubber rapidly degrades from the effects of UV and weathering, leading to costly, regular replacement of this system.
Belzona Solutions
Belzona’s flexible and microporous solutions adhere to both concrete and steel substrates, offering corrosion protection at the base of the tank. As they can be applied in service there is no need to drain the tank prior to carrying out the applications.
The breathable systems stop water from entering, at the same time allowing any trapped vapours/moisture to escape, which in turn prevents corrosion from occurring underneath the tank.
Can be applied in service
Easy and safe installation
Breathable system
How to use Belzona materials to seal a tank base
Case studies from around the world
1. Refinery, France
- Existing system failed due to poor flexibility
- Inspection of the annular ring using NDT methods
- Inspected 13 years after application, still in perfect condition
This Belzona system was originally installed over thirteen years ago and is still in service.
The problem initially was due to movement in the tank, causing the previous system to crack due to it’s rigidity. A flexible, membrane-based solution was applied, which follows the expansion and contraction of the tank.
An added benefit of the membrane is being able to inspect the thickness of the steel ring via Non-Destructive Testing methods through the flexible membrane. This, and the longevity of the application has left the refinery very satisfied with the Belzona solution.
2. Petrochemical Plant, UK
- Over the years the sand base had compressed, to such an extent that the annular ring was now 10mm below the concrete plinth
- Positive inspection after 7 years of Belzona application
- Confident customer sealed 50 tank bases
Click here to view the full case study
Showing above is a very standard example of a Belzona system, which was applied to the base of a fuel storage tank. The structure of the base had moved over time, leaving the annular ring needing added protection. After seven years of applying the Belzona solution the base was inspected and was still in perfect condition. The customer was very satisfied and approximately fifty tanks within the plant have now been coated.
One of the many benefits of this system is that the light colours allow continuous monitoring of the tank base, ensuring no corrosion is present.
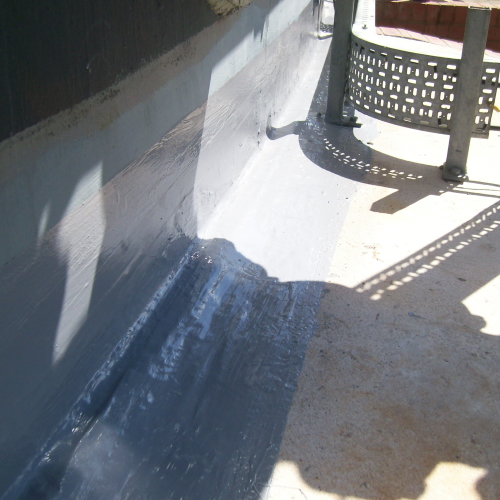
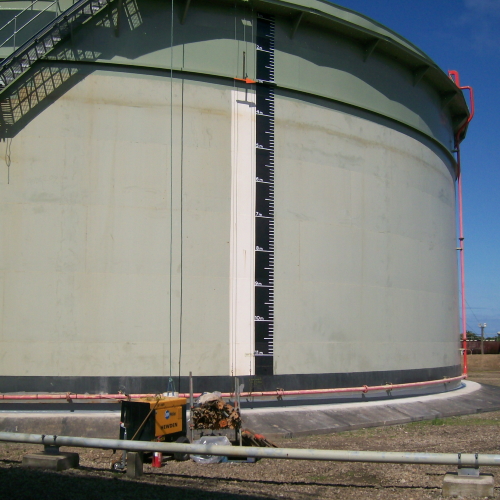
Belzona materials used:
3. Petroleum Company, China
- Original base cracked due to moisture penetration
- 40 tanks repaired over two years
