What Is Cold Bonding?
Cold bonding can be described as the joining of two parts or materials without the use of heat. Traditional bonding techniques such as welding use high temperatures generated by an electric arc or the burning of gasses to ‘melt’ the materials so that they fuse into one. Cold bonding is achieved with the use of an adhesive that forms a bond between the two materials. Belzona cold-curing composites allow for this bond to be created without the use of heat.
A Welcome Alternative to Welding
Welding is one of the most recognized bonding techniques; however, it also presents several personal and environmental safety challenges, downtime, and defects that can lead to failures.
Safety
The risk of sparks can limit the applications where welding is acceptable, especially in potentially explosive atmospheres. A random spark created while welding can cause a fire or even an explosion. Initiatives to minimize the risks of hot work have been implemented for many years, but accidents still happen. In addition, toxic gases produced during the welding process can harm the welder in confined spaces and affect the environment, since they contain nitric oxide, nitrogen dioxide, carbon monoxide, and ozone.
Downtime
Welding can be time-consuming due to the number of necessary steps required to carry out the application. Equipment needs to be degassed before application, the surface must be machined back to the initial profile and once the application has been completed, the equipment needs to be stress relieved. The required post-weld heat treatment and inspection further extend downtime.
Defects And Failures
Galvanic corrosion commonly occurs if the filler or parent metals are dissimilar. In addition, the heat generated by welding can lead to the creation of heat-affected zones (HAZ) – which can also cause increased corrosion. Residual stresses caused by uneven expansion-contraction change the structure and the properties of the metal and can lead to potential material degradation. Voids and porosity may also occur during the welding process. These can weaken the weld joint if not repaired and can be difficult to detect if they are not visible on the surface of the weld.
Belzona Cold Bonding
Belzona bonding was first used in the late 1950s to attach equipment ID tags. Over the years, materials were enhanced to resist higher pressures and temperatures as well as demonstrate comparably high adhesion and compressive strength. Cold bonding is now considered to be a viable alternative to welding due to several reasons:
• There is no risk of sparks or electrical hazards and no need for hot work permits.
• Cold bonding can be used when cutting and welding are restricted due to a potentially explosive atmosphere.
• Fast and simple in-situ application without the need for special equipment makes cold bonding ideal for emergency repairs and challenging application areas, where access is restricted.
• There is no need for on-site machining, stress-relieving, and post-weld heat treatment.
• Cold bonding adhesive can conform to irregular shapes and substrates, filling the void between the surfaces. This ensures 100% contact which enhances load-bearing capability.
• The system is solvent-free, 100% solid, and environmentally friendly.
A Simple Solution for Complex Situations
The cold bonding application is simple as it uses the Belzona material as an adhesive between two surfaces. This simple technique can solve highly complex issues in different and challenging situations.
An example is the deck renovation plate bonding technology, developed in the early 2000s, which involves the use of multiple plates bonded in place using the Belzona material to create a new deck. The video that demonstrates this system can be seen on the BelzonaTV, the dedicated Belzona YouTube channel (youtube.com/belzonatv).
Various other applications including irregular shimming or chocking, restoring structural integrity, and permanently bonding equipment and structures in harsh and challenging environments have been developed and proven through testing and case histories.
Introducing A New Adhesive for Structural Bonding
Belzona’s newest product is Belzona 7311, a fatigue-resistant structural adhesive. It is optimized for applications requiring high mechanical strength, cleavage, and shear resistance making it ideal for cyclic and repeated loading.
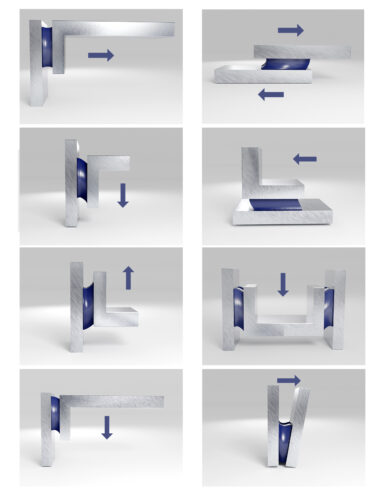
In general, epoxy adhesives tend to have less resistance to peeling and cleavage forces, in contrast to greater resistance to shear, tensile, and compressive loads. However, Belzona 7311 combines all of these allowing for high resistance to these common problems in infrastructure and assets. Greater adhesive strength decreases the bonded area’s susceptibility to failure. In return decreasing the cost of a repair or replacement. It is also important to take into consideration the amount of downtime that can be saved when using a product like this which can save operations from a heavy loss. Thus, making it an excellent product to have in anyone’s toolbox.
This solvent-free product does not require any specialized tools or hot work and can be easily applied to equipment support brackets, handrails on steel substrates, staircases/ladders, plate bonding, vessel furniture: internal and external.
Nevertheless, Belzona 7311 is not the only cold bonding product in our catalog that has the power to repair and improve assets and operations.
Giving A Robot A Hand
In February of 2021, at a brewery in Romania, a robotic arm broke. The robotic arm had been in service for around 20 years as it lifted and moved large boxes of beer from stacks to process lines. This led the robotic arm to break due to metal wear that accumulated over the years. The brewery needed a quick and inexpensive repair seeing as replacing the robotic arm would be very expensive and downtime was estimated at seven weeks. The use of Belzona products prevented these obstacles for the brewery.
