This technical article was written by Osmay Oharriz, MSc., Technical Manager, Belzona, and was published by Hydrocarbon Processing.
Most industrial assets operating at elevated temperatures require thermal insulation for energy conservation, thermal protection or process stabilization. As soon as the insulation is installed and in service, the risk of the underlying substrate of suffering from corrosion under insulation (CUI) increases.
It should be noted that CUI represents a severe threat to the onstream reliability of many of today’s refining, chemical, power generating, and pulp and paper industries, including onshore and offshore installations. The mechanism of CUI is initiated by the ingress of water into the thermal insulation, which traps the solution at the annular space between the metal substrate and the insulation. As a result, the substrate starts corroding under the insulation.
Elevated temperatures exacerbate this corrosion mechanism. NACE SP0198 defines carbon steel, austenitic and duplex stainless steels as the primary metallic substrates potentially suffering from CUI. In practice, CUI commonly appears in thermal ranges between 50°F and 350°F, or where there is cyclic operation of the equipment.
For carbon steels, CUI manifests in the form of uniform and localized corrosion. For austenitic and duplex stainless steels, CUI is normally localized, leading to stress corrosion cracking if appropriate environmental conditions and stress levels are met.1 Additionally, thermal insulation can prevent operators and personnel in general from experiencing skin burns after accidentally touching substrates at moderately elevated temperatures.
As technology has expanded, the processes and associated equipment and pipework have become more complex and convoluted, creating more situations where workers are exposed during their shifts. Subsequently, worker organizations and governmental agencies have demanded the increased use of insulation for personnel protection, mostly for metallic equipment at ≥ 140°F.
No mandates or statutes govern the upper limit temperature for personnel protection. To correct potential CUI problems and provide effective thermal insulation, asset owners are urged to implement comprehensive corrosion and insulation protection strategies. As a rule, any such strategies should at least comprise three components: coating, insulation and jacketing.
High-quality corrosion resistance coating is applied to the substrate and, if it is properly applied, it should perform as a water barrier isolating the substrate from the trapped water. Conversely, the insulating material should be protected with an effective and durable weather barrier or jacketing.
However, today’s high energy prices— and, at times, maintenance budget reductions— render these solutions costly and laborious. This is the reason why asset owners and process engineers are constantly looking for ways to reduce labor or implementation costs by using other non-conventional, cost-efficient alternatives.
One of these alternatives, which seems to be of growing interest, is the use of thermal insulating coating systems that can also provide corrosion resistance. This article details the development of a novel epoxy closed-cell foam insulating and corrosion protection barrier by a coating manufacturer.
Design considerations of such a material, fitness-for-service testing and results will be presented, as well. Potential application areas and benefits, including worksite personnel and CUI protection, will also be discussed.
Background
Polymer foaming, simply defined, is the technology that allows the generation and stabilization of bubbles
within a polymeric matrix.² When a system is excited into an unstable foaming state, a stabilization mechanism must be established in time to transform the foaming into a stable foamed product. In theory, it sounds very simple to accomplish; in reality, it is not. Produced foams can be categorized in accordance with different perspectives², as detailed in TABLE 1.
