Process vessels play a vital role in a variety of industries, particularly within the oil & gas and petrochemical sectors. These vessels often contain high-temperature media within highly corrosive environments. Such challenging conditions lead to issues such as erosion, corrosion and chemical attack, which are exacerbated further by elevated temperatures and entrained solids.
However, traditional repair methods can be both time-consuming and costly, often necessitating dangerous hot work. Belzona’s high-temperature epoxy applications for industrial equipment repair simplify maintenance procedures and extend the life of valuable assets.
This blog post offers step one of a two-step guide for the repair and protection of high-temperature process vessels. First, mending pitting damage using the heat-resistant epoxy paste, Belzona 1511 (Super HT-Metal) and then part two, applying an overcoat of the high-temperature coating, Belzona 1593, to ensure lasting protection against corrosion and chemicals.
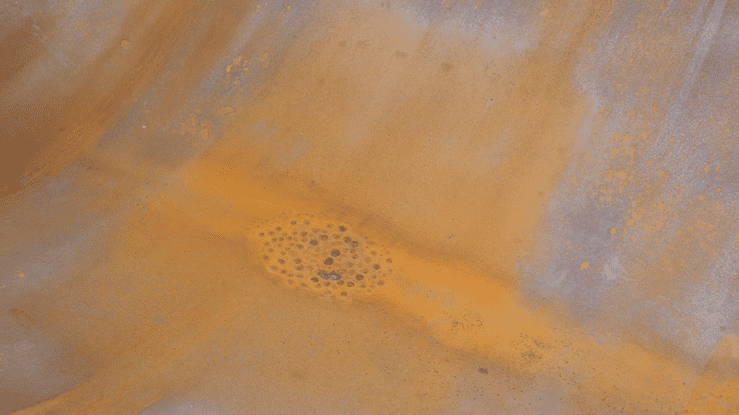
Step-by-Step Guide: How to Repair and Protect High-Temperature Process Vessels | Part One
Before a high-temperature process vessel can be lined, it is crucial to carry out a pitting repair with an epoxy paste. Belzona 1511 (Super HT-Metal) is an ideal choice as it is a heat-resistant epoxy paste, specifically designed to repair and rebuild areas damaged by corrosion or erosion at elevated temperatures. It can withstand immersed service environments up to 150°C (302°F) and is dry heat resistant up to 210°C (410°F). Its excellent chemical resistance and durability make it well-suited to lining high-temperature process vessels.
Step 1: Surface Preparation Prior to Application of Belzona 1511 (Super HT-Metal)
To ensure a successful pitting repair application, proper substrate preparation is essential. First, the surface must be grit blasted to Swedish Standard Sa2½ (near white metal finish) with a minimum profile of 3 mils (75 microns). It is also vital to ensure the soluble salt contamination levels are below 20mg/m2 (2ug/cm2).
Throughout the preparation and application process, environmental conditions should also adhere to those laid out in the Instructions for Use (IFU). This preparation ensures the Belzona 1511 (Super HT-Metal) will adhere strongly to the vessel’s surface.
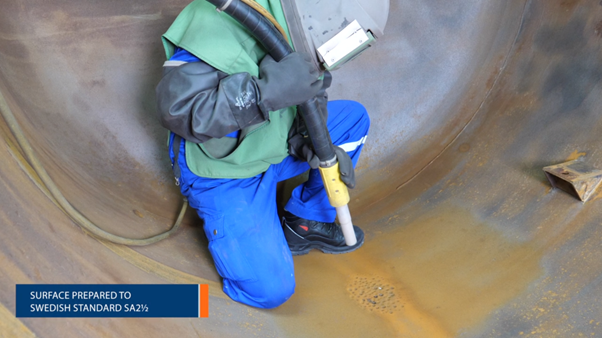
Step 2: Mixing the Heat-Resistant Epoxy Paste
Next, measure out the heat-resistant epoxy paste, Belzona 1511 (Super HT-Metal), at a metric ratio of five parts base to one part solidifier. Mix the two parts thoroughly, using a figure of eight motion, to achieve a uniform streak-free grey colour.
