Turbo Separators frequently found in industries such as Pulp and Paper and Waste to Energy…
…are developed to remove products from their packaging, releasing them for recycling or disposal. Through a combination of centrifugal forces, self-generated air flow, and mechanical action, up to 99% of dry or liquid materials can be removed from their packaging. When compared with other methods, the turbo separator achieves higher separation efficiencies with lower power consumption which results in reduced running costs.
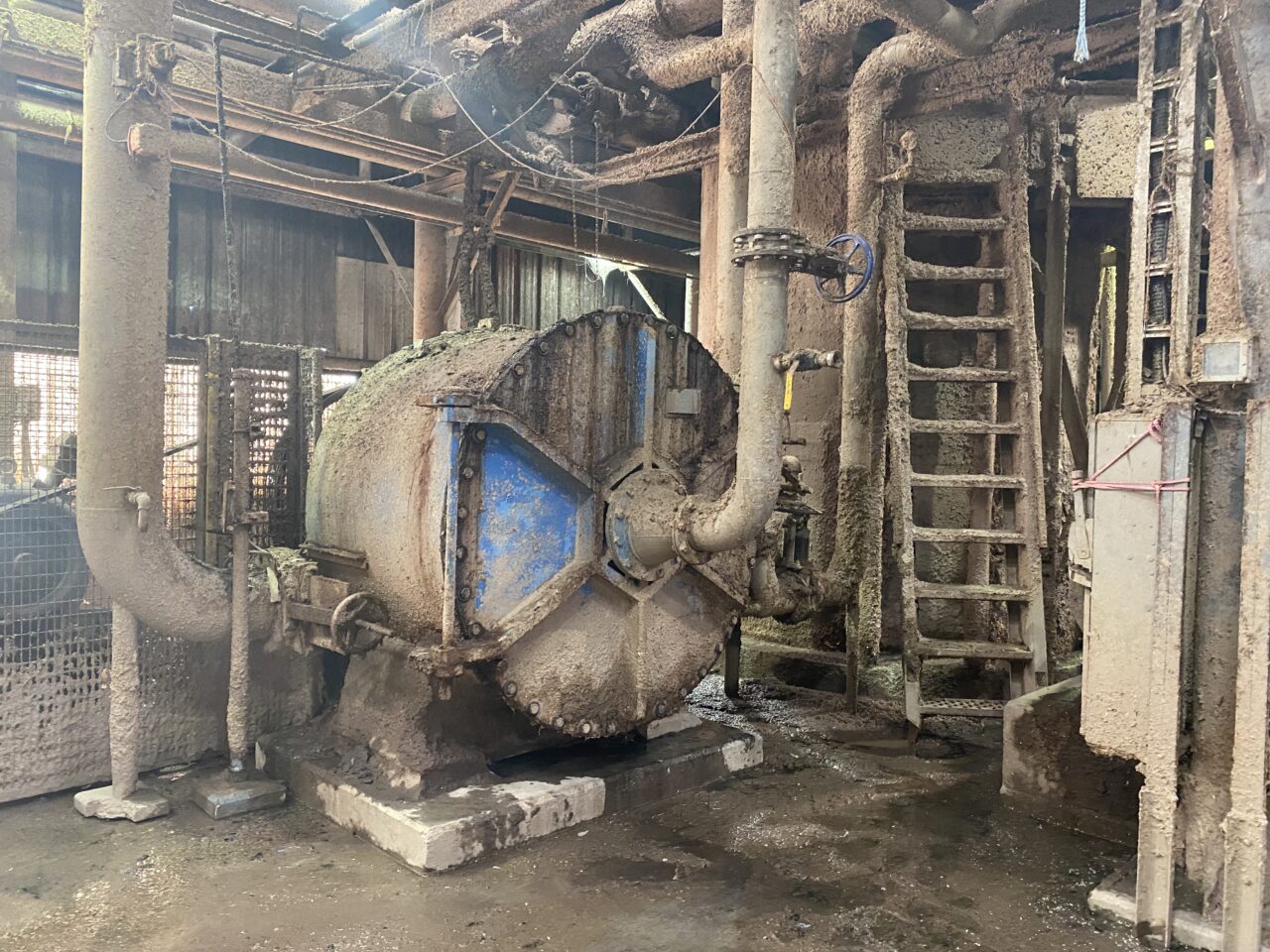
The separator unit itself is lined with thick tiles and has a hard-wearing grouting compound applied over the joints between the tiles, and below the tiles to adhere to the harsh substrates that pass through.
