- Video: Welding Risks vs Cold Bonding
- Introduction to Metal Bonding
- What is Cold Bonding?
- Why Use a Metal Adhesive Instead of Welding?
- Common Equipment Repaired with Metal Bonding
- Understanding Surface Preparation
- Step-by-Step: How to Use a Metal Adhesive for Metal Bonding Repairs
- Extend the Life of Your Equipment with Cold-Applied Metal Bonding Adhesives
- Frequently Asked Questions
Video: Welding Risks vs Cold Bonding
Introduction to Metal Bonding
When corrosion or cracking puts the integrity of industrial equipment like deck plates of marine vessels and offshore structures, storage tanks, pipes and pipelines at risk, metal bonding can be used as a quick, effective, and long-lasting repair solution.
Metal adhesives, particularly epoxy systems, have long been trusted in industrial environments for their strong adhesion to metal, high mechanical performance, and simple in-situ application. When used to bond reinforcement plates or structural patches, they eliminate the need for welding, reduce downtime, and extend the service life of critical equipment. In this guide, we’ll share the process of performing an industrial-strength repair with a metal-to-metal adhesive, perfect for industries like petrochemical, power generation, and water treatment. Whether you’re dealing with wall thinning, cracks, or even complete through-wall defects, this repair method offers a high strength, cold-applied alternative to traditional hot work.
What is Cold Bonding?
Cold bonding refers to the process of joining two parts or materials without the use of heat. Unlike traditional methods such as welding, which use high temperatures from electric arcs or gas flames to melt and fuse materials, cold bonding uses an adhesive to create a strong, lasting bond. Belzona’s cold-curing metal bonding composites make it possible to achieve this connection without the risks or complications associated with heat.
Why Use a Metal Adhesive Instead of Welding?
In many situations, cold bonding plates with a metal adhesive as a repair method can be used over traditional welding or mechanical fastening, offering several key advantages:
- No hot work required – Ideal for hazardous or flammable environments.
- 100% surface contact – Bonding with metal adhesives provides full-area support.
- Bonds dissimilar materials – Effective where welding would be impractical or unsafe.
- Even stress distribution – Lowers the risk of failure due to stress concentrations.
- Absorbs vibration – Enhances durability in dynamic or rotating equipment.
- Easier application – No specialist welding skills required.
- Prevents distortion – Cold bonding avoids heat-affected zones that could compromise the structure.
- Chemical resistance – Many Belzona adhesive systems resist acids, alkalis, hydrocarbons, and salt spray.
For industrial repairs, Belzona offers a proven range of metal bonding epoxy adhesives, including:
- Belzona 1111 (Super Metal) – A multipurpose epoxy composite used for rebuilding and bonding metal components, offering high compressive and adhesion strength.
- Belzona 7311 – Designed for structural bonding of metallic plates. Ideal for load-bearing applications and certified to withstand high mechanical stress.
- Belzona 4301 – Formulated for bonding situations where maximum chemical resistance is required.
- Belzona 1161 (Super UW-Metal) – Designed for metal bonding in oil-contaminated or underwater conditions.
Common Equipment Repaired with Metal Bonding
Metal plays a key role in industrial equipment and is an ideal material for bonding with industrial-grade adhesives. Some common examples include:
- Deck plates of marine vessels – Reinforce corroded or weakened structures without welding, especially in high-risk or restricted-access zones.
- Storage tanks – External wall loss repairs using patch plates.
- Pipework and elbows – Plate bonding and leak sealing.
- Heat exchangers – Plate reinforcement and tube sheet repairs.
- Clarifiers and digesters – Patch corroded steel panels.
- Pump casings and housings – Structural restoration.
- Stacks, scrubbers, and ducts – Corrosion-resistant bonding in chemical environments.
- Steel beams and support frames – Bond plates in high-stress areas.
Understanding Surface Preparation
A large proportion of the reported bonding failures are related to poor surface preparation. For a metal bonding repair to be effective, correct surface preparation is essential. Here are some best practices to follow:
Best Practices:
- Start by degreasing the surface thoroughly with a solvent-based cleaner.
- Use abrasive blasting or grinding to roughen up the surface to SSPC-SP10 (Near White Metal), 75 µm (3 mil) anchor profile).
- Ensure a dry, stable surface – condensation must be avoided.
