An epoxy repair mortar was used to repair the damaged concrete substrate in a clarifier tank at a wastewater Plant in the UK. The system achieved a complete cure despite being completely submerged in water due to a rainstorm during the curing period. In this way, the concrete resurfacing epoxy, Belzona 4131 (Magma-Screed), was an excellent alternative to concrete. It enabled the Customer to bypass the serious problems that would otherwise have arisen had poured concrete been used in the application instead of the epoxy mortar.
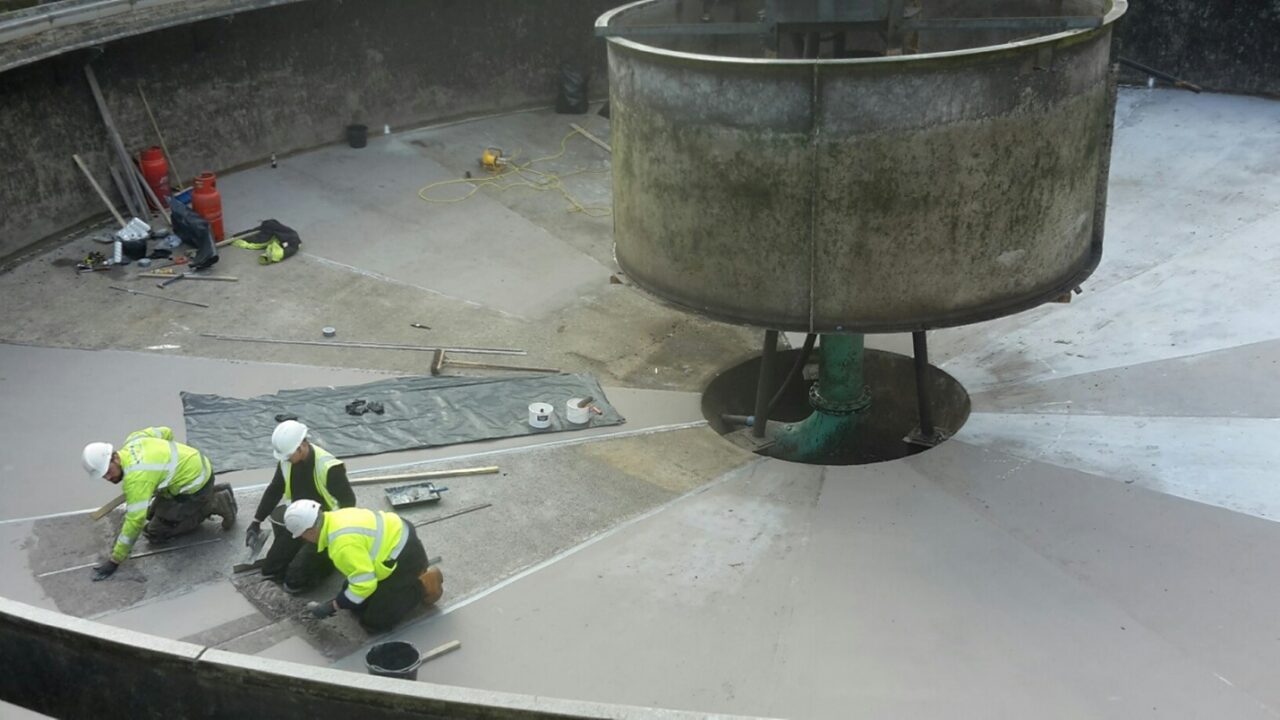
Severely Damaged Concrete in Need of Repair
The clarifier tank, 18 metres (59 ft) in diameter, was suffering from severe deterioration on the concrete base. This had been caused by the combined effects of corrosion and abrasion from the scrapers that run around the clarifier, moving sludge to the centre of the tank. The damaged concrete in the tank had led to a loss of efficiency of the scrapers and premature wear of the rubber scraper pads.
In addition, this had caused the pumps operating downstream to become damaged by the pieces of the broken concrete which had been sucked downstream with the sludge. Repouring concrete onto the base of the tank was considered as a repair solution. However, this was deemed inappropriate as the bond to the original concrete would be insufficient.