Due to the nature of this abrasive environment in which they operate, over the years, this grouting compound wears away leaving the joints unprotected and in some cases, the tiles disbanding from the substrate. The process of replacing tiles on a turbo separator can be both costly and a time-consuming operation in which plants would need to shut down. In addition, in these environments, surface preparation can also be an issue and contamination is common. As a result, they cannot always be fully cleaned or ideally profiled as required for many repair materials. The desire to deal with adverse application conditions creates a need, not only fast curing but also a surface-tolerant material that can withstand abrasion.
A Year on From Launch- A Fast Curing Abrasion Resistant Repair System
Belzona 1818 is a fast curing, surface tolerant, abrasion resistant system ideal for patch repairs on surfaces subject to high erosion and abrasive environments, the product was designed with built-in surface tolerant technology to bond firmly with steel substrates with minimum surface preparation and can be applied and cured underwater. Building on existing knowledge of fast-curing materials and high erosion resistance expected from the Belzona 1800 series, Belzona 1818 seemed like the next step in Belzona’s portfolio of existing innovative products. You can read more about the opportunities for Belzona 1818 in our previous blog post.
In addition to its anticipated application areas such as chutes, hoppers, slurry pumps, and grinding mills, since its launch in September 2020, Belzona 1818 has also seen success in the repair and protection of turbo separators.
Rezitech, Exclusive Distributor for Australia Leads The Way
Leading the way with this application was Rezitech Services Pty Ltd, exclusive Distributor of Belzona products in Australia, who completed their first application on a turbo separator using Belzona 1818 for a Brisbane-based recycling company. Rezitech has been repairing and protecting the inside surface of separators for many years; however, this was the first time they had used Belzona 1818.
The turbo separator at the client’s recycling plant was lined with basalt tiles due to their outstanding hardness and wear resistance; the tiles were bonded in place using a special grouting compound.
After several years in operation, the compound had degraded due to the highly abrasive service conditions, and this had accelerated the wear rate on the tiles, resulting in the separator becoming less effective and prone to breakdowns.
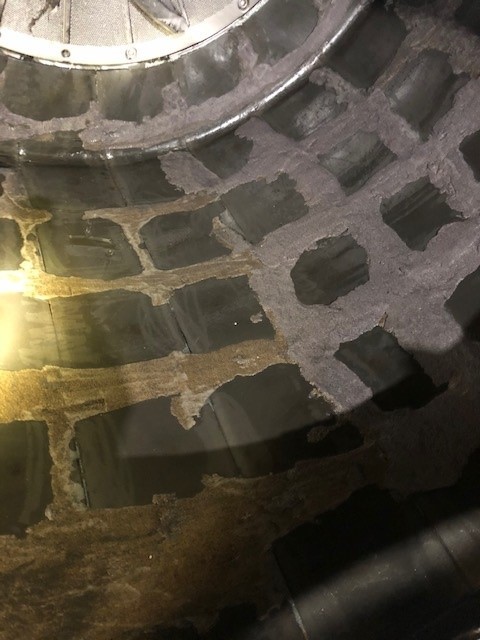
In previous turbo separator repairs, the application team from Rezitech used Belzona 1812, which had performed very well; however, with the release of the Belzona 1818 and its additional benefits of surface tolerant and faster cure, the decision was made to use this product instead as it was better suited for this application.
Quick Turn Around Required in Three Day Shutdown
The application project was scheduled during the recycling plant’s three-day shutdown and began with plant employees opening the separator and washing out the left-over wet pulp. The Rezitech team then took over and proceeded to dry up the residual water with cloths to allow the diamond grinding of the surface to begin.