- Customer so happy with the results, specified for global standard
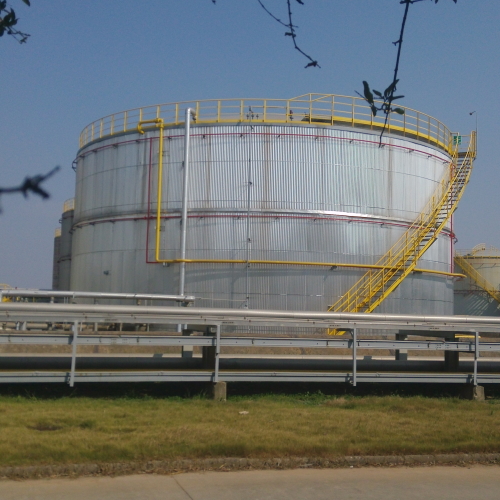
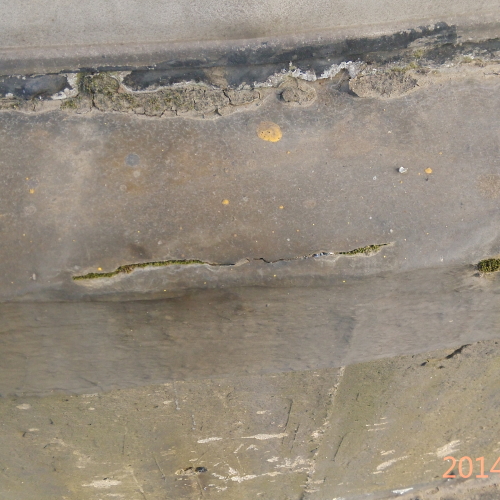
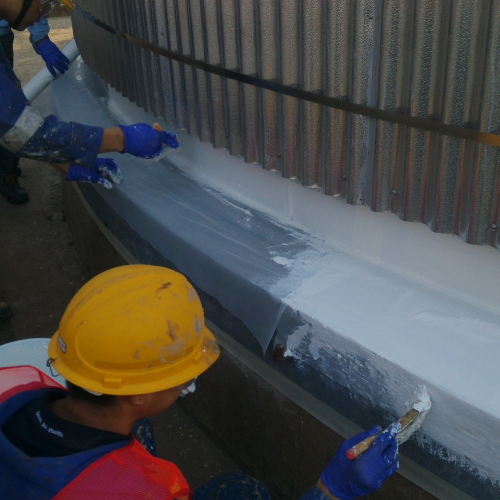
Click here to view the full case study
This case study took place at a petroleum plant in China. The problem here was moisture penetration at the base of their tanks, once again, resulting in cracking.
For this company, the priority was that the repair material must resist water, weather and fire, all of which Belzona could provide with just one product.
After the application, the customer was very happy with the results. Over the course of two years they ended up using this material on all fourty tanks across their site and also specified the solution into the company’s global standards.
Belzona materials used:
Small Bore Nozzles & Flange Face Forming
Common problems and different solutions to repair them
Typical problems and conventional repair methods
The main problem with flange faces within industry is corrosion on the flange face. This can be caused by several factors. One of the main causes being galvanic corrosion, which is when we have two dissimilar metals in contact with one another. Crevice corrosion, steam cuts and chemical attack are the other common types of attack we see.
Conventional repair methods include welding and then cutting back the flange face. However, unless machined, it can be very tricky to achieve a gramophone finish. Another common method is to cut and replace the flange. Both of these methods include hot work and therefore present the associated health and safety risks involved when welding.
Belzona Flange Face Forming
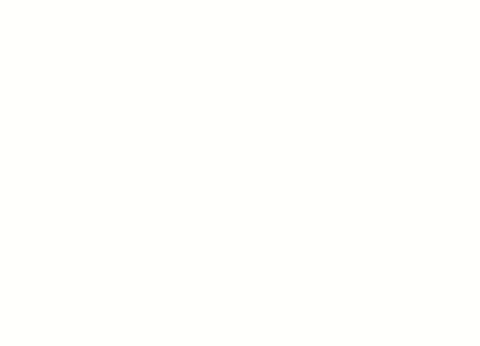
So, how does Belzona flange face forming work? It is a cold applied solution which uses a paste material to re-create the sealing face, using a mould designed to replicate the original dimensions of the flange face.
Belzona solutions for flange face forming are 100% epoxies and contain no solvents, meaning the exact dimension can be formed. They are also electrical insulators, eliminating any metal-to-metal contact and the risk of galvanic corrosion.
Exact dimensions can be formed without machining
In-situ repair method
Cold repair solution
Electrical insulator
Small Bore Nozzles
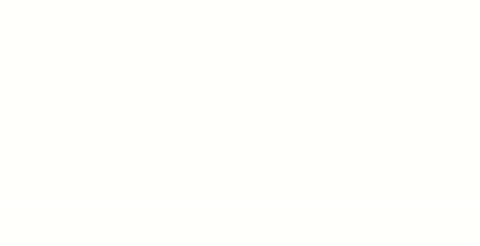
Belzona solutions ensure 100% coverage of the protective coating. A prefabricated section of pipe, made from a suitable polymeric material, is bonded in place using an adhesive, which will offer an optimum long-term protection for corrosion, erosion and chemical attack.
