Introduction to Corrosion
The word “corrosion” comes from Latin corrōdō which literally means “to gnaw to pieces”. That is just what corrosion is – eating or gnawing away at metal, steel, concrete, and other types of materials.
Video: Conservation of Man-Made Resources
Corrosion Awareness
In an effort to bring awareness to corrosion as a natural force that destructs man-made resources, environment, costs jobs, and even lives, in 2012 The World Corrosion Organization designated April 24th as Corrosion Awareness Day.
Apart from being a very costly problem that the governments are tasked to solve due to its effect on infrastructure, transportation, industries, structures, and simply everything around us, and will continue to affect and cost us resources and financial capability, if not taken into account as a problem of an utmost importance.
In its IMPACT Study published in 2016, NACE International attempts to examine the extent of corrosion impact, the approach that industries and governments take to manage the problem and to establish the best corrosion mitigation practices.
Video: The NACE International IMPACT Study (by NACE International)
MICROBIOLOGICALLY INFLUENCED CORROSION (MIC)
Microbiologically influenced corrosion (MIC) is among the many modes of corrosion commonly found in industrial environments. This post uses the Oil and Gas Industry as an example of the environment in which MIC strives. However, O&G is not the only industry where MIC occurs. Other industries affected by MIC are petrochemical, marine, pulp and paper, wastewater and mining – just to name a few.
MICROBIOLOGICALLY INFLUENCED CORROSION
(MIC) is the degradation of structures as a result of the activity of various microorganisms. Although the electrochemical nature of the corrosion phenomenon remains valid for MIC, the participation of microbes or microorganisms induces unique features such as biofilm formation (1). This biofilm comprises microbial populations and their hydrated secretions. Most of the time, bacteria secrete byproducts that can build up in the biofilm and accelerate the rate of corrosion in the process.
MIC can adversely affect a great variety of industrial processes and equipment, including heat exchangers, pumps, pressurized vessels, offshore structures, and storage tanks. Microbial growth can lead to potentially catastrophic environmental consequences and costly operational shutdowns.
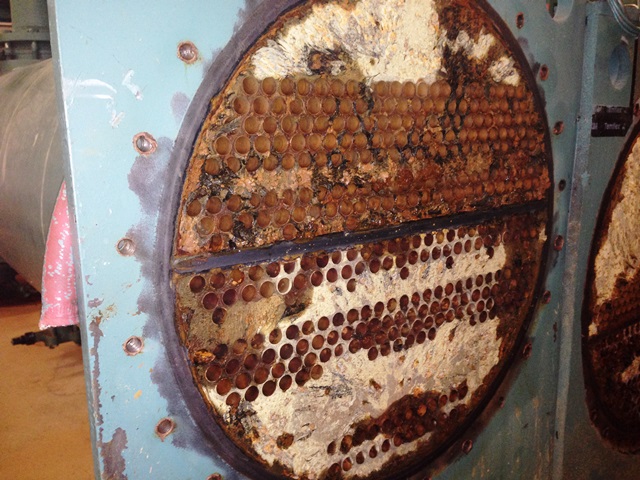
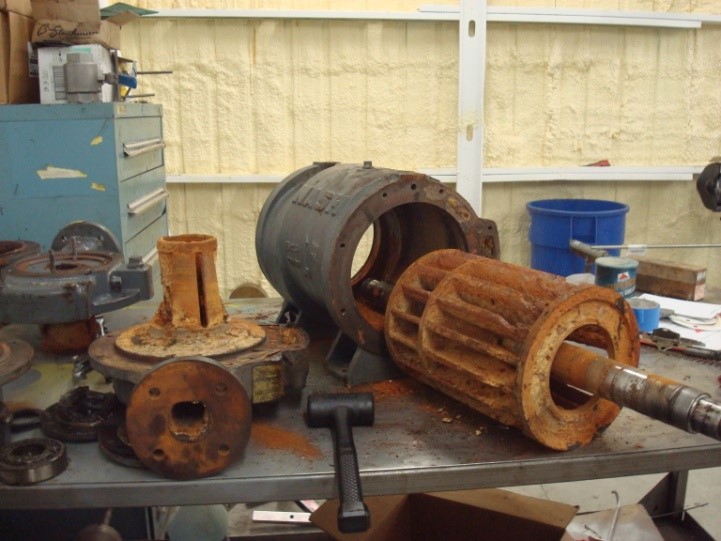
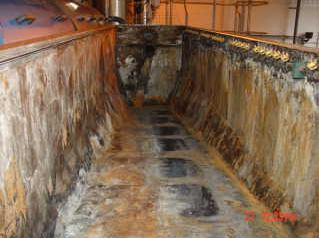
Following the Microbes in the Oil and Gas Industry
Well-known microbes in the oil and gas industry include sulfate-reducing bacteria (SRB), acid-producing bacteria, sulfuroxidizing bacteria, and iron-oxidizing bacteria. In the past, it was believed that SRB was the most significant biological driving force associated with MIC. However, recent reports and studies show that under natural circumstances, it is highly likely that mixed populations of bacteria will be encountered (2).