After the diamond grinding was completed, the dust it had created was washed out of the separator as Belzona 1818 is surface tolerant, and the application would not be affected by small amounts of surface water. Next, the team applied the Belzona 1818 to repair and replace the damaged grouting between the Basalt Tiles. Rezitech used a total of 27x1kg units to complete the application project.
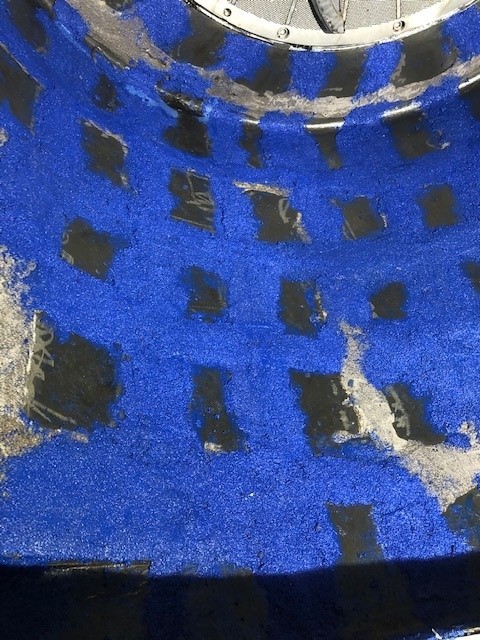
Belzona 1818 was more suited to this type of application as it was easier to apply on both vertical and overhead sections compared to Belzona 1812, and due to the faster curing time of the product, the Turbo Separator was returned to service well within the given time frame.
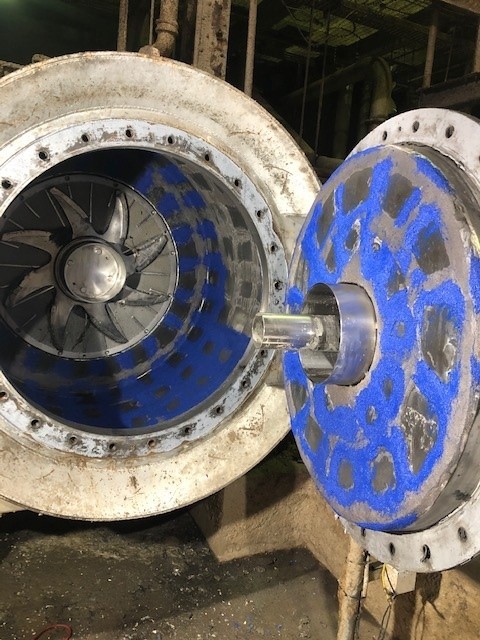
Rezitech has been repairing and protecting Turbo Separators with Belzona for the last three decades; over this time, we have gained valuable experience and knowledge on this type of repair project. With the recent release of Belzona 1818 and the improved benefits it provides, we are now able to increase our efficiency, even more, much to the delight of our clients
Andrew Petroff, Sales Manager at Rezitech
U.S. Customers Also Taking Advantage of Innovative Repair
Across in the U.S, Oklahoma-based Belzona Distributor, Belzona Industrial Solutions LLC, has also been utilising this innovative repair at a paper recycling plant in Texas, USA.
During regular operation, a large metal object had found its way into the main chamber of their turbo separator, causing significant damage across an area of approximately 4ft x 3ft. The replacement of the damaged tiles and surrounding grout would have been very time-consuming, and as the plant only shuts down for just 12 hours each month, a speedy and effective repair solution was needed.
