Video: How to Repair a Heat Exchanger
Introduction to Heat Exchanger Repair
Leakage of system fluids across the tube sheet and cracking of tube sheet ligaments are two of the most common problems affecting heat exchangers. These issues are often caused by wastage and weakening of the ligaments due to electrolytic corrosion, which compromises the structural integrity of the tube sheet over time.
If left unaddressed, these types of damage can lead to severe operational inefficiencies, costly downtime, and potential safety hazards.
Keeping heat exchangers in optimal condition is essential for industrial facilities to function efficiently and avoid expensive heat exchanger replacement costs. Replacing an industrial heat exchanger can be a significant investment, with depending on several factors such as design pressures, temperatures and materials (carbon steel vs. stainless vs. exotic alloys). This highlights the importance of regular maintenance and timely repairs to prevent extensive damage and the need for costly replacements.
This guide provides a step-by-step guide to heat exchanger repair using epoxy composites and industrial coatings, ensuring long-term durability against heat exchanger corrosion.
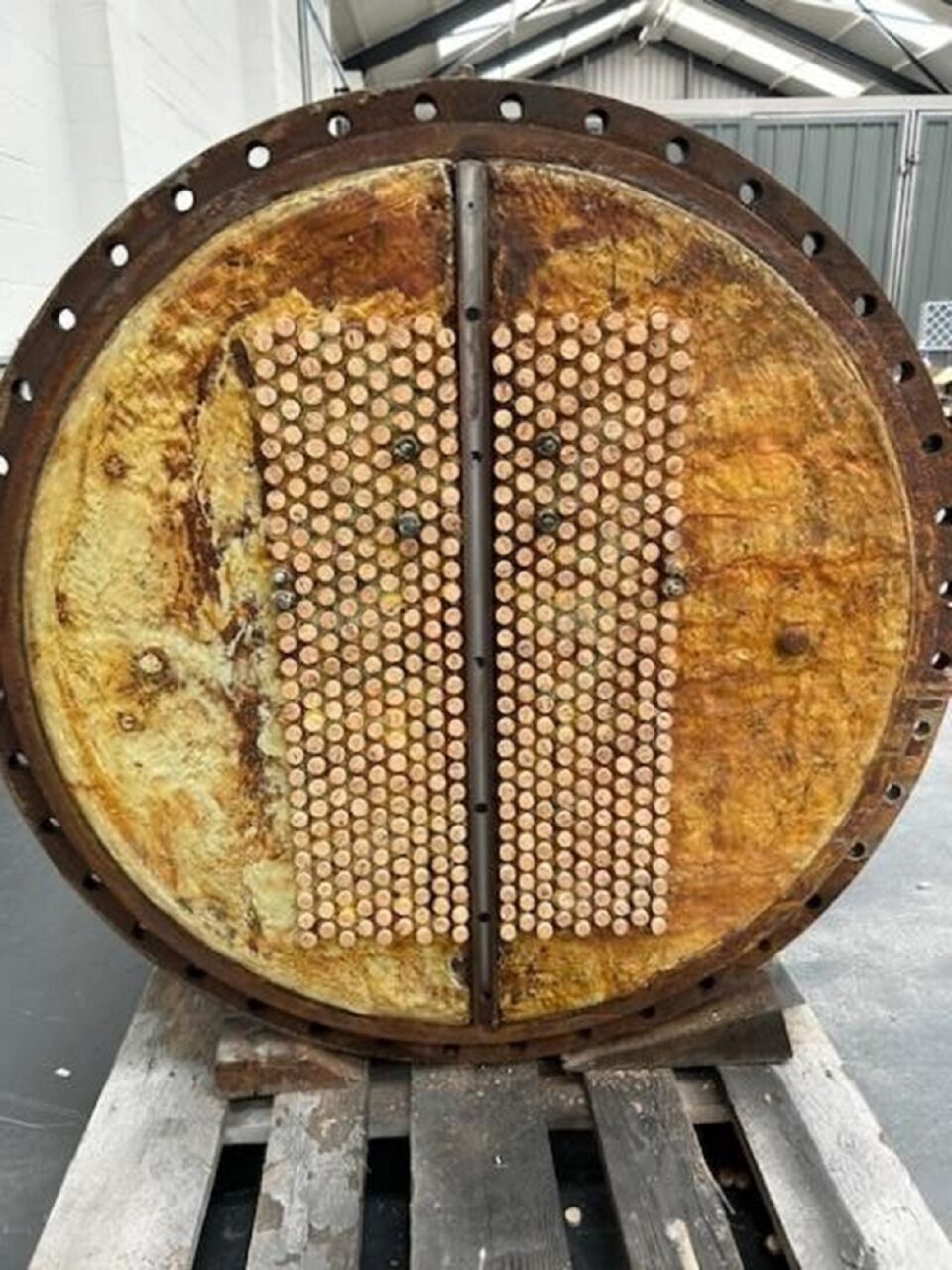
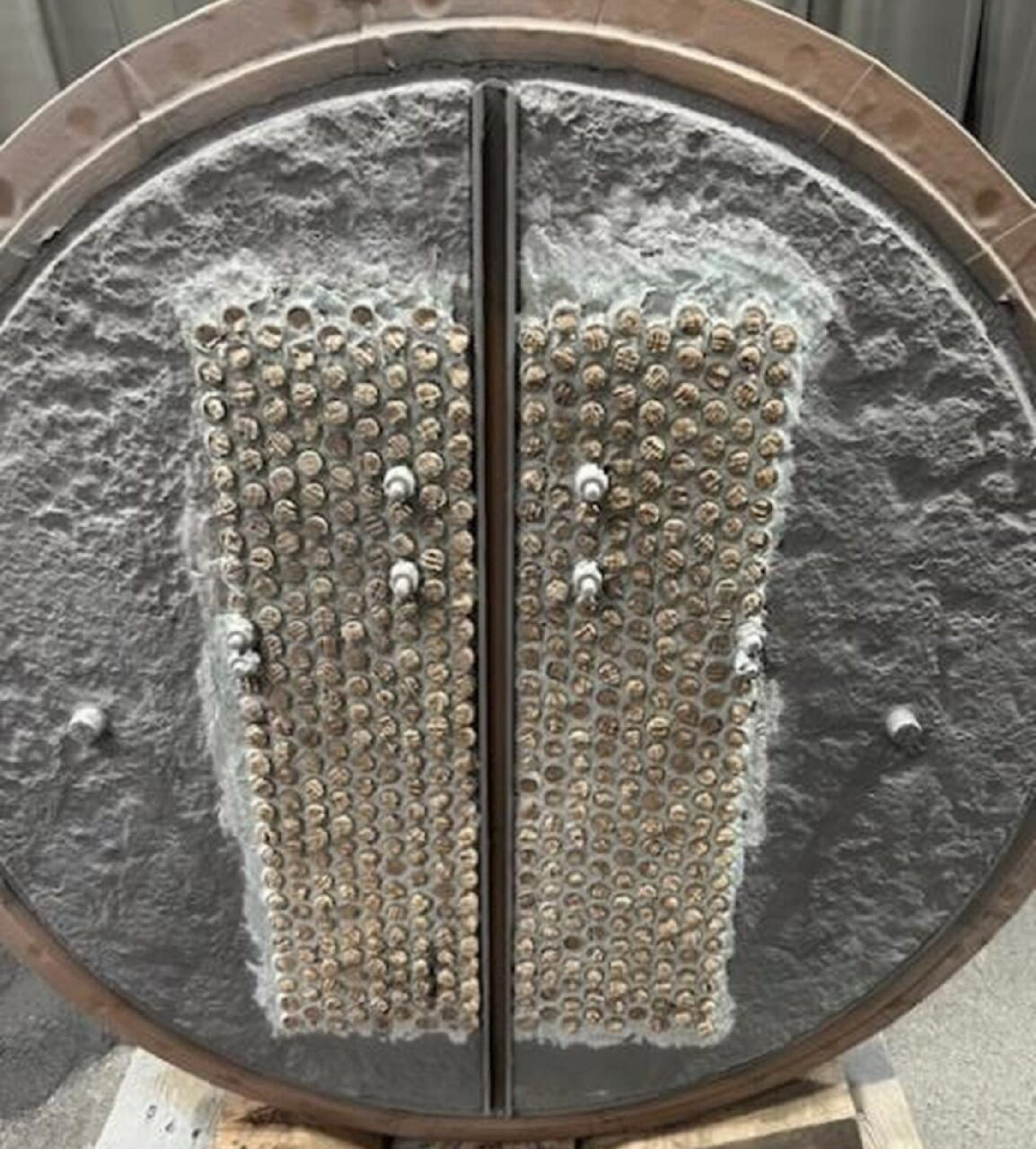
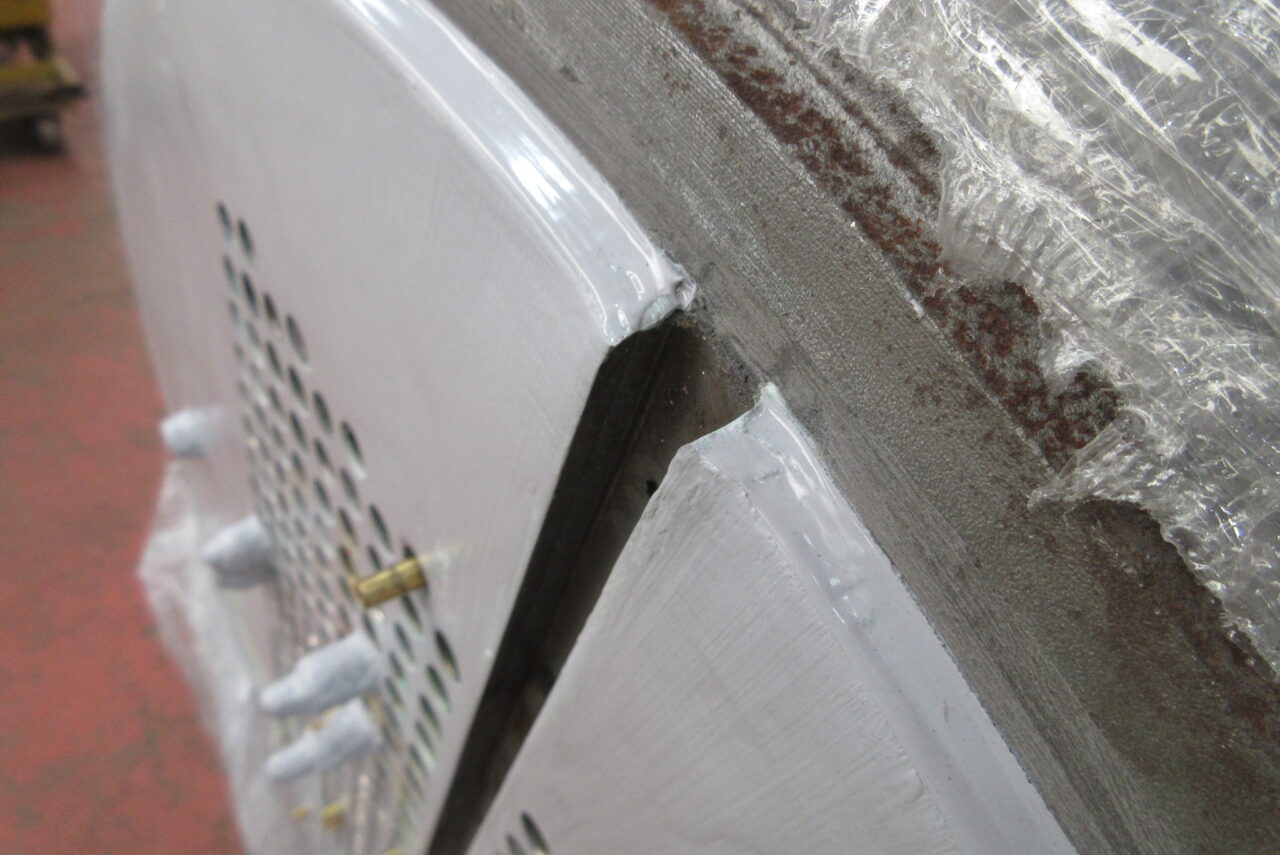
Common Causes and Risks of Damaged Heat Exchanger
Heat exchangers play a vital role in heating and cooling systems, particularly in industrial and HVAC applications. However, various factors can contribute to damage, including
- Galvanic Corrosion – Often occurs on the heat exchanger tube sheet, leading to metal loss and leaks.