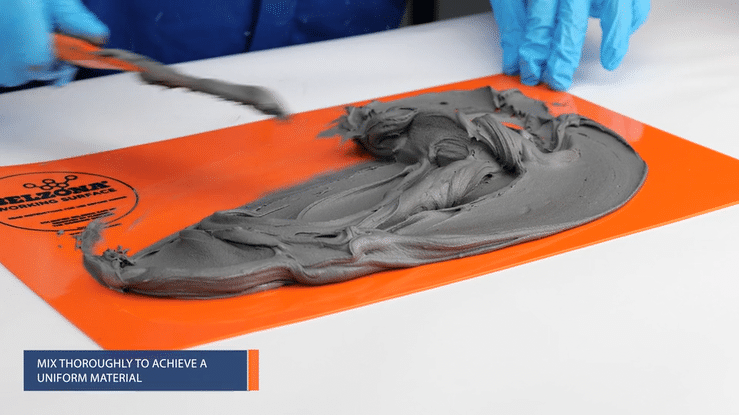
Step 3: Apply the First Coat
Once mixed, carefully use a brush to wet out the substrate with an initial layer, pressing hard into crevices as this helps to prevent air entrapment. Then move on to rebuilding with more product, using a Belzona applicator to restore the surface to its original profile. Ensure the epoxy paste is spread evenly and covers the entire damaged area.
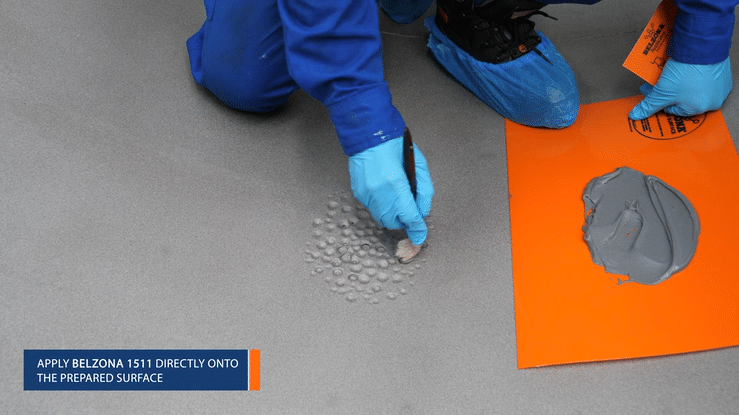
Step 4: Leave the High-Temperature Epoxy Paste to Cure
For the final step in the process vessel application, allow the Belzona 1511 (Super HT-Metal) enough time to cure, forming a strong durable repair. Please note the length of time taken to cure varies depending on application temperature so be sure to consult the IFU for specific timings.
Video: How to Repair and Protect High-Temperature Process Vessels
Frequently Asked Questions
Where can I purchase Belzona 1511 (Super HT-Metal)?
Contact your local authorised Belzona Distributor to purchase Belzona 1511 (Super HT-Metal). To do this, visit the Distributor Finder page on Belzona’s website and use the contact details provided.
What is the application temperature range of Belzona 1511 (Super HT-Metal)?
The application temperature range of Belzona 1511 (Super HT-Metal) is from 10°C (50°F) to 40°C (104°F), making it suitable for a variety of high-temperature environments, including metal pitting repair and resurfacing. It can be applied to both heated and ambient surfaces, provided the surface is properly prepared.
What is the cure time of Belzona 1511 (Super HT-Metal)?
When overcoated with a Belzona high temperature coating, Belzona 1511 (Super HT-Metal) will post cure in service and the relevant cure schedule for the Belzona coating should be followed.
Alternatively, allow to cure at ambient temperature before post curing for at least one hour at minimum 50°C (122°F). Temperature should not be increased at more than 30°C (55°F) per hour.
Alternatively, allow Belzona 1511 (Super HT-Metal) to solidify as below before subjecting it to the conditions indicated.
