*TRANSCRIPT FROM MANUFACTURING TODAY MAGAZINE*
Though not necessarily a household name in the consumer market, Belzona is widely recognized for its advanced polymer technology in myriad industries – oil and gas, marine, renewable energy, waste-to-power, petrochemicals, steel, and wastewater treatment to name just a few. Now, though, it’s turning its attention to plant-based chemicals as a source of sustainable polymer products.
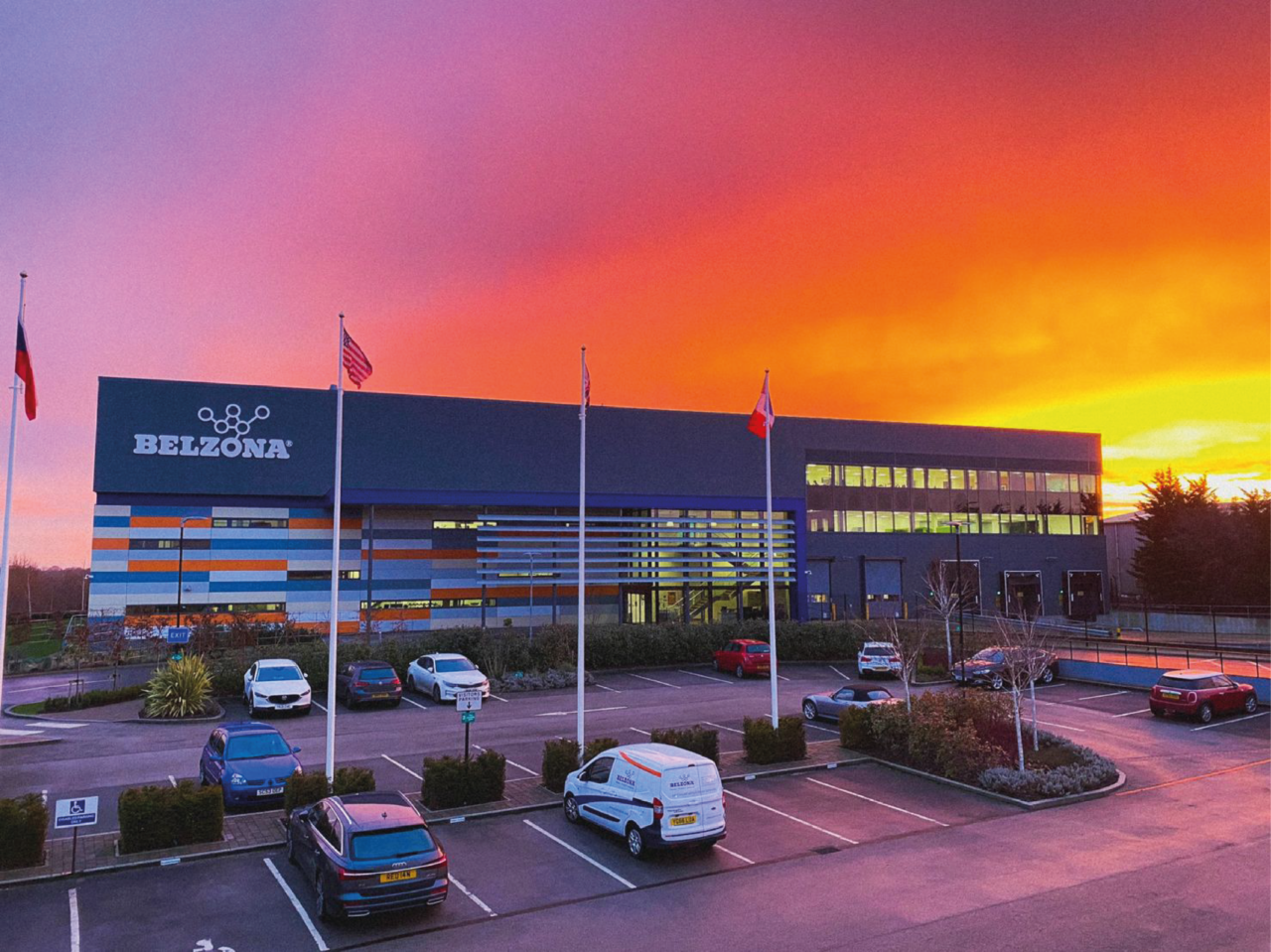
Having specialized in combating erosion, corrosion, and chemical attack for 70 years, Belzona has become the go-to provider of innovative, high-performance polymer coating solutions, allowing its industrial partners to repair and protect a wide range of machinery, buildings, and equipment.