- Chemical Attack – Exposure to harsh chemicals can deteriorate metal surfaces over time
- Thermal Stress – Fluctuations in temperature can cause cracking, particularly in welded areas.
- Erosion and Wear – Continuous exposure to fluid flow and contaminants can thin the metal walls.
- Leakage of System Fluids – This can occur across the heat exchanger tube sheet due to wastage of the tube sheet ligaments caused by electrolytic corrosion.
- Cracking of Ligaments – Electrolytic corrosion can weaken the ligaments, leading to structural cracks that compromise the integrity of the heat exchanger.
If left untreated, a corroded heat exchanger can result in leaks, contamination of the working fluid, and reduced efficiency.
Step-by-Step Guide: How to Repair a Damaged Heat Exchanger Using Epoxy Composites and Industrial Coatings
Step 1: Surface Preparation
Correct surface preparation is essential for a successful, long-lasting repair. Follow these simple steps:
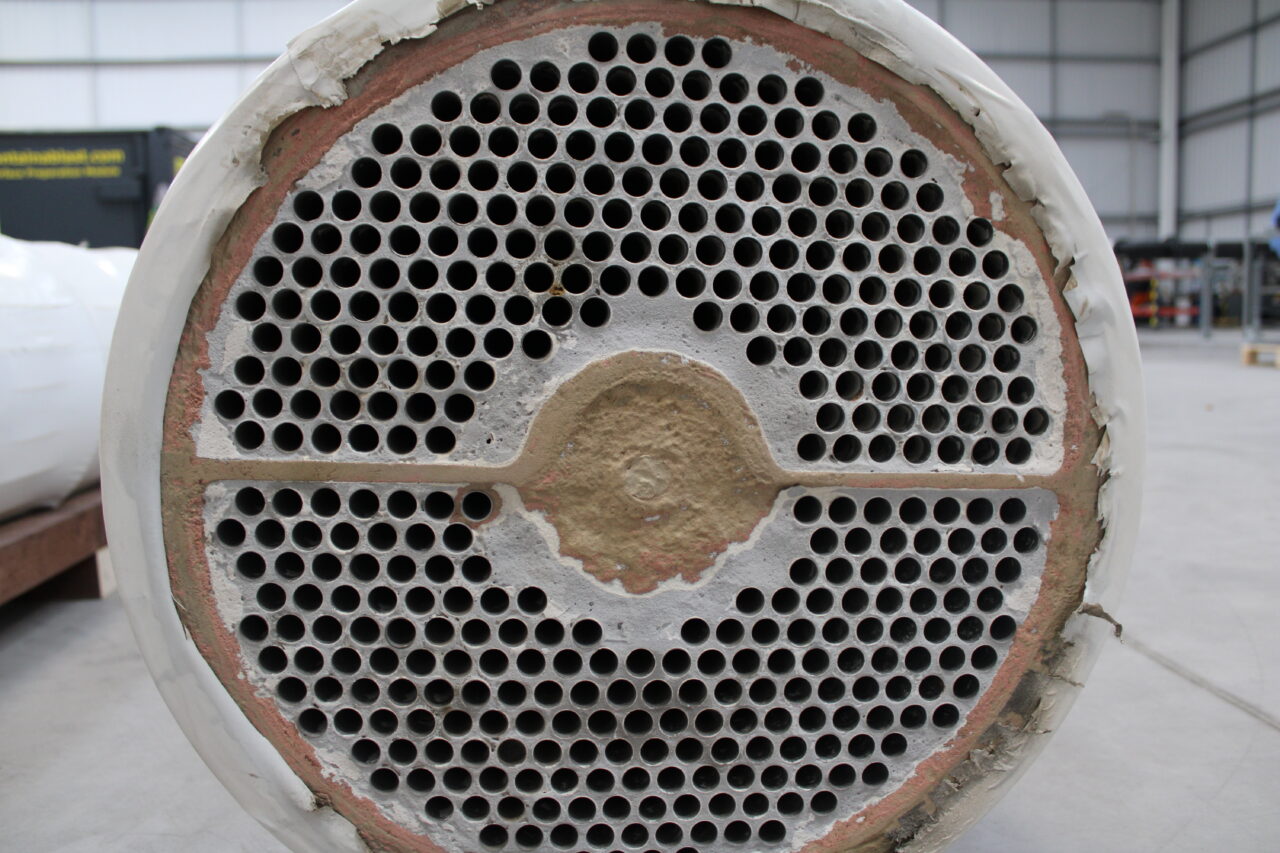
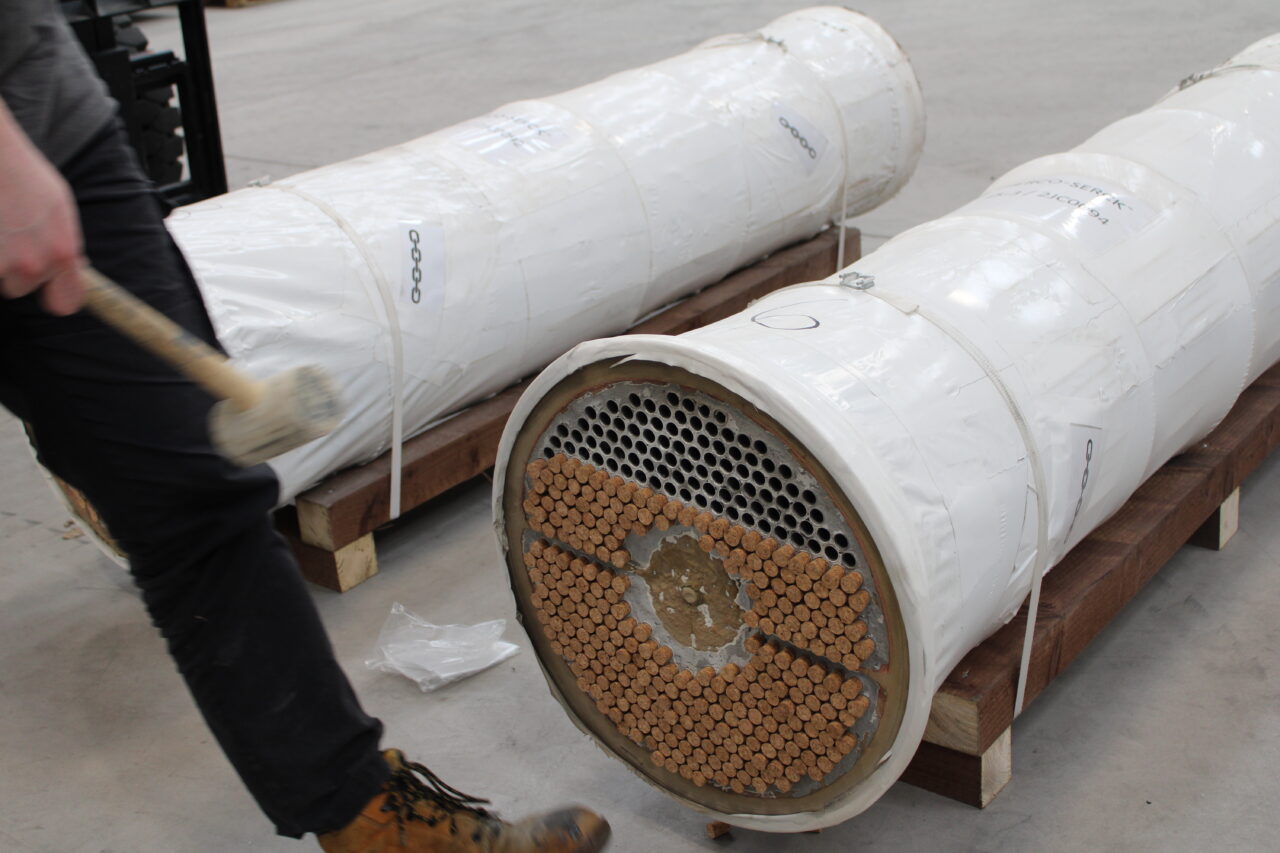
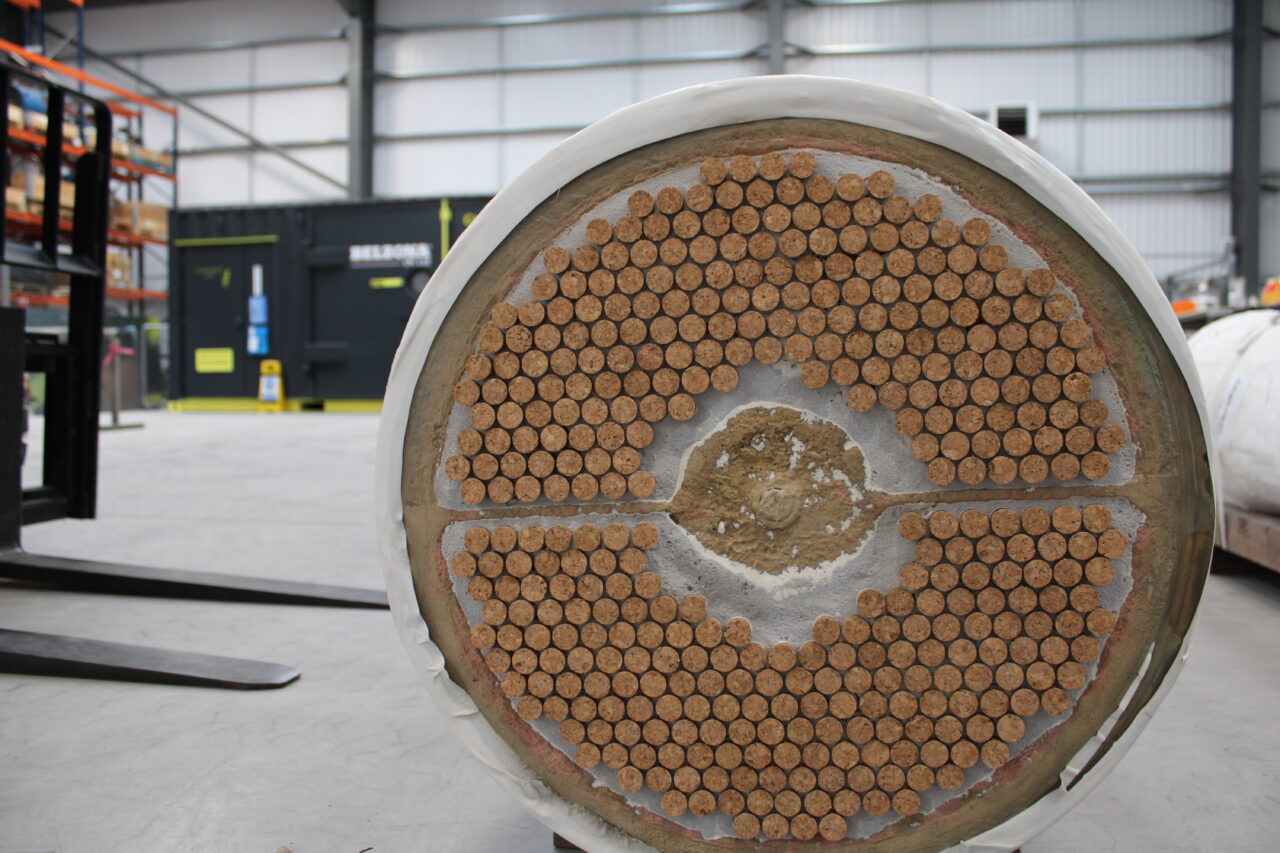
- Block the tubes – Use tapered corks or plugs to prevent debris from entering the tubes.
- Grit blast the area – Clean the surface to Swedish Standard Sa 2 ½ / American Standard SSPC SP10, ensuring a minimum profile roughness of 75 microns for proper adhesion.
- Degrease the surface – Use Belzona 9111 to remove any residual contaminants.
- Remove the corks and replace with new ones prior to the surface rebuilding application.