Temperature | Light Loading | Full Mechanical or Thermal Loading | Immersion in Chemicals |
10°C (50°F) | 72 hours | Post cure required | Post cure required |
20°C (68°F) | 18 hours | 30 hours | Post cure required |
30°C (86°F) | 5 hours | 24 hours | 60 hours |
40°C (104°F) | 4 hours | 6 hours | 8 hours |
Further Reading
How to Repair and Protect High-Temperature Process Vessels | PART 2
Tank Repair: How to Fix Metal Loss in Vessels (with Video)
How to Repair Pitting Corrosion
Contact Your Local Distributor to Learn More About Belzona Solutions for Process Vessels
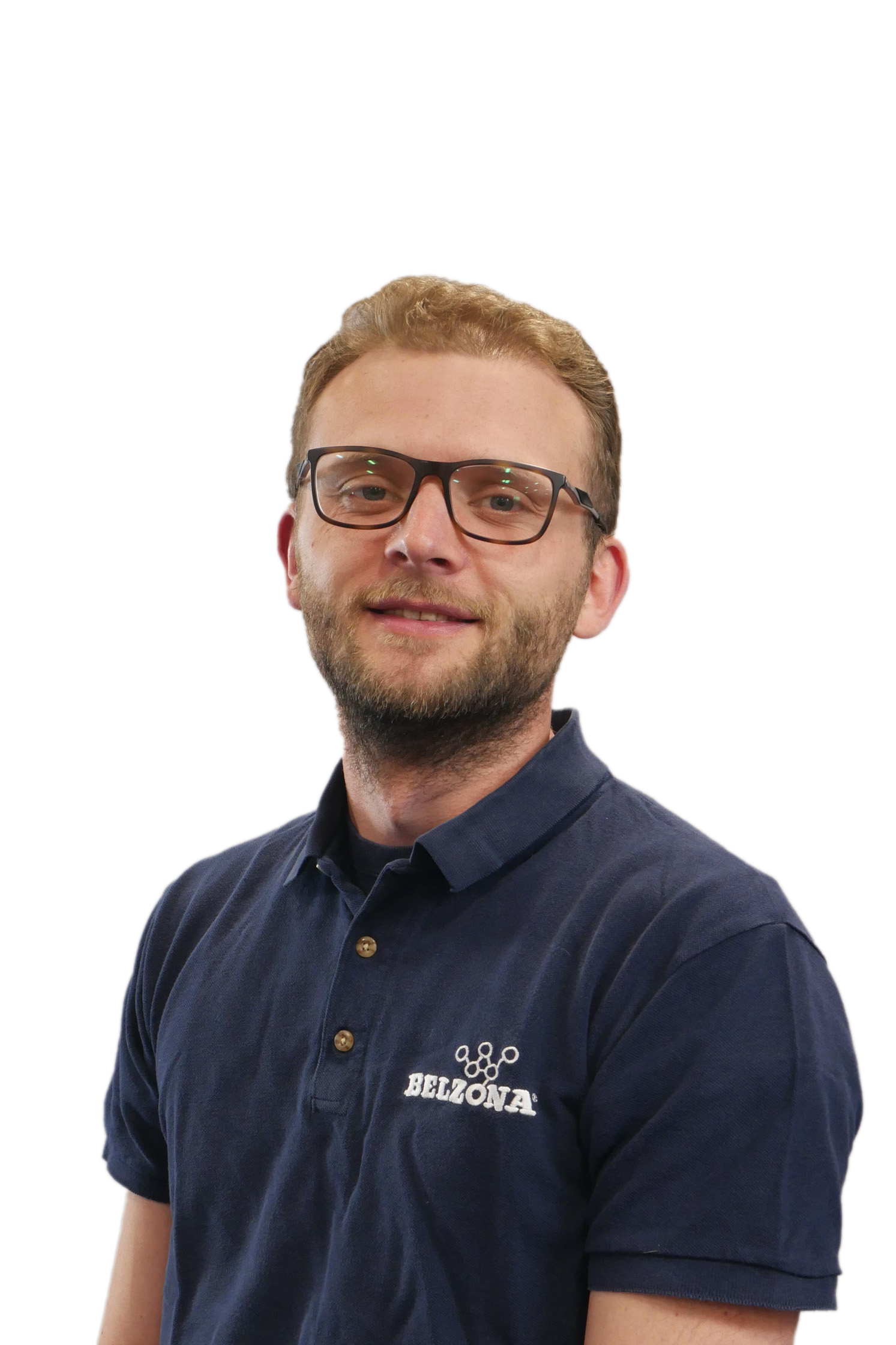
Phil Robinson is an Association for Materials Protection and Performance (AMPP) Coating Inspector Program (CIP) Level 3 Inspector, with nearly 20 years of experience in executing major Belzona applications worldwide, both onshore and offshore. He currently holds the position of Applications and Training Director, based at Belzona’s Headquarters in Harrogate, UK. His expertise spans multiple industries, with a primary focus on the preservation of process equipment in the oil and gas sector.
In addition to his field experience, Phil plays a key role in the development of Belzona training programs, supporting Belzona’s global Distributor Network. He has also developed numerous application procedures and techniques to enhance the effectiveness of the product range. For example, in 2024, Phil was one of the key developers behind Belzona SF6-FIX, a sulphur hexafluoride (SF₆) leak solution that can be applied online, and without specialist tools.
With a passion for troubleshooting and implementing technical solutions, Phil excels at identifying and resolving complex challenges utilising protective coatings and repair composites.