Specification of Epoxy Repair Mortar, Belzona 4131 (Magma-Screed)
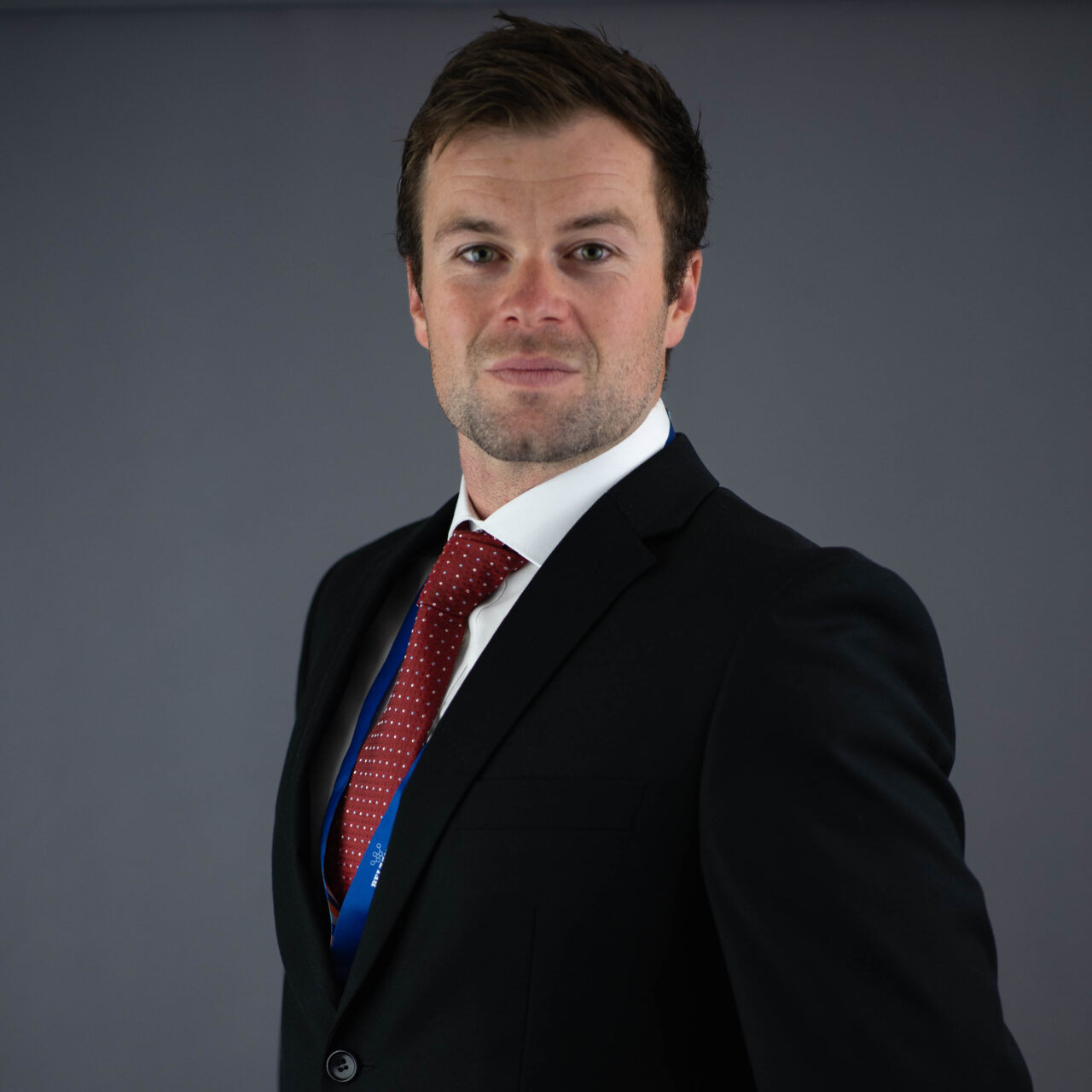
Following an inspection by Douglas Potts, Senior Fields Solutions Engineer at Belzona UK, the epoxy repair mortar, Belzona 4131 (Magma-Screed), along with Belzona 4911 (Magma TX Conditioner), were specified. Belzona 4131 (Magma-Screed) was selected due to its excellent mechanical properties as well as its abrasion resistance capabilities. In addition, as this system can be fully cured in just three days in temperatures of 15°C (59°F), this makes it an excellent alternative to concrete which concrete typically takes around 28 days to achieve a full cure.
To accompany this specification, case studies and test data were supplied demonstrating the strength and adhesion capabilities of Belzona 4131 (Magma-Screed) to concrete. This, along with the fact that the Customer had used Belzona technology in successful applications before, further cemented their decision to opt for the polymeric technology.