In general, MIC can be found in the oil and gas industry whenever the following conditions are present (2).
Untreated, stagnant water
Water can collect in small crevices where the area is wide enough for water to penetrate yet small enough for the fluid to stagnate. Oxygen in the stagnant water is readily depleted by normal corrosive reactions, resulting in an ideally anaerobic environment under which bacteria can develop biofilms and thrive.
Rough surfaces from welding
Microbes can settle preferentially on materials with discontinuous composition and anisotropic properties. The microscopic heterogeneity of engineered materials, whether created intentionally or as an artifact, is the basis for their anisotropic properties. Weld regions are particularly attractive to microbes as the welding process alters the material surface characteristics (3).
Temperature and pH suitable for bacterial growth
Bacteria are extremely adaptable and can survive in almost any environment. Most bacteria thrive at moderate temperature levels, ~30 °C (86 °F), and pH values between 5 and 7; however, others grow faster at 80 °C (176 °F) and survive in pH values between 1 and 3 (4).
Chemicals produced by bacteria have corrosive properties that affect oil production and transmission pipelines, storage tanks, oil and gas platforms and rigs, ships, and refining equipment operating at high temperature and pressure levels. The generation of these chemicals can also lead to the premature abandonment of oil and/or gas fields, refining outages, decreased revenues, and a great number of environmental problems.
Coating Alternatives for Corrosion Prevention and Correction
MIC can be proactively assessed based on two approaches, which consider the materials to be used and the service conditions. In the material selection process, the cost is a very important element to consider. A material with less susceptibility to MIC is expected to be more expensive than one that is not. One solution to this economic burden is to use a less expensive construction material and coat it with polymeric materials. In this case, the service approach would then be targeted to properly identify and select polymeric materials that are chemically resistant to the environment and less susceptible to MIC.
Little and Wagner cite some myths regarding MIC control practices.5 One of the industrial beliefs they considered to be false is that polymers are more resistant to MIC than metals. This statement is mostly based on the use of polyurethanes (PURs) and polyether PUR coatings in microbiologically affected environments. The generalized conception is that the chemical resistance of PUR materials is not as great as other corrosion-resistant coatings (2).
Although it is true that bacteria can use a coating from which to derive their metabolic needs and energy, not all coatings are equally stable against biological degradation. Filip and Pommer ranked epoxy and polystyrene polymeric materials as very stable with regard to their resistance to microbial attack (6). This fact has been corroborated by several authors, who also list epoxies as very resistant to microbial attack. Several laboratory experiments have been carried out in which epoxy resins and epoxy composites were exposed to sulfur reducing and hydrogen-producing bacteria for 90 days. After the exposure time, the epoxy resins and composites were not adversely affected by microbial degradation (7).
