This technical article was written by Yusuke Nishi, Senior Technical Services Engineer, Belzona. Part one is available here.
Compliance with standards
The composite repair of pipework requires a high degree of reliability, especially in the case of high pressure piping systems or for pipes carrying hazardous media. For this reason, rigorous third-party and in-house testing is carried out to demonstrate compliance with a series of requirements set out in ISO 24817 and ASME PCC-2. For the tests aimed at assessing the mechanical properties of the materials, plate specimens made of reinforcing fibre and each resin were used. On the other hand, in the pressure resistance test aimed at evaluating durability of the system, a short pipe spool with pseudo-defects of the specified dimensions was repaired with the system, followed by a pressure resistance test for confirmation. A summary of each test is given in Table 2.
Test items | Details | Test methods |
Tensile properties | Tensile strength, tensile modulus, Poisson’s ratio, strain to failure | ISO 24817 – Annex B ASTM D3039 |
Structural integrity | Wrapped pipe with defect to survive short term pressure test | ISO 24817 – Annex C |
Energy release rate | Toughness parameter for the repair/substrate interface | ISO 24817 – Annex D |
Long-term strength | Long-term (creep rupture) strength of the repair | ISO 24817 – Annex E |
Impact performance | Low velocity 5 J impact performance | ISO 24817 – Annex F |
Thermal properties | Coefficient of thermal expansion Glass transition temperature | ISO 11359 ISO 11357-2 |
In-plane shear modulus | Shear modulus by V-Notched beam method | ASTM D5379 |
Lap shear adhesion strength | < Short-term condition > Shear adhesion strength of resin bonded to substrate ____________________________________________________ < Long-term condition > Measurement of lap shear adhesion strength after 1000 hours of exposure to immersion | EN 1465 EN 1465 |
Test results and verification
Table 3 shows some results of the physical property tests. In parentheses are the curing temperatures of the specimens.
Test items | Belzona 1981 resin | Belzona 1982 resin | Belzona 1983 resin |
Short-term lap shear strength | 15.5 MPa (20°C) | 15.0 MPa (80°C) | 11.2 MPa (150°C) |
Long-term lap shear strength | 15.5 MPa (40°C) | 19.0 MPa (40°C) | 10.3 MPa (150°C) |
Glass transition temperature | 90°C (60°C) | 115°C (80°C) | 188°C (150°C) |
Young’s modulus | 38.8 GPa (20°C) | 38.6 GPa (20°C) | 36.9 GPa (150°C) |
Thermal expansion coefficient | 9.44 x 10-6 /K | 11.26 x 10-6 /K | 9.40 x 10-6 /K (20°C) 5.19 x 10-6 /K (150°C) |
In the tensile shear bond strength test, the bond strength of the resins is measured in two ways as: 1) cured for 7 days at specified temperature conditions (short-term condition), and 2) immersion in water for 1000 hours at specified temperature conditions (long-term condition), both using carbon steel as the adherend. The comparison of the results of the low and high temperature tests is intended to see the effect of temperature changes on the adhesive strength of the resins. All the results comply with the requirements of ISO 24817 in two respects:
- (a) The tensile shear bond strength of each resin is >5 MPa for short- and long-term conditions
- (b) For each resin, the long-term values are at least 30% of the short-term values
The glass transition temperature (Tg) is the temperature at which a polymer material begins to soften as it is heated. It is a common phenomenon for thermoplastics and its value is often referred to in assessing the thermal properties and thermal resistance of resin-based repair techniques. When the resin is heated while it is curing, the density of the cross-linking increases and the glass transition temperature rises. When Belzona 1981 resin is cured at 60°C, Belzona 1982 resin at 80°C and Belzona 1983 resin at 150°C, the glass transition temperatures are 90°C, 115°C and 188°C respectively (see Table 3).
Piping systems under pressure are subject to the Poisson effect. Due to the circumferential stresses occurring inside the pipe, the diameter of the pipe increases slightly, but at the same time there is a contraction in the axial direction and the pipe becomes shorter. Therefore, a Poisson’s ratio close to the value of the pipe is required for the composites to be a suitable material to restore the mechanical strength of the pipelines. The Poisson’s ratio of the Belzona SuperWrap II material is close enough to that of steel. This means that when a typical steel pipe is subjected to compressive or tensile loads, the accompanying SuperWrap II repair reacts similarly to the base metal.