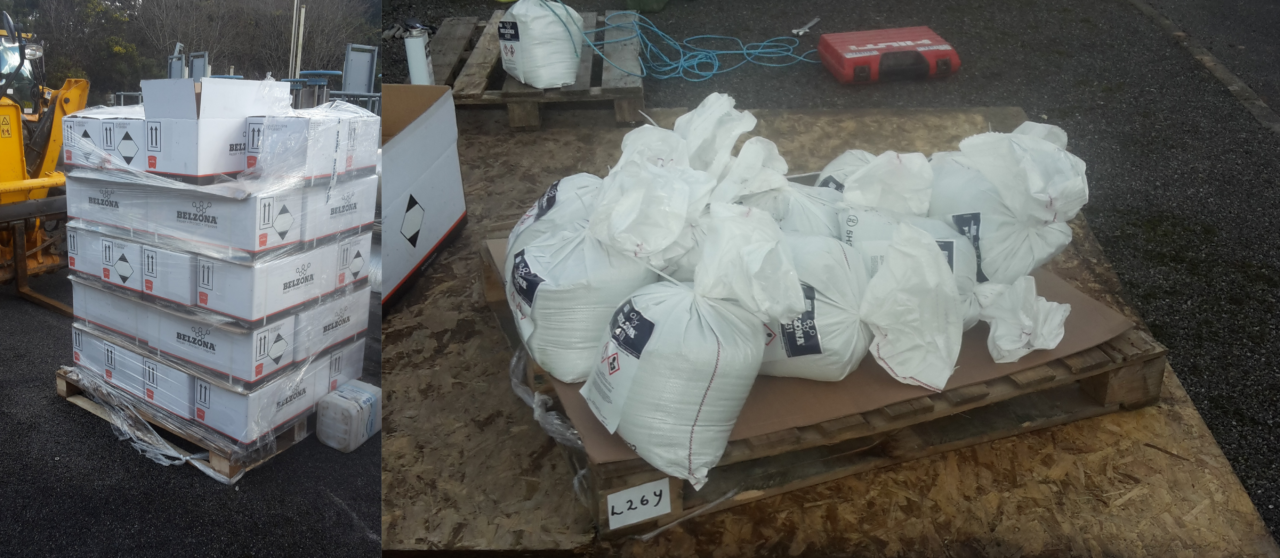
Application of Concrete Resurfacing Epoxy
Firstly, the surface was power washed, and mechanically prepared using grinders and scabblers. Next, the clarifier was marked into sections and each section was then conditioned with Belzona 4911 (Magma TX Conditioner), using a stiff bristled brush. Screed rails were then used to set the level of the Belzona 4131 (Magma-Screed). 4,500 kg (9920.8 lbs) of Belzona 4131 (Magma-Screed) was then applied using metal floats to a thickness of 6mm (0.24 in).
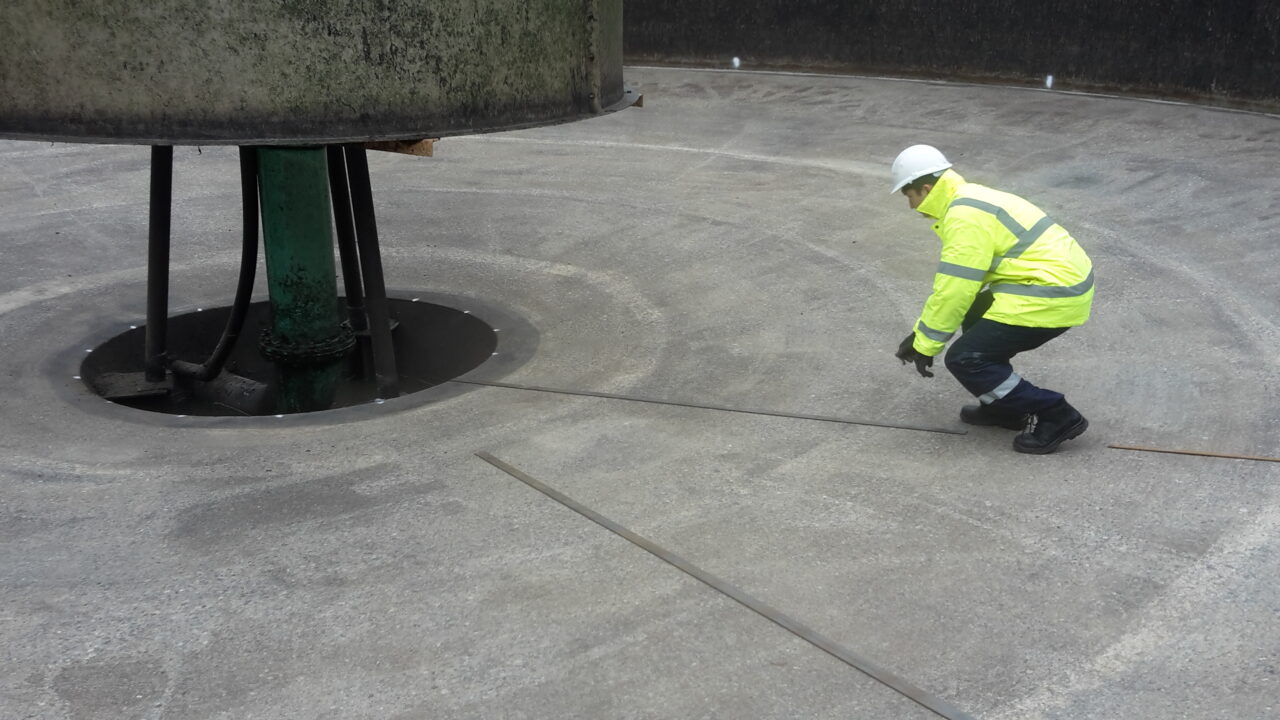
During the curing process, a rainstorm hit the site and the tank was submerged in water. After the storm, the tank was drained and destructive testing was conducted, with