This technical article was written by Ian Wade, Senior Technical Services Manager, Belzona.
An edited version of this article was published on the Hydrocarbon Processing website.
Click here to read PART 1 of the technical article.
Experimental Procedure
1. Cleavage Adhesion – ASTM D1062
Cleavage adhesion is used to assess the strength of an adhesive bond between two substrates when exposed to cleavage stress.
Belzona 7311 was applied between two identical grit blasted metallic cleavage test pieces to create a fixed bond area of 125mm² of minimal bondline thickness.
The specimen was allowed to cure then attached to a 25kN tensometer using suitable grips. The tensometer then applies a load at a fixed rate of 1.3mm/min exerting a cleavage force on the specimen until bond failure. This test is repeated five times so an average force can be calculated.
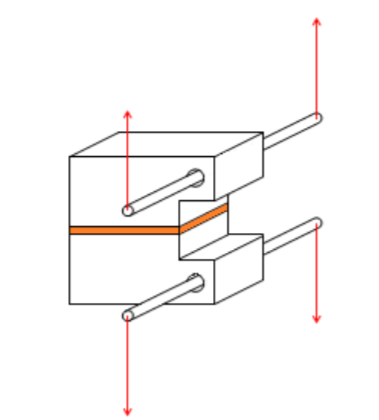
2. Tensile Shear Adhesion – ASTM – D1002
Tensile Shear Adhesion or lap shear adhesion is used to determine the adhesive strength of a material when bonded between two ridged metallic substrates.
Samples are 100 x 25.4 x 2mm and are overlapped lengthwise by approximately 12.7mm and bonded to a minimal bondline thickness with Belzona 7311.
The specimen was allowed to cure then attached to a 25kN tensometer using suitable grips. The tensometer then applies a load at a fixed rate of 1.3mm/min exerting a cleavage force on the specimen until bond failure.
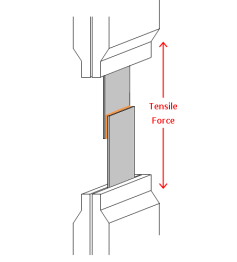
A standard static Tensile shear adhesion test was conducted to determine the mean breaking stress – 24.17 MPa following this 35% of the mean breaking stress value is used as the mean stress in fatigue testing – 35% mean shear stress = 8.461 MPa (24.17 MPa x 35%)
3. Fatigue resistance – ISO 9664
Fatigue resistance is the highest stress that a material can withstand for a given number of cycles without breaking.
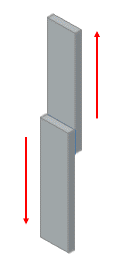
At four different alternating stresses, fatigue testing was conducted at 30Hz until failure:
- 80% = 6.8 MPa (8. 461 MPa x 80%) Stress amplitude cycles between
- 60% = 5.1 MPa (8. 461 MPa x 60%) Stress amplitude cycles between
- 57.5% = 4.9 MPa (8. 461 MPa x 57.5%) Stress amplitude cycles between
- 55% = 4.7 MPa (8.461 MPa x 55%) Stress amplitude cycles between
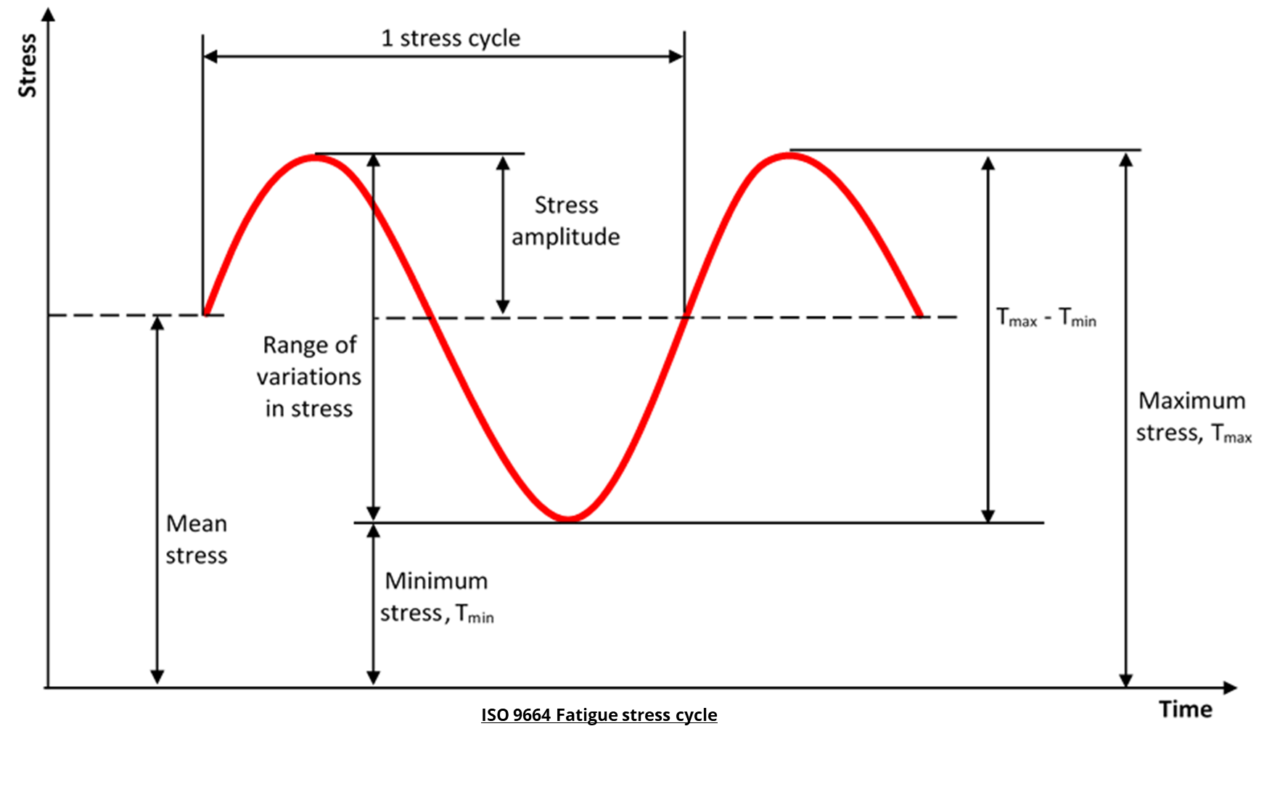
4. Impact Resistance – ASTM D256
Impact tests can be used to assess the toughness of a material, a material’s toughness is a factor of its ability to absorb energy during plastic deformation. Brittle adhesives have low toughness as a result of the small amount of plastic deformation that they can endure. Tougher materials on the other hand can absorb greater energy during fracture and thus, have improved impact resistance.
The Izod impact test allows for samples to be tested in two forms: either ‘notched’ or ‘un-notched’ in our case the testing will be notched which has a V-shaped notch of approx. 2.5mm in depth with a total defect angle of 45° in the centre of a specimen sample with dimensions of 12.7 x12.7 x 65mm. The notch concentrates stress and allows measurement of crack propagation.
Non-standard testing:
5. 3 Point load test
This comparative technique is used to assess the relative flexibility of adhesives when applied to a metallic substrate. In this test a mild steel panel of dissimilar dimensions
Plate 1 550 x 50 x 10 mm thick
Plate 2 225 x 50 x 10 mm thick
are stressed to the point the adhesive fails. The panel is held in position at two points, one at either end of the sample and is gradually stressed at a single point in the centre of the specimen via a hydraulic press as seen in figure 3. The greater the displacement i.e., the further the press travels until failure the more flexible the adhesive. The thickness of the adhesive will influence the degree of flexibility so analysis should be duplicated for repeatability purposes. In the case of this testing at the manufacturing stage the specimens were compressed by hand pressure only, to try and replicate ‘in field’ applications of achieving below the maximum bondline thickness of 2mm.