Perspective | Types | Comments |
Material | Thermoplastic Thermoset | A wide variety of thermoplastics such as polypropylene, polyethylene, polystyrene, polycarbonate, and polyvinyl chloride, to cite a few, have been used in foam processing techniques. Epoxy is an example of thermosetting insulating material. |
Mechanism | Physical Chemical | Physical (or soluble) mechanism involves physical action, e.g., blowing a gas into a polymeric matrix. Chemical action is when the foaming mechanism solely depends on a chemical reaction, e.g., the reaction of an isocyanate with water. |
Nature | Flexible Rigid | Flexible foams tend to be less cross-linked than rigid foams. |
Structure | Open Cell Closed Cell | Closed cell refers to a foam which minimizes permeability by entirely isolating the substrate, whereas open cells are higher in permeability. |
Cell Size | Microcellular Cellular | Microcellular cell sizes are reported in the order of 10 μm4. |
Density | High Density Low Density | The density of foams varies in general. Lower densities are achieved when the polymer holds higher proportions of air. |
Foaming Perspectives
Epoxy foams are becoming a more attractive alternative to the more prevalent urethane foams used as thermal insulators. Reasons for this include the mechanical strength of epoxy matrices and the elimination of toxic or sensitizing isocyanates, typically used in the polyurethane formulations.³
Additionally, some literature has cited the rigidity and dielectric properties (volume resistivity, dielectric constant and dissipation factor) of epoxies over polyurethanes. Whether epoxies or polyurethanes, polymeric foaming requires the presence of a blowing agent, herein defined as a substance that produces a cellular structure in a polymer mass by releasing a gaseous phase due to thermal decomposition or a chemical reaction.⁴
The blowing agent plays a significant role in both the manufacture and performance of the polymeric foam. In the case of foaming of high molecular weight polymers [e.g., polystyrene (PS), polyolefins, polyamides, polyester], the blowing agent modifies the rheology of the polymer during foam formation and shaping.
In cases where polymerization, foaming and shaping all happen in one step, [e.g., during the formation of typical polyurethane (PU), epoxy or phenolic foams], the blowing agent not only affects the liquid viscosity and thermal history, but also the compatibility, reactivity and phase mixing of the components.⁵
Some of the most used physical blowing agents include halogenated hydrocarbons, hydrocarbons and inert gases, among others, which can be bubbled through thermoplastic materials or expanded by heat treatment. One of the most common blowing agents is water, which can be reacted with isocyanates to form an unstable intermediate of carbamic acid that readily decomposes to generate carbon dioxide (CO2 ).⁴ Alternately, alkylhydrosiloxanes can be used to produce epoxy-based foams. These reactions are well-documented.
As previously discussed, years ago, epoxy resins were not as readily foamed as urethanes; therefore, they saw limited used in encapsulant applications. This is changing because of the potential advantages of epoxy foams over urethane foams. The primary advantage is the elimination of toxic or sensitizing isocyanates used in polyurethanes, which is being enforced by health and safety legislations. Polyurethanes are readily foamed by the simple addition of water. Epoxies, on the other hand, do not foam in the same way.
Designing an epoxy foam
Designing an epoxy foam. This section details the development of a novel epoxy closed-cell foam insulating and corrosion protection barrier by a coating manufacturer. This barrier, referred to here as a proprietary epoxy foama, uses a solvent-free phenol formaldehyde Novolac epoxy as a base and a polyamine as a solidifier. Both components react in stoichiometric amounts to yield a thermosetting polymer, as in a well documented mechanism of nucleophilic addition to an epoxy.
Specifics of the epoxy resin and amine curatives used are proprietary and, therefore, not detailed and included in this article. During this polymerization process, a modified polysiloxane is used as the blowing agent. Its chemistry and reaction mechanism constitute proprietary details and, again, are not discussed here. Both the chemistry and quantity of the blowing agent are used to adjust the foaming action and final density of the epoxy foam. The polymeric system is further modified with functional extenders to achieve specific qualities depending on target design considerations.
Upon polymerization, the epoxy foam resulted in a cured epoxy foam with the following characteristics: rigid closed cell, low density/light weight, and a final expansion of up to three times its applied thickness. FIG. 1 shows the growth of the foam during curing. FIGS. 2 and 3 illustrate an application of the proprietary epoxy foam onto a pipe section and a cross section cut, respectively.