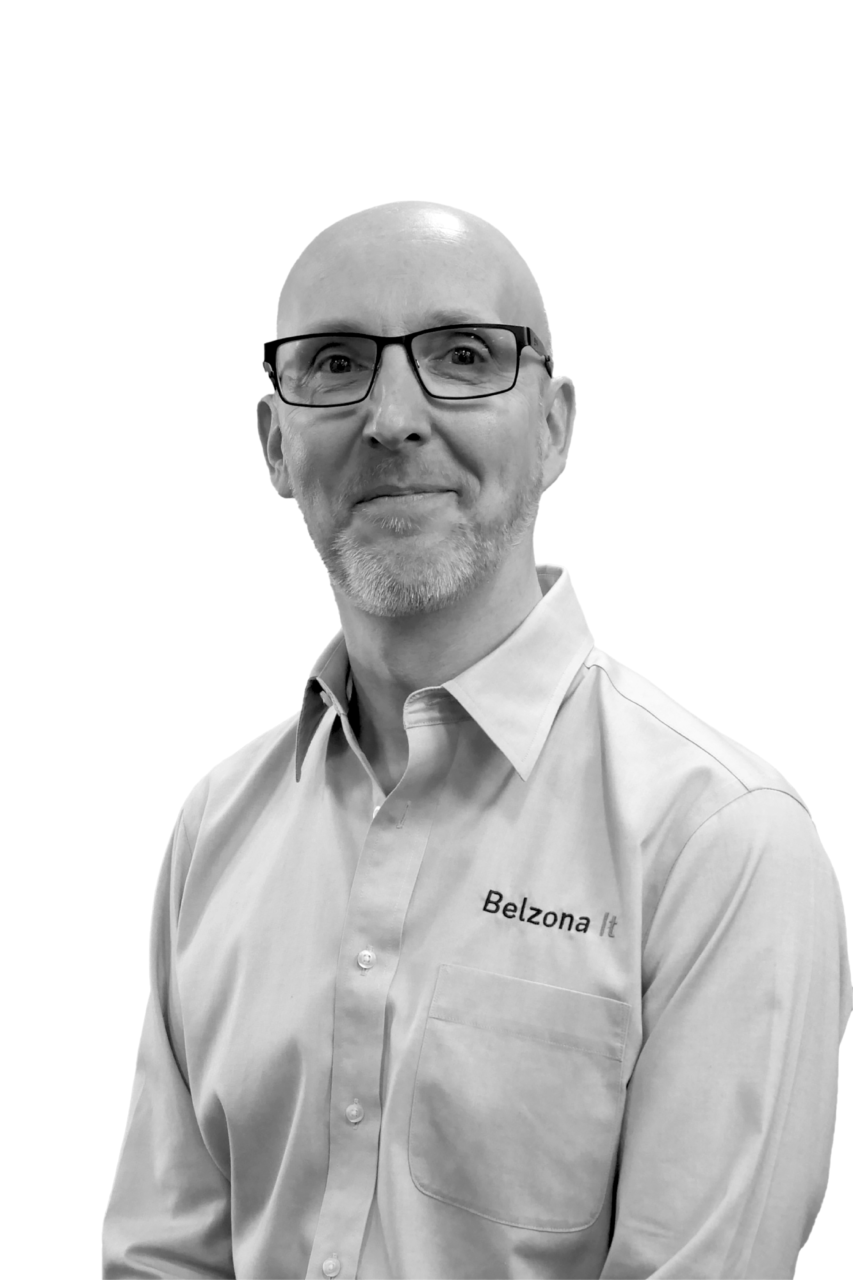
Offering us an insight into the chemistry and methodologies employed behind-the-scenes is Jevon Pugh, Research and Development Director at Belzona. “Our core technology is polymer chemistry,” he begins. “In our laboratories, we design, formulate, and manufacture a range of coating solutions, enabling our industrial customers to protect assets that would otherwise suffer from the effects of aggressive service conditions. For instance, slurries and strong chemicals cause abrasion and corrosion as they pass down pipes and through production equipment, and factors such as these as well as elevated temperatures mean that conventional protective coatings won’t survive. Therefore, companies must turn to a high-performance polymer solution to appropriately protect their assets – and that’s where we come in.