Designing Epoxy Coatings for MIC Protection
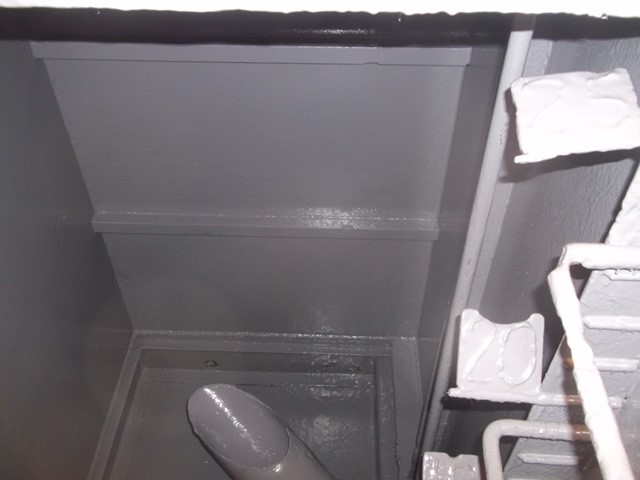
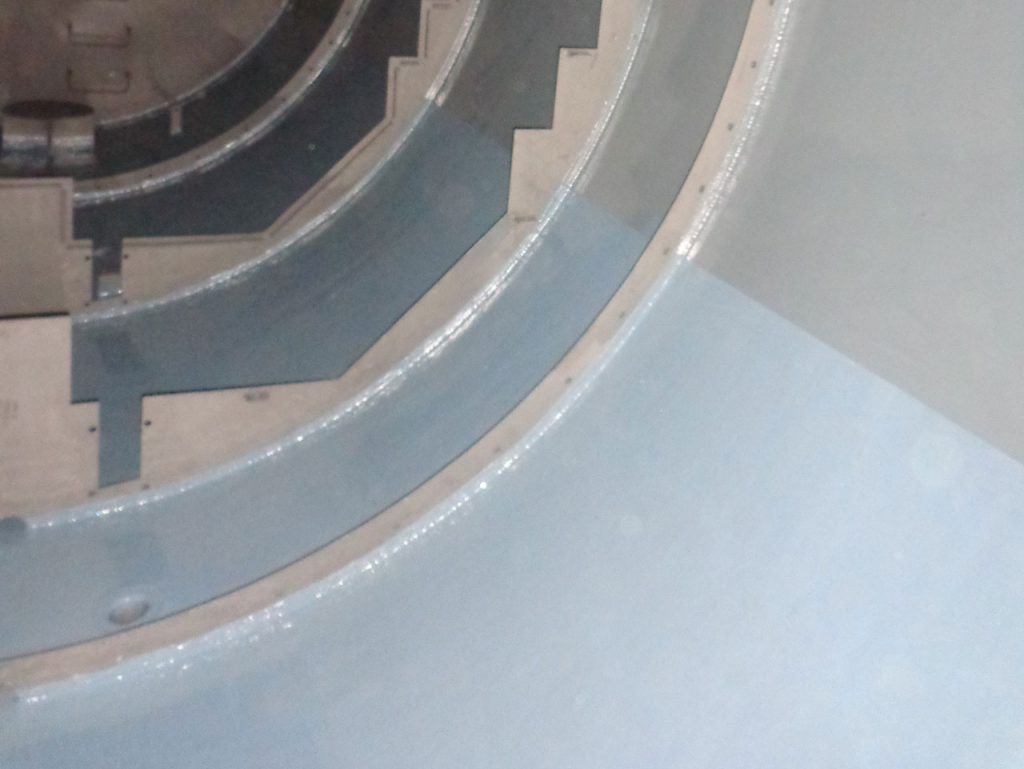
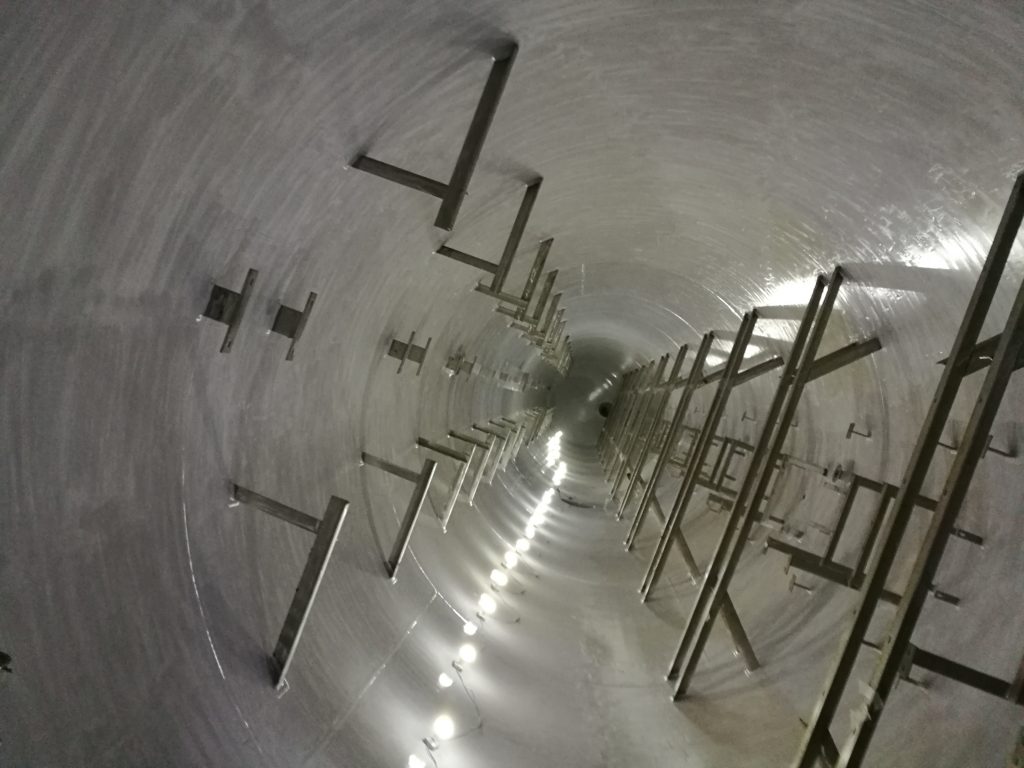
As Previously Stated:
Epoxy Polymeric Coating must, therefore , be Designed for:
There are several epoxy polymeric options available for achieving these requirements. In general, coatings provide a protective barrier between the substrate and the environment. Solvent-free epoxy materials provide additional features such as very low shrinkage during polymerization, very low odor, a minimal number of coats to achieve the desired thickness, quick drying, and better mechanical properties than epoxy materials that contain solvents.
The key to successful operation of an epoxy polymeric coating at high-temperature levels and chemically challenging environments lies with the polymers’ cross-linkage. In addition to the bonds between atoms that hold the polymeric chain altogether, many polymers form bonds between neighboring chains using chemical crosslinks. The multifunctionality of resins and crosslinks provides higher cross-linking density, which leads to enhanced chemical properties, mechanical strength, and thermal resistance. Novolac coatings, in particular, can be formulated by using phenol formaldehyde epoxy resins along with chosen additives