The network of pipelines in the US is extensive. It has been reported that approximately 72 000 miles of midstream pipelines transport crude oil to refineries. Typically, these pipelines are strategically run underground over long distances with little disruption to surrounding communities. However, this safe and environmentally friendly way of transporting crude oil may generate problems given the corrosive environment that underground pipelines are exposed to.
Underground pipelines are typically fabricated of carbon steel because it is a cost-effective alloy with desirable mechanical properties. However, carbon steel’s main drawback in soil environments is its limited corrosion resistance. According to data collected by the American Petroleum Institute (API) pipeline performance tracking system (PPTS) over the past 14 years, corrosion has caused 24% of all incidents in buried hazardous liquid pipelines.
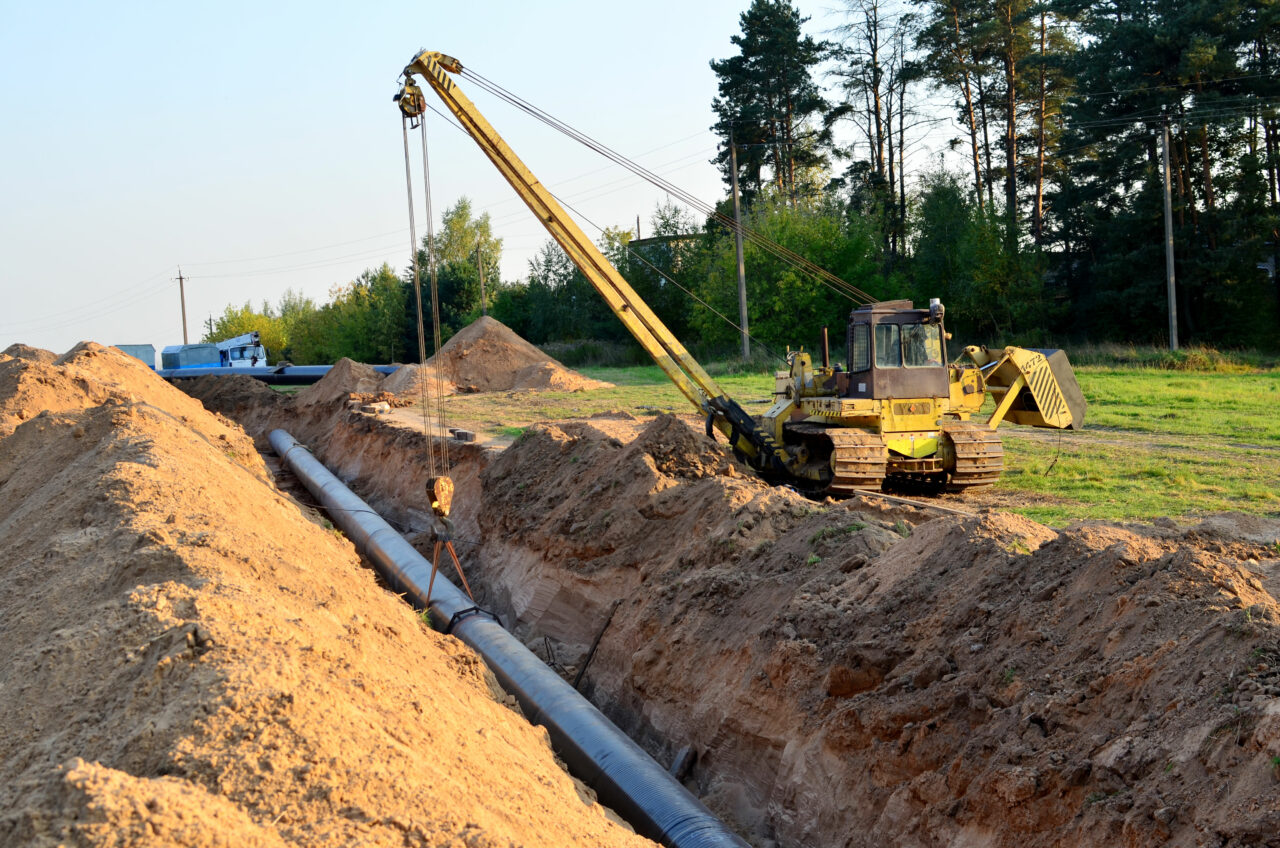
Soil Corrosion
Soil composition differs geographically, but is essentially an aggregate of minerals, organic matter, water and gases. These basic soil constituents account for its properties, including corrosivity. The variation in soil corrosivity throughout the pipeline trajectory can lead to differential cell corrosion, a major contributor to external corrosion of buried pipelines.
