Corrosion can cause numerous issues within HVAC equipment. If left without maintenance repairs, equipment can decrease in efficiency and service life. Replacement costs can be incredibly high and can result in downtime, having an impact on productivity. In the blog post “HVAC Maintenance: Corrosion in Heating and Cooling Systems”, we discussed HVAC maintenance and the types of alternative repair options available.
IN DEPTH – HEAT EXCHANGER DAMAGE AND REPAIR
More specifically within HVAC maintenance, heat exchangers are a crucial part of heating and air conditioning systems. Failure to protect these units quickly allows galvanic corrosion to take place, leading to significant metal loss on the tube sheet around the coolant tubes – a common problem encountered. Left untreated, the loss of metal will allow leakage of the coolant and contamination of the chilled water.
Corrosion is not restricted to the tube sheet, as the water box and end covers are also susceptible to severe deterioration. In particular, corrosion of division bars and seal faces can cause leakage and bypassing on multi-pass systems, leading to loss of efficiency.
Metal repair composites and epoxy coatings can be used for the repair and protection of heat exchangers, including areas such as tube sheets, water boxes and end covers, amongst many more. To protect against galvanic corrosion and chemical attack, cold applied systems facilitate in-situ applications, minimising downtime whilst providing long-term erosion and corrosion protection.
CASE STUDY: REPAIRING A SEVERELY DAMAGED HEAT EXCHANGER
APPLICATION OVERVIEW
This particular heat exchanger was in service for 4 years and subject to chemical corrosion generated by hydrochloric acid (5-10%) at a temperature not exceeding 35°C (95°F). Due to the aggressive environment, there was severe damage caused by corrosion. The original thickness of the metal was reduced throughout the heat exchanger, with the tubular plate in an especially critical state. The sealing between the plate and the tubes was lost, severely restricting performance, or causing it not to run at all.
The replacement costs were incredibly high for such a piece of equipment. In addition, replacing the heat exchanger would also add a further problem of a lengthy production downtime. The Customer required a solution that avoided the need for replacement, had a fast turnover time, high durability and outstanding chemical resistance.
BELZONA SOLUTIONS SPECIFIED
Belzona 1111 (Super Metal)
Due to the severe damage caused by corrosion, the surface of the Heat Exchanger needed to be rebuilt back to its original profile. Belzona 1111, an epoxy-based repair composite, was chosen due to its outstanding resistance to corrosion and a wide range of chemicals. The multi-purpose repair system is able to be applied without the need for specialist tools, making for a simple application.
Belzona 4341 (Magma CR4)
A coating was then required to provide future long-term corrosion and chemical resistance. For this purpose, Belzona 4341 was chosen. The chemical resistant epoxy coating, optimised for resistance to hot inorganic acids, isolates metal and concrete surfaces from deteriorating chemical environments.
Heat Exchangers – Erosion and Corrosion Protection
Belzona offers a wide range of metal repair composites and epoxy coatings to repair damaged heat exchangers and provide erosion and corrosion protection for different application situations. Discover more below:
The Application
Surface Preparation
All the tubes of the heat exchanger were blocked with tapered corks off ahead of surface preparation. The surface was then grit blasted to Swedish Standard Sa 2 ½ / American Standard SSPC SP10 cleanliness with a minimum profile of 3 mils (75 microns) using angular grit. In order to remove any further debris or contaminants, the surface was cleaned using Belzona 9111, a general cleaner and degreaser. The tapered corks were then removed, and replaced with new ones ahead of the surface rebuilding application.
Rebuilding the Surface
Due to the severely eroded surface, Belzona 1111 was used to restore the areas back to the original profile. The material was applied to the entirety of the tube sheet. Once cured, the system was sanded back to the tampered corks, allowing them to be drilled out, revealing the newly restored surface profile.
In the most eroded areas, such as the division bar located in the end plate, metal mesh was used to support the rebuilding of the surface and restore the bar back to its original state.
Applying a Chemical Resistant Epoxy Coating
In order to provide future long-term protection against the harsh chemical environment, Belzona 4341 was applied in two coats. The 2-part epoxy barrier coating is optimised for resistance to hot inorganic acids such as sulphuric and hydrochloric acid up to 90°C (194°F). Unlike other alternative methods, the Customer was impressed with the outstanding chemical resistance, adhesion levels and the simplicity of application.