support from Belzona Limited’s Research and Development Team, on the patch most recently laid. Other than slight cosmetic damage of surface whitening, the system was found to be fully cured and unaffected. A very different outcome would have been observed had the Customer chosen to use poured concrete for the repair and such flooding occurred.
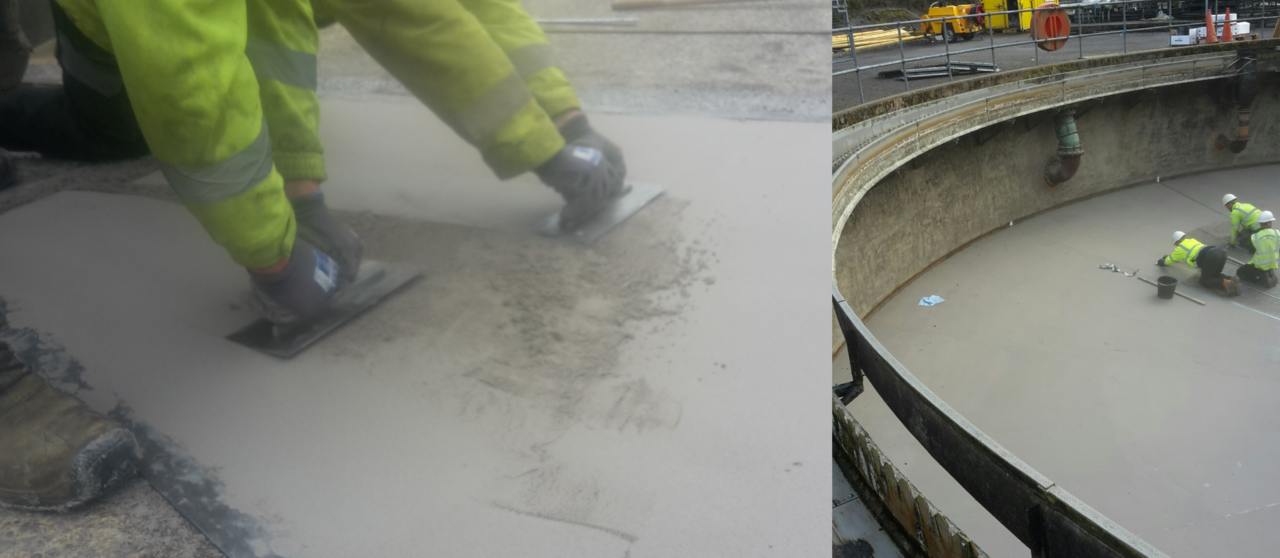
An Alternative to Concrete
The application and cure was completed in eight days. Had the Customer chosen to use the poured concrete method to repair the substrate, the application and cure would have taken weeks to be completed, rather than days. Thus, by opting for the epoxy repair mortar, this ensured that minimal disruption was incurred to the Plant’s operations.
