An underground oil pipeline at a Refinery in Spain was suffering from severe corrosion. If left unchecked, the pipeline, 872 metres (2860.8 ft) in length, would have incurred severe metal loss. As a result, disastrous consequences, both financially and also from an environmental perspective, could have ensued.

Solution Sought to Mitigate Cost and Carbon Footprint of Pipeline Replacement
A prompt repair was required for the carbon steel pipeline, 55.9 cm (22 inches) in diameter, in order to mitigate any further corrosion damage being incurred. In fact, if left unrepaired, this would have caused the substrate to completely corrode through and, therefore, serious environmental issues could have ensued.
A potential solution would have been to completely replace the pipeline. However, considering its mammoth length, this process would have required considerable financial expenditure and, furthermore, would incur a hefty carbon footprint.
For every ton of steel that is produced, 1.85 tons of CO₂ – nearly double the amount – is released back into the atmosphere (Carbon Clean). In addition to this, the process of removing and disposing of the damaged pipeline further ratchets up the carbon footprint of this process.
As well as the environmental impact of replacing the corroded pipeline, this process would also require a considerable period of downtime which would lead to further profit-loss. The combination of these factors, costly in both a financial and environmental sense, led the Customer to seek out an alternative solution to replacing the steel pipeline.
Expensive Replacement Process Bypassed with Composite Wrap
The Customer decided to repair and protect the pipeline with a combination of polymeric technology in order to bypass the drawbacks associated with replacing the pipeline.
The following systems were specified and applied following an inspection from Elena Expósito Fernández, AMPP (NACE) Certified Coating Inspector Level 2 and Technical-Commercial Delegate at authorised Belzona Distributorship Rodator Composites:

“The 2-part epoxy paste, Belzona 1111 (Super Metal), was specified to fill in any gaps in the weld seams to ensure the pipeline had a smooth profile. For heavily corroded areas, plate bonding was required using steel plates which were 50 cm x 60 cm (19.9 in x 23.6 in) in size, with a thickness of 5 mm (0.2 in). These were bonded into place using the epoxy structural adhesive, Belzona 7311. To reinforce the pipeline, the composite wrap, Belzona SuperWrap II, was specified. Finally, the anti-corrosion coating, Belzona 5811 (Immersion Grade), was chosen to provide long-term corrosion protection.”


Polymeric Technology Supports Decarbonisation of Oil and Gas Industry
The Customer was able to successfully bypass the drawbacks associated with complete pipeline replacement by instead, opting to repair and protect the pipeline with a combination of polymeric technology. As well as making huge financial savings, this solution enabled the Customer to also minimise its environmental impact as well.
As the oil and gas industry continues to decarbonise, this latter point is particularly paramount. Polymeric technology is an extremely viable way in which oil and gas asset managers can make great strides in mitigating the carbon footprint of their facilities. An increased uptake in the use of cold-applied repair composites and protective coatings would help to accelerate the decarbonisation of this industry.
This article was originally published in International Oil & Gas Magazine.
Want to learn more about Belzona SuperWrap II?
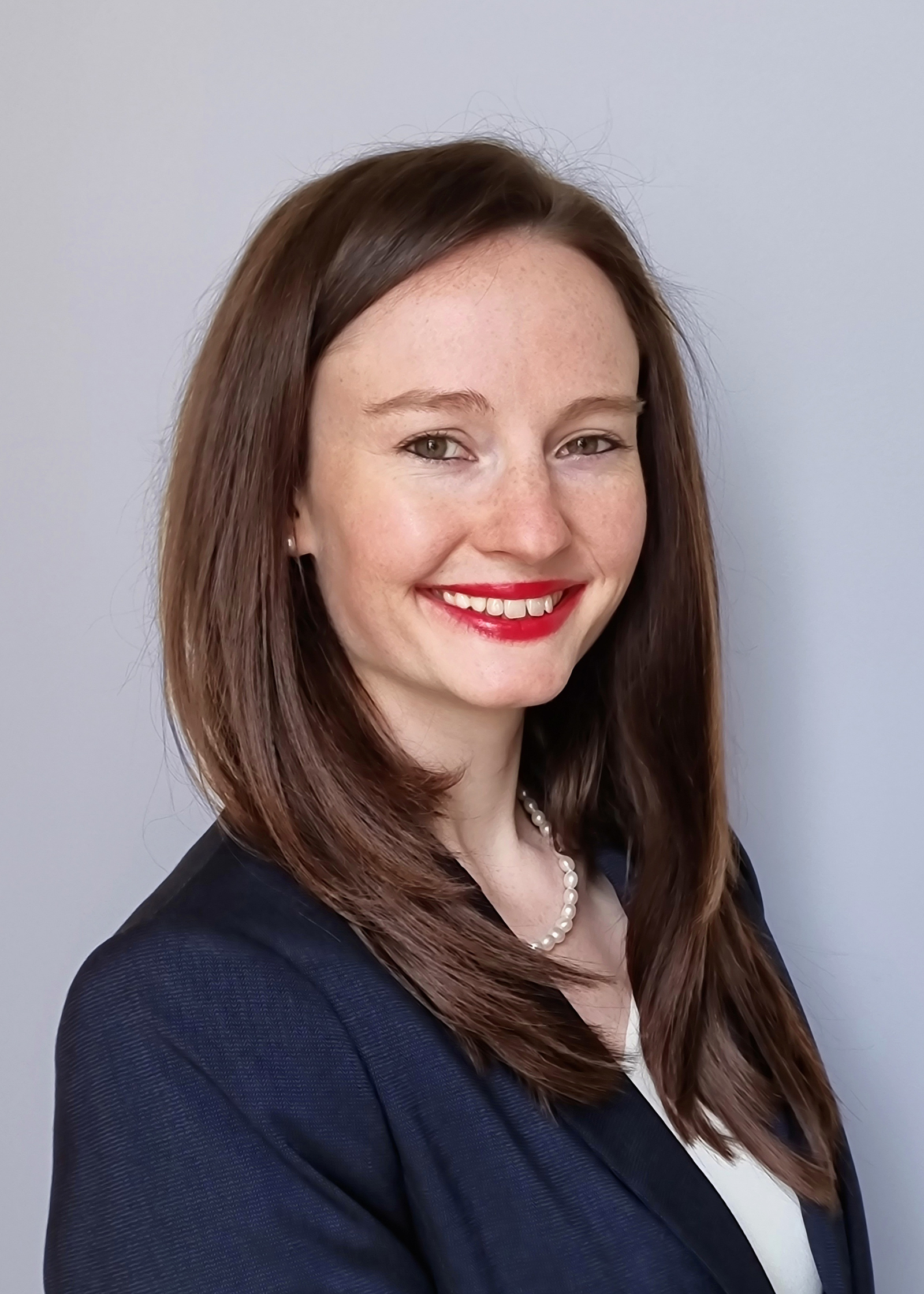
Chloe Hirst is the Senior Copywriter at Belzona Limited and is based in Harrogate, England. She gained a Bachelor’s Degree (with Hons.) in Media and Communications (specialising in Journalism) at Goldsmiths College, University of London. Chloe regularly writes case studies and thought leadership content featuring a variety of different industries, with a special focus on the renewables sector. In both 2023 and 2024, she won the Best Manufacturing Content Creation Specialist (UK) Award as part of Acquisition International’s Influential Businesswoman Awards.