The heat exchanger application was carried out by Rodator, a Belzona Authorised Distributor based in Asturias, Spain. The results exceeded all expectations from the Customer. The Belzona solution eliminated replacement costs and downtime was kept to a minimum.
The heat exchanger application was carried out by Rodator, a Belzona Authorised Distributor based in Asturias, Spain. The results exceeded all expectations from the Customer. The Belzona solution eliminated replacement costs and downtime was kept to a minimum.
THE FINISHED APPLICATION
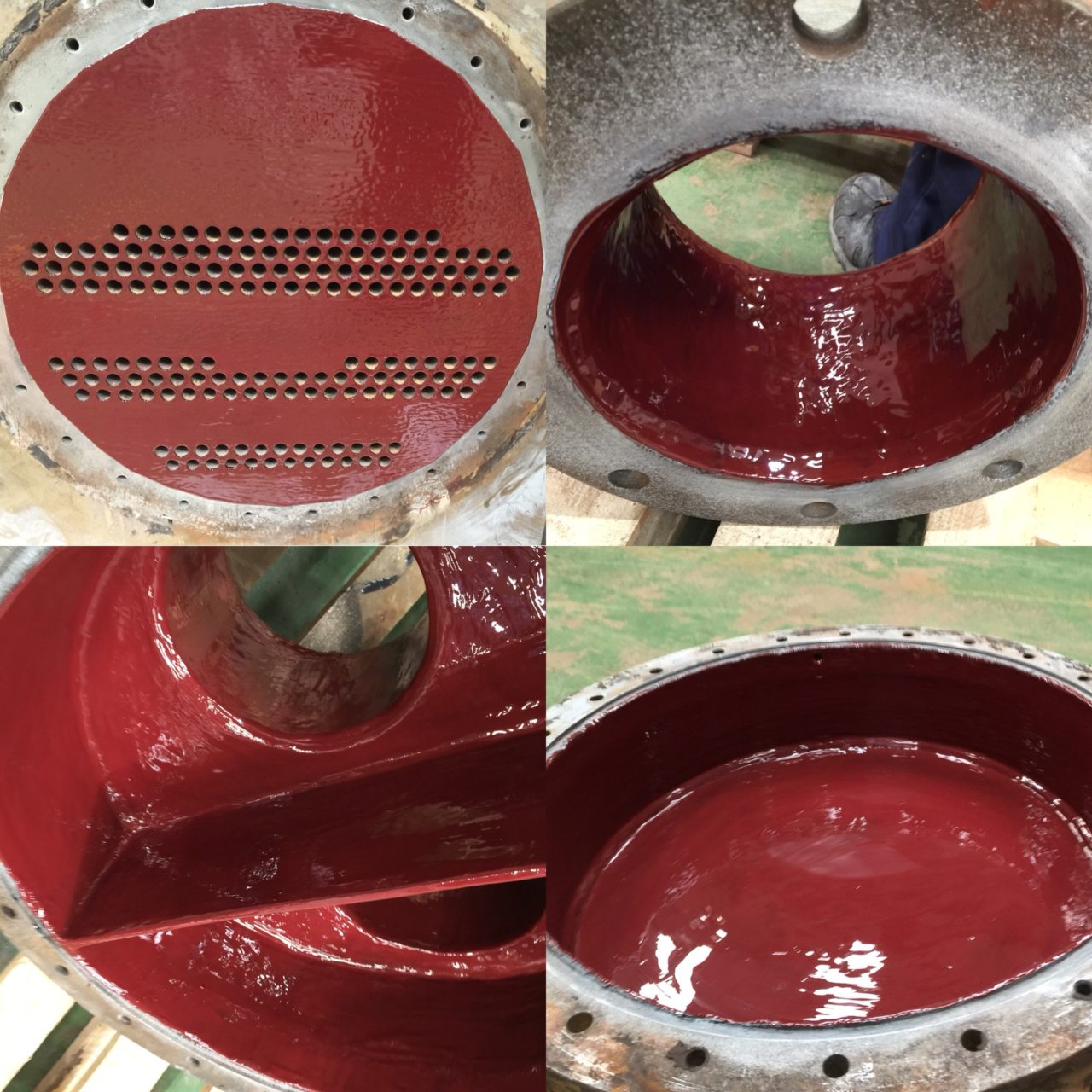
Discover more of Belzona’s solutions for the HVAC industry:
Focus Area: Heating, Ventilation and Air Conditioning
Belzona Case Studies for Heat Exchanger Repairs