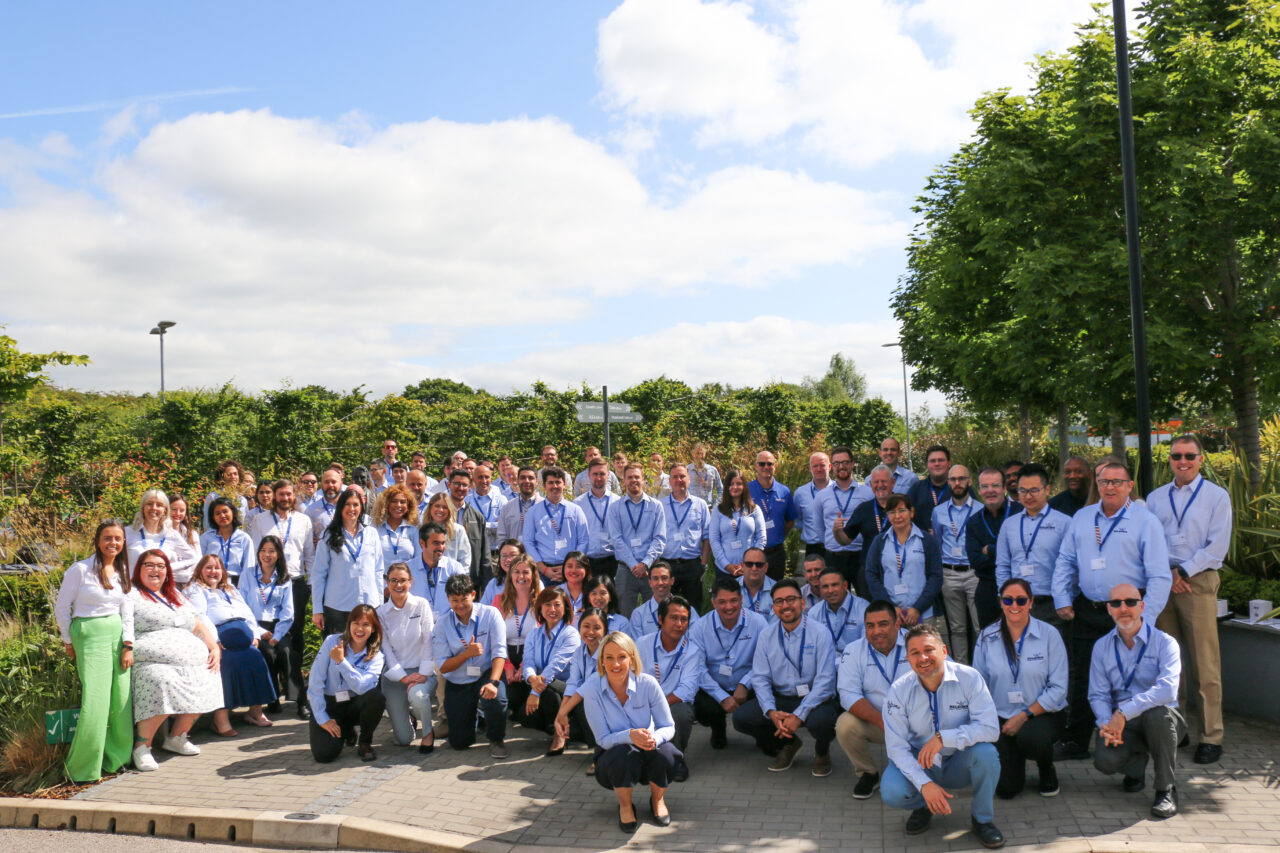
“The Company was born in 1952 off the back of pioneering zinc-rich corrosion protection technology,” Jevon adds. “It could be applied to all kinds of steel structures, creating a polymer-zinc barrier that would resist aggressive corrosion and protect the integrity of the steel beneath it. Belzona then developed a range of polymer coatings and repair pastes – the original being Super Metal which has been widely copied over the years – for the repair and rebuilding of assets, before then coating and protecting them against any future damage. These metallic pastes can be applied onto a damaged or worn surface in thick layers, allowing it to be reshaped and reformed back to its original profile. The paste then sets rock hard, almost like the steel itself, and brings that original asset back to life.”
