The notepad you’re writing on. That cardboard box that your last online order arrived in. Even the poster you saw for the latest blockbuster film. Finished products from the Pulp and Paper sector are everywhere. Overall, worldwide consumption of paper has risen by 400% in the last 40 years (including recycling used materials) highlighting the added emphasis on the pulp and paper process.
Trends indicate that paper companies are increasingly combining their forest harvesting and lumber mill operations in a bid to improve the efficiency of their sourcing and production. As a result, the number of functions and types of equipment found within paper mills has escalated, alongside the variety of issues that spark the requirement for maintenance.
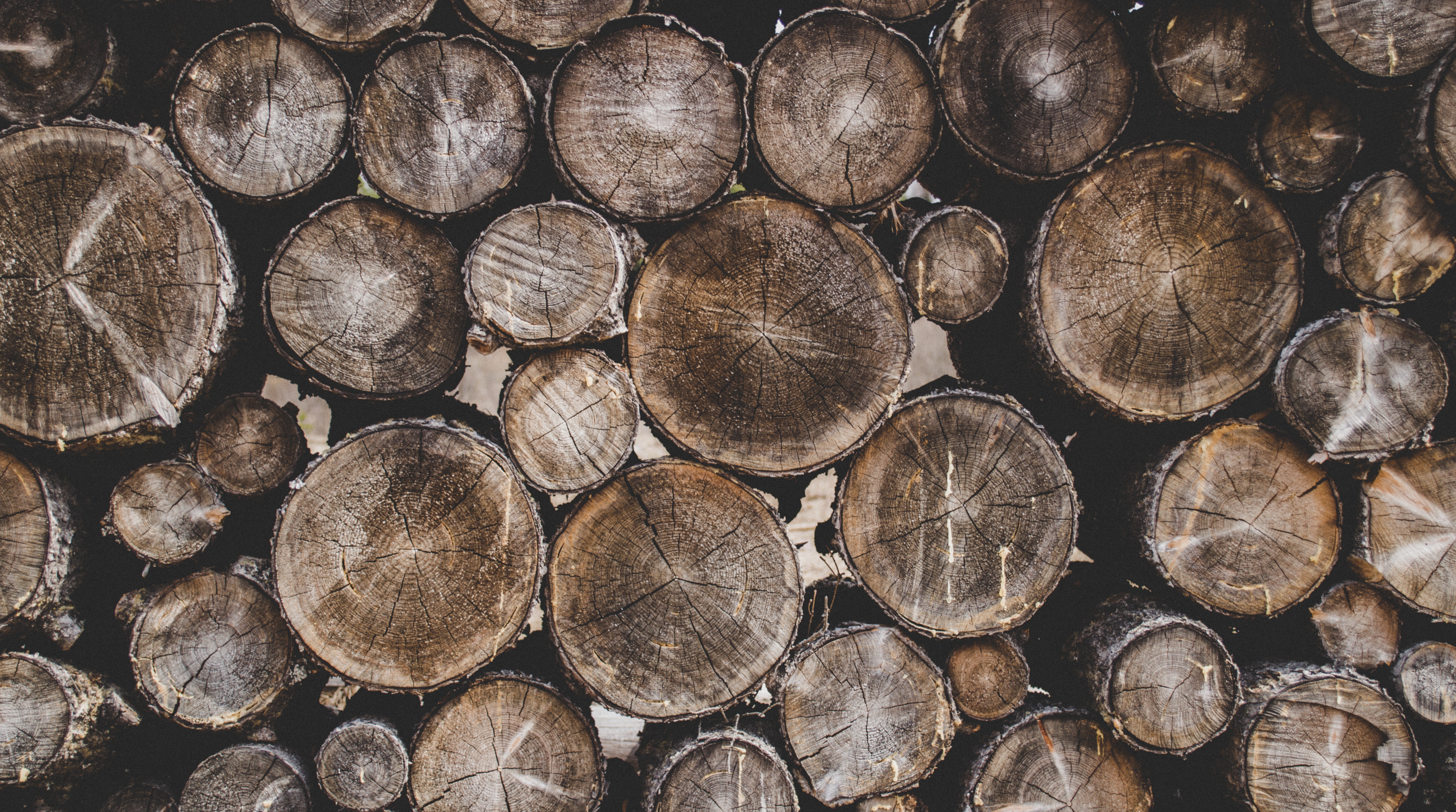
To accommodate the soaring production levels, maintenance needs to remain effective for the long term, avoiding downtime and ensuring maximum output. Thankfully, over time, maintenance methods have also advanced, ensuring greater protection against the effects of abrasion, corrosion and erosion throughout the course of paper manufacture.