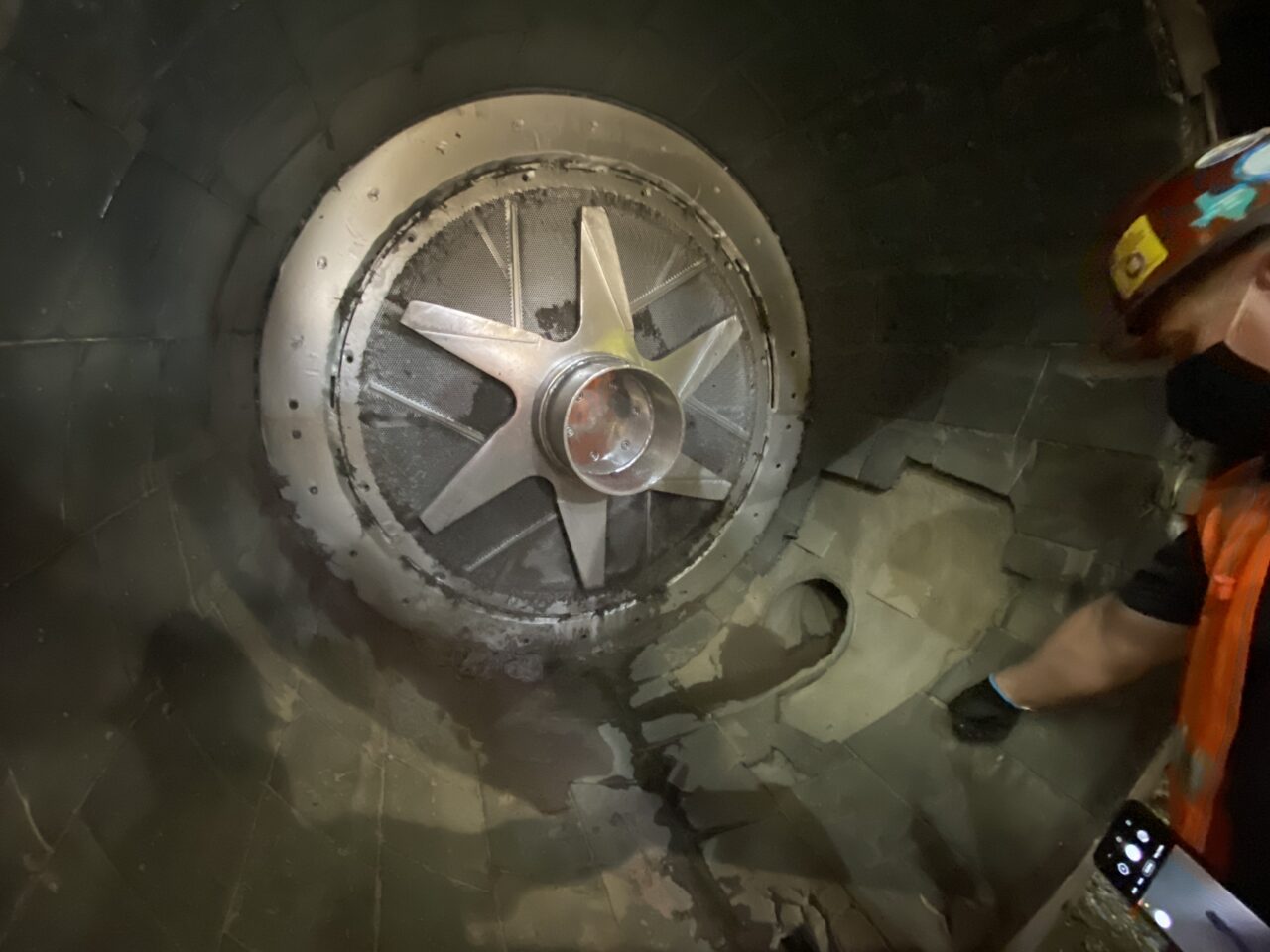
Similar to the application at the recycling plant in Brisbane, the customer was already familiar with the Belzona 1800 series of products as they had previously used Belzona 1812 and therefore had no hesitation in selecting Belzona 1818 for this urgent repair project. First, the damaged and loose tiles were removed, followed by abrasive blasting to the affected area to create a suitable profile for the application. Belzona 1818 was then applied to the damaged area to rebuild the original profile and provide an abrasion-resistant coating. The application was completed in less than 7 hours, and the equipment resumed operations with no delay.
