A wastewater treatment facility opts to use Belzona to repair corrosion on a booster tank instead of a costly replacement.
Water and Wastewater Facilities
Water and wastewater treatment plants are key operations in municipal and industrial settings. The harmful materials, chemical compounds, and microorganisms removed from the water during the treatment process create a harsh environment for their operations. The treatment plant’s machinery and equipment need to be fully functional and clean to ensure that water is safe to use.
After decades of research and development, Belzona has been providing the water and wastewater industry with advanced repair epoxy composites safe for potable water, and corrosion-resistant coatings designed to withstand harsh environments. The products are a solution to have on hand since they are suitable for emergency or routine repairs. They cure quickly, repair corrosion and abrasion, are solvent-free, and guarantee safety and environmental compliance while, above all, helping supply water to communities.
Why Wastewater Treatment Facilities Need Corrosion-Resistant Epoxies
A state-of-the-art wastewater treatment facility serving over 3.5 million residents and thousands of businesses and industries in Southern California was faced with a problem that Belzona was available to fix.
The facility was recently honored by the U.S. Environmental Protection Agency with the National Clean Water Act Recognition Award for Outstanding Operations and Maintenance at the Water Environment Federation’s Annual Technical Exhibition and Conference in Chicago. The treatment facility was given the first-place award in the Large Secondary Plant category for “demonstrating outstanding and innovative operations and maintenance practices.” The plant was selected because of its achievements in process control, biosolids management, and pollution prevention.
Yet, the roof of a Booster Tank on the fire suppression system had severe corrosion and large through-hole defects. The tank could not be taken out of service for repair.
The only other option was a full area replacement which would have consisted of offloading the tank via secondary tank rentals, cutting out and disposing of the tank and all associated pipework, fabricating a custom carbon new steel tank, and installing/retrofitting it upon site arrival. This process would have taken many months to complete and cost more than half a million US dollars. However, they chose Belzona’s cost-effective repair epoxy.
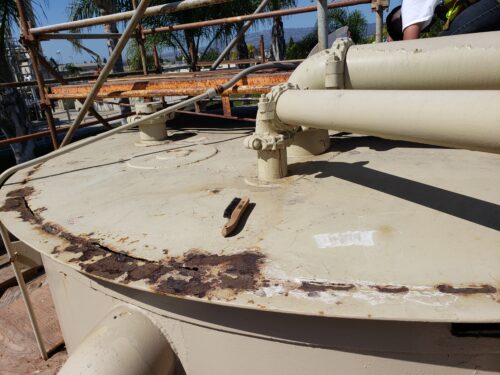
Application of Corrosion-Resistant Epoxy
All the loose, damaged, and flaked metal was removed prior to the application of the Belzona corrosion-resistant repair epoxy. The surface was then prepared using grinders, wire brushes, and high-power pressure washers (vapor blasting) before application of the Belzona materials.
Belzona 1111 (Super Metal) was used to repair any defective areas that had metal loss back to their original wall thickness once the proper level of surface cleanliness was achieved.
Belzona 1111 and all remaining corrosion spots were then top coated with Belzona 5811 (Immersion Grade).
The 10” wide Belzona 9381 hybrid carbon/glass fiber reinforcement sheet filled with Belzona 1982 SuperWrap II resin was installed in three wraps once the Belzona 5811 had been cured for light-loading.
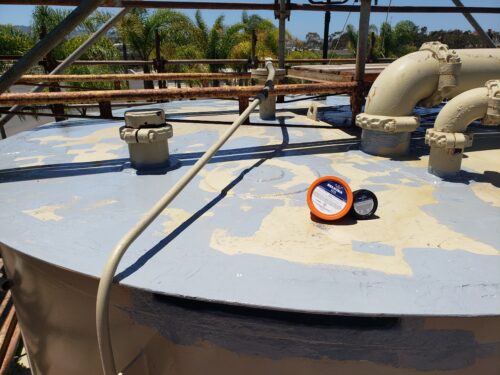
The Belzona 3111 (Flexible Membrane) was utilized to provide a long-term U.V. resistant repair after the Belzona composite system was installed.
Although it was an established customer, the one-on-one relationship is very important. The customer was already discussing another tank roof repair with this same corrosion-resistant repair system.
The results were beyond expectation, and now the customer is looking forward to working with the Belzona distributor on future applications.
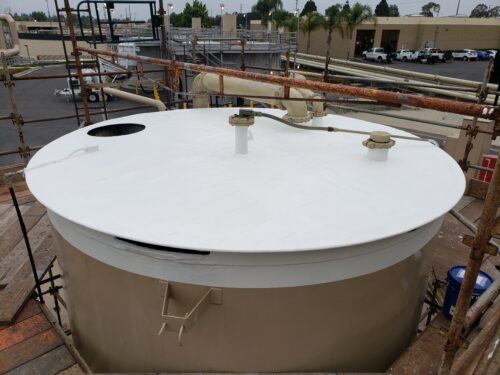
Interested in purchasing Belzona’s repair composites and protective coatings?
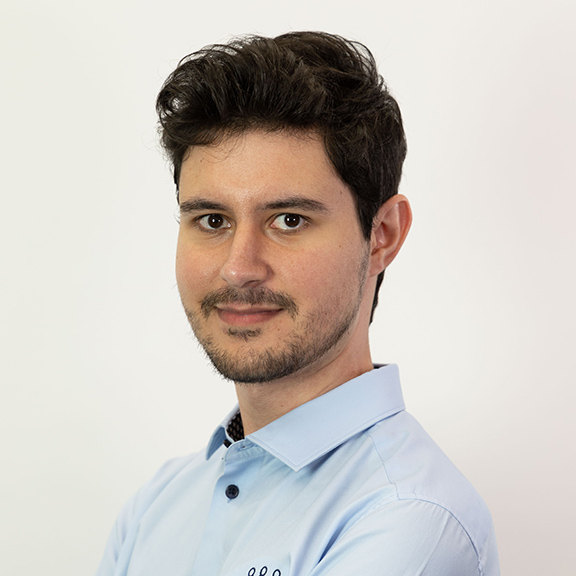
Digital Content Creator, Belzona Inc., Miami, Florida
To repair corrosion at a wastewater treatment facility, identify affected areas, clean surfaces to remove rust and debris, apply anti-corrosion coatings, and replace damaged components. Implementing regular maintenance and using corrosion-resistant materials can prevent future issues.