The brewery decided that Belzona repair composite materials were the solution they were searching for as it provided a less expensive alternative to replacing the arm and faster results. Belzona 1111 (Super Metal) and Belzona 9341 were selected for the job.
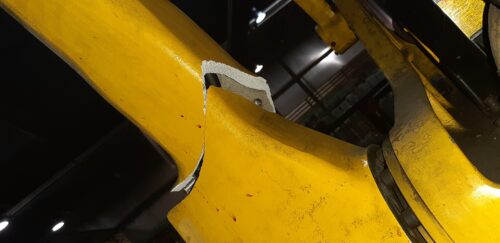
The application began by preparing the substrate, the aluminum robotic arm, by cleaning and creating a rough profile to ensure optimal adhesion between the arm and the materials. Both halves of the broken arm were joined by bolting metal plates to it. Belzona 1111 was applied between the two pieces of metal right on the tear of the halves. After bonding the two halves of the arm, Belzona 9341 reinforcement sheets were wrapped around the damaged area as more Belzona 1111 was applied in tandem with the sheets.
Belzona provided a fast return to service; the robotic arm was operational within two days. An inspection was completed after three weeks of the repair and results found that the arm was in good shape and worked according to specifications.
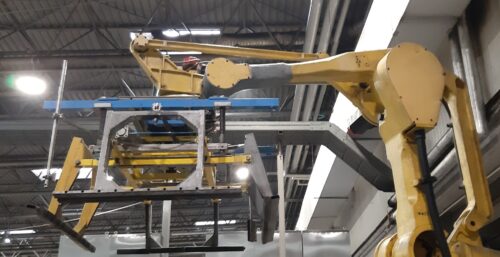
Repairing A Weather Deck is A Breeze
In some instances, Belzona is often the preferred repair method over traditional welding. Welding is a risk because it involves specialized tools that generate heat and sparks creating an unsafe environment. Additionally, it does not guarantee full adhesion. Voids can be left between two surfaces since welding attaches mainly at two points.
These were obstacles to an offshore rig in Norway. The weather deck was experiencing heavy corrosion. The deck was 50 square meters and areas were found to have a thickness below the minimum required thickness—some areas had 100% metal loss. In addition, some areas had holes that caused leakages into the insulated storage areas below the deck.
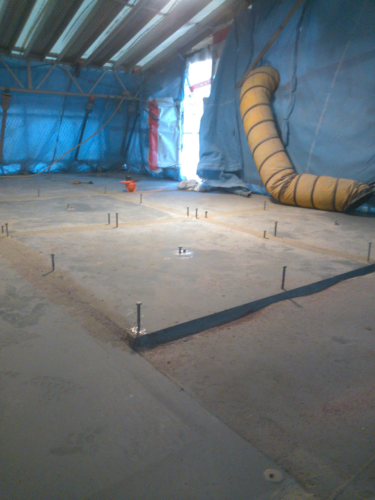
Belzona was chosen as an alternative to traditional welding. The location evaluated that Belzona was safer and more cost-effective than conventional plate welding alternatives. Moreover, Belzona solutions are stronger than welding and eliminate the void where corrosion might continue.
In two weeks, the weather deck was repaired by resurfacing the through-wall holes with Belzona 1111 (Super Metal). Afterward, manufactured steel plates of varying sizes and the weather deck were grit blasted. The plates were positioned and leveled using jacking bolts. The edges of the plates were sealed using Belzona 1111. Then, Belzona 5811 (Immersion Grade) was injected using a single component airless spray into the crevice between the deck and the reinforcement plate.
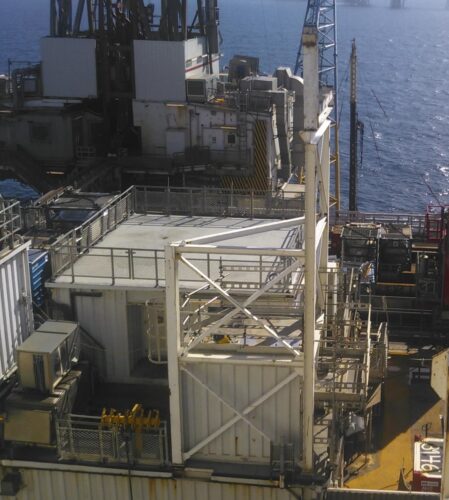
Interested in purchasing Belzona’s repair composites and protective coatings?
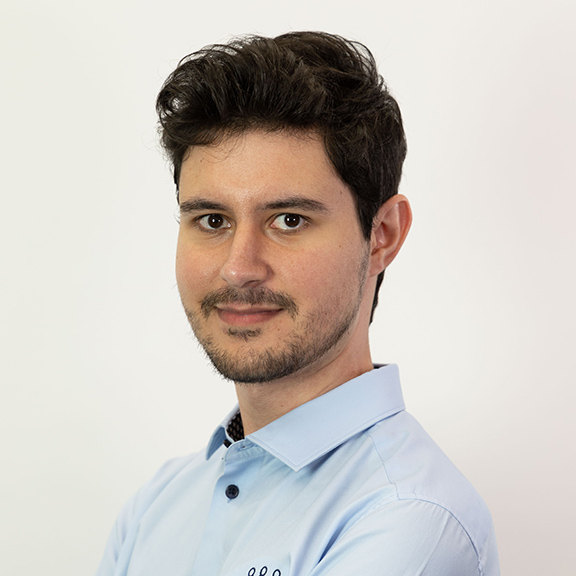
Digital Content Creator, Belzona Inc., Miami, Florida