and crosslinkers for achieving superior properties. Part of the design process involves collecting demonstrable evidence that the coating is indeed fit for service. This implies that the epoxy coating requires laboratory testing for high-temperature immersion and chemical resistance to bacterially generated byproducts. The immersion heat resistance of a coating can be determined through Atlas cell testing in accordance with NACE TM0174 (8).
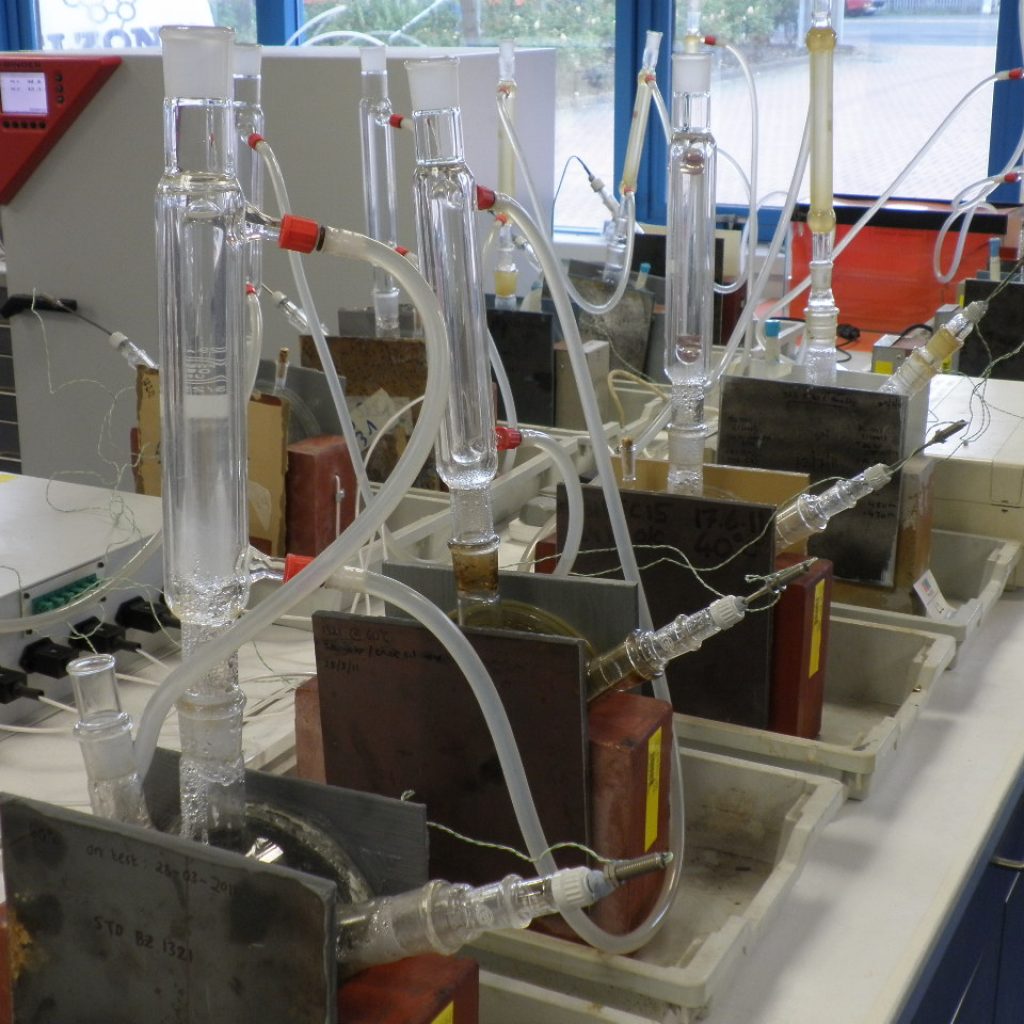
This method is employed to determine the maximum temperature at which a coating is able to offer adequate long-term immersion protection. The Atlas cell can also be used in conjunction with electrochemical impedance spectroscopy (EIS) in accordance with ISO 16773 (9). EIS is gaining in popularity among oil and gas asset owners as an indicator of a coating’s capacity to offer long-term substrate protection. EIS measures the resistance of a coating to the flow of current through it. By comparing the coating’s impedance before and after the Atlas cell testing is carried out, it can be determined whether or not the coating has been affected by the environment. Chemical resistance, on the other hand, is assessed by laboratory testing in accordance with ISO 2812-1 (10). The samples are periodically reviewed for any sign of damage in the form of erosion, blistering, cracking, or delamination.
The test is typically run for 52 weeks. The observations, coupled with the length of exposure of the coating to the chemical, are used to assign a chemical resistance rating
CASE STUDY: AN OIL & GAS PROCESS VESSEL PROTECTED WITH AN EPOXY COATING
An example of a project where a solvent-free epoxy coating was employed to protect a process vessel operating at temperatures below 90 °C (194 °F) comes from an oil and gas producer in the Americas. The vessel is a carbon steel electrostatic coalescer (Figure 1) located in an oil refining plant. The function of the coalescer is to induce droplet coalescence in emulsions of water in crude oil by using electrostatic fields. Conditions inside of the vessel are ideal for bacteria to grow and induce corrosion. As a result, the lower section of the vessel was suffering from extensive metal loss (Figure 2). A solution was required to avoid further complications and possible shutdown. The asset owner opted for an epoxy polymeric solution, including the use of a paste-grade material to rebuild the affected areas and a coating material for lining purposes. The affected area was dry-abrasive cleaned to produce a surface cleanliness of NACE No. 2/SSPC-SP 1011 with an average anchor profile of at least 3 mils (Figure 3).
