Water Management is an essential part of many industries, for which clarifier and settlement tanks play a crucial role. Whether it is for a pharmaceutical site, a mine or a wastewater treatment plant, ensuring correct and effective processing is the cornerstone of this sector and any damage to these pieces of equipment can have significant consequences.
Damage can Range from Spalling Concrete to Leaks and Corroded Metal
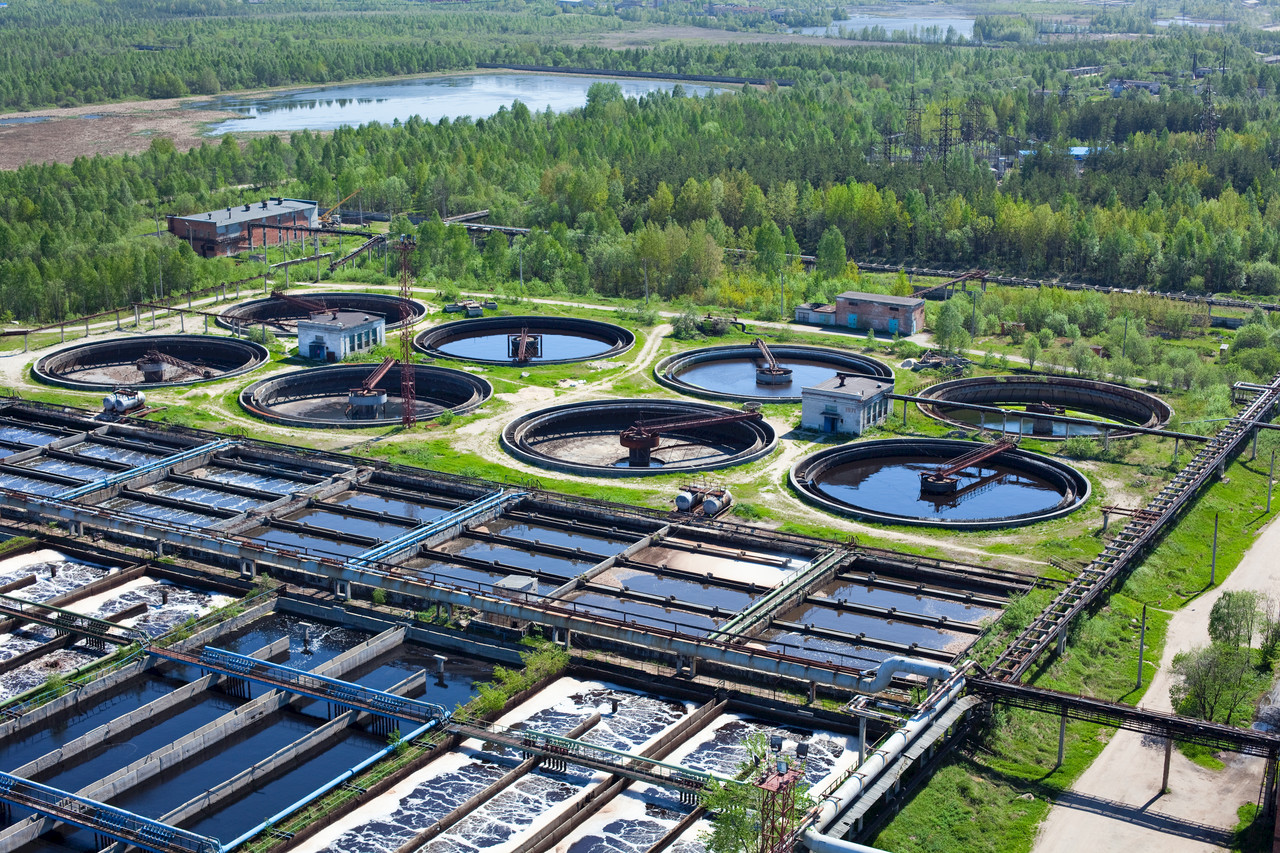
Polymeric Solutions for Settlement and Clarifier Tanks
By their very nature, settlement and clarifier tanks are susceptible to three main issues: corrosion, erosion and chemical attack. Of course, steps are taken to reduce the impact these issues have, simply by controlling their operation. For instance, the flow speed from inlet pipes is kept low. This minimises the amount of turbulence and disruption of the settled and coagulated solids. However, effective operation still cannot completely eliminate these problems.
Whether these problems arise in the form of deteriorated concrete; eroded and corroded metal, or failed expansion joints, the appropriate solutions must be able to withstand the operating conditions and demonstrate long-term resistance to the aforementioned effects. Belzona has been involved with maintenance for clarifier and settlement tanks for over 65 years and therefore, has significant experience in providing long-lasting repair and protective materials.
Below are a selection of three case studies which highlight a variety of different applications and solutions that have proved particularly successful:
WANT MORE INFORMATION?
See Belzona solutions for the Water and Wastewater Industry