Testing Capability
Since then, the Company has gone on to develop high temperature immersion linings, which are widely used in the oil and gas industry on structures that have to contend with water, steam, oil, sand, and chemicals throughout their processing life. Belzona has also developed composite repair systems made from densely woven structural fabrics made from glass fiber or carbon fiber, that can be used to return strength and fortify compromised pipes or other structures.
“Composite repair is a rapidly growing market,” says Jevon. “For that niche, we have a brand called SuperWrap II, which effectively creates a composite pipe that surrounds the original steel pipe. When a steel pipe is damaged or corroded, perhaps through chemical attack, then it will ultimately lose strength and can, in the worst cases, leak. This can result in entire plants or facilities being shut down for extensive periods of time. This is a major issue, and one that could result in millions of dollars being lost every day. To protect our customer’s assets, we developed a solution that restores the integrity of that pipe via a composite wrap; bringing back its original strength and improving it, through increased rigidity, corrosion resistance and chemical resistance.”
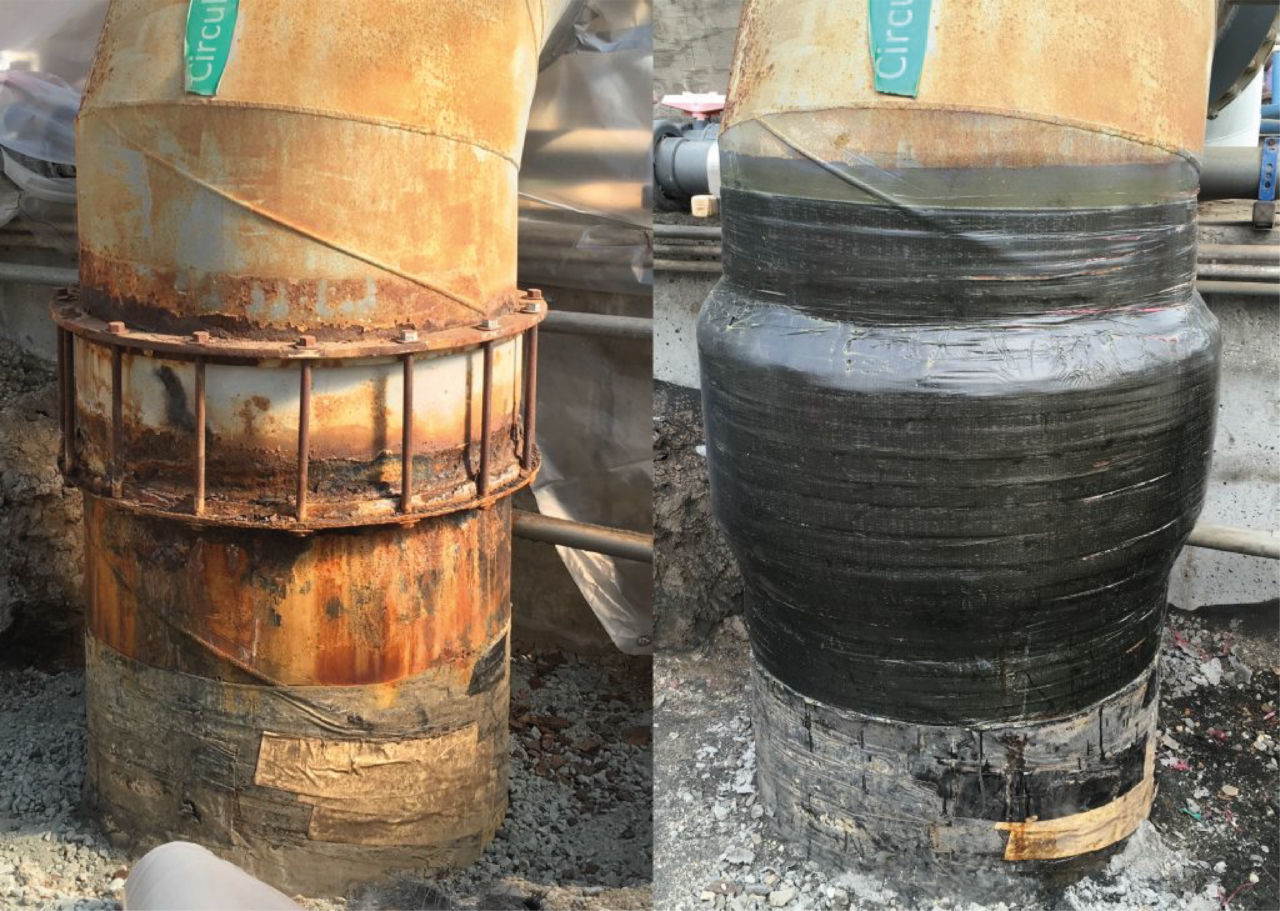
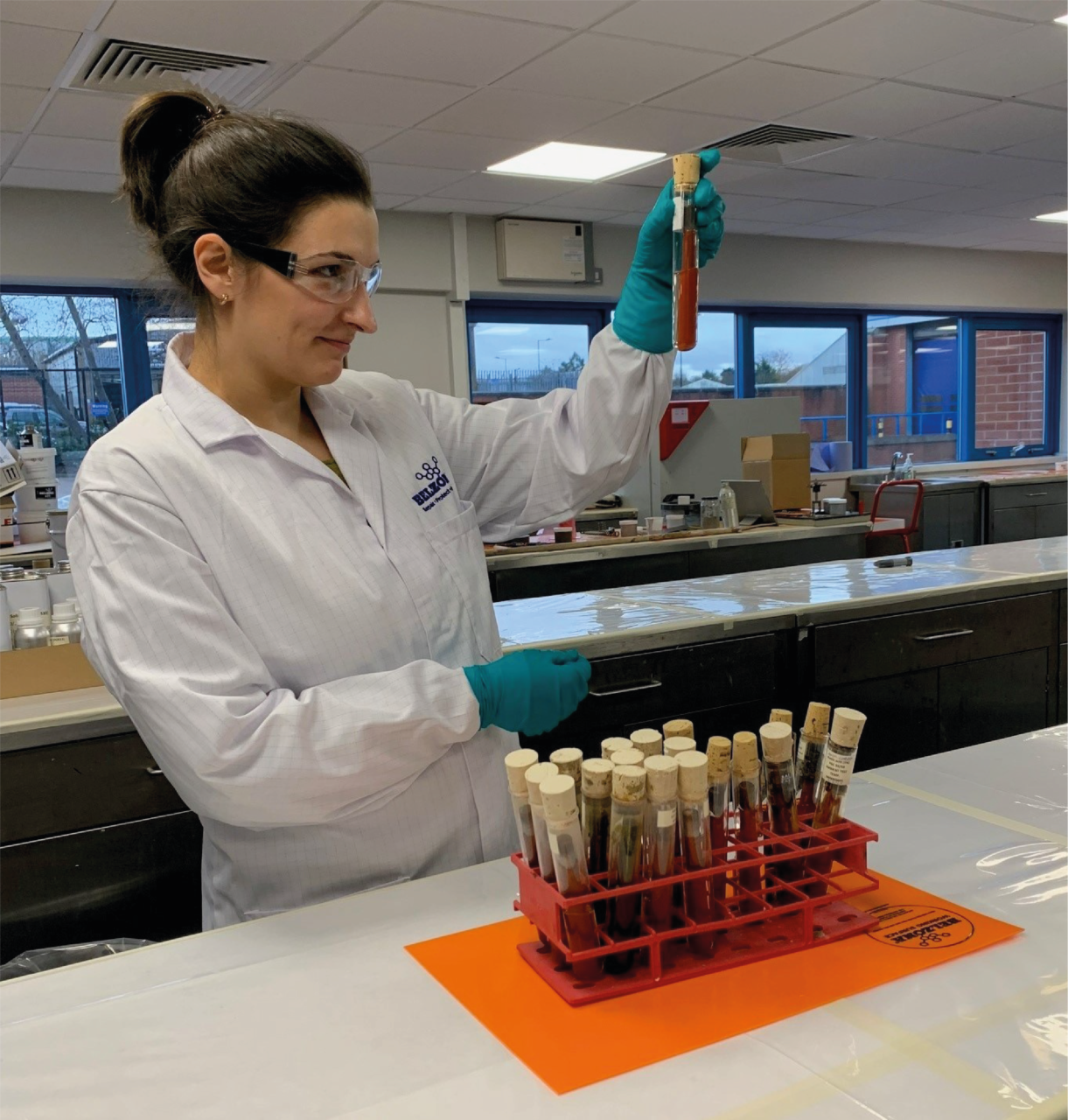
To create market-leading products of this kind and supply them to global industries, a lot of research and development (R&D) must take place. To that end, Belzona has two R&D facilities – one in Harrogate, UK and the other in Miami, US. Both of which also possess manufacturing capabilities, which enables the Company to not only design, formulate, and test its polymer solutions, but also produce them on a commercial scale.
“Going back to my chemist roots, it’s wonderful to walk through our facilities and follow the journey of our products,” explains Jevon. “Our chemists are involved at all stages, through design, development and manufacture. You can see people working at the metaphorical drawing board all the way through to those supervising the first batch of a new polymer solution being made. As part of the development and manufacturing process, we focus on sourcing materials that are commercially available, can provide the requisite performance, are of the highest quality, and which are as safe and sustainable as possible. By working with different chemical manufacturers, who create the building blocks of these solutions, we’re able to apply our scientific knowledge and expertise, creating an easily appliable, safe, high-performance polymer product.
“A key step in the development process is testing,” he continues. “We have fully equipped testing laboratories at our UK and US sites, allowing us to study and characterize the performance of our products, and thereby optimize our formulations. We put every solution through an extensive programme of testing – which is defined by the intended end-use for the product. For example, abrasion resistance testing for a slurry pump lining, or weathering testing for an exterior anti-corrosion coating – the majority of which is carried out in-house. It is Belzona’s investment in this testing capability which sets us apart from most competitors.”
PART 2 of the interview will be published next week.
Please click on the following link to read the full article: https://issuu.com/schofieldpublishingltd/docs/mt202?fr=sNGU5OTUxOTEwMjM
Interested in purchasing Belzona’s repair composites and protective coatings?