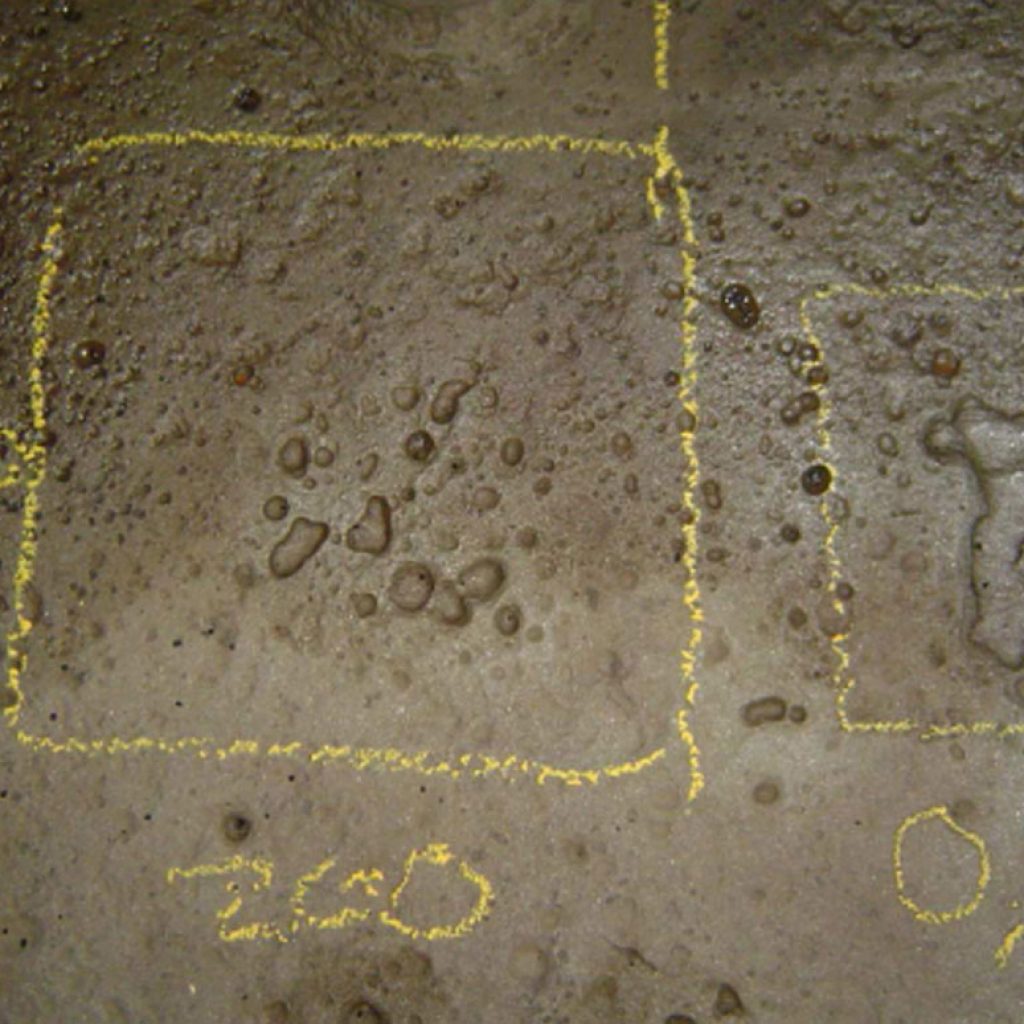
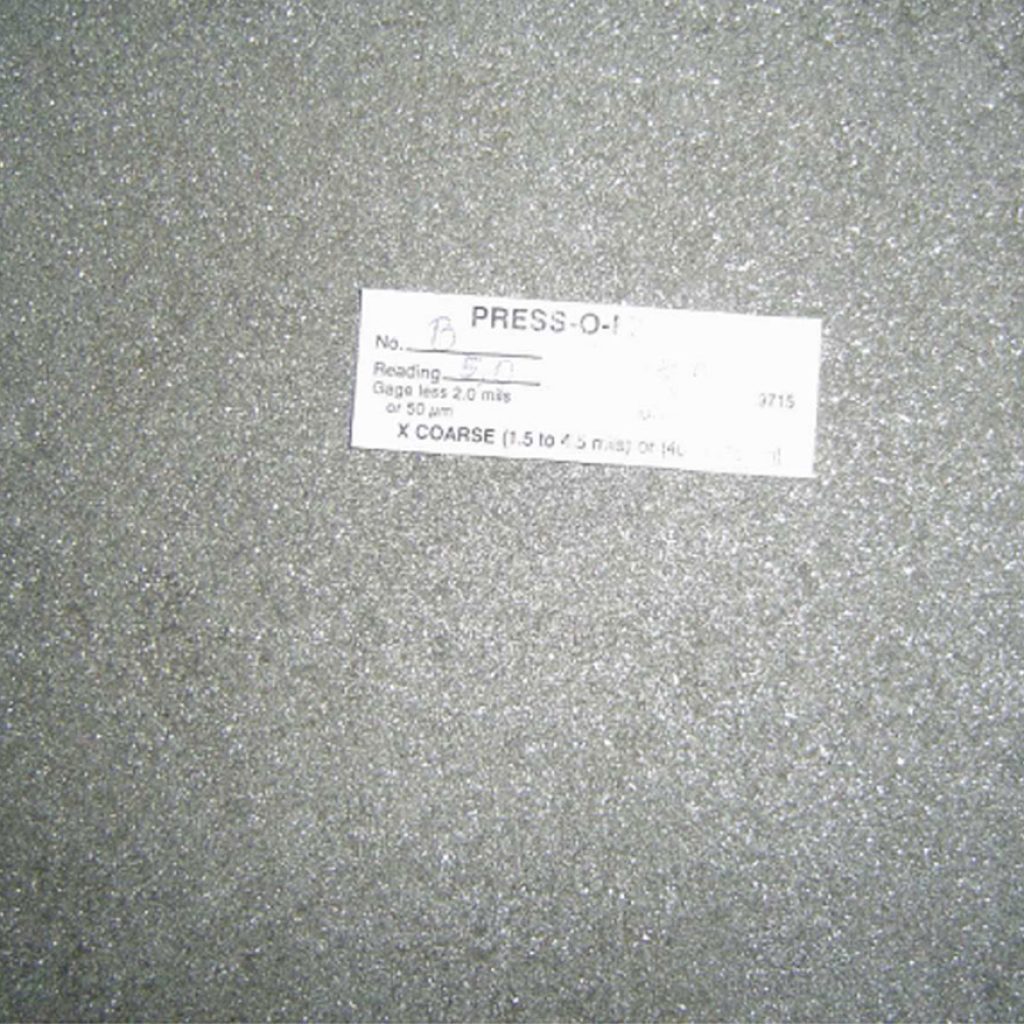
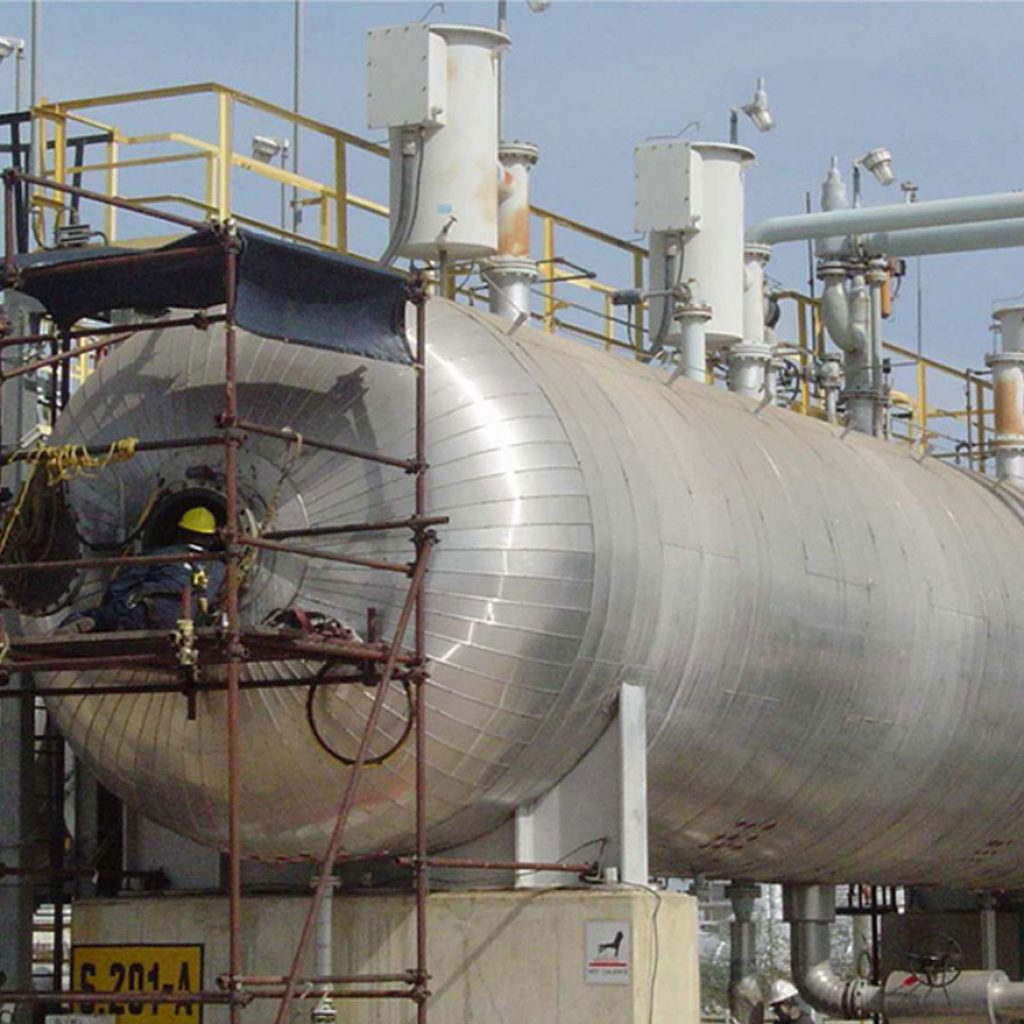
The surface was tested for bacterial activity using BART† biodetectors and treated according to the BART coding observed. Upon confirmation that the bacterial populations were eliminated, the surface was cleaned and degreased. The paste-grade epoxy material was applied to fill all pitted areas and smooth the substrate (Figure 4). A solvent-free epoxy coating was applied in two coats with contrasting colors to achieve a minimum total dry film thickness of 16 mils (Figure 5). Upon completion of the application (Figure 6), the coating was allowed to cure for inspection. Spark testing was carried out to confirm coating continuity and spot any defects. All defects were repaired prior to final curing. The vessel was returned to operation and the coating achieved full cure while in service.
The application took place in 2003. The vessel was last inspected in 2014, and the coating was in perfect condition. No corrosion or damage was observed. The owner has expressed interest in lining a sister vessel with the same epoxy polymeric solution.
Conclusions
REFERENCES