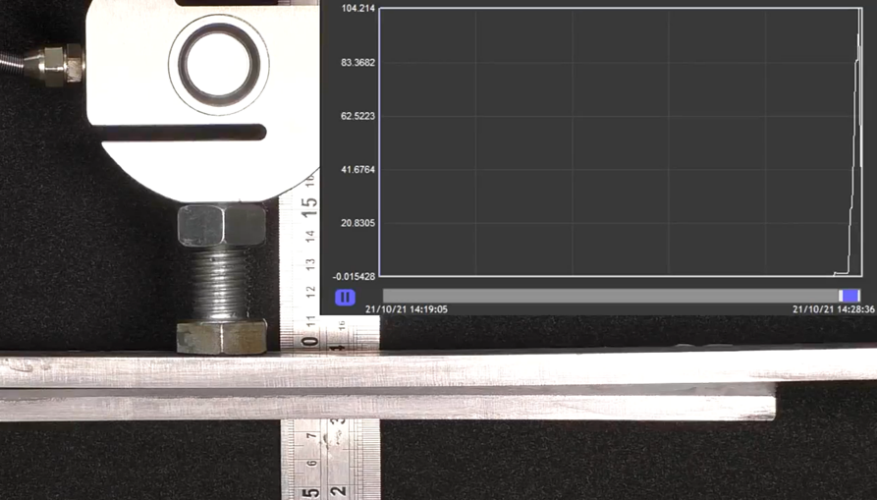
Testing results and discussion
1. Cleavage Adhesion – ASTM D1062
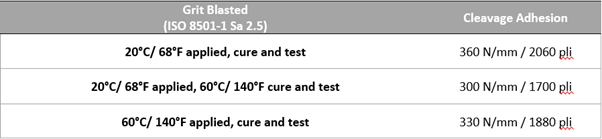
2. Tensile Shear Adhesion – ASTM – D1002
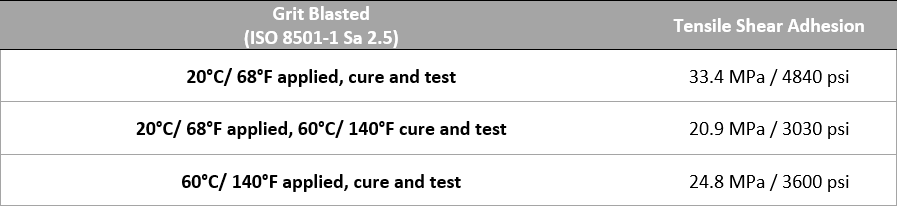
3. Tensile Fatigue Resistance – ISO 9664
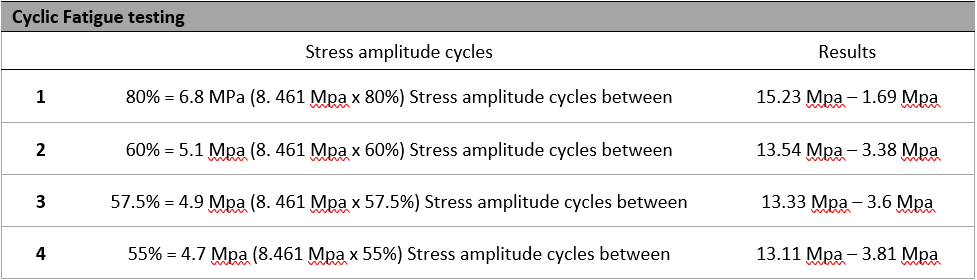
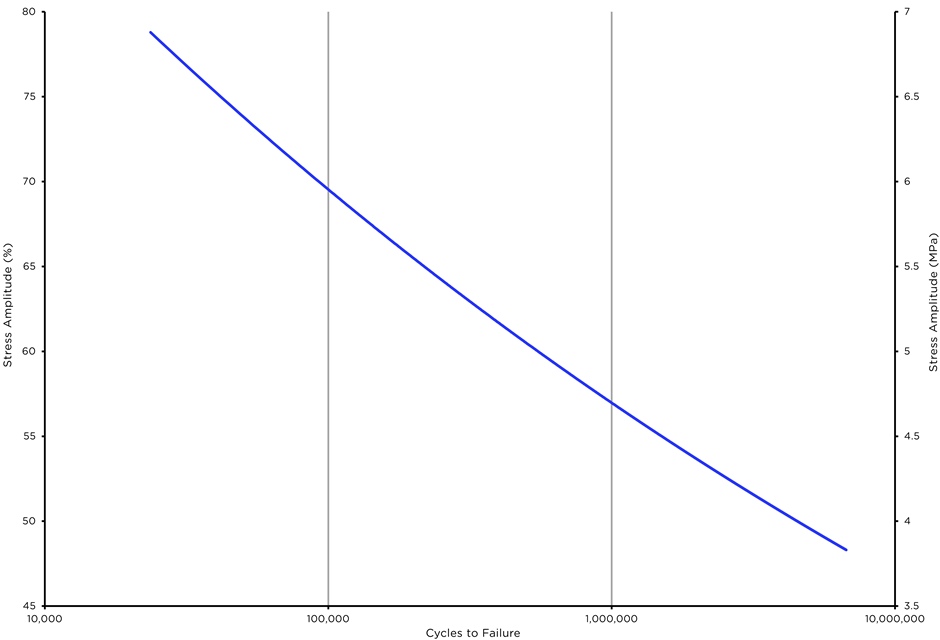
From a mean breaking stress of 35% (8.461 Mpa), Belzona 7311 will survive 106 cycles at 56.6%, with an alternating stress amplitude of ± 4.791 Mpa = 13mpa to 3.67 Mpa
4. Impact Resistance – ASTM D256
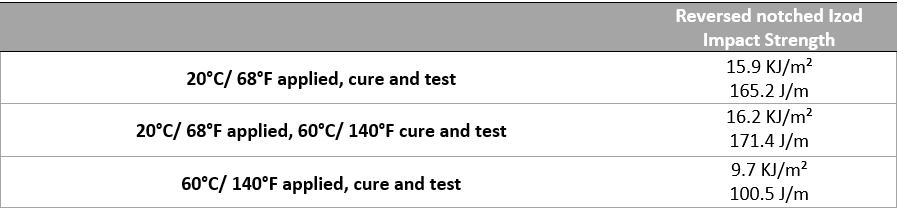
5. 3-Point load test

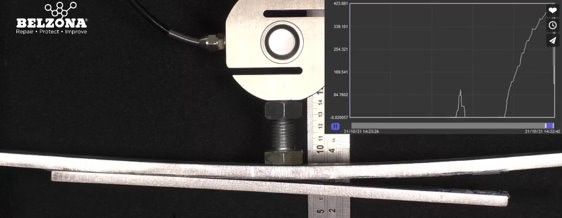
Conclusions
Several conclusions can be drawn from the use of Belzona 7311 as a solution for the repair or maintenance of assets:
- Belzona 7311 offers high resistance to structures that are subjected to forces such as peel, cleavage, vibration, or cyclic loading. These include, but are not limited to, support brackets for fire deluge systems, internal and external fixtures on process equipment, wear pads and wind girders on storage tanks.
- As Belzona 7311 offers an array of additional practical features including ease of application, ability to hold its own structure when placed in vertical applications and superior adhesion to metallic substrates, the toughened epoxy can be used on structural support reinforcements, load transfer supports and metallic staircases and ladders.
- Plate bonding to repair thinning or through wall defects on areas such as pipe/piping, process equipment, storage tank floating roofs and platform decks can utilise Belzona 7311 as it offers high impact resistance and flexural properties.
- Belzona 7311 has been optimised for metal-to-metal adhesion and exhibits an extensive data list with over 20 tests solely based on adhesion. The performance data can be used for Finite Element Analysis (FEA) or simulations to aid in bond designing or qualification of the adhesive in areas that would normally be seen as high risk for standard epoxies such as handrails and walkways.
Interested in Purchasing the Epoxy Structural Adhesive, Belzona 7311?
