Many process vessels or/and storage tanks in industry are commonly subjected to a wide variety of aggressive chemicals and elevated temperature. What solutions are out there to maintain process vessels and storage tanks in tact? Are their alternatives to the traditional repair methods? What role do high-temperature coatings have been playing recently in protecting these assets?
For this episode of our podcast we sat down with Osmay Oharriz – Belzona Oil and Gas Industry Manager – to discuss the challenges that the storage tanks industry faces and how high-temperature coatings have increasingly become popular amongst the asset owners.
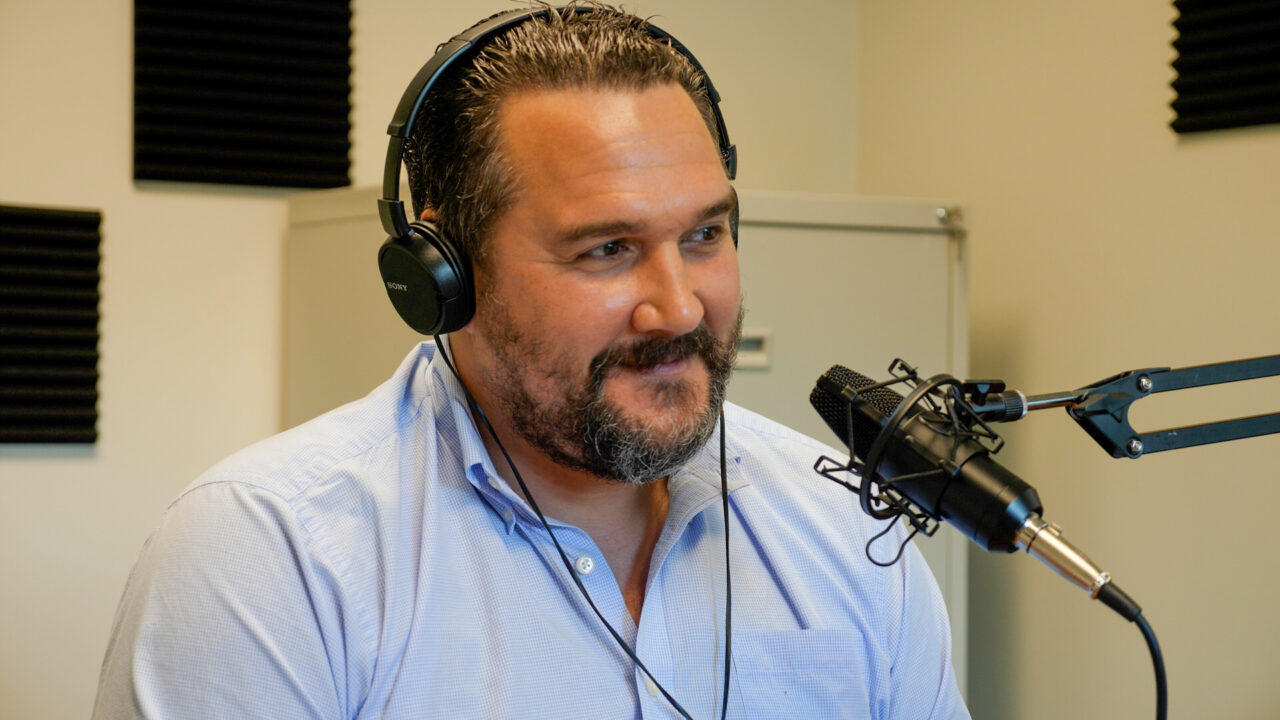
Osmay explains:
In many industries, most process vessels and storage tanks are made of carbon steel because. It is a readily available material and inexpensive in comparison to other alloys or more exotic materials.
Osmay Oharriz, Oil and Gas Industry Manager, Belzona 2021
The problem arises when carbon steel is exposed to several chemicals combined with elevated temperatures and pressures. However, it is not the stream to be processed but the chemicals added to aid in the processing of such a stream. They often lead to corrosion or other damaging effects to carbon steel. As a result of this interaction of carbon steel and its service environment, corrosion/erosion, or a combination of both can occur leading to interrupted operations (forcing the process to be halted and re-started – which is, believe it or not, the most costly issue).
