Epoxy pipe repair is an alternative to using hot work and welding to repair a pipe. In industries, epoxy is used to repair equipment and machinery due to its accessibility and cold-curing properties. The following are three tips for why epoxy pipe repairs are preferable to alternative repair methods.
1. Corrosion
Chemicals, water, and components in water, such as salt, cause corrosion. Over time these factors create a corrosive environment for metal pipes. They lead to rust, wear, chipping, and leaks. Welding metal to metal may not resolve corrosion since the new metal will also corrode due to the environment.
One way to prevent damage is by using an epoxy pipe repair method. An epoxy coating will create a barrier between the substrate and any corrosive variable that could affect the pipes whether in the interior or exterior. Epoxy coatings cure into a solid material that has a long service life which will, in return, protect the equipment for an extended amount of time.
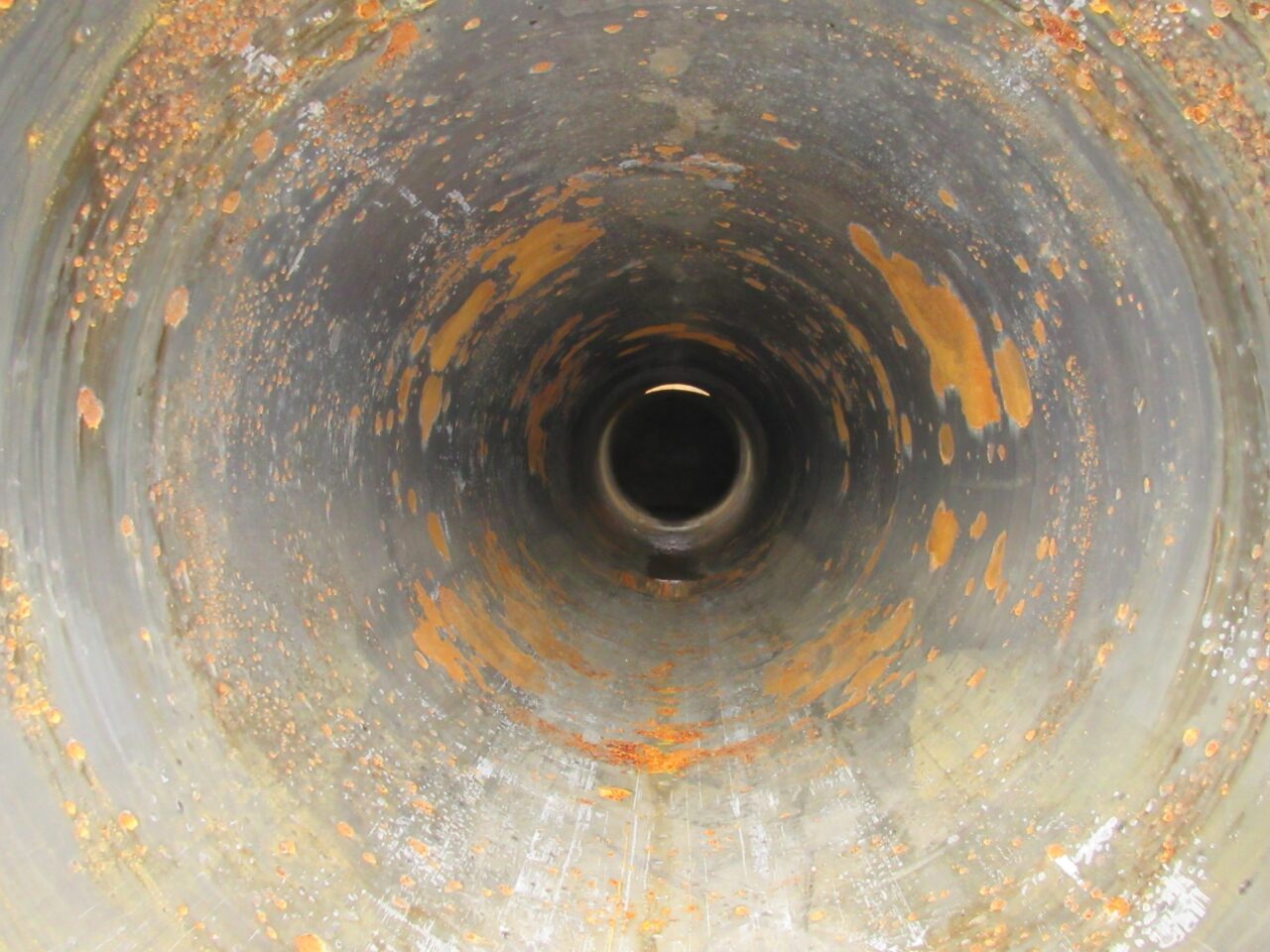
2. Erosion
Abrasive materials cause erosion. For example, stones and metals wear down the interior surface of pipes and shafts. The pipe will eventually have through-wall holes and other defects that impair operations. An erosion-resistant epoxy coating can shield a pipe’s interior from abrasive materials and withstand any impact and wear over time. Rather than replacing or welding the pipe, which takes a long time and is a temporary solution, an epoxy pipe repair will allow for a quick return-to-service