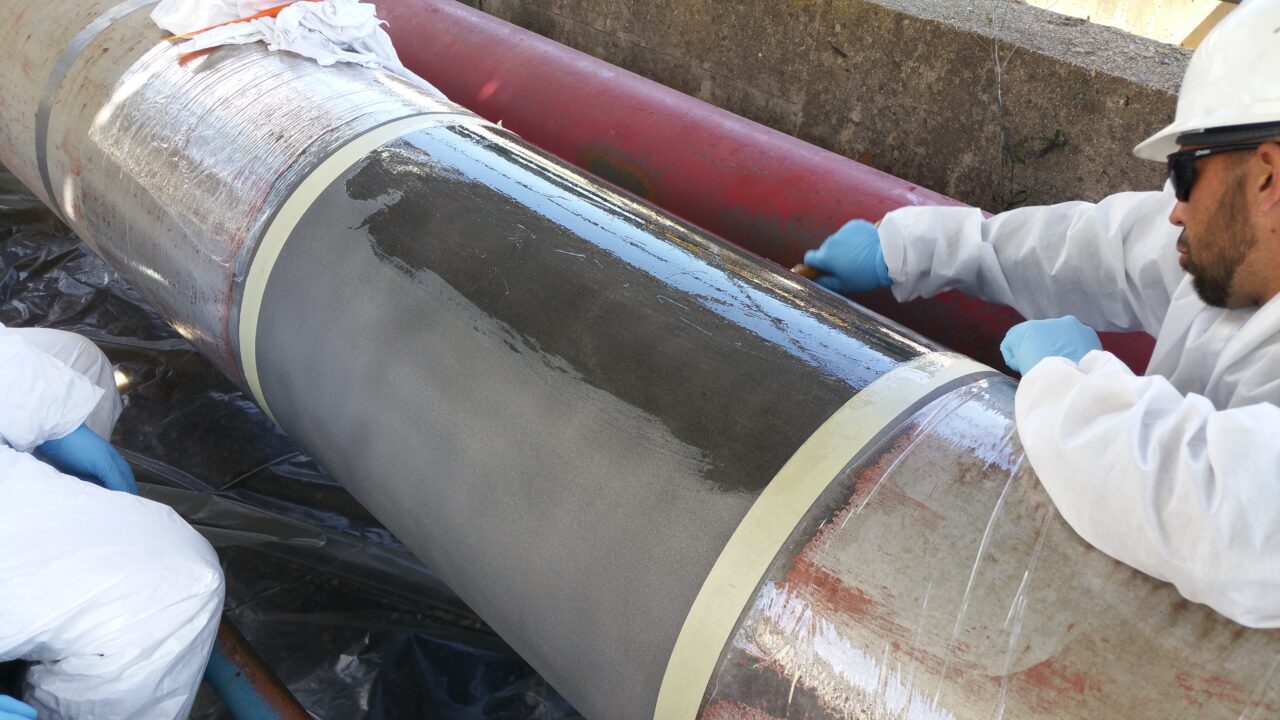
Young’s modulus (tensile modulus) is a measure of the stiffness of a material, and the SuperWrap II materials have high Young’s modulus of 37-39 GPa, meaning that the repair will have good stiffness and bending moment. From a practical point of view, when assessing the performance of a composite pipe repair, it is reported that a standard modulus of elasticity of 6,895 MPa or higher is desirable,3 and the values of SuperWrap II materials are well above this. On the other hand, considering that the Young’s modulus of ordinary steel is about 200 GPa, SuperWrap II materials, which have about one-fifth, are far more elastic than steel, and in this sense, it can be said that SuperWrap II repair has excellent elasticity and can easily follow the movement of the base metal.
The thermal expansion coefficient of a solid material indicates the extent to which its length and volume change when subjected to a change in temperature under constant pressure conditions. Piping, which is subjected to a variety of operating conditions, generally undergoes repeated expansion and contraction as a result of temperature changes. Therefore, composite materials used to restore the mechanical strength of pipe materials must also be able to cope with thermal strain. The linear expansion coefficient of Belzona SuperWrap II materials cured at ambient temperature are between 9.40 and 11.26 x 10-6 /K, which is close to that of ordinary steel (11-12.5 x 10-6 /K).4 This means that the stress effect (thermal strain) on the adhered surface caused by the difference in thermal expansion between the composite materials and the base metal is minimal.
Table 4 shows the conditions for durability testing of the SuperWrap II composite materials.