Step 2: Rebuilding the Damaged Areas
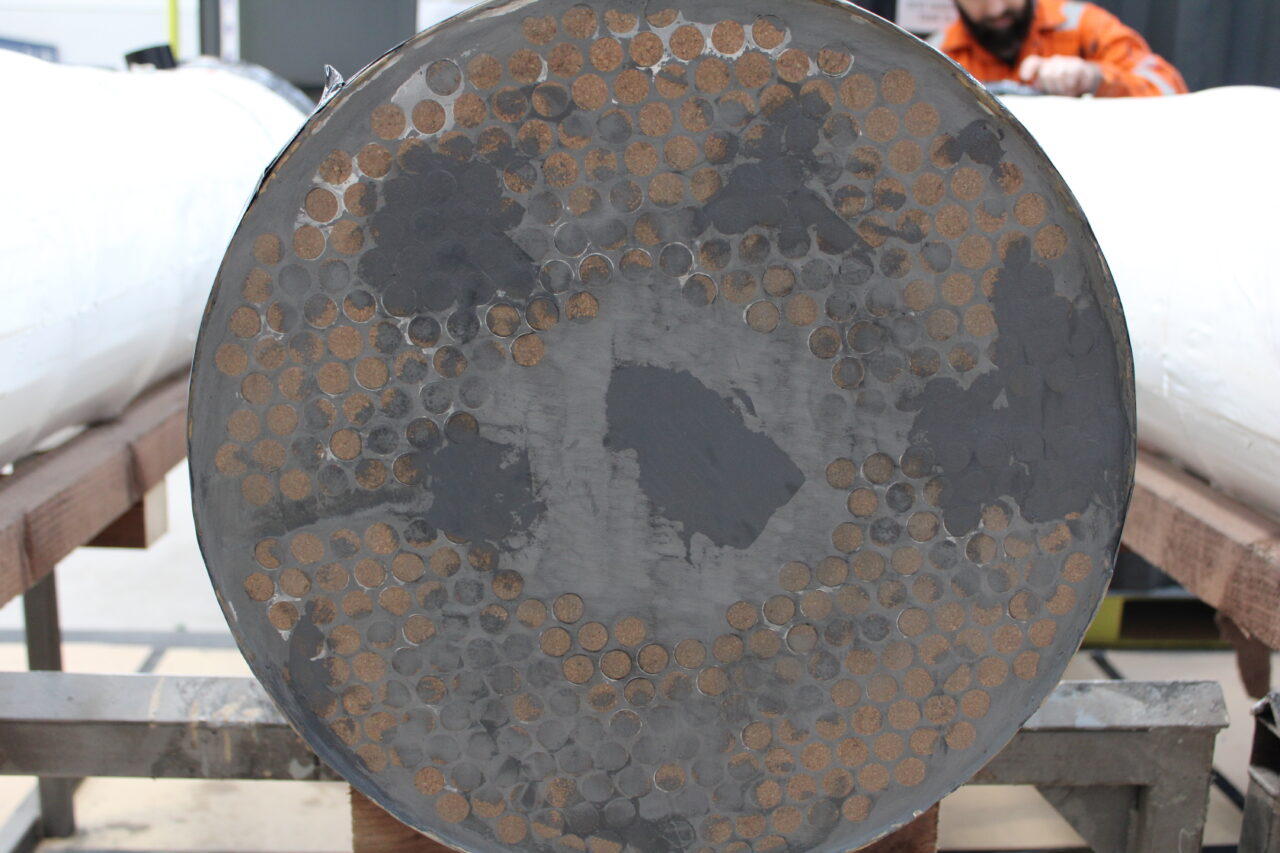
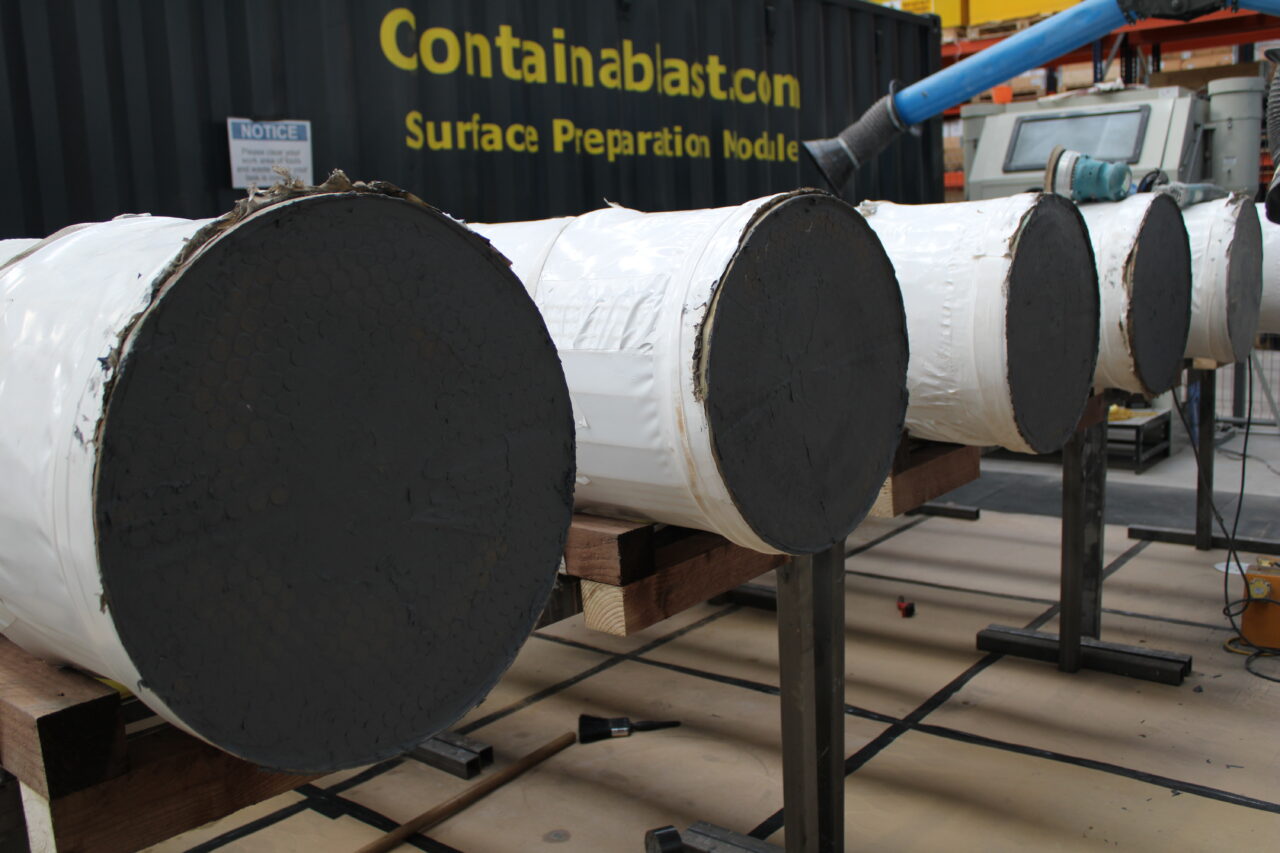
Apply a Belzona metal repair composite such as Belzona 1111 (Super Metal) to rebuild the damaged areas and restore the original profile.