without stopping operations. Equally important, the hardened epoxy coating will not suffer the same damages as a welded solution as the metal will suffer the same as the previously existing substrate.
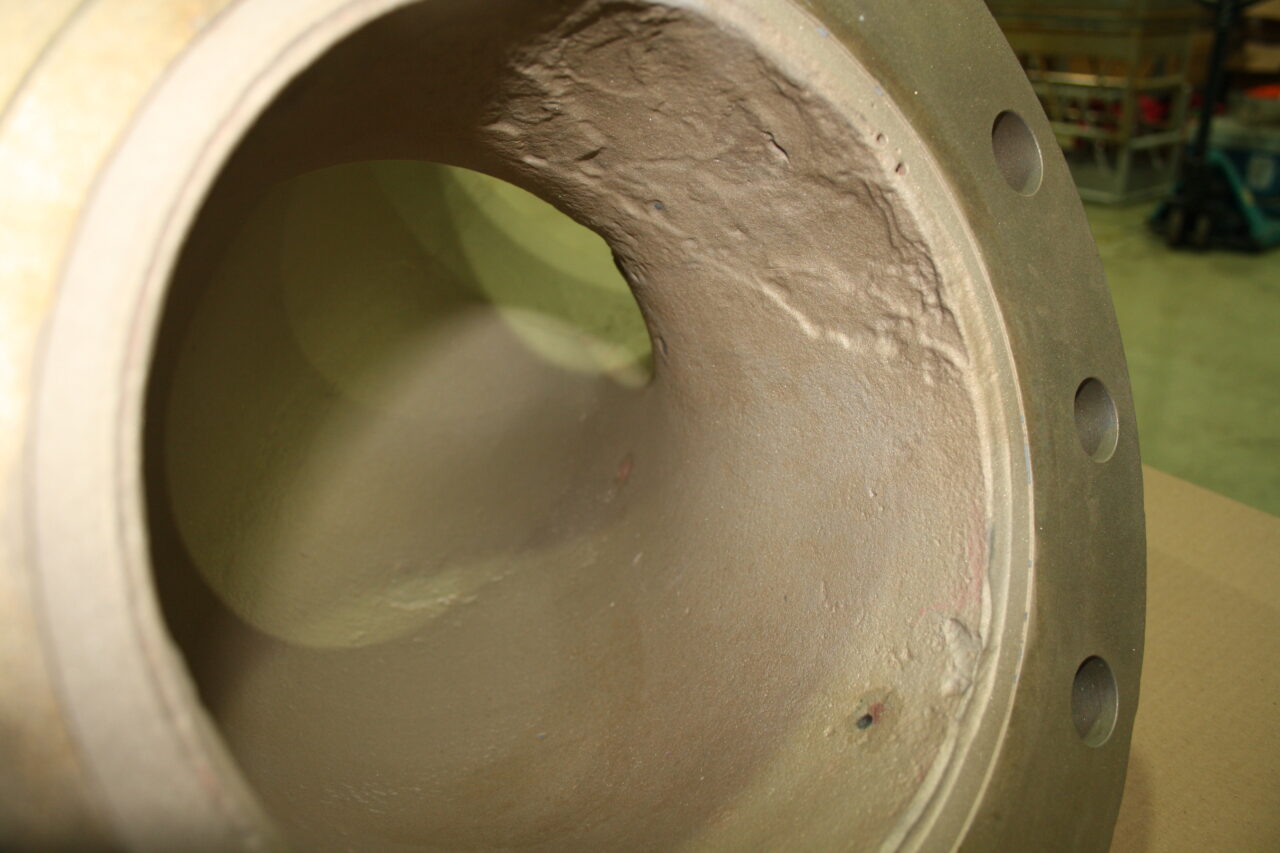
Epoxy Pipe Repair Case Study
In mining operations, slurries of solids and liquids are transported via pipes. These slurries are highly corrosive as they are made of chemicals and solvents. Also, they are highly erosive as they include rough heavy substances. Usually, mining facilities will coat equipment and pipes to prevent any damage.
A phosphate plant in Africa acquired new discharge pipes; however, they required erosion and corrosion-resistant lining to protect it from an acidic slurry. The new pipes were grit