Mining & Quarrying Application Overview
The mining and quarrying industry poses significant challenges to machinery and equipment due to a combination of abrasion, corrosion, wear, impact, and chemical exposure. Damage varies based on the specific mine or quarry conditions and the materials being excavated. With over seven decades of experience in mining solutions, Belzona understands the unique demands of these environments. We’ve identified the top five areas where damage is most prevalent:
- Repair of rubber components
- In-situ repair of damaged and scored shafts
- Lining chutes, hoppers and pipework
- Repair and protection of pumps
- Shimming of machinery and equipment
In this post, we’ll delve into each area to uncover the reasons behind their recurring issues.
REPAIR OF RUBBER COMPONENTS IN MINING FACILITIES
Problem
At the top of our list is the repair of damaged rubber components and equipment, a prevalent issue in mining operations. Rubber damage is frequently associated with conveyor belts and off-road tires, susceptible to tearing, ripping, and splitting due to the abrasive materials they handle, and the friction generated during their operation. Conveyor belts endure extensive wear from the rough sliding and impact of the materials they transport. Despite the design’s intention to absorb impact energy, sharp materials can still penetrate the rubber, leading to tears and splits in the conveyor belt.
Similarly, off-road tires on large trucks, diggers, and other mining equipment face harsh conditions, experiencing immense stress on their sidewalls, shoulders, and crowns. Extended service periods, impacts, incorrect inflation, or the presence of rocks can all contribute to cracks and damage in the rubber in these crucial areas.
Solution
In mining, vulcanization stands as the traditional method for rubber repair, involving heat and pressure to form a durable chemical bond. However, this process is often constrained by specific environmental conditions and specialized equipment requirements, leading to extended shutdowns. These shutdowns can incur significant costs and inefficiencies, particularly considering the immense material output of heavy industrial belts, reaching over 5,500 m3 (194,231 ft3) per hour when fully operational.
Alternatively, cold cure resins present a distinct solution, allowing for in-situ application without the need for specialized tools or hot repair processes. Offering durability, elasticity, abrasion, and tear resistance, they provide a versatile alternative for various repair needs in mining operations.
IN-SITU REPAIR OF DAMAGED AND SCORED SHAFTS
Problem
Our second mining and quarrying application area concerns damage that can occur to shafts. In this instance, machine and equipment shafts are susceptible to routine damage from erosion and corrosion, which can cause mining process delays and severe downtime. Damage to shafts usually occurs at bearing locations, journal, and seal areas due to wear. Generally, the erosion and abrasion are attributed to vibration, wear, and lubrication loss, all of which can lead to scoring, distortion, and misalignment.
Solution
Many solutions are available to the mining and quarrying industry that require dismantling the equipment to remove the shaft. However, this creates excessive downtime periods that are expensive and unnecessary. Some instead utilize orbital welding, which operates 360o around the shaft, welding to the static workpiece in constant motion. Orbital welding can require a large amount of equipment to be brought to the site, increasing downtime and potential hazards.
Conversely, cold-applied, metal repair, polymeric composites are available to restore shafts in situ to their original dimensions. Once cured, these materials provide erosion and corrosion protection; in some instances, their self-lubricating properties help to safeguard against vibration and wear.
LINING CHUTES, HOPPERS AND PIPEWORK
Problem
Chutes and hoppers are among the most heavily threatened pieces of equipment in mining. Much like conveyor belts, solid handling equipment is exposed to extensive erosion and abrasion from excavated materials of varying sizes. Not only that, but the impact, trajectory, and volume with which some of the material is transported through the chutes and hoppers can have detrimental effects on their structure. The process can often leave equipment affected by cracks, holes, and wall thickness loss because of the intense abrasion, erosion, corrosion, and impact.