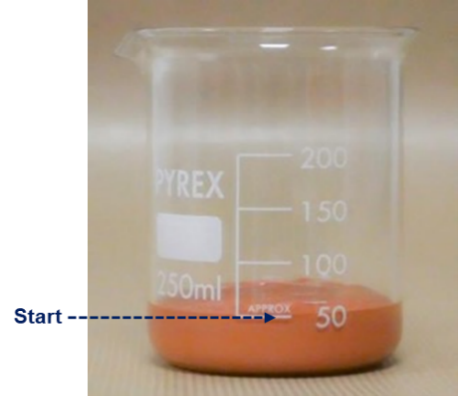
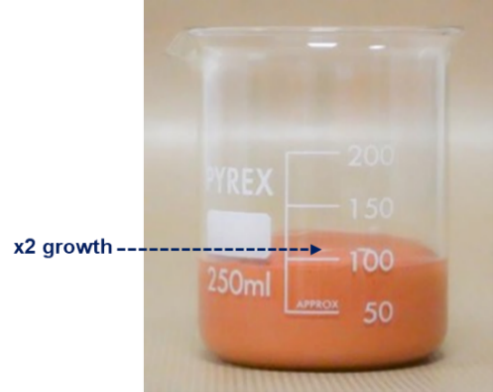
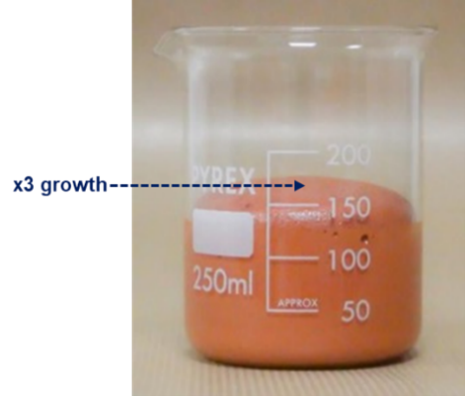
Figure 1: BZ5871-EF as applied inside a beaker and allowed to cure until achieving growth of up to three times its original thickness
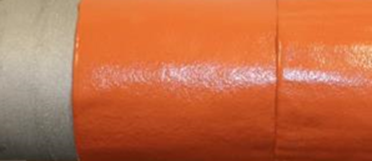
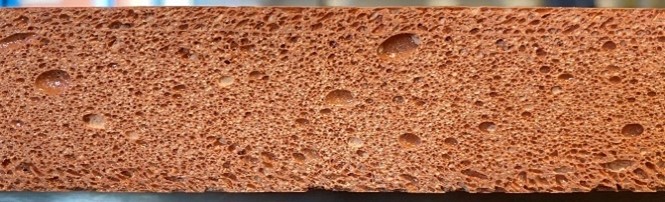
Design considerations for the epoxy foam were based on both technical target requirements and a practicality approach, as summarized in TABLE 2. The epoxy foam was subjected to the tests and evaluation protocols shown in TABLE 3 to ensure that it met the design criteria previously discussed. Where possible, internationally recognized standards were used.
Technical
Excellent corrosion protection | A system which would show no signs of failure or damage after exposure to simulated corrosion under insulation scenarios, salt spray, and water immersion |
Cool-to-touch properties | A system which could offer safe touch by reducing the surface temperature of the industrial equipment to less than 140°F allowing direct hand contact |
Excellent thermal insulation | A system with reduced heat transfer across its volume |
No primer or topcoat required | A system with adequate adhesion to mechanically prepared and clean substrates without any conditioning, and robust enough to provide corrosion protection by itself |
Solvent free | Solvent-free epoxy systems show greater mechanical properties when compared to solvented formulations. Experimental work has shown that solvent remaining within the epoxy can hinder the cross-linking process resulting in lower exotherm, initial curing rate, reaction order, and glass transition temperatures (6) |
Durability (Ageing) | A foaming system which would show no cracking or sign of deterioration when subjected to thermal cycling |
Practical
Tolerance to minimal surface preparation | A foam which could be applied onto substrates cleaned to the requirements of both SSPC-SP 10 (7) and SSPC-SP 11 (8) and profiled to at least 1 mil and successfully offer corrosion protection |
Ease of application | A system that could be conveniently applied by brush, cartridge spray, or heated plural component airless spray |
Short overcoat times | A system which could be overcoated with additional coats, if needed, as soon as possible |
Fewer layers (coats) required | A foaming system which would need less layers (coats) than most typical coating systems to achieve insulative properties through a controlled catalytic process |
Quick return to service | A foaming system with shorter drying times to provide a definite appeal for asset owners |
Proprietary epoxy foama design considerations
BZ5871-EF was subjected to the following tests and evaluation protocols in to ensure that it met the design criteria previously discussed. Where possible, internationally recognized standards were used.