Eliminates the risk of pinholes
Long-term protection
Provides excellent chemical and corrosion resistance
Nozzle inserts and flange face forming techniques are not just limited to damaged equipment. Both systems combined can also be implemented as part of the design for newly fabricated vessels. These Belzona solutions have been used with carbon steel instead of solid Corrosion Resistant Alloys (CRA) for the nozzle or weld overlay for the flange faces.
Case studies from around the world
4. Chemical Manufacturer, Spain
- Nozzle interior was damaged
- Belzona solution was chosen as a faster repair than relining with an ebonite coating
- In situ repair performed
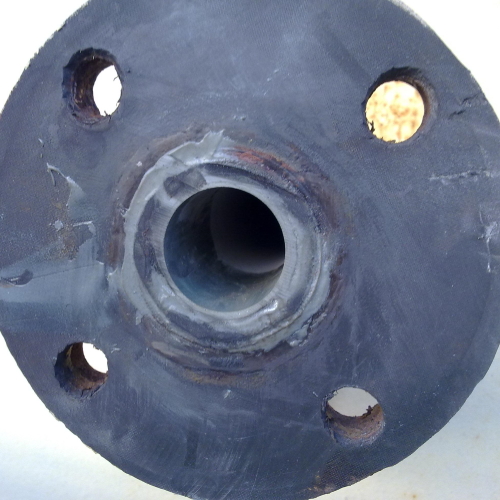
This case study took place at a chemical manufacturer in Spain. The interior of an ebonite lined nozzle, handling 26% hydrochloric acid, had suffered damage from the acid and needed a replacement. A Belzona nozzle insert was used to offer excellent chemical resistance and long term corrosion protection. In addition, the application allowed a rapid return to service which could be applied in-situ. The Belzona solution also proved to be a more cost effective solution than relining the nozzle with ebonite.
Belzona materials used:
Cold Bonding
How to use polymeric materials in lieu of welding
Welding
To add strength back into the structure of a substrate, welding a plate onto a defect area is a common repair method. It provides a strong bond and is a very well-established method. However, before a tank can be welded it must be drained, which means lengthy downtime and a loss of resources
Welding creates a heat affected zone, introducing heat stresses into the metal. This can result in further problems, such as cracking in the future and as always, hot work holds certain health and safety risks.
A further downside to welding is that there are fewer points of contact, which leaves a void between the plate and the wall. If there was a through-wall leak, this gap would fill up with fluid, making the plate susceptible to crevice corrosion.
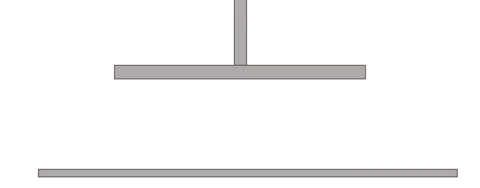
Cold Bonding
Belzona solutions offer 100% contact with the substrate, allowing an excellent load distribution. Plus, being non-metallic, these polymeric solutions act as electrical insulators, eliminating any potential for galvanic corrosion, therefore offering long term corrosion protection.
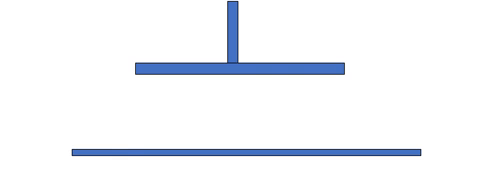
Cold bonding solutions include:
- Metallic plate bonding – has been successfully used for over 20 years as a repair method
- Composite plates – have been used to offer a non-metallic solution in recent years
Using Belzona solutions requires no downtime as no hot work is needed and therefore the tank does not need draining.
Cold bonding techniques can also be used to repair thin-and-through-wall defects, extending the structure and equipment beyond its original design life.
Get a better idea of how cold bonding compares to welding, by checking out the below video, where we put this to the test.
How to Bond Metal Brackets to a Metal Tank Without Welding
Case studies from around the world
5. Refinery, China
- ATEX rated zone restricted hot work
- No tank cleaning necessary
- Belzona system used for over 200 tanks
This case study was prompted by a legislation change in China, meaning VOC treatment was to be implemented on all oil tanks across the country. This required the customer to attach pipe rigs to the tank wall. With hot work restricted within the tank farm, a cold bonding application was necessary, Belzona offering the ideal solution for this problem.
