It is no surprise that biomass plants are growing in popularity as they satisfy two main needs of the modern generation. First of all, they help reduce the amount of waste and, secondly, they produce energy in a sustainable way.
According to the International Energy Agency biomass generation is forecast to expand as planned projects come online. The global installed capacity for biomass generation is expected to reach close to 140 gigawatts (GW) by 2026, which will be fuelled primarily by expansion in Asia using residues from food production and the forestry processing industry.
Like most industrial assets, some elements of the biomass plant can be affected by corrosion. The fermentation and oxidation processes lead to the anaerobic digester corrosion, both at the gas and liquid phase. Internally, ADs are typically protected by a glass lining. Sludge tanks face similar corrosion issues and maintenance challenges.
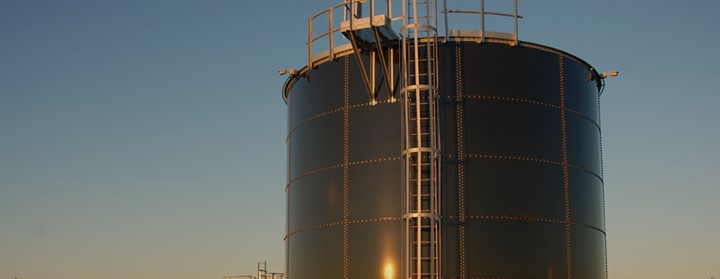
GLASS LININGS
Glass-lined steel provides superior corrosion resistance to acids, alkalis, water and other chemical solutions (with the exception of hydrofluoric acid and hot concentrated phosphoric acid). As a result of this chemical resistance, glass linings can serve for many years in environments that would quickly render most metal vessels unserviceable.
At higher temperatures, glass is not as effective against alkalis, where an increase by 10ºC (18ºF) can double the rate of attack on glass. Of course, as a glass lining provides protection to the extremely aggressive environments, its costs are directly proportional. In addition, they are very susceptible to impact damage and the repairs can be very costly.
Find out more about storage tank maintenance with polymeric systems
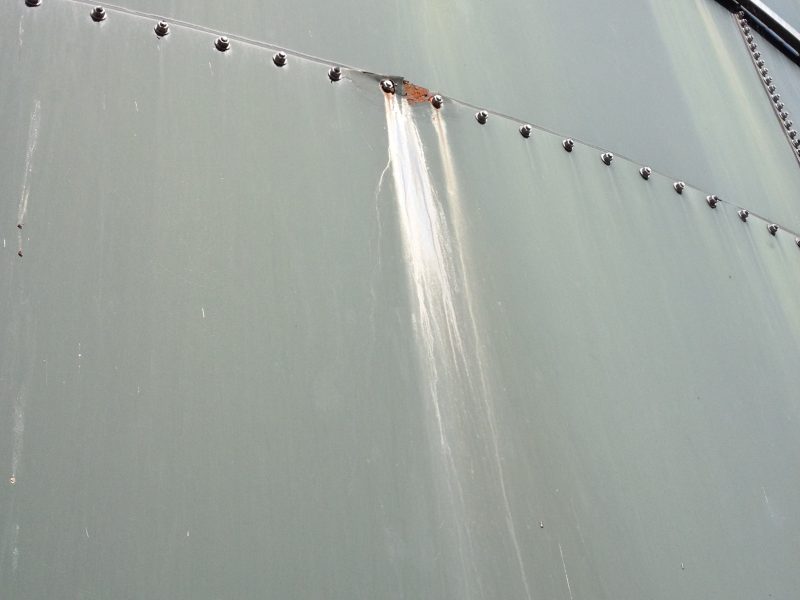
APPLICATION ERRORS
Application errors and mechanical damage during installation can result in pinholes within the glass lining. Aggressive chemicals produced during the anaerobic digestion process then attack the steel and corrosion can set in very quickly both at the liquid and gas phase.
We see defects the size of 1cm diameter, which quickly go through-wall leading to the escape of liquid digestate or methane.