This post looks at 4 key application areas in Pulp and Paper, analysing the damage mechanisms at the heart of the problem and suggesting some appropriate solutions available for them.
PULP AND PAPER MAINTENANCE AREA 1
Wood handling equipment
The first stage is the harvesting of the raw product – wood. Once gathered, wood handling equipment plays a fundamental role in delivering a usable material at the beginning of the pulp and paper process. Used to exfoliate the bark from logs, de-barkers are among the most robust pieces of machinery operating within the industry and facilitate high volume processing. This method creates an incredibly abrasive environment, progressively wearing the machine’s components.
Durable repair composites, such as Belzona 1811 (Ceramic Carbide), are designed to withstand the harsh de-barking environment. They bond tenaciously to steel substrates, allowing worn and damaged equipment to be easily rebuilt. The finish they provide is seamless, and excellent protection is achieved against abrasion and wear from all coarse materials including bark.
MAINTENANCE AREA 2
Wood chipping
The process of wood chipping causes continuous wear and abrasion from wood chips entering chippers at high velocity, damaging the knives but, more importantly, the knife pockets as well. Worn knife pocket profiles can further deteriorate the rotor assembly, as well as lead to the generation of off-size chips. Unsatisfactory chips will adversely affect the pulping process and the quality of the resultant paper, therefore this issue can be costly.
As a cold-applied maintenance option, worn knife pockets can be reformed using a 100% solids Belzona 1000 Series material, such as Belzona 1311 (Ceramic R-Metal). Not only can these create a perfectly mated profile, but they will eliminate future corrosion issues, making the reoccurrence of worn knife pocket profiles unlikely.
Abrasion resistant coatings can be the final piece of a comprehensive maintenance solution. Applied following sufficient rebuild, worn chipper components can be protected from impact and wear damage, ensuring the satisfactory production of chips. This significantly benefits the pulping process and the quality of the manufactured paper.
MAINTENANCE AREA 3
Pulping and pumping
Regardless of the pulping methods, paper mill pumps are put under immense strain due to the transfer of viscous material throughout the pulping process. Together, the sludge and slurries combine a high solids content, copious amounts of entrained air and often processing chemicals for screening, cleaning and bleaching. As a result, issues associated with erosion, corrosion and chemical attack are common place.
Severely damaged equipment, such as diffusers, rotary vacuum washers or liquid ring vacuum pumps, can be restored to their original profile and protected from deterioration using our range of epoxy repair materials and coatings. Belzona’s cold-applied, paste-grade, metal-repair composites, such as Belzona 1111 (Super Metal), can be used to repair cracked and holed pumps, providing outstanding chemical resistance.
MAINTENANCE AREA 4
Conveyor belts
Transportation of raw and processed materials keeps the pulp and paper production system rolling. Whether it is screw conveyors initially or conveyor belts towards the latter stages, both play a crucial role. The inclusion of conveyor belts within the 4 key maintenance areas is guaranteed as a result of the increase in recycling. More than half of the paper produced each year comes from recovered sources and experts have said that paper can be recycled an average of four to six times.
Conveyors belts cater for this element of the pulp and paper sector especially, moving the recycled materials on to the next stage of process. However, over time, rubber belts can be damaged after catching on poorly-lubricated or sharp elements, resulting in rips, tears and splits.
Traditional conveyor repairs can encumber long lead times, waiting for specialist vulcanisers to carry out maintenance. This means longer downtime and lost production. Belzona rubber repair materials, such as Belzona 2111 (D&A Hi-Build Elastomer) and Belzona 2311 (SR Elastomer), can be used for flexible repairs, including worn and torn conveyor belts. Notably, these can implemented without the use of hot work or disassembling the equipment. Additionally, by incorporating positive grip systems, belt slippage can be eliminated, protecting driver rollers from abrasion and corrosion.
A world of wear
These are just 4 key maintenance areas that follow the pulp and paper production path. Of course, handling such abrasive and sometimes erosive materials makes the industry a whole world of wear. Honourable mentions for other maintenance areas include hoppers, screw conveyors, silos, storage tanks, rollers, refiners, dryer cans and any number of different mechanical transmission components. What would feature in your key maintenance areas? Let us know about what issues are troubling your pulp and paper plant in the comments below. Visit Belzona.com for more information about our range of solutions for the Pulp and Paper sector.
Alternatively, contact us to discuss your maintenance issues.