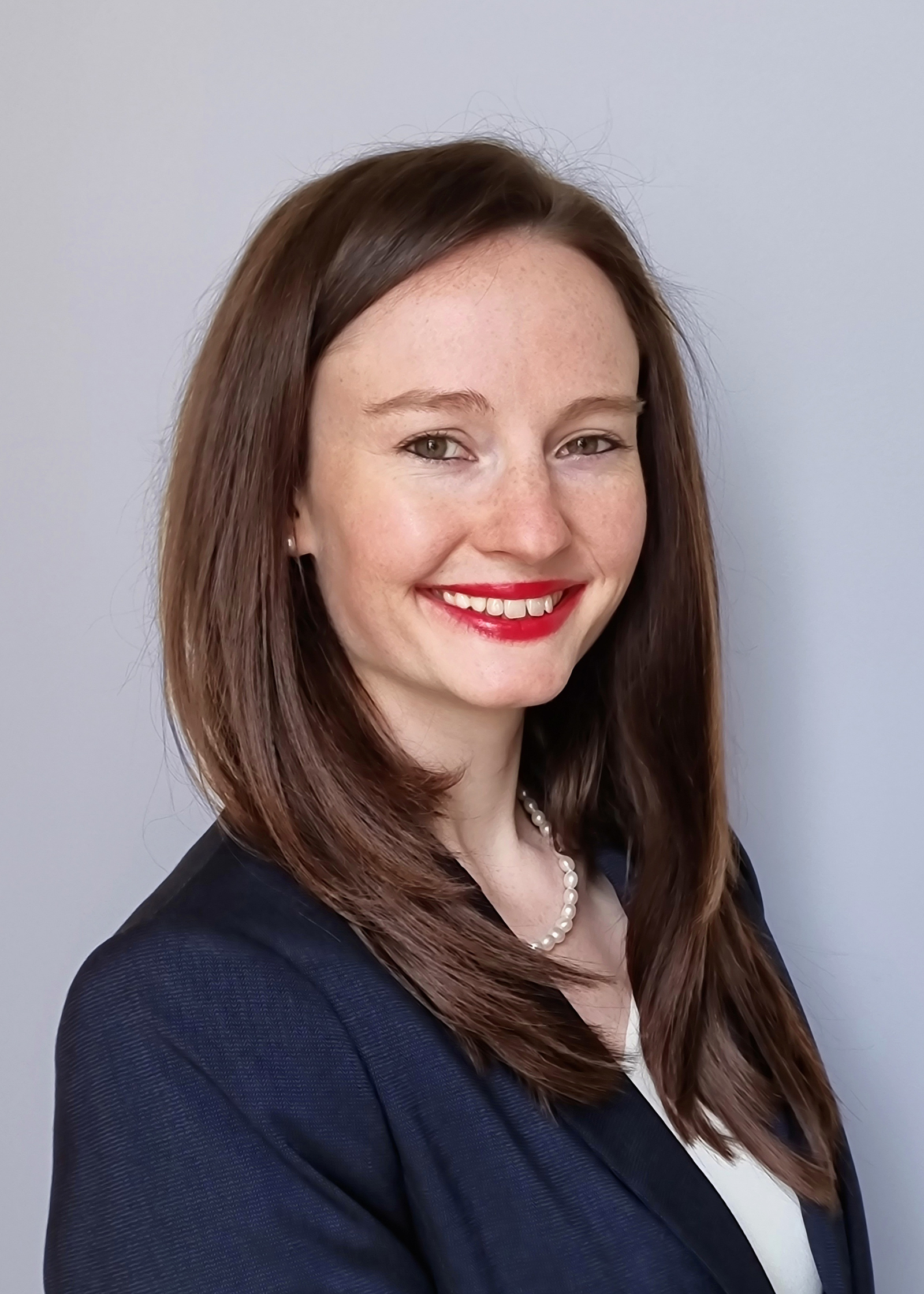
Chloe Hirst is the Senior Copywriter at Belzona Limited and is based in Harrogate, England. She gained a Bachelor’s Degree (with Hons.) in Media and Communications (specialising in Journalism) at Goldsmiths College, University of London. Chloe regularly writes case studies and thought leadership content featuring a variety of different industries, with a special focus on the renewables sector. In both 2023 and 2024, she won the Best Manufacturing Content Creation Specialist (UK) Award as part of Acquisition International’s Influential Businesswoman Awards.