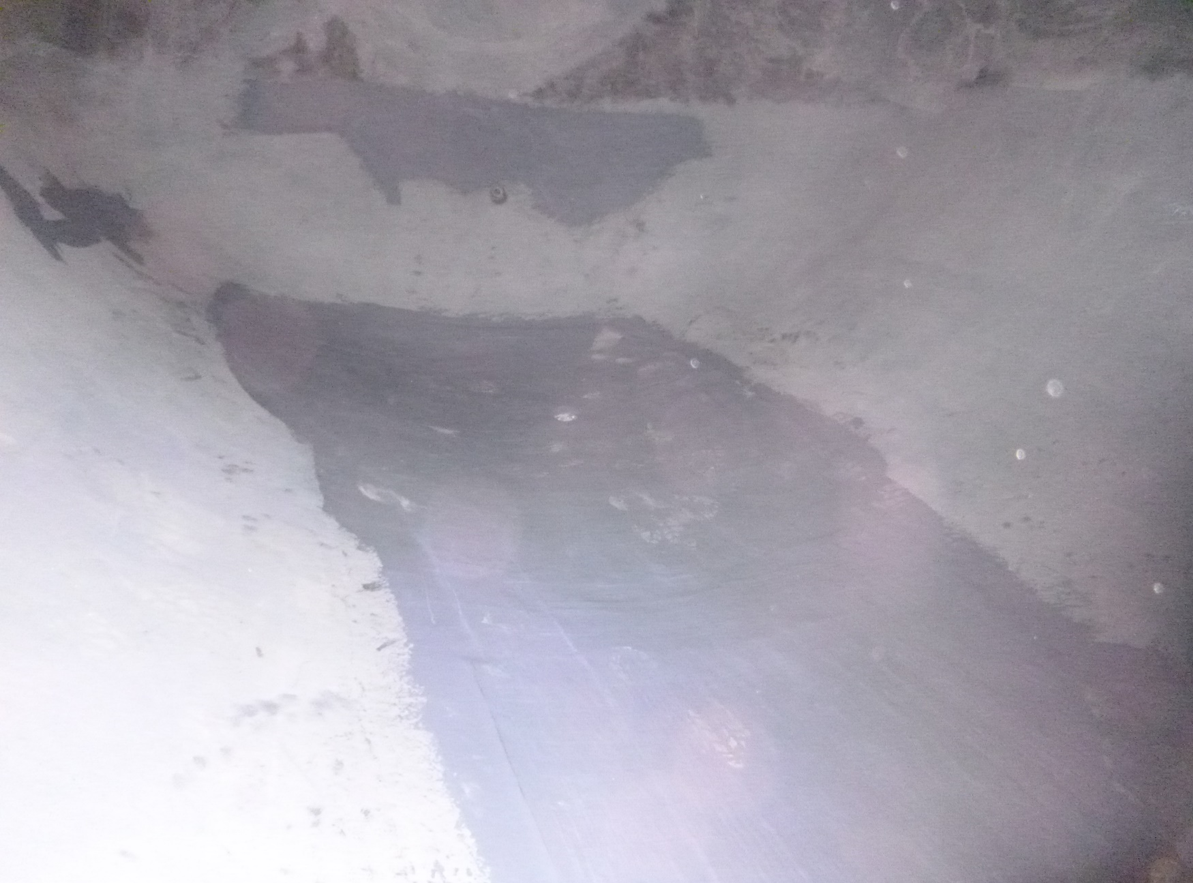
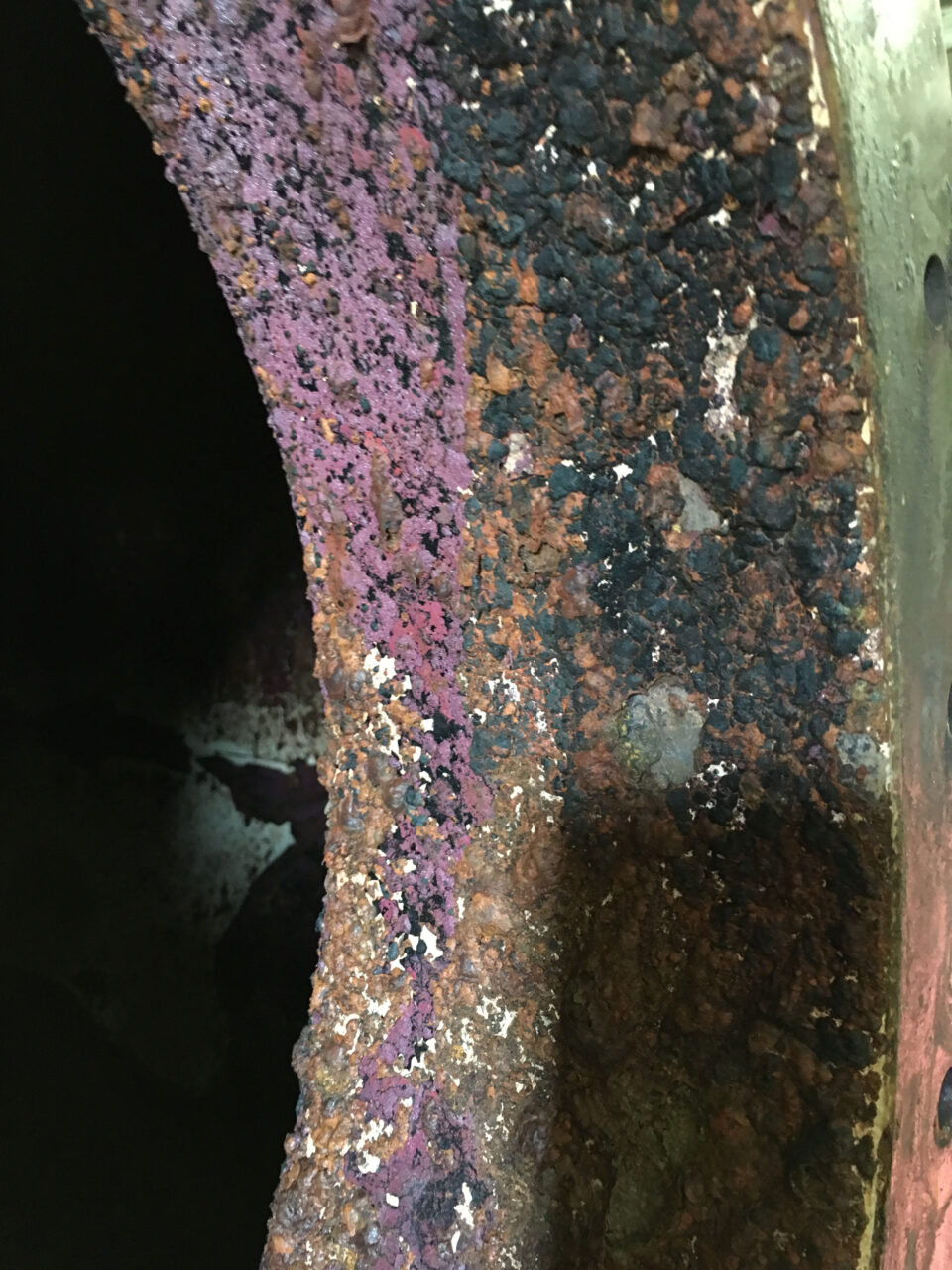
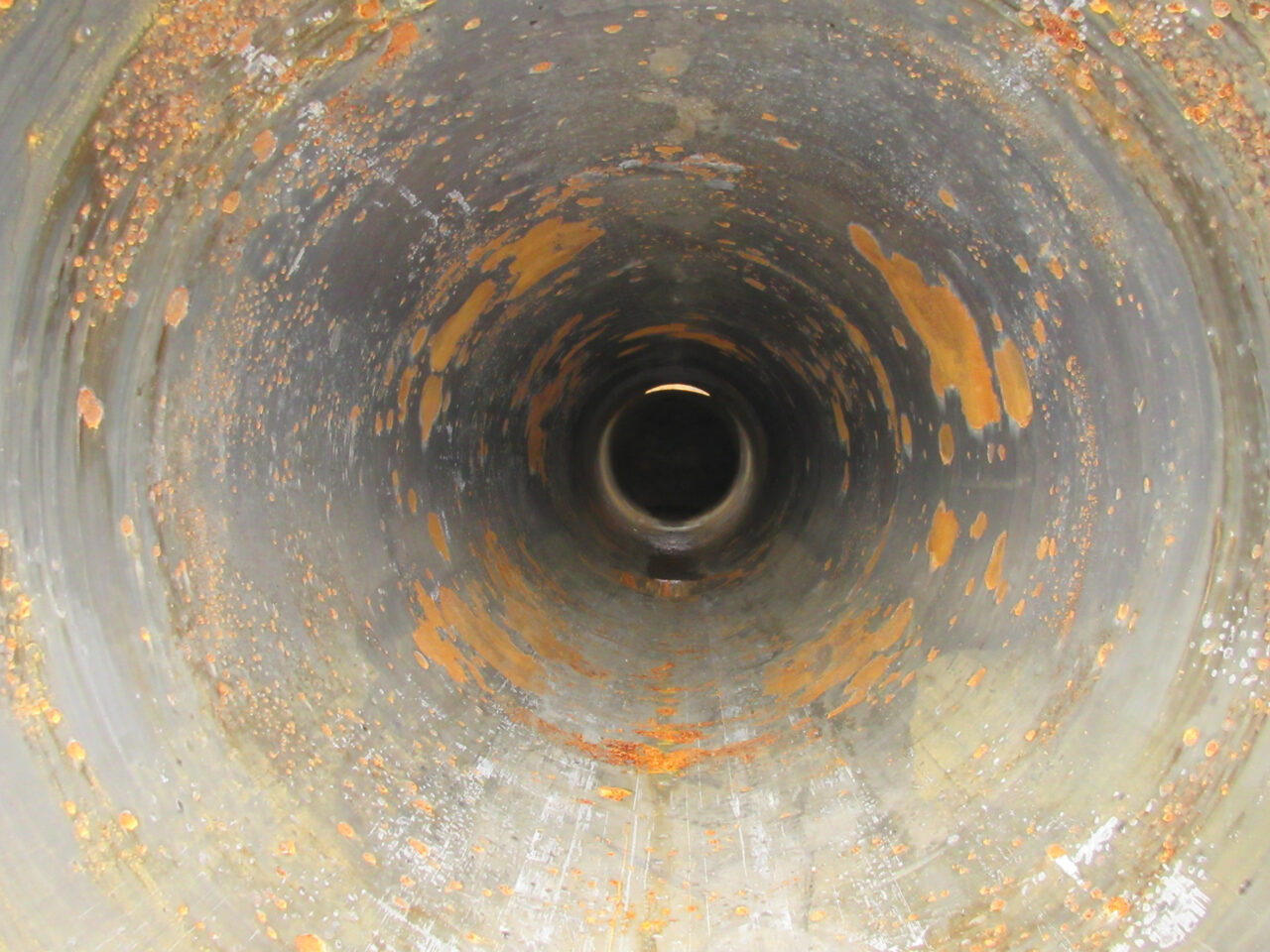
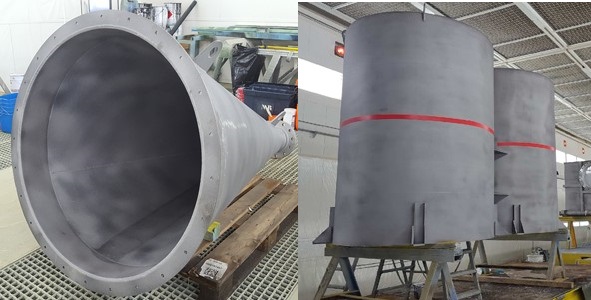
Correlation between elevated temperatures and pressures
Based on his experience, Osmay explains, the thermal threshold is around 90 – 100 °C (194 – 212 °F). Any services above 212 °F are typically considered elevated temperature. In fact, several industries divide corrosion into low temperature and high temperature corrosion based on the presence of water. Evidently as temperature increases, corrosion models do not include aqueous conditions. Pressure plays a big role too. The higher pressures and elevated temperatures are a way more critical situation than higher pressures and lower temperatures for instance. Pressure levels above 1000 psi (70 bar) can become problematic if combined with high temperatures. There are so many industrial processes with varied services, that it’s hard to assign a critical number to both parameters.