Step-by-Step: How to Use a Metal Adhesive for Metal Bonding Repairs
- Assess the damage – Where possible, all cracks should be terminated by drilling small holes and vee’d out using grinding equipment. Where liquids are flowing from damaged areas, efforts must be made to stem the flow.
- Select the correct metal adhesive – E.g., Belzona 7311 for structural bonds.
- Surface preparation – Having stopped the leak, wash down the area with Belzona 9111 (Cleaner Degreaser) to remove all dirt, grease and surface contaminants. Then roughen the surface of both the repair area and the metal plate to SSPC-SP10 (Near White Metal), 75 µm (3 mil) anchor profile. Clean the prepared surfaces again with Belzona 9111 and tape up the area ready for repair.
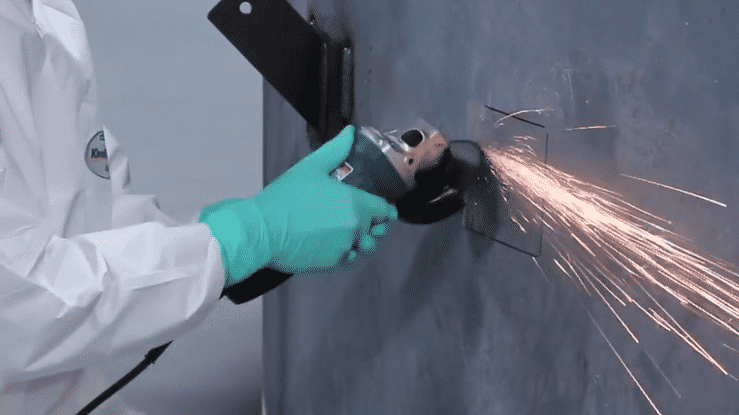
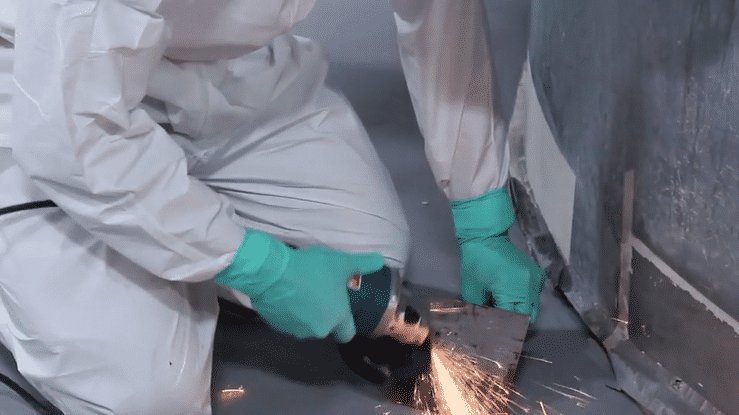
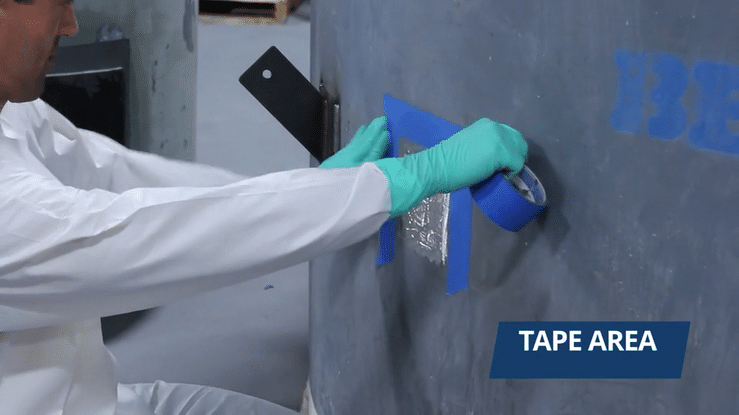
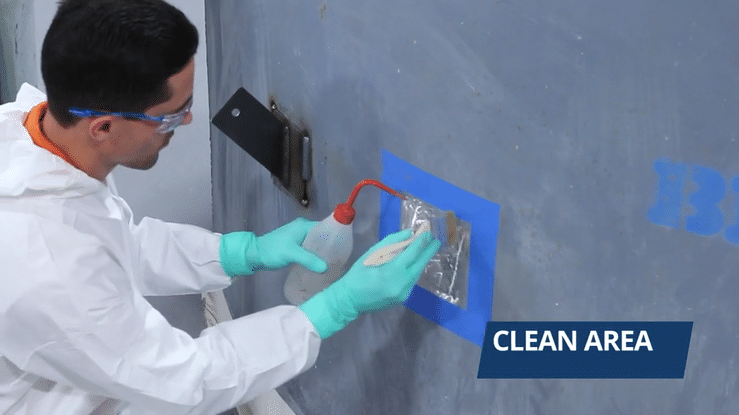
4. Mix the selected product as specified in the product Information for Use sheet.
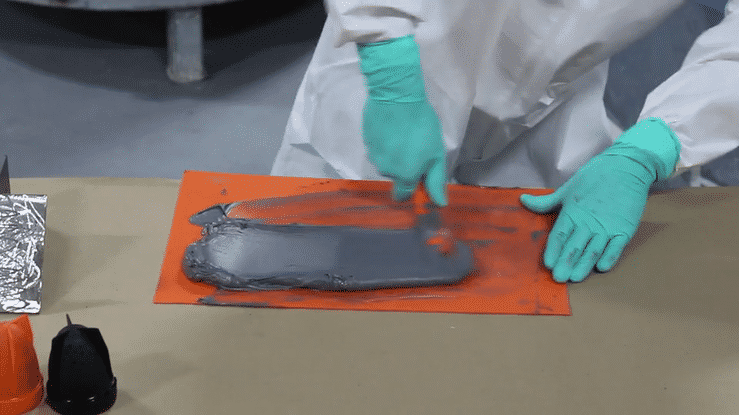
5. Apply the metal adhesive in a thin layer across all prepared areas, pushing the material well into the prepared profile. Apply more material to the plate, forming a peak of material in the centre.
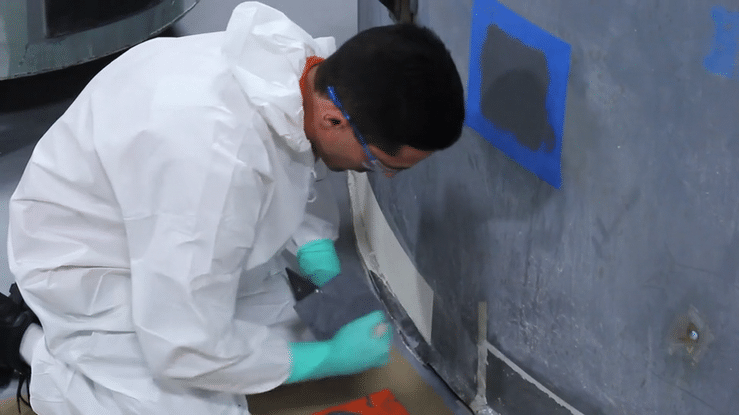
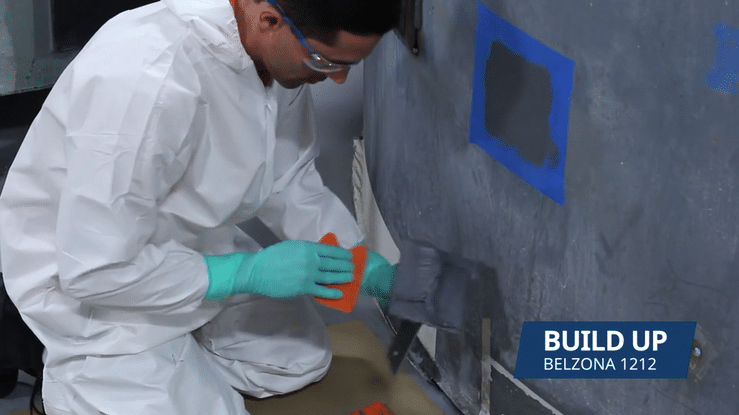
6. Push the plate into place allowing the excess material to exude from beneath the plate ensuring minimal air entrapment.