At the start of this application vapour blasting was used to prepare the surface. This was necessary, as grit blasting was not allowed in this ATEX rated zone. The applications were a big success and the customer was so happy with the result, after the first applications for 18 tanks, the system was used for more than 200 tanks around the region.
KHIA CASE STUDY: COLD BONDING PIPE SUPPORTS WITH BELZONA
Belzona materials used:
6. Tank Farm, The Netherlands
- Hot work and grit blasting restricted
- Solution needed for bonding new water sprinkling and foaming systems
- Over 1000 brackets/supports were bonded over 8 tanks with Belzona method
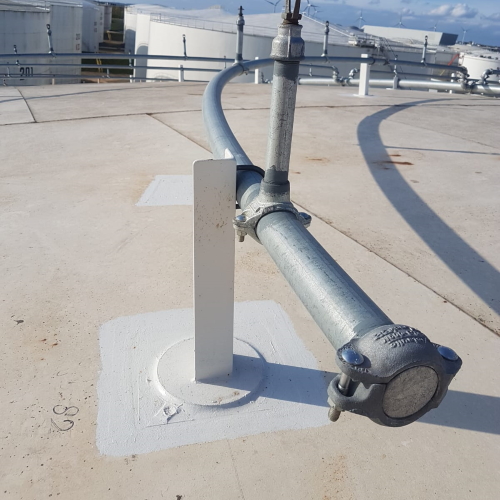
Click here to view the full case study Here is a similar case study in the Netherlands, showing that cold bonding can be used for plates and much more!
The company wanted to bond a water sprinkling and foaming system on top of their oil tanks. Again, hot work and grit blasting were banned on site.
To apply the Belzona application the substrate was prepared with a dust free blasting system to achieve the right surface roughness without generating dust and any potential fire hazards near the oil. Over 1000 brackets and supports were bonded onto the sides and tops of 8 different storage tanks, leaving another satisfied customer.
Belzona material used:
Protection for the floor and bottom section of a tank.
A common problem with storage tanks is corrosion on the internal surface of the tank. Generally, the only areas affected by the corrosion are the tank floor and 1-2 metres (3-6ft) up the side of the tank wall.
This is caused by the mixture of water and hydrocarbons in the tank which, as the density of the water is higher than the hydrocarbons, leaves the water sitting at the bottom of the tank, which is where the corrosion occurs.
Having identified the problem and reasoning behind it, we can look at the range of solutions Belzona can offer to protect the tanks:
- Paste grades can be used for pit filling
- Plate bonding methods can be used for larger areas
- Once the structure of the tank has been restored, the tank can be coated with the most suited lining based on the operating parameters
The lining will be able to offer corrosion resistance in immersion, steam out resistance and also chemical resistance.
7. Oil Company, Tunisia
- Only the bottom section of the tank needed protection
- Welding wasn’t an option
- Cold bonding, pit filling and Belzona internal coating applied
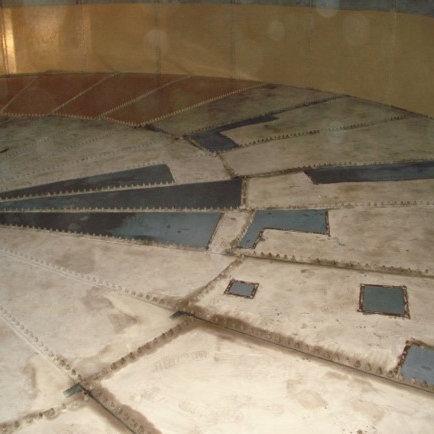
An oil company in Tunisia were experiencing severe pitting at the bottom of their storage tank. As it was a rivet tank, welding wasn’t an option otherwise the rivets would pop off. The Belzona solution here was to pit fill the smaller localised pitting and use plate bonding for the larger areas. The tank was then coated with a Belzona lining which was selected based off the operating parameters of the tank. As the corrosion was due to a mixture of water and hydrocarbons, only the floor and lower section of the tank wall were coated.
Belzona material used:
Additional Links
Want to learn more about Belzona and our solutions?
Totally agree—cold storage breakdowns are more than just an inconvenience. Whether it’s for food, medicine, or other perishables, cold storage repair should be a priority for anyone relying on consistent temps. A good repair tech is worth their weight in gold