Why Use a Pipeline Coating?
Contractors and Maintenance Workers use a pipeline coating to repair various industrial problems found in their field. Common causes of damage and deterioration to pipelines include impact, frost damage, corrosion, erosion, and chemical attack. Epoxy coatings offer outstanding erosion and corrosion protection and demonstrate excellent chemical resistance.
Benefits
Usually, the substances that the pipes transport will cause erosion and corrosion damage. For example, in a water and wastewater plant, the substances and the cleaning agents in pipes and tanks might corrode the system over time. Additionally, pipelines are damaged by their environment. If the pipelines are in the presence of saltwater, they will rust. Pipeline epoxy coatings protect pipework in facilities that use chemicals or are near saltwater, such as general facilities and offshore rigs.
The following are some more benefits of using a pipeline coating system:
- Leak sealing: pipeline coatings seal liquid (water and chemicals) and gas leaks in addition to solving health and environmental hazards. Increases efficiency from pressure drop caused by leaking.
- Plate bonding: an alternative to welding. Polymeric structural adhesives allow two metal structures to bond. The bond seals holes and leaks. Conforms to irregular shapes and substrates, filling the void between the surfaces.
- Composite wraps: restores the strength of holed, weakened, and corroded pipelines; provides chemical and corrosion resistance; seals both liquid (water and chemicals) and gas leaks.
- Corrosion protection: coatings create a barrier between the pipework and harmful environmental factors. The coatings are chemical-resistant and temperature resistant. Coatings protect pipework from Corrosion Under Insulation (CUI), corrosion caused by damp insulation.
- Specialist repair composites: certain lines of pipeline coatings are engineered to be applied on wet or oily surfaces. Moreover, some coatings can be applied immersed in water and remain submerged.
- Internal pipeline coating: pipeline coatings can also line pipework interior. The linings increase efficiency due to hydrophobic properties. Additionally, it creates a stronger barrier to resist erosion and corrosion.
Pipeline coating materials do not require hot work and allow for simple and safe applications, which minimize cost and downtime. Epoxy coatings are utilized to provide corrosion resistance, as well as erosion and chemical protection across a range of temperatures.
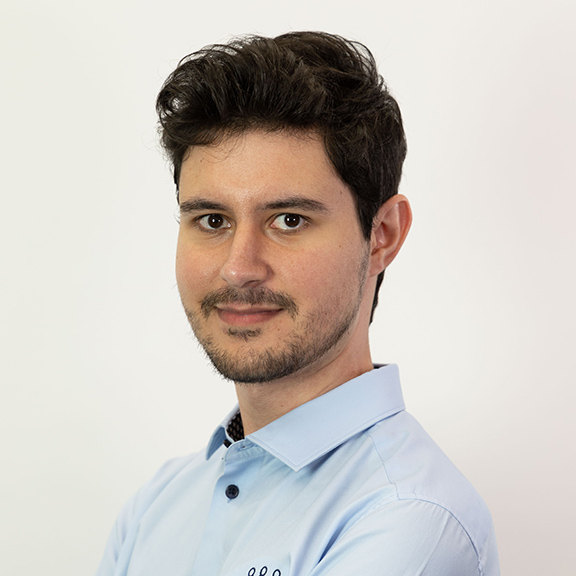
Digital Content Creator, Belzona Inc., Miami, Florida
Hello,
My name is William van Rijswijk
I am HR Manager by PeSa Personal GmbH
We are looking for pipecoaters
Can you help us out
Hello William, thank you for your comment. For more information about this solution, please use the following link to contact your local Distributor – https://belzona.com/en/about/disfinder.aspx. Best regards, Belzona Team.
Thanks for also talking about how the need for corrosion protection necessitates internal pipe coating. I’m interested in looking for a good service like that because I will be getting one of my commercial properties renovated. Getting ample protection for it will surely require such coatings.