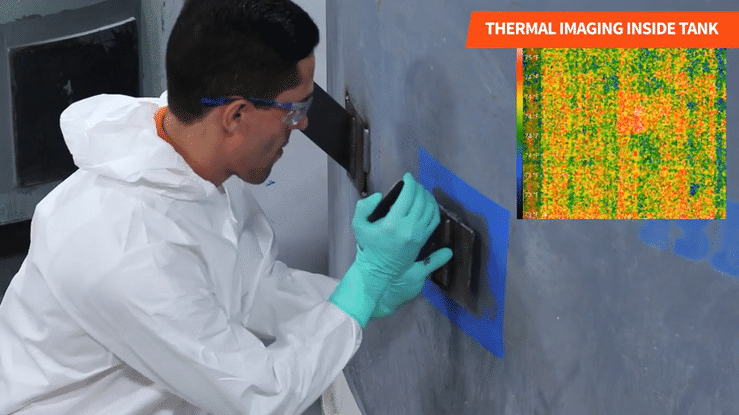
7. Remove the excess product immediately and remove the tape.
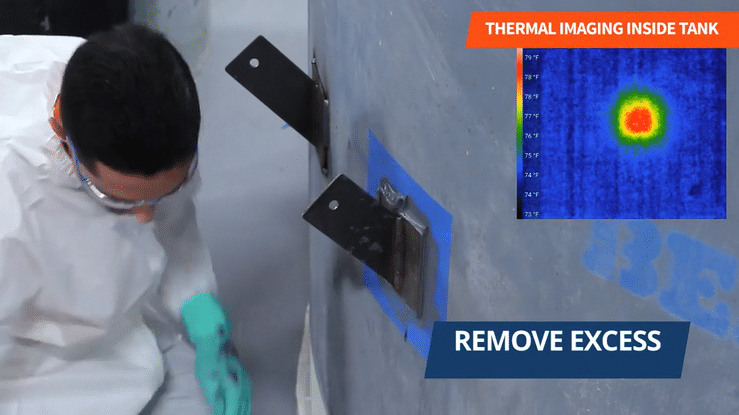
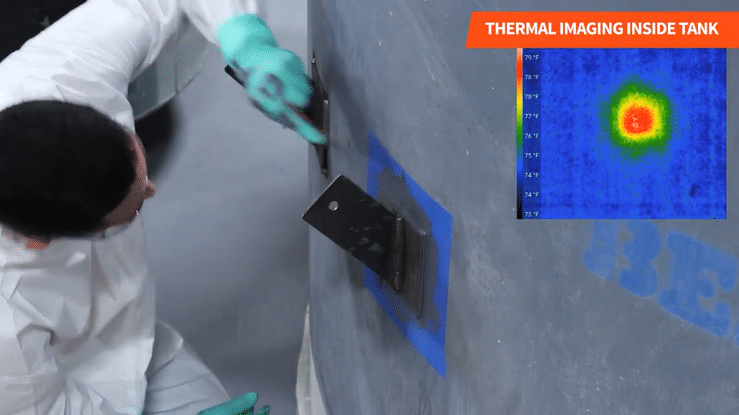
8. Allow the metal bonding adhesive to fully cure as explained in the product specification sheet.
9. Inspect and return the asset to service.
Extend the Life of Your Equipment with Cold-Applied Metal Bonding Adhesives
When welding isn’t practical – or just isn’t safe – Belzona’s metal bonding solutions offer a reliable, cold-applied and technically backed solution. Whether you’re working on offshore platform decks, steel tanks, corroded pipework, or structural reinforcements, a metal-to-metal adhesive like Belzona 7311 can restore performance, reduce risk, and extend service life.
Frequently Asked Questions
Can metal adhesives replace welding in structural applications?
Yes. Metal bonding with Belzona adhesives is now a recognised alternative to welding in many structural applications particularly where hot work poses safety risks or would result in significant financial expenditure due to permits, shutdowns, or specialist labour.
Are metal to metal adhesives strong enough for load-bearing equipment?
Absolutely. Products like Belzona 1111 (Super Metal) and Belzona 7311 offer excellent tensile, shear, and compressive strength – even under dynamic or cyclic loading.
Can you use metal bonding adhesives in chemical or offshore environments?
Belzona’s range of epoxy-based metal adhesives are designed to resist acids, alkalis, hydrocarbons, seawater, and aggressive cleaning chemicals – making them suitable for offshore platforms, refineries, and chemical plants.