blasted and coated with Belzona 1321 (Ceramic S-Metal), a product for the epoxy pipe repair, as it can withstand erosion and corrosion. The phosphate plant created pipes that would have the extended service life they needed.
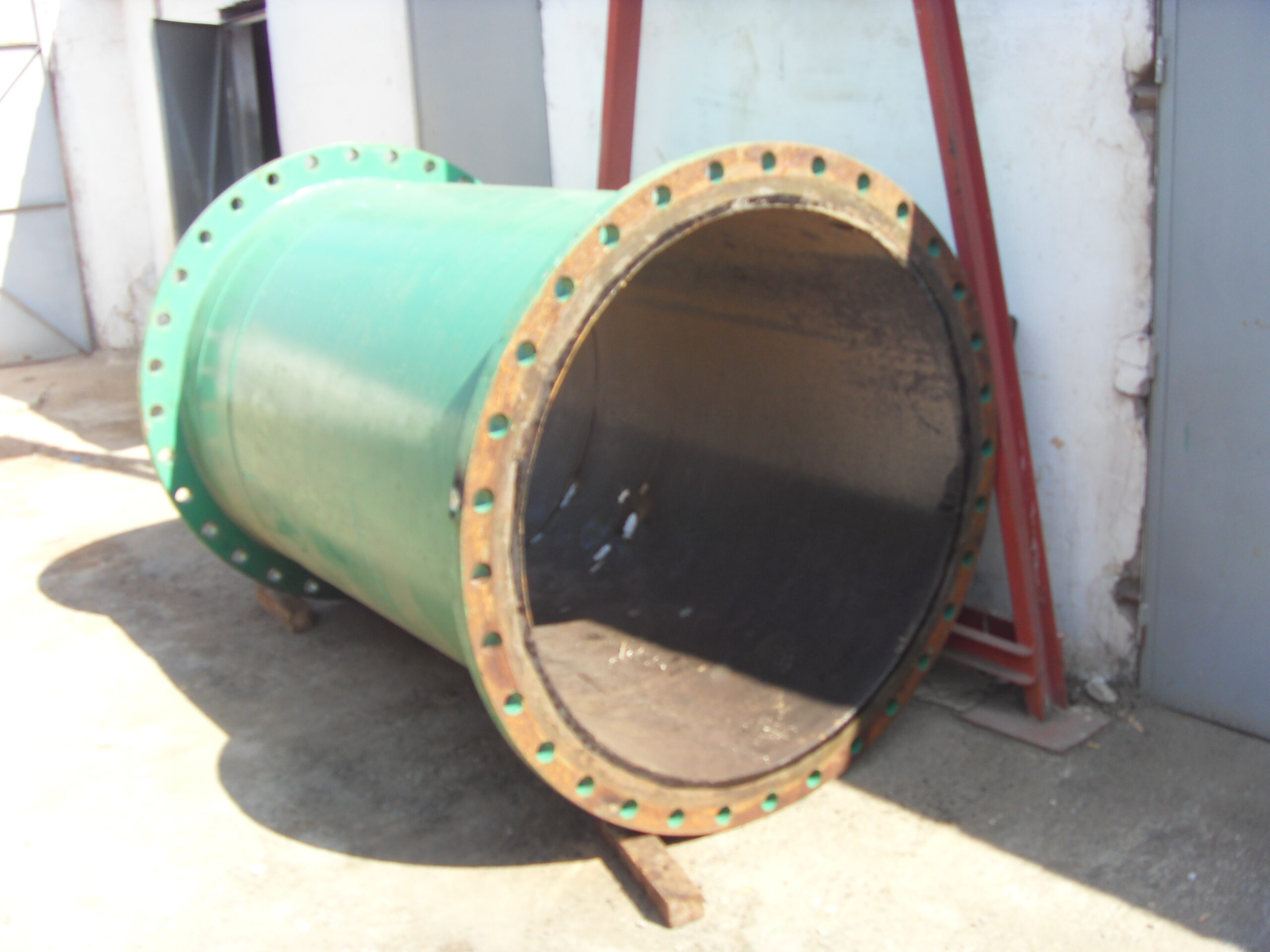
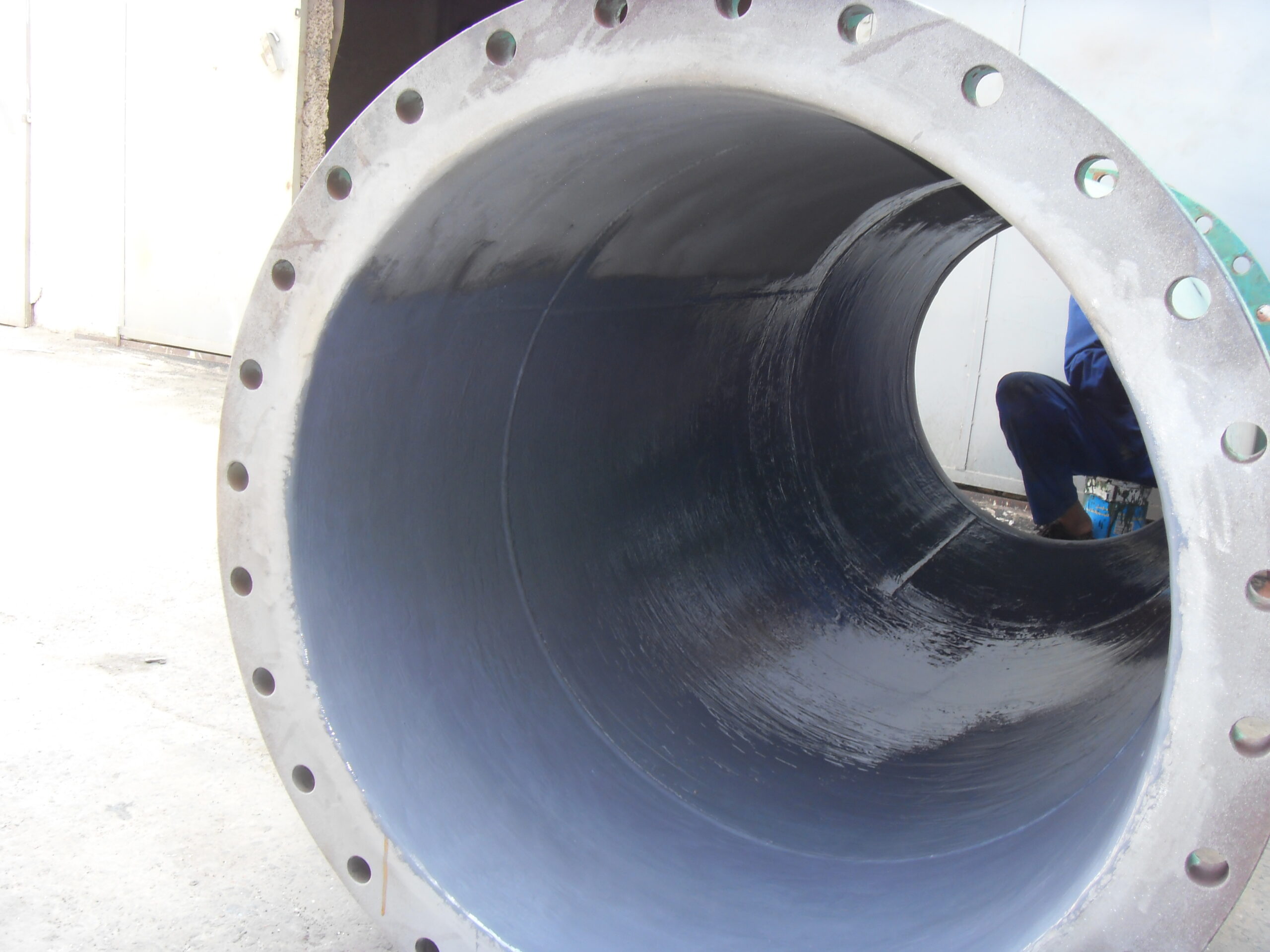
3. Efficiency
Finally, erosion and corrosion damages will affect the efficiency of pipes. Any indents and more will make it more work for transported items, especially liquids, to get through. However, a hydrophobic coating will allow liquids to glide throughout a pipe. In addition, the hydrophobic coating provides excellent corrosion resistance at a low cost, making it a preferable epoxy repair method.