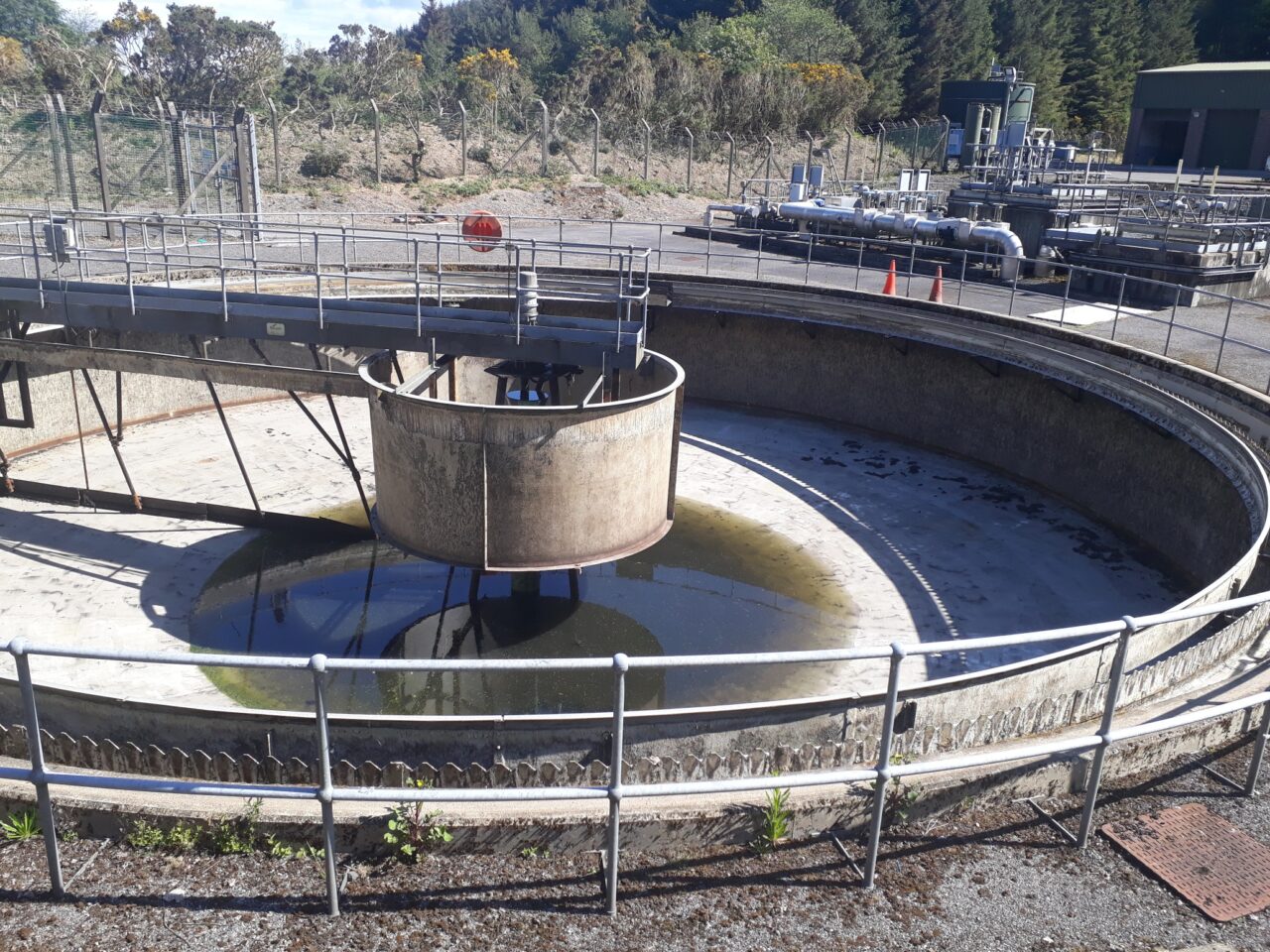
About Belzona UK:
Established in 1952, Belzona UK provides polymeric epoxy repair mortars and high-performance coatings to commercial and industrial facilities within the UK. On the 31st of January 2024, the Company announced the official opening of its independent UK Distributorship in Wales. The new facility features a fully equipped presentation suite, a practical workshop space and fully-stocked warehouse.