Use reinforcement in critical areas – For heavily eroded, critical area incorporate a reinforcement mesh to reinforce the repair and restore structural integrity.
Allow the Belzona rebuilding material to cure before sanding it back to achieve a smooth, uniform surface.
Step 3: Applying a Protective Industrial Coating
Following rebuilding of the tube sheet, mix a selected Belzona fluid grade coating such as Belzona 1321 (Ceramic S-Metal) and using short bristle brushes, apply two even coats to the entire tube sheet. This will ensure long-term protection of the heat exchanger.
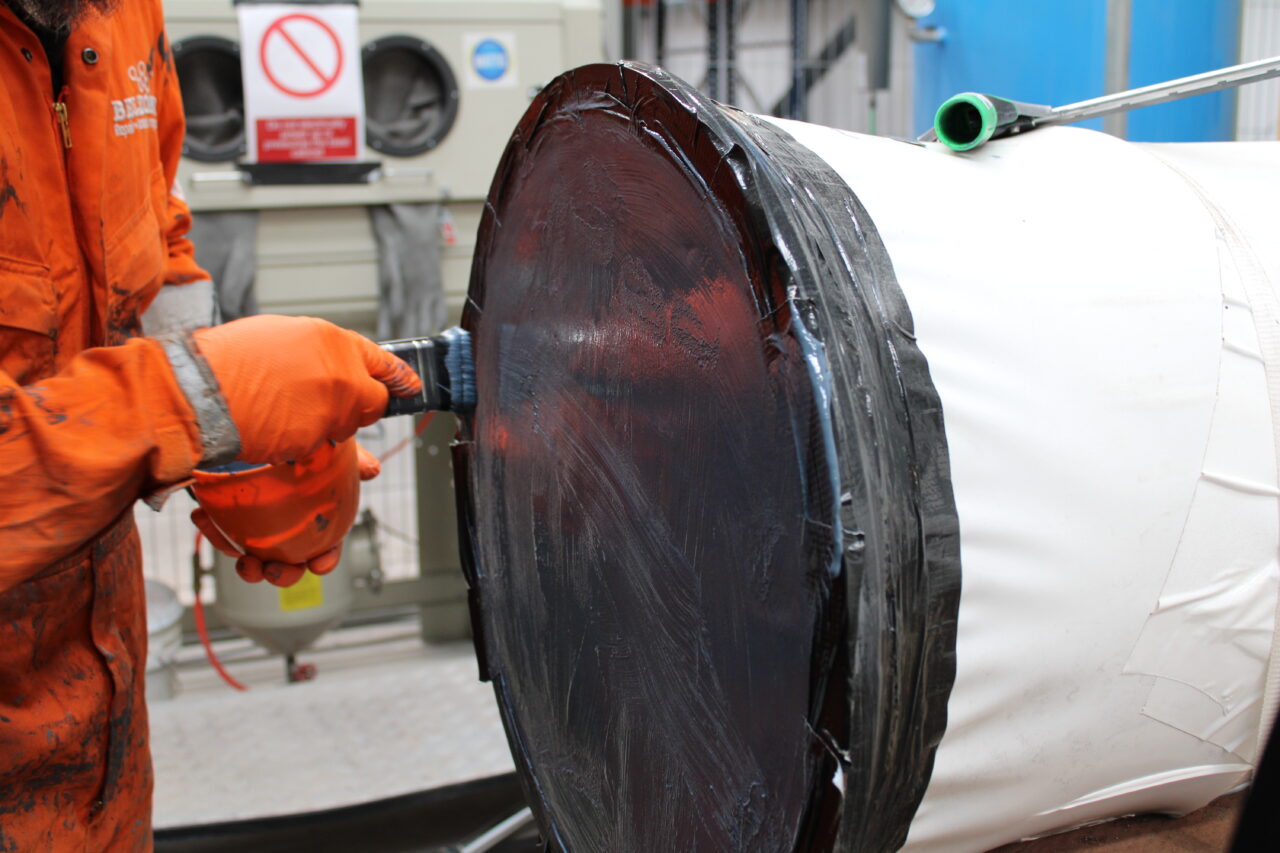
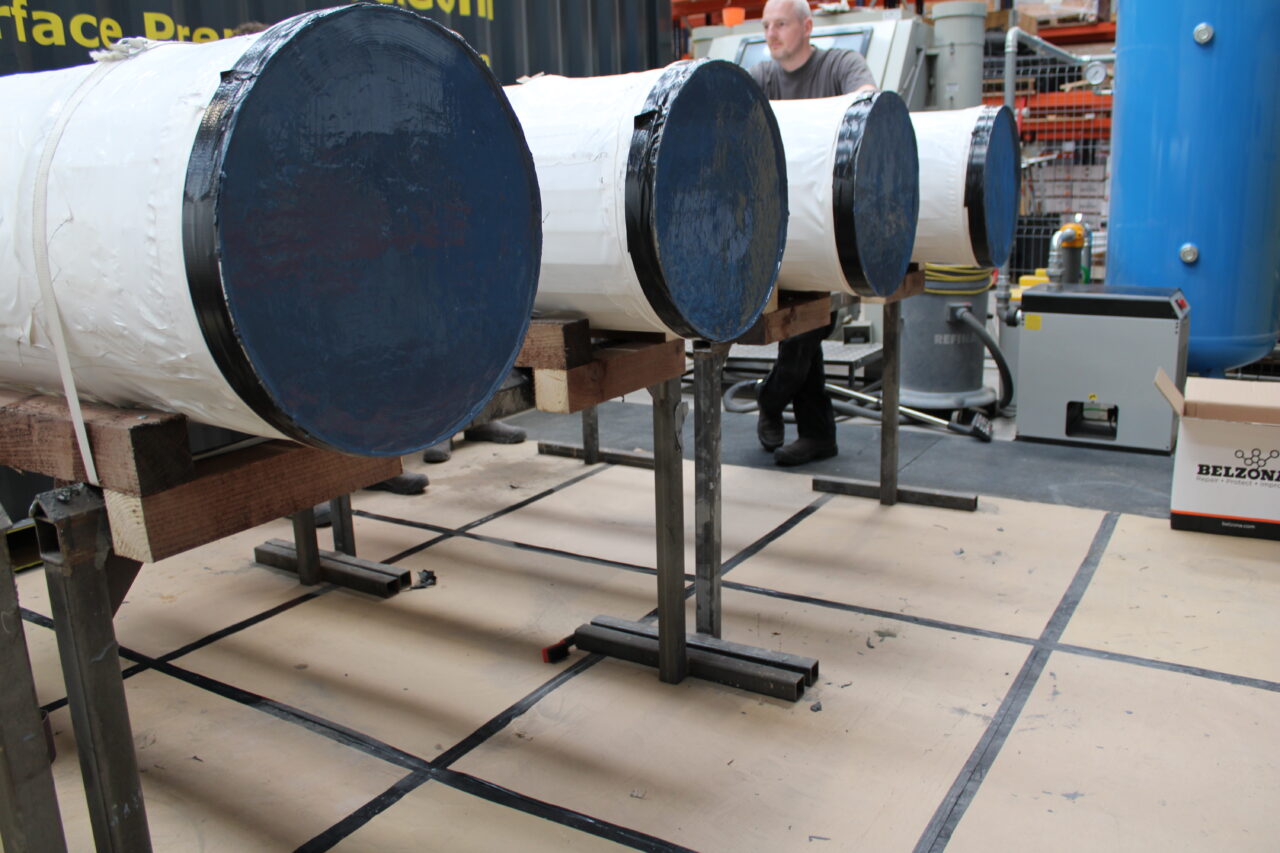
Following completion of the application of all Belzona materials and, after the designated cure time, gently remove the corks with a ball peen hammer. Chamfer all tube ends using a conical grinding stone (deburr the tube ends).
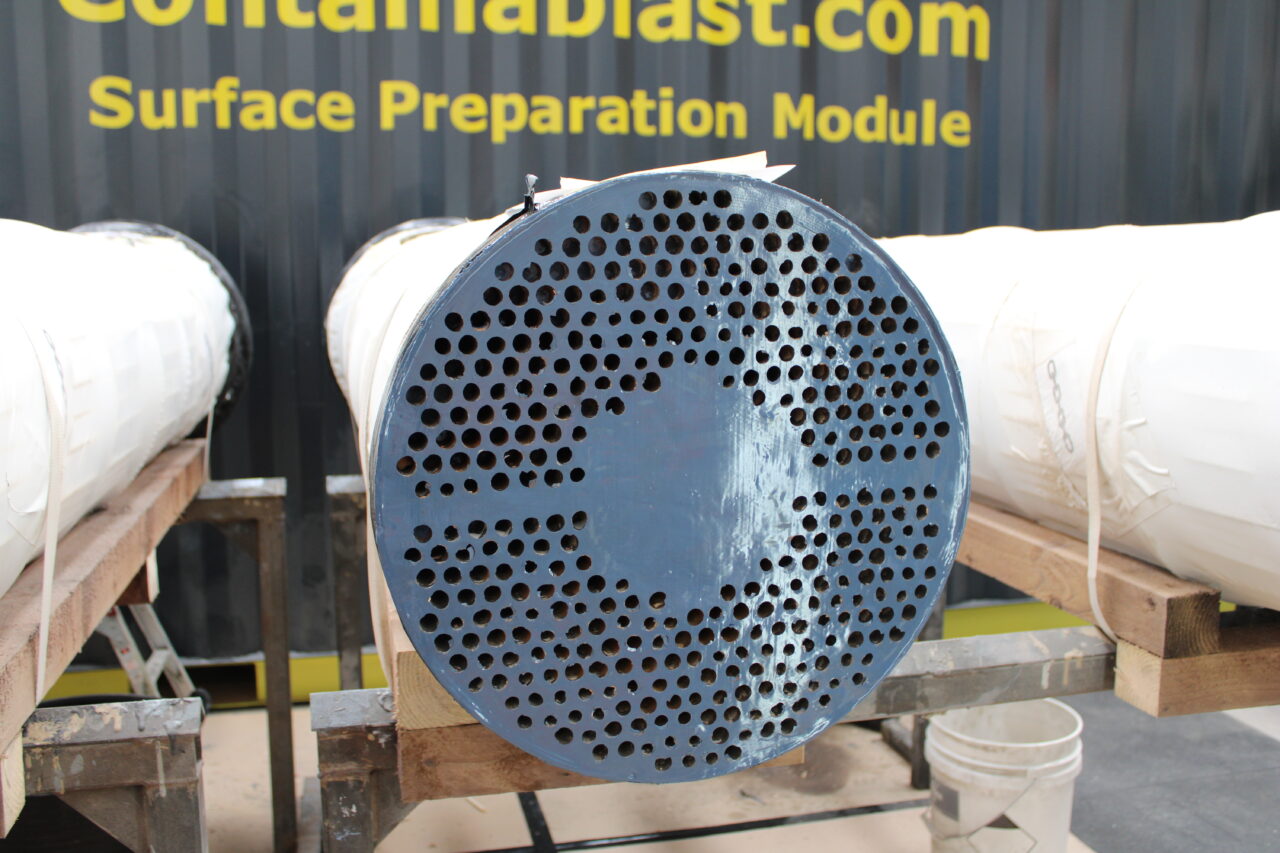
Belzona industrial coatings can be specified for a variety of in-service conditions including erosion, corrosion, high temperature and chemical attack. For product specification, please contact a Belzona Distributor.