1. H.A. Videla, L.K. Herrera, “Microbiologically Influenced Corrosion: Looking to the Future,” International Microbiology 8, 3 (2005): pp. 169-180. 2. R. Javahersdashti, et al., Corrosion and Materials in the Oil and Gas Industry (Boca Raton, FL: CRC Press–Taylor & Francis Group, 2013). 3. R.S. Kurissery, Y. Sato, Y. Kikuchi, “Antibacterial Metals—A Viable Solution for Bacterial Attachment and Microbiologically Influenced Corrosion,” Material Transactions 46,
7 (2005). 4. T. Brock, K. Brock, “Sulfolobus: A New Genus of Sulfur Oxidizing Bacteria Living at Low pH and High Temperature,” Microbiology (1984): pp. 54-48. 5. B. Little, P. Wagner, “Myths Related to Microbiologically Influenced Corrosion,” MP 36, 6 (1997): pp. 40-44.
6. NACE No. 2/SSPC-SP 10, “Near-White Metal Blast Cleaning” (Houston, TX: NACE International). 7. Z. Filip, E.H. Pommer, “Microbiologically Influenced Deterioration of Materials,” Microbiological Degradation of Materials and Methods of Protection, European Federation of Corrosion Publications, no. 9 (Leeds, UK: Maney Publishing, 1992).