Test items | Belzona 1981 resin | Belzona 1982 resin | Belzona 1983 resin |
Short-term survival | 39.2 MPa | 39.2 MPa | 28.4 MPa |
Long-term survival | 60.0 MPa | 60.0 MPa | 36.0 MPa |
Impact | 5 J | 5 J | 5 J |
The short-term pressure test evaluates the performance of Belzona SuperWrap II against wall thinning defects (no penetration). The objective is to determine the maximum level of wall thinning that can be repaired. The test is carried out on a short carbon steel spool with a pseudo-defect (wall loss) of a specified size. The repair is designed to restore the yield strength of the original pipe wall. The test pressure was calculated as the yield pressure of the test spool in its original sound condition (test pressures indicated in Table 4). The difference in test pressure between the Belzona 1981/1982 resins and Belzona 1983 resin is due to the different test spools used. All the resins passed the test and the results demonstrate that the repair conforms to the design specification and is able to restore the durability of the pipe material.
The long-term pressure test also evaluates the performance of Belzona SuperWrap II against thin-wall defects. Here, the durability of the repair is assessed after 1,000 hours of sustained loading by maintaining the pipe internal pressure at a constant level (test pressures indicated in Table 4). As a result, no cracks, delamination or any other degradation was observed and the test was therefore deemed a pass.
The impact endurance test examines the effect on the repair of a low velocity 5 J impact, simulating a tool drop such as a spanner being dropped on the repair. The objective of this test is to determine the minimum thickness of the repair layer where external impact is concerned. In accordance with ISO 24817 Annex F, an impact of 5 J was applied to the pipe repair by dropping a weight from a height of 1 m, followed by a pressure test. The results showed that there was no difference between the measured and calculated energy release rates, and it was concluded that this level of impact did not affect the integrity of the SuperWrap II repair system.
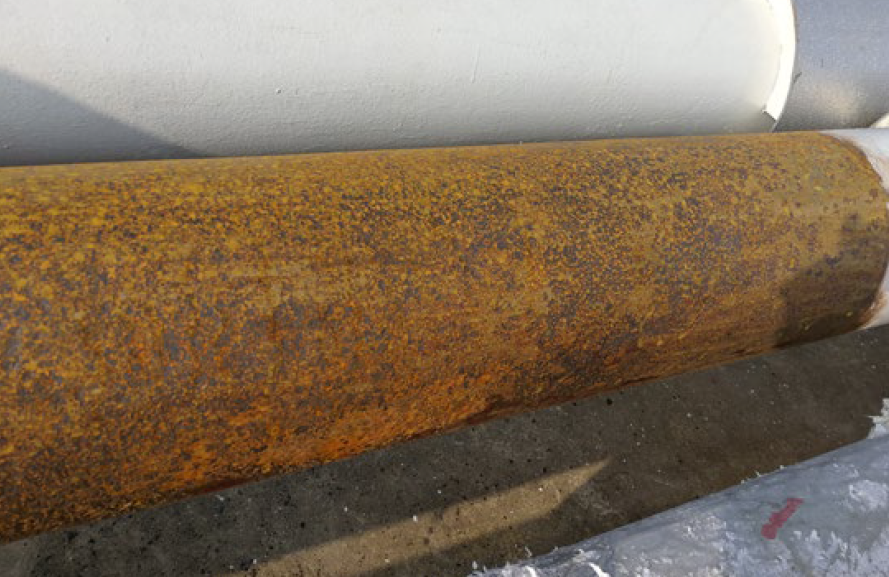
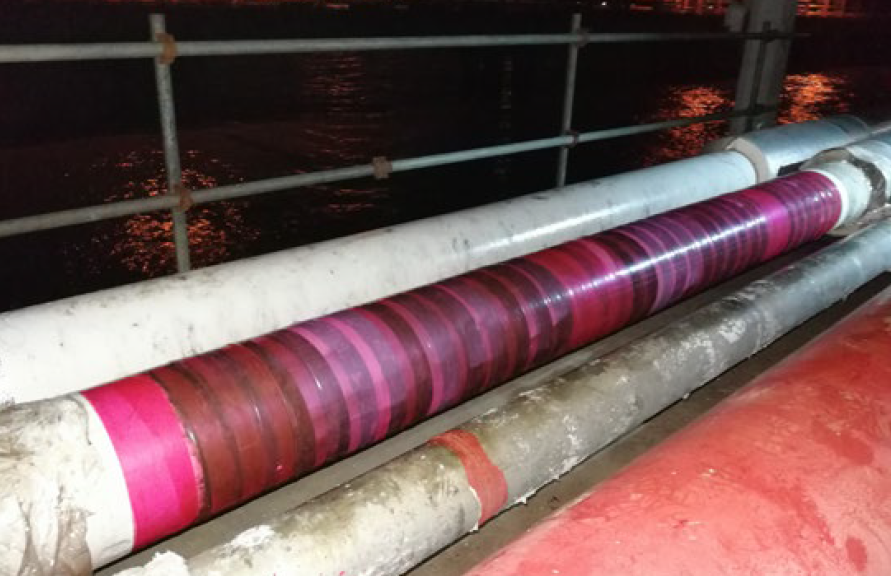
Requirements for Belzona SuperWrap II application
The repair design of Belzona SuperWrap II is determined by strength calculations based on actual defective conditions of pipes in accordance with the ISO/ASME standards, which also take into account factors such as surface preparation method, pipe geometry, environmental conditions, operational/design pressures, etc. The repair is then carried out following the design, but there are certain conditions that must be adhered to during the application.