MAINTENANCE CONSIDERATIONS
The biogas produced by an AD consists primarily of the combustible gases – methane and carbon dioxide. At normal atmospheric conditions, the volume concentration of methane-in-air required to form an explosive mixture is between 5% (Lower Explosive Limit) and 15% (Upper Explosive Limit). This can be readily ignited by sparks from welding and maintenance operations, or even by static electricity discharge.
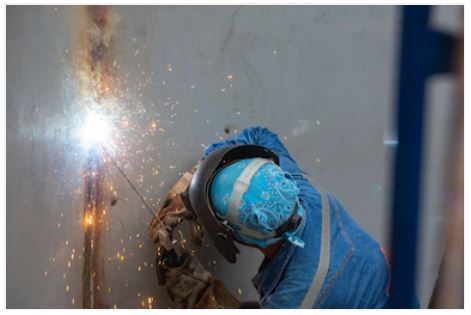
WHAT DO WE DO WHEN WE CAN’T WELD?
Potentially explosive atmospheres mean that welding repairs are out of the question. In addition, welding could damage the internal glass lining leading to its disbondment. Solutions that are applied and cure at ambient temperatures, therefore, need to be considered. 100% solids epoxy paste grade systems can be used to patch repair defects in the glass lining on the inside or to bond plates on the outside of the AD tanks to seal live leaks.
Epoxies have long been known for their excellent adhesion to a variety of substrates, including both steel and the glass linings. The absence of solvent within the polymer matrix also makes them safe to use in confined spaces and prevents shrinkage during cure.
COLD BONDING VS WELDING
PLATE BONDING WITH BELZONA ADHESIVE (BEFORE AND AFTER)
MATERIAL SELECTION
