This is a transcript of the Belzona “Solve it Session” webinar conducted on March 1, 2018. You can watch the webinar recording here:
WHAT’S THE PROBLEM?
First of all, let’s look at the problems that metallic assets can experience. External and internal erosive forces and corrosive substances can lead to pitting and thin-wall defects. Eventually, if not addressed soon enough, they are likely to go through-wall. Issues described above are mainly seen on pipework and pipelines, but we should not forget storage tanks and process vessels, which can experience similar problems, such as CUI damage on a storage tank.
Let’s look at some repair methods you may be familiar with, such as cut and weld. Apart from all the typical metallurgical issues associated with hot work, there is of course downtime. We also know that welding requires a high level of expertise.
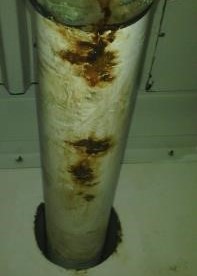
When methods alternative to welding are being used, there is a question of longevity. Even when we accept the repair to be “temporary”, we want it to last close to the lifetime of the asset and not require ongoing maintenance.
WHAT’S THE SOLUTION?
Composite repairs can provide a viable solution to common maintenance problems. Belzona manufactures and supplies a composite repair system, Belzona SuperWrap II. It is a combination of resin and a reinforcement sheet which have been strategically designed to provide structural reinforcement to weakened structures.
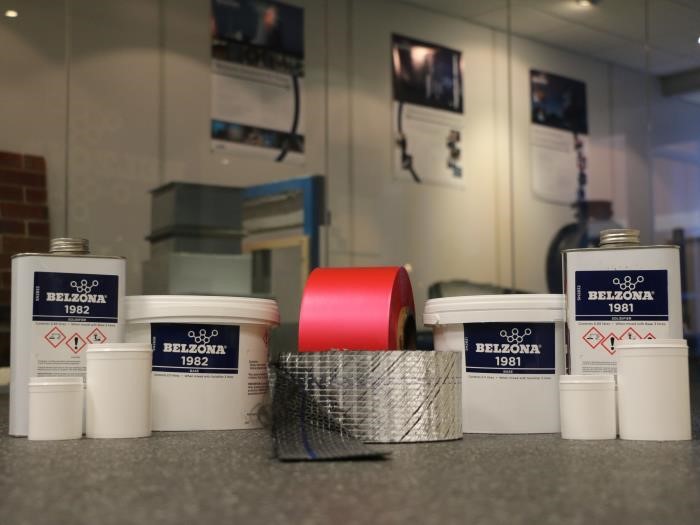
The resin used in the Belzona SuperWrap II system is 100% solids epoxy. As a result, Belzona SuperWrap II:
- Exhibits outstanding mechanical adhesion to metallic substrates
- Has low tendency to creep
- Does not shrink when the product is finally cured
- Is an extremely durable solution as it does not corrode.
The reinforcement sheet is a hybrid of carbon and glass fibers. By combining these two materials, we are able to have a reinforcement with high tensile strength and less stiffness, two important properties for any nonmetallic composite repair system.
BELZONA SUPERWRAP II RESINS
In conjunction with the reinforcement sheet, there are three different resin grades that can be used. The resin chosen is dependent on the operating and environmental conditions of where the repair is taking place.
Belzona 1981 is a fast curing resin that is designed primarily for cold environments. Belzona 1981 is designed for applications within 5°C-20°C (41°F-68°F). Belzona 1981 can be used for service temperatures up to 60°C (140°F).
Belzona 1982 is a resin designed for applications in warmer climates. It is chemically enhanced, so it’s working life is extended. Thus, it is easier to apply in warm climates like those found in the Middle East and Brazil for instance. Its application temperature range is between 20°C-40°C and can be applied onto assets operating up to 80°C (176°F).
Belzona 1983 is a recent addition. It is a resin that is designed for service temperature levels up to 150°C (302°F). It is applied within 5° C -40°C (41 F -104°F).
