Equipment Maintenance in the Steel Industry
In the steel and metal processing industry, critical equipment such as heat exchangers is essential for maintaining efficient operations. However, like other machinery in harsh environments, heat exchangers require regular heat exchanger maintenance to combat issues like abrasion, erosion, and corrosion. Belzona offers metal repair composites and durable protective coatings designed to reduce downtime and extend the life of your equipment.
Heat Exchanger Maintenance in Steel Manufacturing: Addressing Galvanic Corrosion
In a recent heat exchanger maintenance project in Brazil, Belzona was tasked with addressing a significant problem: galvanic corrosion on the tube face of a heat exchanger, which resulted from the contact between dissimilar metals. The heat exchanger is crucial for transferring heat in the steel manufacturing process, making its optimal functionality essential for production efficiency.
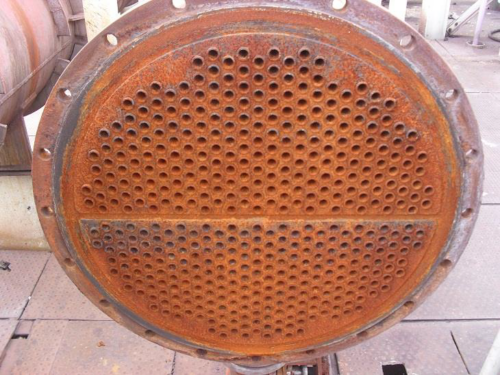
Galvanic Corrosion
Galvanic corrosion occurs when two dissimilar metals come into contact in the presence of an electrolyte, leading to accelerated corrosion on one of the metals. In this case, the tube face of the heat exchanger made from carbon steel was suffering from this issue, jeopardizing its integrity and performance.
Application Method: In-Situ Heat Exchanger Maintenance
To address the corrosion issue, the heat exchanger maintenance process was carried out in situ, according to Belzona’s system leaflet HEX-01, a step-by-step guide on how to apply a Belzona product to a heat exchanger. The key steps included:
- Preparation: The application area was meticulously marked out before the tube face was grit blasted to SA2.5, achieving a minimum 75-micron (3 mils) profile. This preparation is critical for ensuring proper adhesion of the repair materials.
- Rebuilding the Tube Face: The first step in the repair involved rebuilding the tube face with Belzona 1111 (Super Metal). This high-strength repair composite is ideal for rebuilding worn or damaged metal surfaces.
- Coating Application: Following the rebuilding, two coats of Belzona 1321 (Ceramic S-Metal) were applied, each at a thickness of 250-375 microns (9.84-14.76 mils). This ceramic-filled epoxy coating provides excellent resistance to abrasion and corrosion.
- Inspection and Touch-Ups: Once the Belzona products had cured, a thorough visual inspection was conducted. Any areas needing touch-ups were marked, abraded, and re-coated to ensure a uniform finish.
- Hydrostatic Testing: Before the heat exchanger was returned to service, the Customer performed a hydrostatic test under a pressure of 30 kg/cm² (426.7 psi), verifying the integrity and reliability of the repair.
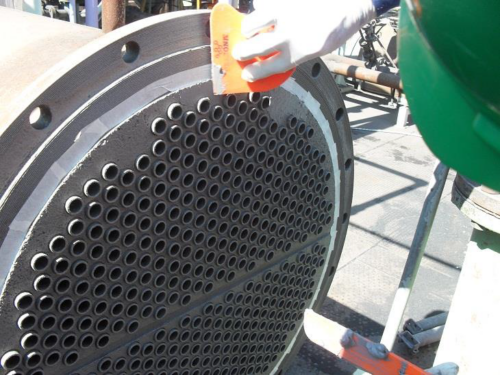
The Results: Enhancing Heat Exchanger Maintenance Efficiency
The Customer expressed satisfaction with the heat exchanger maintenance, as the in-situ application eliminated the need to disassemble the heat exchanger, thus saving time and labor costs. Belzona’s products not only resolved the corrosion issue but also enhanced the efficiency of the heat exchanger, ensuring it continues to perform optimally in the steel manufacturing process.
Regular heat exchanger maintenance is critical for the steel and metal processing industry to ensure equipment longevity and operational efficiency. Belzona’s innovative in-situ solutions offer proven protection against common issues like galvanic corrosion, helping companies maintain high levels of productivity.
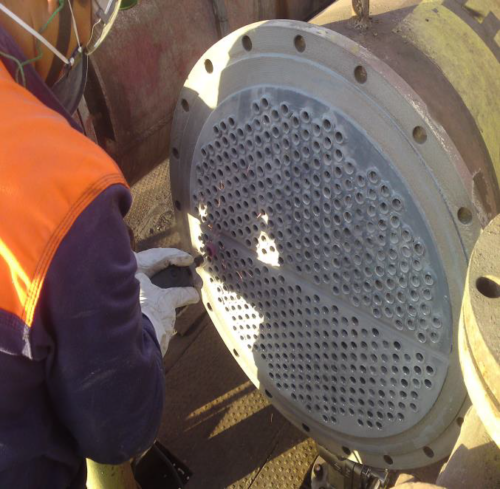
For more information on how Belzona can support your needs, contact us today.
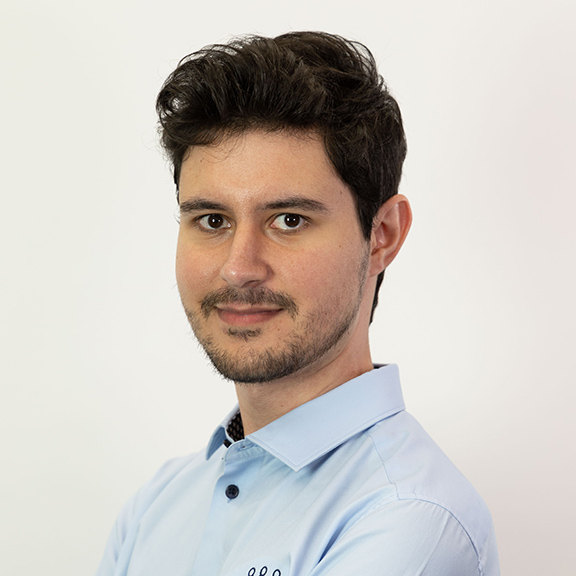
Digital Content Creator, Belzona Inc., Miami, Florida