Epoxy composites, such as Belzona 1111 (Super Metal), are supplied as a two-part system with base and solidifier stored in separate modules. Once mixed, the hardening process starts and the material ultimately cures sealing leaks or preventing any defects from going through-wall. By their very nature, epoxies do not corrode and will protect the steel from any further corrosion attack.
PATCH REPAIR WITH BELZONA (BEFORE AND AFTER)
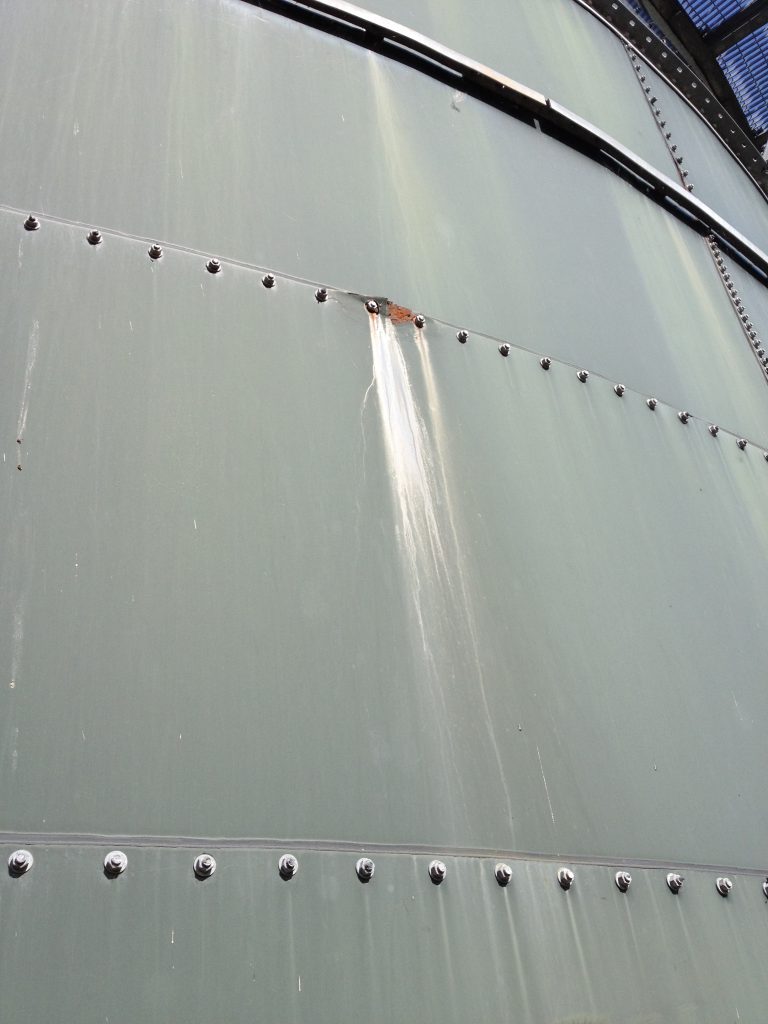
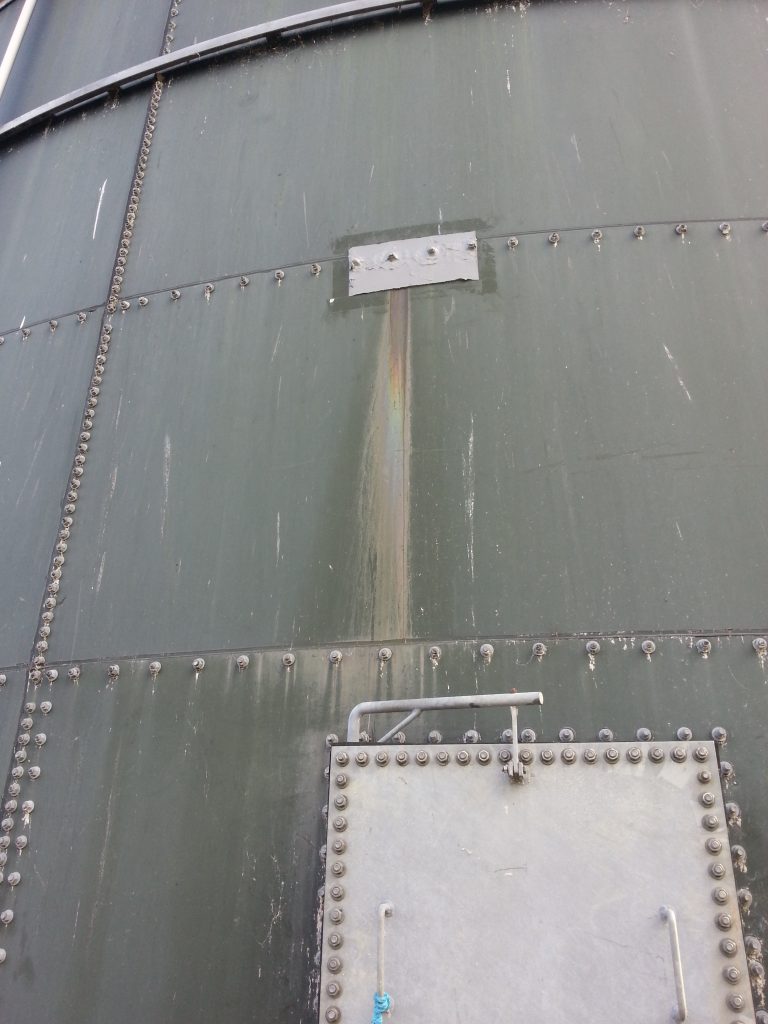
INNOVATION
In terms of using epoxy adhesives to restore integrity of the assets and mitigate anaerobic digester corrosion, prefabricated composite patches are now being considered in place of metal plates. The benefits of using a completely non-metallic solution ensure the repair is lightweight and has zero potential for corrosion. This application is becoming a preferred choice for water treatment sludge tanks, among others, and may be considered for anaerobic digester maintenance.
It’s interesting to learn about the specific challenges of corrosion in anaerobic digesters and sludge tanks, especially with the increasing popularity of biomass plants. The reliance on glass linings and the issues with welding repairs in potentially explosive environments make the use of epoxy composites for maintenance seem like a really smart and safe solution. The idea of prefabricated non-metallic patches is a great innovation too! We’d be pleased to give you the opportunity to write an article for our website if you email us.