For More Information about Belzona UK:
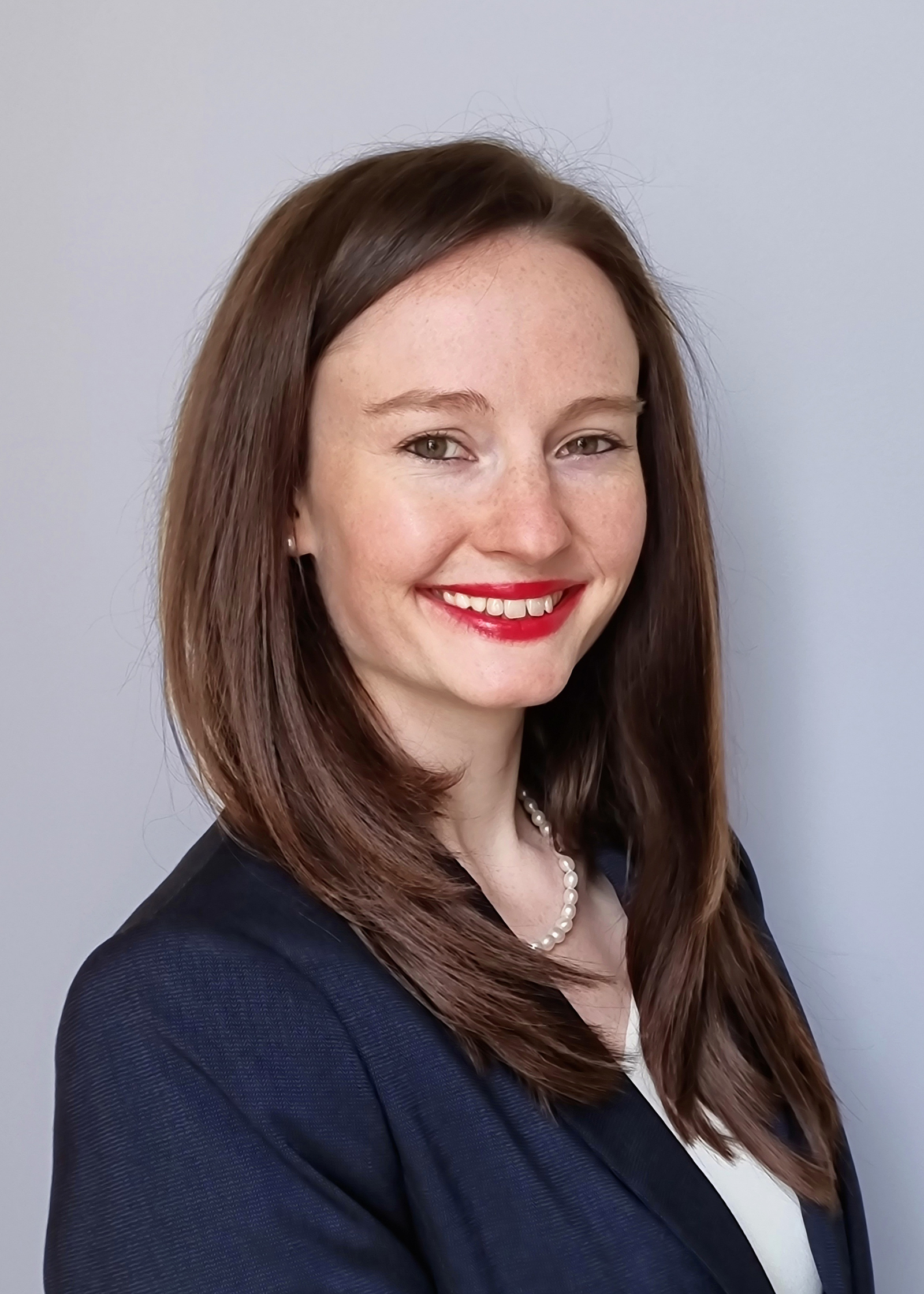
Chloe Hirst is the Senior Copywriter at Belzona Limited and is based in Harrogate, England. She gained a Bachelor’s Degree (with Hons.) in Media and Communications (specialising in Journalism) at Goldsmiths College, University of London. Chloe regularly writes case studies and thought leadership content featuring a variety of different industries, with a special focus on the renewables sector. In both 2023 and 2024, she won the Best Manufacturing Content Creation Specialist (UK) Award as part of Acquisition International’s Influential Businesswoman Awards.