WRAPS AND PATCHES
There are two types of repairs that you will regularly see: wraps and patches. Wraps around the full circumference are repairs typically used onto piping, pipelines, and pipework components in general. Provided that the diameter of such components makes it easy and practical, wraps can be used.
However, if the pipe diameter is so great that encompassing the whole circumference is no longer practical, then patches, using the SuperWrap II system, can be used. However, applicators may find it easy to use wraps onto large 24” OD pipes, it comes down to personal preference.
The photos below show the versatility of previous Belzona SuperWrap II applications. As you can see Belzona SuperWrap II has not only been applied on straight sections, but also tee geometry and even extremely large wraps on storage tanks!
APPLICATIONS ONTO MANUALLY PREPARED SURFACES
Previously, Belzona SuperWrap II could only be applied onto substrates that have been abrasively blasted, however we are now happy to announce it can now be applied onto manually prepared substrates compliant to ISO / ASME standards, if compliance is required.
Although this method is not as effective as blast cleaning, its known that hand or power tool cleaning is often more practical, especially where access for blasting may be restricted.
Out in the field the issue was, if the client still requires an ISO / ASME complaint pipe repair solution, however they are unable to blast. What can they do? Which got us thinking… what can we do to accommodate the client requiring a compliant repair, whilst being unable to grit blast?
We therefore decided to enable our composite pipe wrap repair system, Belzona SuperWrap II, to also be compliant when applied on to manually prepared surfaces…. or without having to be prepared by grit blasting!
Extensive testing had been previously done to enable the SuperWrap II system to be compliant on grit blasted surfaces. All this specific testing would have to be conducted again using the same substrate material, surface preparation, repair laminate, filler material, adhesive and application method before the system could be classed as compliant to ISO / ASME standards on manually prepared surfaces.
As you can see, the surface preparation change means all qualification tests need to be redone. The next stage was to select which standard to comply with whilst ensuring that a replicable and consistent substrate preparation can be achieved.
Looking at the standards, there were some similarities, ISO 8501-1 ST2 is a very low level of preparation and gives low indicative results, as it does not re-cut a new profile. ISO 8501-1 ST3, using a power tool was better, but still does not specify a level of profile with the required cleanliness level. Finally, we investigated SSPC SP-11 standard which specifies conditions for the appropriate cleanliness AND a minimum 25-micron roughness profile, therefore this was selected.
The manually prepared compliance testing has been carried out on two of our Belzona SuperWrap II resins, Belzona 1981 and Belzona 1982.
We have not conducted the testing using Belzona 1983 resin as this resin is designed to be used in higher temperatures / higher risk applications, therefore we would only recommend abrasive blasting preparation when conducting a Belzona SuperWrap II repair using Belzona 1983 resins.
We have completed the required compliance testing, however we want to provide further evidence of the long lasting performance of the Belzona SuperWrap II system, therefore we have undertaken the Annex E – 1000-hour test. Once this testing has been completed we are confident the results will provide further evidence of the endurance of the Belzona SuperWrap II system over long periods of time. Vigorous testing is not the only way we ensure that the solution performs well in service. We also run training courses to raise and maintain global application standards from our training centres in Miami, Harrogate and Chonburi.
We can train installers, supervisors, designers and trainers. Upon achieving a trainer level, that person is then able to run installer and supervisor courses locally. We also keep records of all people who received Superwrap training. Most countries now have validated applicators and supervisors. There are also many designers who can produce Belzona SuperWrap II designs in accordance with ISO or ASME standards. There is also a handful of trainers who are then able to deliver Belzona SuperWrap II training locally.
Now let’s put this training in action and look at some case studies from the field. In fact, Belzona maintains a substantial database of case studies on this publicly accessible website khia.belzona.com
It’s very easy to use. Just go to the website and search by keywords. These keywords can be regarding a specific problem, industry, application or product. Recently, an independent company, Industolutions, conducted research on B2B case studies and found that Belzona is ranked 4th globally at producing success stories.