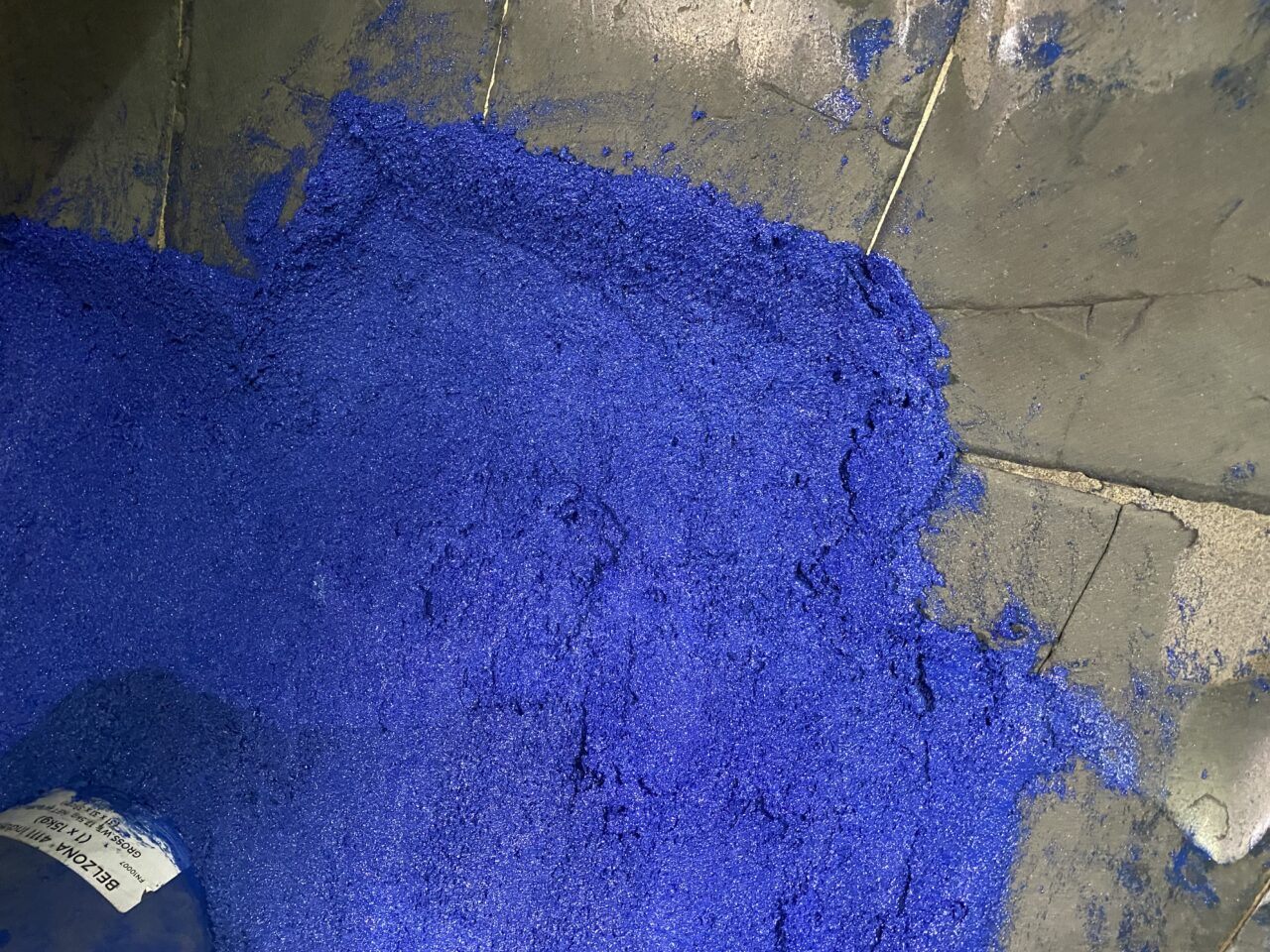
Based on these recent application successes, it is safe to say that Belzona 1818 can be utilised by maintenance engineers globally to repair their turbo separator equipment, with the major benefit of minimal downtime and as a result, reduced costs.
how about cyclone seprator of pulp industries can we apply 1812
Hello Navid, thank you for your comment. For more information about this solution and to receive a technical answer to your question, please use the following link to contact your local Distributor – https://belzona.com/en/about/disfinder.aspx. Best regards, Belzona Team.