8. B. Little, J. Lee, Microbiologically Influenced Corrosion (Hoboken, NJ: John Wiley & Sons, Inc., 2007). 9. NACE TM0174, “Laboratory Methods for the Evaluation of Protective Coatings and Lining Materials on Metallic Substrates in Immersion Service” (Houston, TX: NACE International, 2002). 10. ISO 16773, “Paint and Varnishes—Electrochemical Impedance Spectroscopy on High-Impedance Coated Specimens” (Geneva, Switzerland: ISO, 2009). 11. ISO 2812-1, “Paints and Varnishes—Determination of Resistance to Liquids—Part 1: Immersion in Liquids Other than Water” (Geneva, Switzerland: ISO, 2007).
Osmay Oharriz is O&G, Petrochemicals & Chemicals Manager, Belzona.
A chemical engineer and Master in Engineering Sciences by profession, Osmay Oharriz has 8 years’ experience in the coatings industry. In his role as Oil and Gas Manager, he works with Belzona colleagues, asset owners, engineering firms, contractors, and fabricators in the oil and gas industry across all of the Americas. He has authored several technical articles and conference presentations.
A current member of NACE International, Oharriz’ background spans technical service, manufacturing, research, specification development, failure analysis, and project management. With special expertise in oil and gas, he contributes his knowledge to other industries, such as marine, waste water, and power.