Thermal Conductivity | BS EN 12667 (9) /ASME C177 (10) |
Corrosion Under Insulation | Modified ISO 19277 (11) section 7.4 |
Salt Spray | ASTM B117 (12) |
Cool-to-Touch | ASTM C1055 (13) |
Thermal Cycling | ISO 19277 section 7.3 |
Pull Off Adhesion | ASTM D4541(14) |
Degree of Blistering Evaluation | ISO 4628-2(15) |
Degree of Rusting Evaluation | ISO 4628-3 |
Degree of Cracking Evaluation | ISO 4628-4 |
Keep an eye out for part two of Mr Oharriz’s article on the Belzona blog very soon.
Acknowledgement
This paper was presented by the author or assigned speakers at the Coatings+ 2021 conference.
References
1 NACE SP0198, “Control of corrosion under thermal insulation and fireproofing materials—A system’s approach,” NACE International, Houston, Texas, July 2017.
2 Lee, S.-T. and N. S. Ramesh, Polymeric foams: Mechanisms and materials, CRC Press LLC, Boca Raton, Florida, May 2004.
3 Domeier, L. and H. Marion, “Epoxy foam encapsu-lations: Processing and dielectric characterization,” Sandia National Laboratories, SAND99-8213, Livermore, California, 1999.
4 Eaves, D., Handbook of polymer foams, Rapra Technology Ltd., Shawbury, UK, 2004.
5 Singh, S. N., “Blowing agents for polyurethane foams,” Rapra Review Report, Vol. 12, 2002.
6 Pascault, J.-P., et al., Thermosetting polymers, 10th Ed., Dekker, New York, New York, 2002.
7 The Society for Protective Coatings, SSPC-SP 10, “Near-white blast cleaning (NACE No. 2),” 2006.
8 The Society for Protective Coatings, SSPC-SP 11, “Bare metal power tool cleaning,” 2012.
9 British Standards Institution BS EN 12667, “Thermal performance of building materials and products. Determination of thermal resistance by means of guarded hot plate and heat flow meter methods. Products of high and medium thermal resistance,” 2001.
10 ASTM C177, “Standard test method for steady-state heat flux measurements and thermal trans-mission properties by means of the guarded-hot-plate apparatus,” 2019.
11 International Organization for Standardization ISO 19277, “Petroleum, petrochemical and natural gas industries—Qualification testing and accep-tance criteria for protective coating systems under insulation,” 2018.
12 ASTM B117, “Standard practice for operating salt spray (fog) apparatus,” 2019.
13 ASTM C1055, “Standard guide for heated system surface conditions that produce contact burn inju-ries,” 2020.
14 ASTM D4541, “Standard test method for pull-off strength of coatings using portable adhesion tes-ters,” 2022.
15 ISO 4628, “Paints and varnishes—Evaluation of degradation of coatings—Designation of quantity and size of defects, and of intensity of uniforms changes in appearance—Part 2: Assessment of degree of blistering, Part 3: Assessment of degree of rusting, Part 4: Assessment of degree of crack-ing,” 2016.