Solution
The repairs available for chutes and hoppers are two-fold protection and prevention. Initially, it is necessary to fix holes and cracks to return chutes, hoppers, and other such equipment to service. Historically, this is done using hot work to weld metal plates into place over the defect. However, this is matched by the advent of cold-bonding practices that allow metal plates to be bonded onto the equipment using cold-curing polymeric materials.
Once the repair has been completed, protecting the main impact zones is crucial to preventing further damage. Protection can be achieved by an array of sacrificial barriers or linings, which help to absorb impact and abrasion from the mining materials. More recently, ceramic-filled abrasion-resistant linings have become commonplace to protect chutes, hoppers, and pipework. Solvent-free and cold curing, these linings can be applied in situ without specialist tools, allowing for safe and painless applications in confined spaces.
REPAIR AND PROTECTION OF PUMPS
Problem
Pumps are used throughout the mining industry for a mélange of processes, from transporting slurry to pumping subsoil water. As these materials are pumped through the process chain, they each bring various problems, threatening the service condition of the equipment. The main pump components, such as impellers, casings, and shafts, are subjected to abrasion, erosion-corrosion damage, and chemical attack.
Initially, this damage will lead to rough and pitted surfaces, which will increase friction and lead to a drop in the equipment’s efficiency and increased running costs. However, if not tackled in time, erosion-corrosion and abrasion problems may jeopardize the integrity of the component, ultimately causing the equipment to fail.
Solution
While replacing the damaged components might be an obvious solution, it is usually associated with high costs and lead times of weeks or even months. On the other hand, hot work, including welding and weld overlay, can induce heat stresses into the equipment and create problems with galvanic corrosion. More importantly, however, neither solution will address the underlying problem. For this reason, more pump operators are turning to cold-curing polymer technologies to repair and protect their equipment.
SHIMMING OF MINING MACHINERY AND EQUIPMENT
Problem
Finally, at number five is the creation of shims. Misalignment of machinery and equipment can occur frequently due to the severe impact and vibration within the mining and quarrying industry. These shifts in alignment can lead to potential losses in efficiency and damage to the equipment, particularly to bearing pin and bush housings and incorrectly fitting components.
Additionally, equipment size can differ from OEM specifications to in-service, resulting in loose components that can be damaged or removed by impact and vibrations throughout the industry processes. Typically, shimming applications can be carried out often associated with bearings, housings, and foundations or bases.
Solution
Shims can be created using many types of material, including metals. They are used to align components and foundations or fill gaps (irregular shims). However, shimming can be completed using polymer composites to provide 100% contact and avoid future damage. In the mining industry, surfaces that are difficult to access without dismantling equipment can be supported with fluid-shimming materials that are poured or injected, and then cured. Overall, shims born from polymer composites can be customized to each specific application, dependent on size and shape, while retaining excellent load-bearing strength.
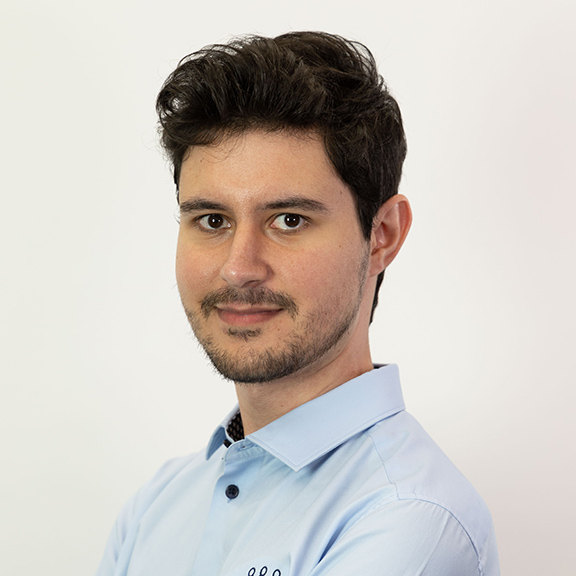
Digital Content Creator, Belzona Inc., Miami, Florida