On the other hand, a new pipe will arrive without imperfections, but it will not have hydrophobic properties which will perform less efficiently than a coating developed for liquid transportation. In general, epoxy coatings for pipe repairs offer long-lasting solutions where welding and other repair methods cannot since they are susceptible to the same industrial issues that cause the initial problems.
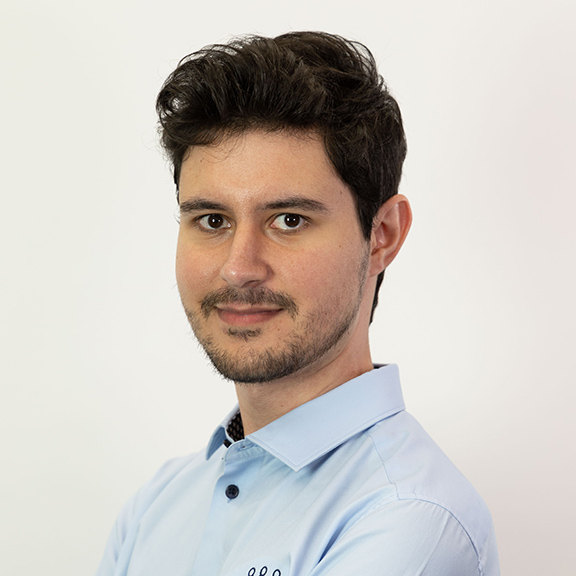
Digital Content Creator, Belzona Inc., Miami, Florida
Alexander, that was a handy post! When opposed to re-piping, epoxy pipe lining has become a popular pipe repair solution since it is a cost-effective alternative with less disruption and construction time. Furthermore, coating avoids leaks, and epoxy pipe lining can last 30 to 50 years, much like newly replaced pipes.