Let’s look at a few examples of Belzona SuperWrap II being used to restore asset integrity. First, we go to the North Sea, where open drain piping of a helideck required extensive repairs. 3 wraps with a total thickness of 6mm were applied over 2 periods of 14 days. A combination of through- and thin-wall defects were repaired with Belzona SuperWrap II. This was a sizeable application with 320 litres of resin used, almost 500 metres of reinforcement sheet and 55 kilos of Belzona 1111 used to fill the pitting prior to the application of the wrap.
Two previous examples showcased offshore opportunities, so now let’s look at some onshore applications. Here we have a carbon steel tank in Spain. It was suffering from corrosion under insulation. In this case, Belzona SuperWrap II was applied as a patch over several areas. As a general rule, as long as Belzona SuperWrap can be consolidated, a patch repair can be completed. As this was a 6m diameter tank, the same release film used to consolidate a wrap was used. Finally, a Belzona UV-stable coating was used over the patch for aesthetic purposes.
In our last example, we wanted to show you something a bit different. At a nuclear power station’s cooling water system, a pipe protruding from a concrete wall was badly corroded. Cut and weld or any externally applied repair wasn’t feasible as the corrosion continued beyond the concrete wall.
So, what do we do when we can’t repair from the outside? We work from the inside. For this repair a composite sleeve made from SuperWrap II was manufactured and installed. It was bonded in using Belzona 1161 and coated with Belzona 1321.
Let’s look at how they did it. A plastic former was used to shape the SuperWrap II sleeve. This insert was consolidated, then upon cure and former removed, it was sanded and ready for insertion. As you can see, even a brand new flange was created. A brilliant unique application!
So, those are just a few examples from the field with more available on khia.belzona.com. Let’s next see the testing behind the SuperWrap II system which helped achieve these successful applications.
Although the SuperWrap II system successfully completed the ISO / ASME compliance testing, we have also conducted additional testing to generate additional data on the performance of the system, even in extreme conditions.This first example was conducted to demonstrate the performance of the Belzona SuperWrap II system at elevated temperatures using hot oil.
We designed 4 pressure spools for a maximum pressure retention of 10 bar. We then wrapped the pressure spools in accordance with the design created, before then testing them in oil at an average 143°C (289°F).
Even though the wrap was only designed to withstand a maximum pressure of 10 bar, the average failure pressure from the 4 wraps equalled 44 bar, which is over 4 times what the system was designed for!
Another example of further testing that we have undertaken recently is the thermal shock testing of the SuperWrap II system.
Here we heated the SWII system up to 100°C (212°F) before then dousing the samples into a solvent bath at a recorded temperature of -60°C (-76°F).
Cycling the system five times, whilst also visualising the samples for cracks. We are happy to announce that the thermal shock testing did not adversely affect the Belzona SuperWrap II system. Even after providing evidence of the testing we have done with Belzona SuperWrap II, we still get asked; why use a Belzona SuperWrap II repair over a standard composite wrap which has been used in the field for years if a compliant repair is not necessary? The video below shows another reason why. Here you can see a conventional pipe wrap being tested against a Belzona SuperWrap II repair. You can see the pressure rising on both repairs, however watch how the conventional wrap fails compared to the Belzona SuperWrap II system.
It clearly shows the conventional wrap failing cohesively, sending a projectile along with it. However, the Belzona SuperWrap II system failed adhesively along the bond line, allowing a slow depressurisation of the system. Belzona SuperWrap II provides an alternative, cost-effective and long–lasting option compared to conventional alternatives. The Belzona SuperWrap II system has many application benefits, ensuring an easy and safe application, plus many in-service performance benefits, for example outstanding mechanical properties and chemical resistance. For more information about Belzona SuperWrap II visit: www.belzona.com/superwrap
Join us for a 30-minute Webinar on 27th March
Main topics:
Concrete maintenance issues – Polymeric materials – Vertical and overhead section repairs – Putting concrete repairs to the test