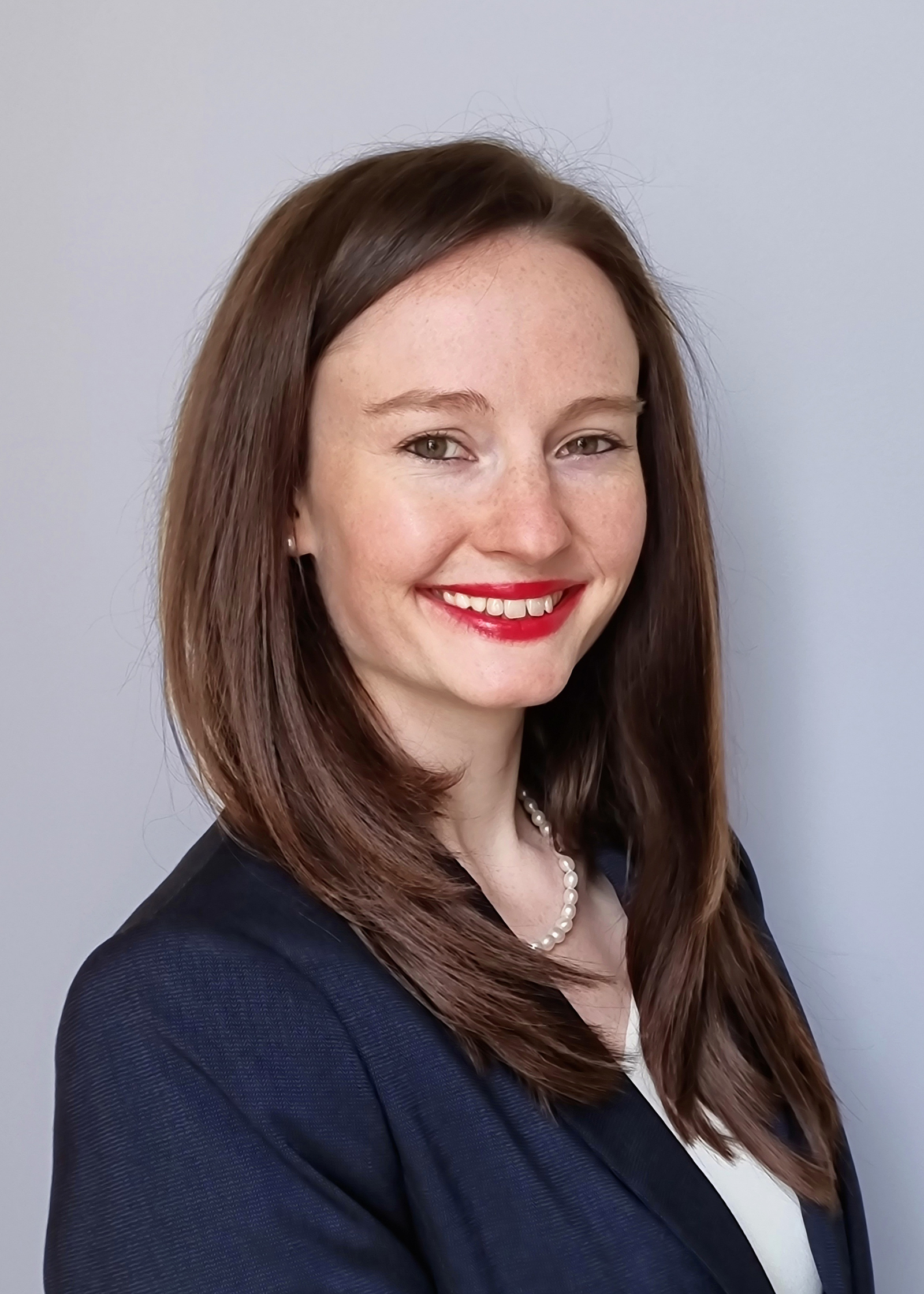
Chloe Hirst is the Senior Copywriter at Belzona Limited and is based in Harrogate, England. She gained a Bachelor’s Degree (with Hons.) in Media and Communications (specialising in Journalism) at Goldsmiths College, University of London. Chloe regularly writes case studies and thought leadership content featuring a variety of different industries, with a special focus on the renewables sector. In both 2023 and 2024, she won the Best Manufacturing Content Creation Specialist (UK) Award as part of Acquisition International’s Influential Businesswoman Awards.