Firstly, to ensure the quality of the work, all Belzona SuperWrap II installers are required to attend and pass a validated training course. The course includes a practical test (as well as a theory exam), in which participants are asked to repair a pipe spool with a simulated defect, which must then pass a certain pressure test.
As a strict rule, a compliant repair must always be conducted by trained installers. The ISO/ASME standards defines repair classes from class 1 to class 3. Class 1 is for low specification duties with least critical conditions such as pressure of <2 MPa and temperature of <40°C and since this is for systems that do not relate directly to personnel safety the repair jobs can be handled by installers alone. Class 2 and 3 however involve more critical scenarios, for example higher pressure and temperature conditions as well as systems transporting hazardous fluids; in those cases therefore the work must be supervised by a certified supervisor who has completed a higher level of training. Periodic annual renewal of qualifications is also compulsory for the installers and supervisors to ensure that they maintain and improve their skills after certification.
All the inspection results, including environmental measurements, surface roughness achieved by surface preparation conducted, batch numbers of products used, and resulting repair thickness, are recorded in QA/QC documents of each project. And this will be collected on all projects, including information on who was the installer/supervisor involved.
After use in service, Belzona SuperWrap II repairs can be revalidated or decommissioned upon reaching its design lifetime, depending on the decision made by the asset owner.
Belzona SuperWrap II repair solution is available worldwide through the network of Belzona International Distributors, and the applications can be carried out by trained and validated personnel from third parties as long as they fulfil the prerequisites. By allowing the asset owner to choose who would carry out the design and also who would apply the wraps on-site (as long as those parties are qualified as per the standard), the operator has the flexibility to appoint the contractors best suited, depending on the specific requirements of a project.
Conclusions
- Belzona SuperWrap II is a pipe repair technology based on a composite material consisting of a two-component epoxy resin and a hybrid reinforcing fibre (carbon fibre/glass fibre).
- Prequalification tests in accordance with both ISO and ASME standards have shown that Belzona SuperWrap II materials have a high level of mechanical properties and are suitable for the compliant pipe repair.
- The composite repair is designed on the basis of engineering strength calculations and is capable of restoring the integrity of damaged pipe materials.
- A system of accreditation and registration of installers/supervisors ensures uniform quality of workmanship and high reliability.
- Belzona SuperWrap II repair, which complies with the ISO/ASME standards, is a reliable long-term repair solution that contributes to the maintenance management of pipework.
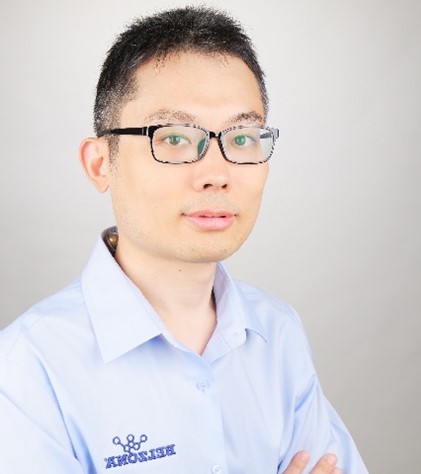
Yusuke Nishi is a Senior Technical Services Engineer for Belzona Asia Pacific based in Thailand. Yusuke has been with the company since 2011. He is an experienced professional within the plant maintenance industry specialising in composite repair and protective coatings. He possesses in-depth technical knowledge in various areas of polymeric solutions with a focus on corrosion management and problem solving, gained from over 10 years of experience at Belzona.