Contact Your Local Distributor to Learn More About Metal Bonding Repairs
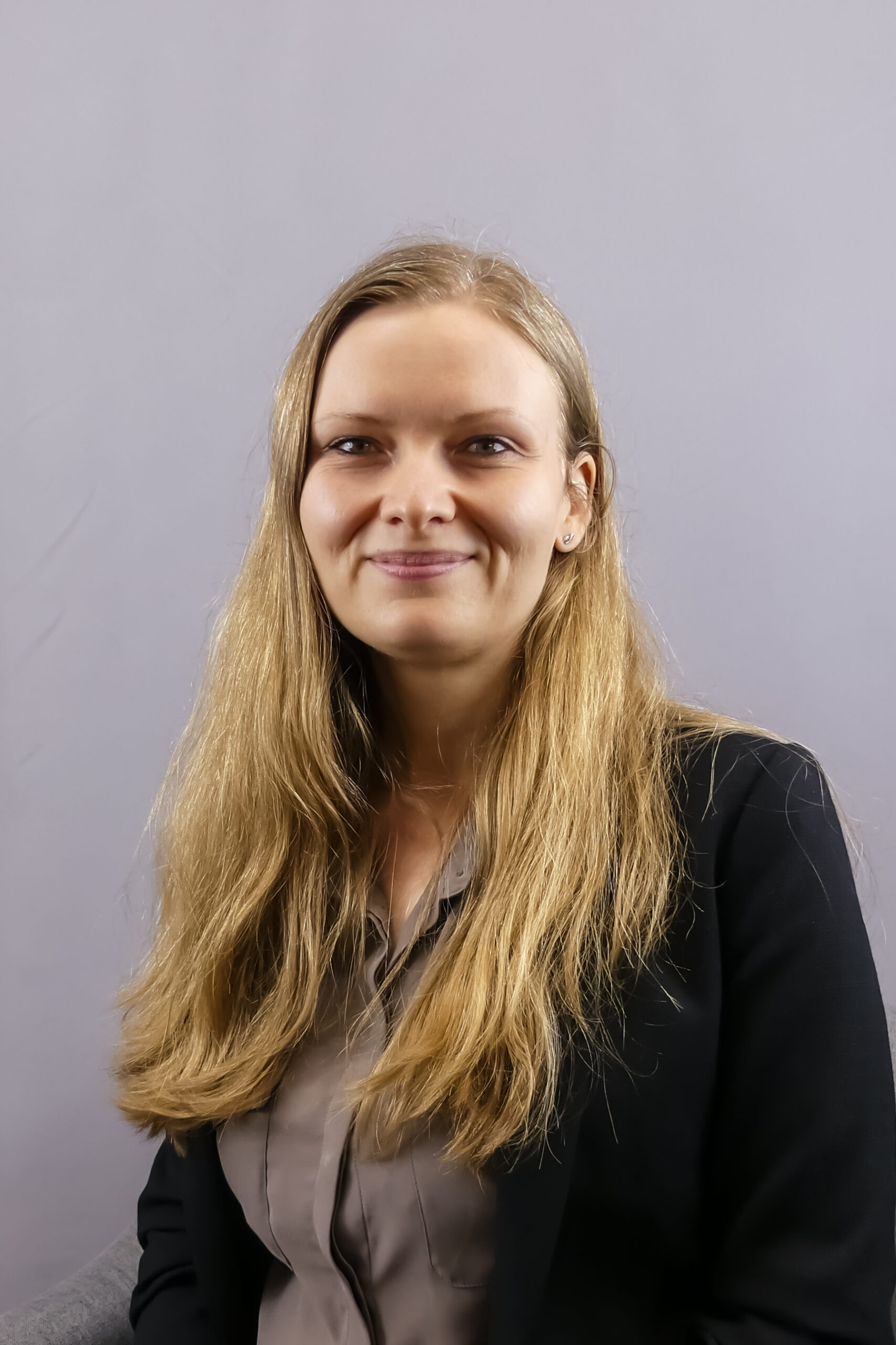
Natalija Skrlec joined Belzona in 2022; since then she has been promoted to the position of Technical Service Engineer based at the Company’s Headquarters in Harrogate. Her main responsibilities involve delivering technical application support and hands-on training in English and German speaking markets.
She graduated with a master’s degree from the University of Ljubljana in Slovenia in 2009 and holds an AMPP (NACE) Coating Inspector Level 1 certification.
Through her technical knowledge and hands-on experience, Natalija supports the application of Belzona’s polymeric solutions across multiple industries worldwide. She is passionate about continuous knowledge exchange, and believes it is the key to engineering excellence and Distributor success.