Inspect and test – Once cured, inspect the coating and ensure the coating integrity before returning the heat exchanger to service.
Why Chose an Epoxy-Based Heat Exchanger Repair?
- Cost savings – Avoids the high heat exchanger replacement cost associated with new equipment.
- Minimised downtime – Repairs can be carried out in situ, significantly reducing operational disruptions.
- Long-term protection – Prevents future heat exchanger corrosion and extends service life.
Conclusion
Addressing a damaged heat exchanger promptly with epoxy-based heat exchanger repair solutions can prevent costly replacements and ensure continued efficiency. Implementing routine heat exchanger maintenance and using industrial coatings for protection can significantly extend equipment life and performance.
For expert guidance and high-performance repair materials, contact a Belzona Distributor today!
Frequently Asked Questions
How long does a heat exchanger repair last?
When properly applied, high-performance industrial coatings can extend the lifespan of a heat exchanger for several years. This example was in service for 35 years. https://khia.belzona.com/khia/VERY_OLD_BELZONA_TUBE_SHEET_REPAIR
What are the signs of a damaged heat exchanger?
Common indicators include reduced efficiency, fluid leaks, unusual noises, and visible corrosion on the heat exchanger tube sheet.
Can a heat exchanger be repaired instead of replaced?
Yes, using epoxy composites and protective coatings can effectively restore structural integrity and prevent further damage.
Where can I find a Distributor for Belzona heat exchanger repair solutions?
Find an Authorised Distributor near you: Belzona Distributor Finder
Learn More
Case Study: Heat Exchanger Repair for Chemical Resistance
Case Study: Heat Exchanger Maintenance in Steel Manufacturing
Contact Your Local Distributor to Learn More About Belzona Solutions for Heat Exchangers
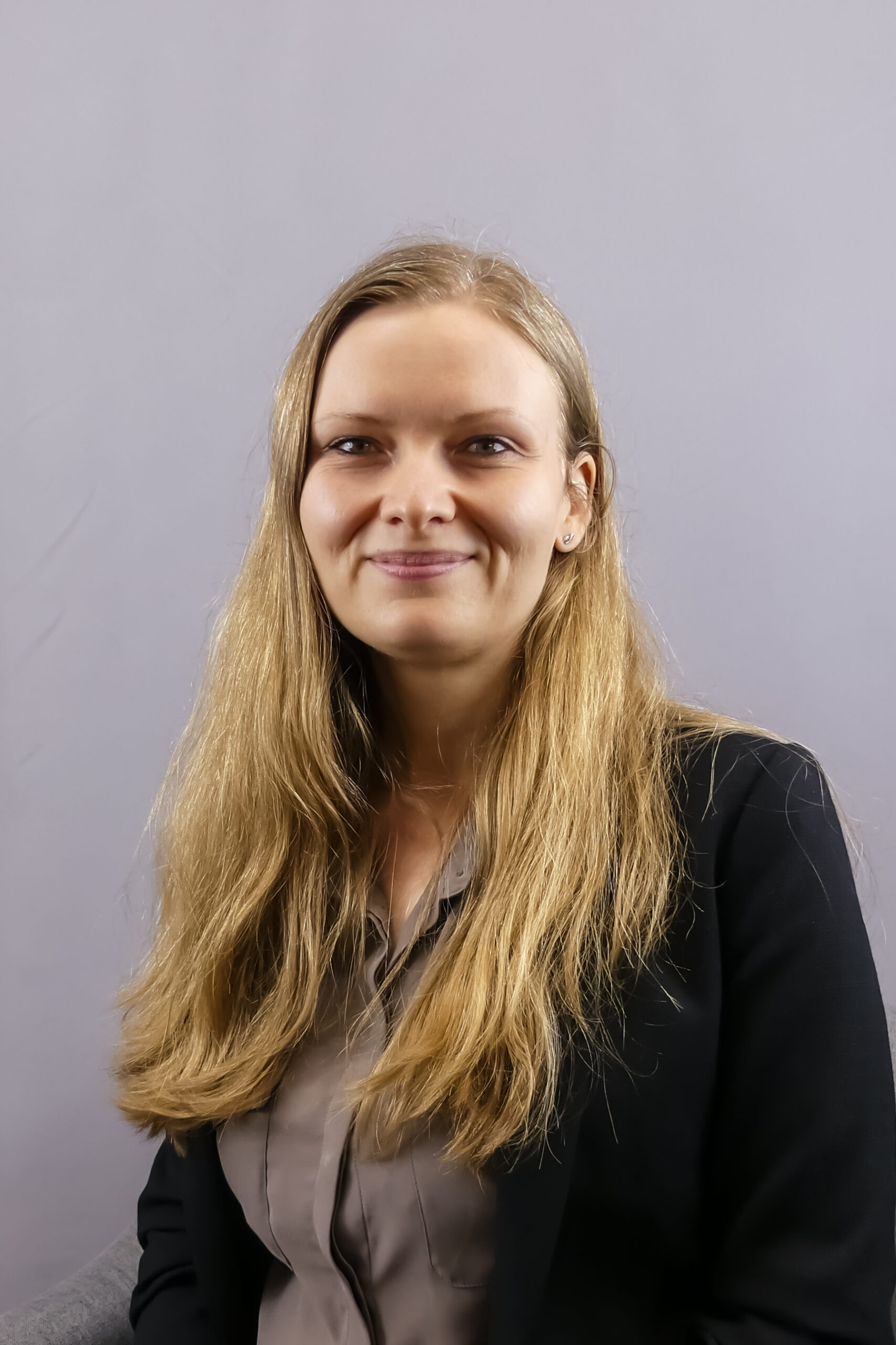
Natalija Skrlec joined Belzona in 2022; since then she has been promoted to the position of Technical Service Engineer based at the Company’s Headquarters in Harrogate. Her main responsibilities involve delivering technical application support and hands-on training in English and German speaking markets.
She graduated with a master’s degree from the University of Ljubljana in Slovenia in 2009 and holds an AMPP (NACE) Coating Inspector Level 1 certification.
Through her technical knowledge and hands-on experience, Natalija supports the application of Belzona’s polymeric solutions across multiple industries worldwide. She is passionate about continuous knowledge exchange, and believes it is the key to engineering excellence and Distributor success.