Is carbon steel the only metal that sees this problem?
Predominantly, yes! However, some metals and alloys tend to form a protective surface film, known as passivation. For instance, carbon steel can form a protective sulfide layer. But the presence of other chemicals in the service, destroy this layer exposing carbon steel to the chemical service. Stainless steels for instance, can passivate. But if chloride ions are present, these ions can destroy this protective layer and induce pitting. So, it is not only related to carbon steel. It can also present in other materials of construction.
Knowing that corrosion is a problem, can improving the thickness of the wall solve the problem?
Osmay explains:
We call it corrosion allowance. The wall can be over-specified to allow for some metal loss over the years due to corrosion.
Osmay Oharriz, Oil & Gas Industry Manager, Belzona 2021
Osmay goes on to clarify that there are two major problems with that.
- Adding more metal increases the weight of the vessels. Some companies fabricate their vessels at one location and later transport them to their final destination. Excessive weights can lead to costly transportation and erection.
- Corrosion allowance is estimated based on expected corrosion rates. Unfortunately, the variety of service conditions and units can generate corrosion rates greater than those expected once the vessel is in service. It is possible, and actually very recurrent, that a vessel loses its additional wall thickness way before expected.
Alternative solutions for corrosion control
Corrosion control methods should be considered during the designing phase. There are several alternatives that exist today. Metallurgy upgrade, cathodic protection, and coatings are the mostly known today.
Metallurgy update implies using corrosion-resistant alloys: stainless steel, nickel, several clads etc. This is a costly method. The designers can combine carbon steel for most sections of the vessel and upgraded metallurgy for those critical areas more prone to corrosion. But this introduces another problem. The use of different materials with different characteristics can lead to bimetallic corrosion, if not properly designed.
Cathodic protection, on the other hand, reduces corrosion by making a surface less prone to oxidation. It can be complex and expensive.
And finally, lining is another alternative. It implies using a coating to isolate the surface of the vessel from the chemical service. Lining can definitely protect the vessel. But it can also fail prematurely, if the coating is not fit for service or/and not applied correctly.
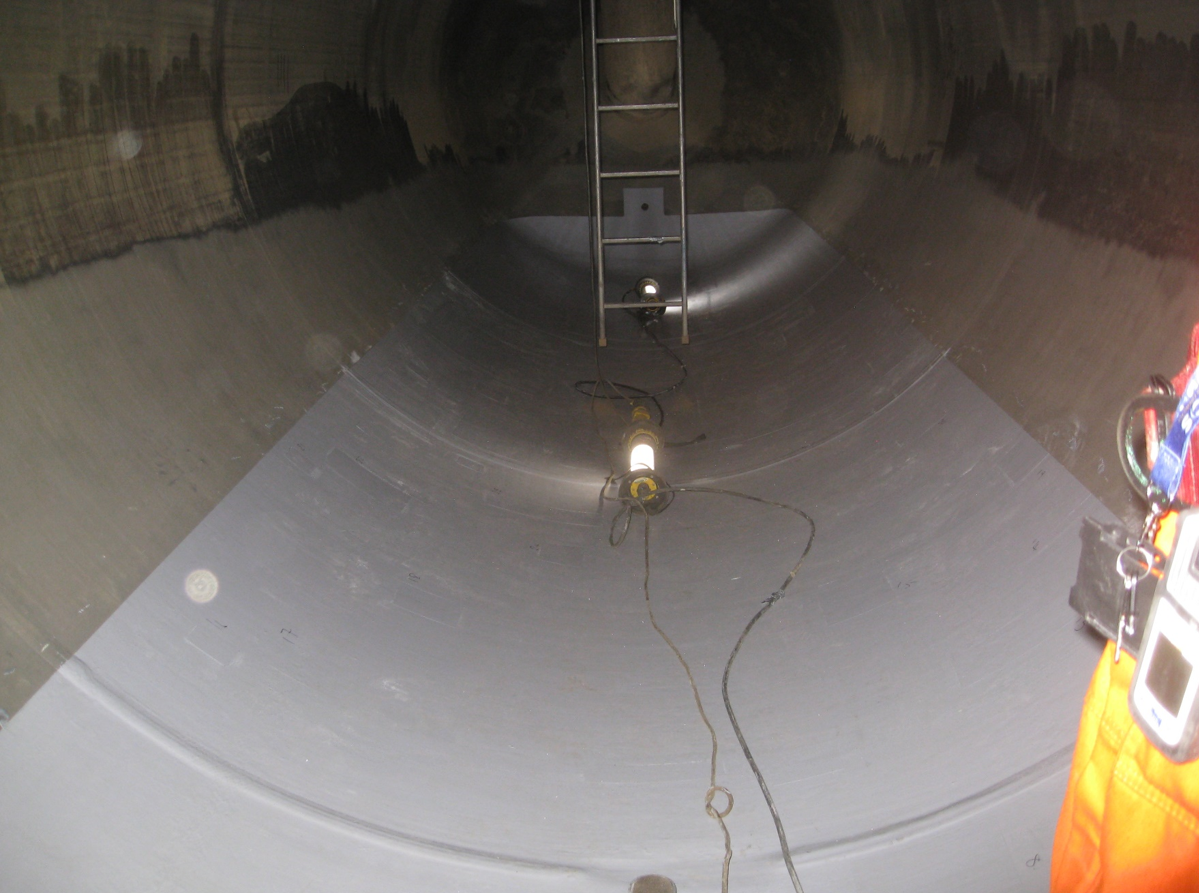
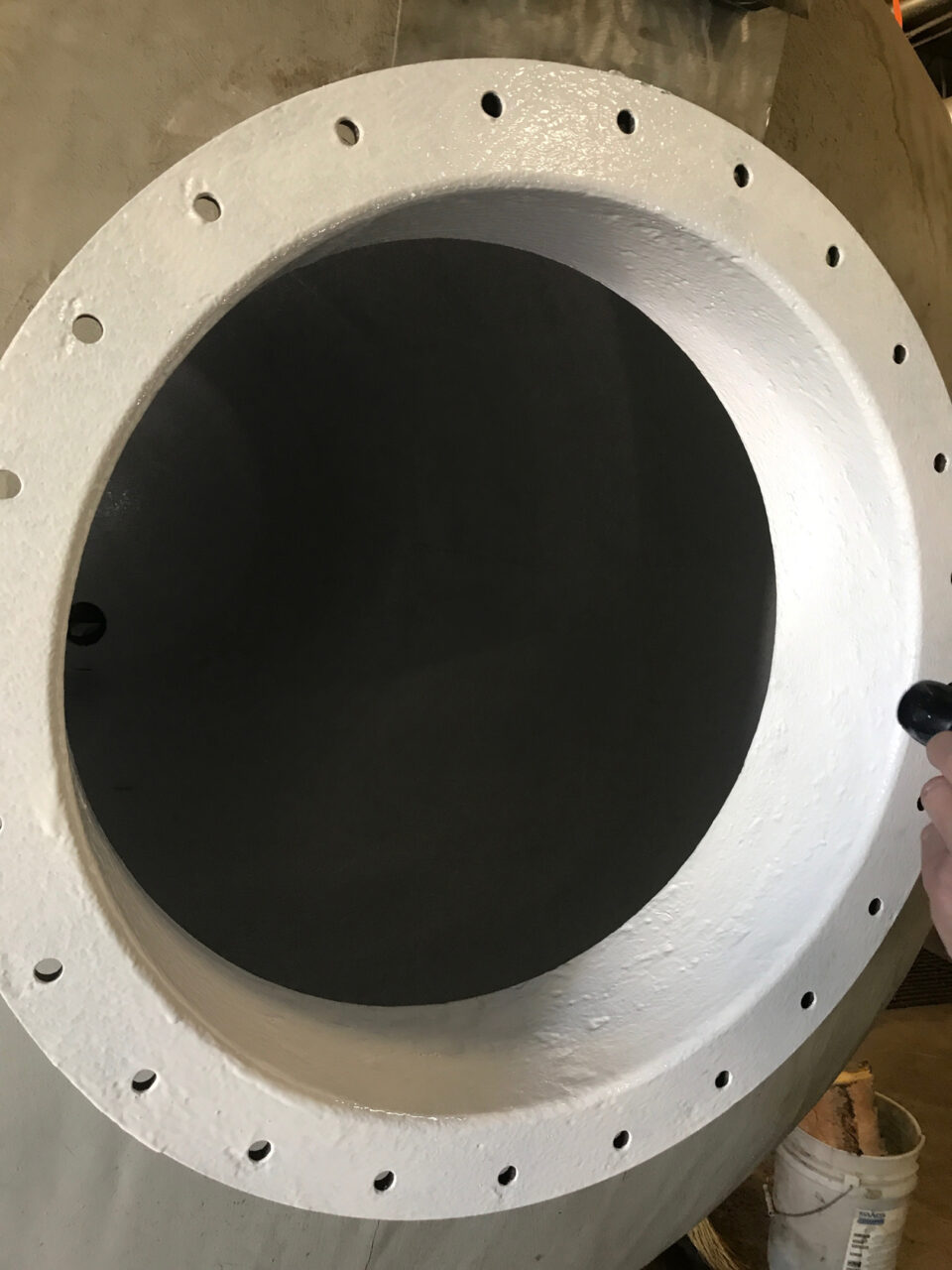
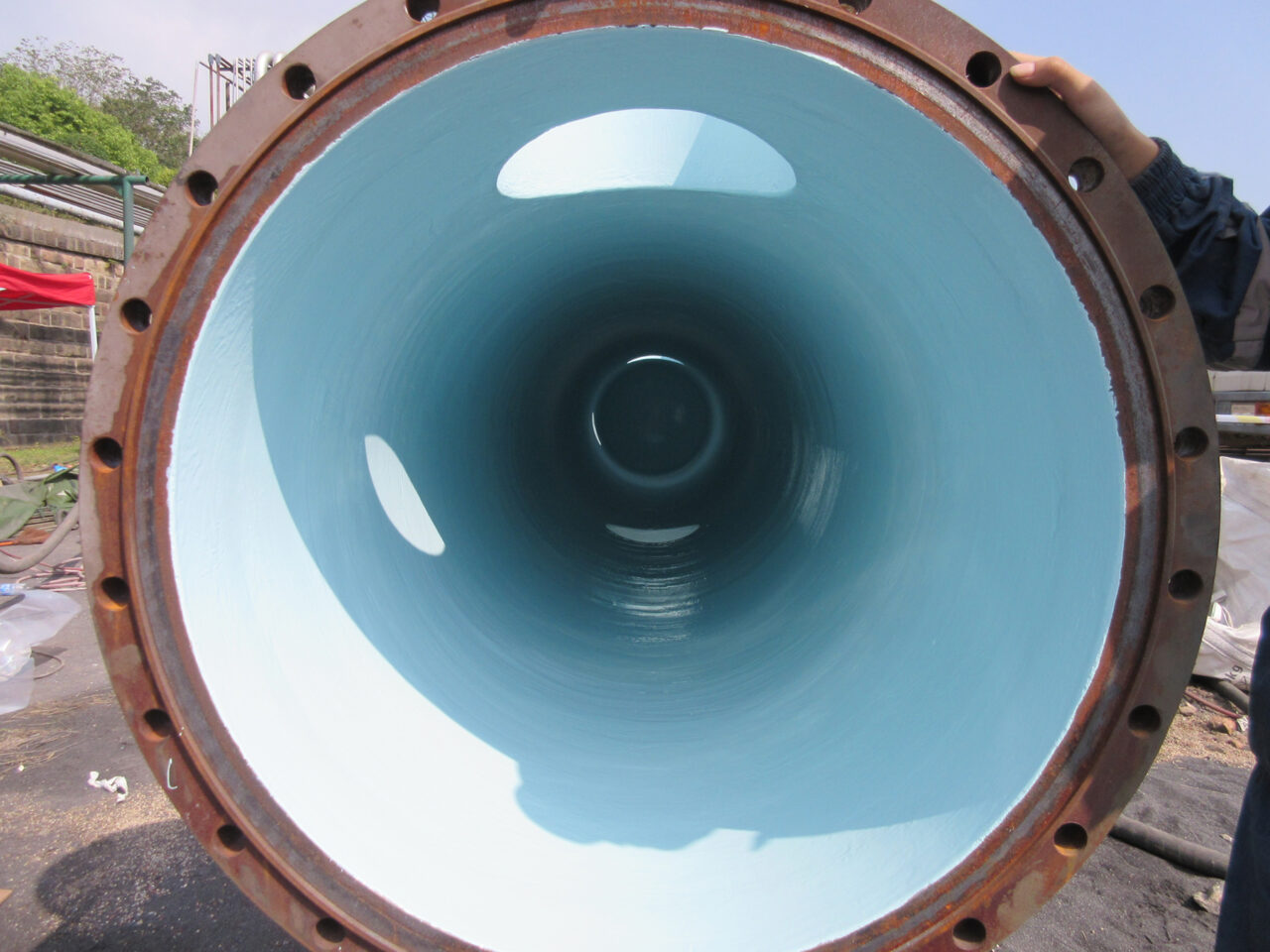
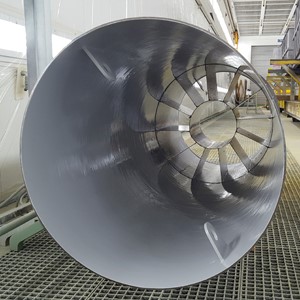
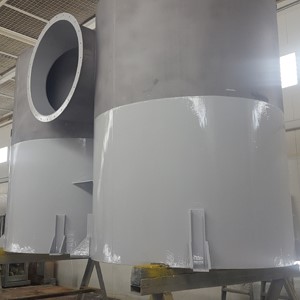
Belzona high-temperature coatings
Belzona provides low & high temperature linings for process vessels and storage tanks at various service conditions.
Osmay adds:
Many asset owners are embracing this option now rather than the other methods. But they may be skeptical at times, as there is penchant for rejecting coating as they can fail. It all comes down to choosing fit-for-service solutions and implementing them following our best practices.
Osmay Oharriz, Oil & Gas Industry, Belzona 2021
Many industrial sectors have developed material pre-qualification tests and set pass and fail values for lining materials. This qualification is obviously based on many years of experience and the recognition of both benefits and risks associated with lining materials. Over the years Belzona have produced testing protocols which align with those found in almost every client’s vessel lining testing requirements. These include adhesion, immersion and permeation resistance, steam-out resistance, explosive decompression, and chemical resistance among others.
Benefits of high-temperature coatings
Steam-out resistance and permeation testing are ones of the most important testing parameters for asset owners.
Maintenance crews typically thoroughly clean the vessels prior to opening for maintenance and inspection. They may use chemicals or a steam-out process. Steam-out is a purging process that employs pressurized steam at temperature levels traditionally close or above 390 °F (200 °C) for as long as 24 hours. Belzona have tested their high-temperature coatings to 410°F (210˚C) for 96 hours with no detrimental effect. This demonstrates the capability of our linings to resist short-term excursions to temperatures above those normally recommended for service under immersion. Definitely, most asset owners are interested in this test.
Permeation testing is very important as it assesses the ability of a lining to act as a barrier between the chemical and the substrate. We test our high-temperature coatings in Atlas cells and sometimes, combine testing with electrochemical impedance spectroscopy, which uses electricity conduction as an indirect measurement of permeation. Evidently, the more water-permeated a lining is, the lower resistance to flow of electrical current through it. This technique is fast becoming an accepted industry measure of lining performance. By combining it with Atlas cell immersion testing for 6 months, it can be demonstrated whether the specific lining can provide protection or not.
Training is the cornerstone of application success
Even if you have the best lining in the world, but if it is not applied correctly, it will fail. Training contractors in the implementation of lining solutions following best practices is paramount. We have several training schools available at several Belzona offices in the world. Training has value to all parties involved in a process. In fact, some asset owners mandate that contractors need to be trained and deemed competent in the application of high-temperature coatings.
Click the buttons below to listen to the full episode of The Belzona Podcast , and find out more about hight-temperature coatings and their benefits.
Subscribe and listen to the full episode on your favorite platform
Yulia Burova, Marketing Director, Belzona Inc., Miami FL, USA