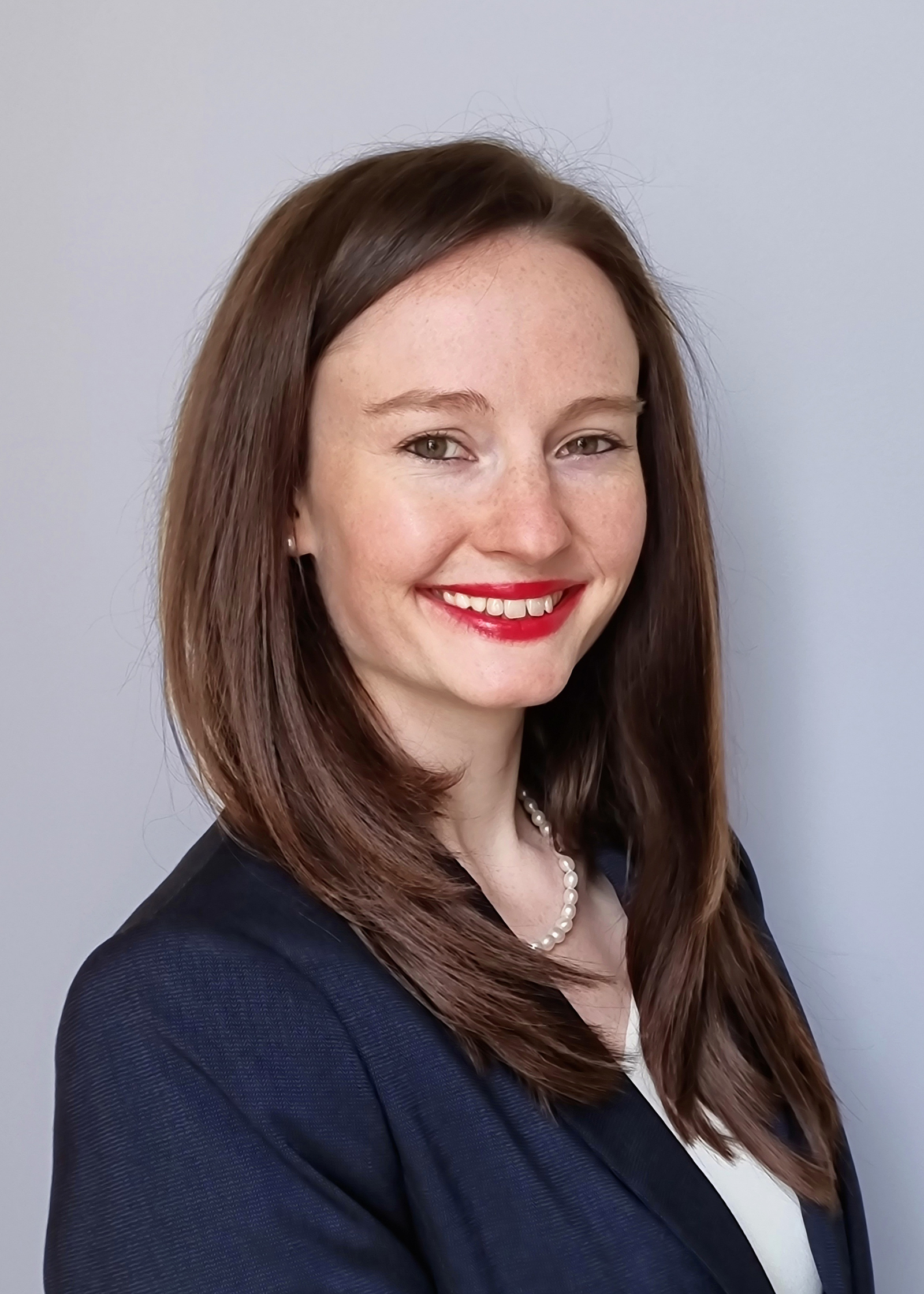
Chloe Hirst is the Senior Copywriter at Belzona Limited and is based in Harrogate, England. She gained a Bachelor’s Degree (with Hons.) in Media and Communications (specialising in Journalism) at Goldsmiths College, University of London. Chloe regularly writes case studies and thought leadership content featuring a variety of different industries, with a special focus on the renewables sector. In both 2023 and 2024, she won the Best Manufacturing Content Creation Specialist (UK) Award as part of Acquisition International’s Influential Businesswoman Awards.