References
3 ALEXANDER, Chris, FRANCINI, Bob, ‘State of the Art Assessment of Composite Systems Used to Repair Transmission Pipelines’, Proceeding of IPC 2006
4 www.engineeringtoolbox.com
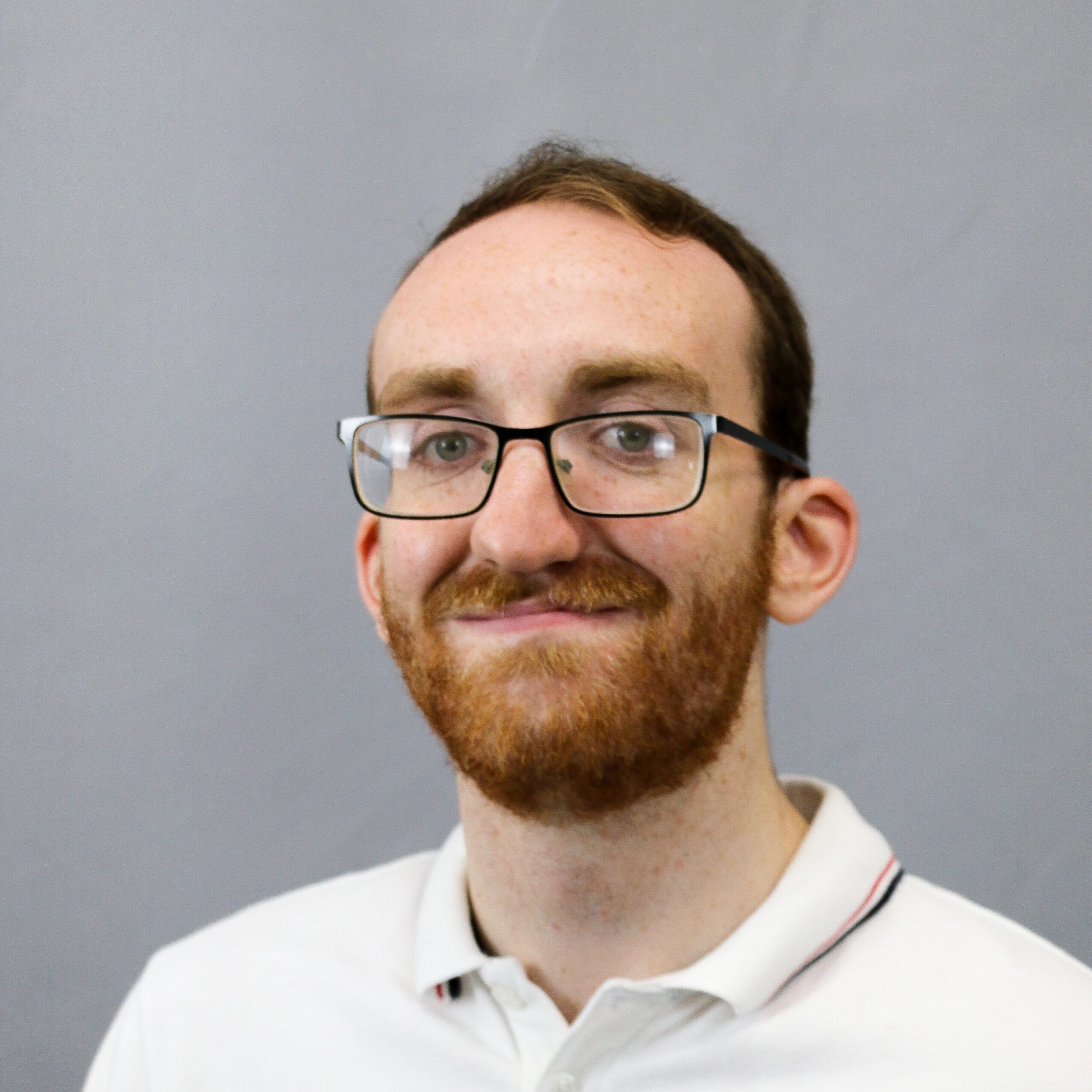
Content Creator, Belzona Polymerics Limited