Some of the driving forces of soil corrosivity include oxygen levels, electrolyte concentration, moisture content and microbial populations, among others. Water, in combination with different ionic species present in the soil, can lead to the formation of strong electrolytic aqueous solutions, which reduce the soil resistivity and accelerate the rate of corrosion. The water holding capacity of the soil is strongly dependent upon its texture and particle size. Soils containing coarse sand of relatively high diameter particles for instance, have a more limited water storage capacity than soils with a high proportion of finer particles, such as fine sand or clay. As finer particles tend to be more saturated with water than coarse sand, pipelines surrounded by finer particles will typically be exposed to a more water saturated environment.
Due to the role of oxygen as an oxidizing agent, the degree of aeration is another parameter affecting the soil corrosivity. Although coarse sands are limited in their ability to store water, they are more effective in oxygen transport than finer particles. This increases the degree of aeration, resulting in a more rapid rate of corrosion. Excavations for inspections or repairs will also surge oxygen levels. As the pipeline travels through soils of different oxygen concentrations, the formation of differential aeration cells is nearly inevitable. The areas of the pipeline exposed to oxygen deficient soils become anodic, whereas those in contact with highly aerated soils become cathodic.
The presence of microbial populations in the soil can influence corrosion and further deterioration of underground midstream pipelines. This type of corrosion, widely referred to as microbiological influenced corrosion (MIC), is related to the activity of various micro-organisms in the soil. Soils can shelter many different types of bacteria, which can adapt to a variety of pH levels, oxygen concentrations and temperatures. Bacteria can influence the corrosion process by forming biofilms on the surface of the pipeline and creating differential concentration cells. Inside the biofilm, aerobic bacteria exhaust oxygen and the acid-producing bacteria reduce pH levels. This microbial activity creates anodes and results in localized corrosion resembling pitting. Some of these bacteria, sulfate reducing bacteria (SRB) to cite one specific group, can reduce sulfate ions into sulfides and increase the chance of stress corrosion cracking.
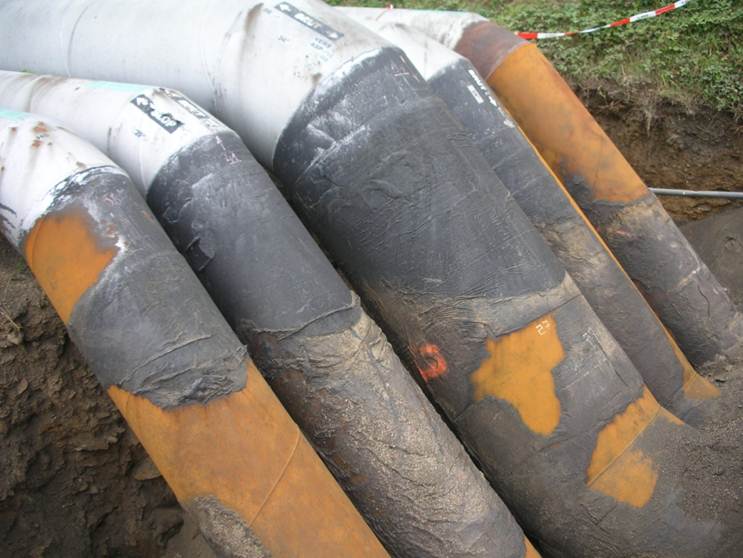
External corrosion affects all buried pipelines and must be combated through the implementation of an effective coating barrier together with CP systems. Coatings provide a barrier between the corrosive soil environment and the pipeline, isolating the substrate in the process. CP, on the other hand, makes the pipeline cathodic by applying direct current electricity to it.
Osmay Oharriz, Belzona Oil and Gas Industry Manager
There is a great variety of coatings currently used to protect buried carbon steel pipelines, each with their own benefits and limitations. Some of the drawbacks seen with coatings are related to limited temperature range, poor shear and compressive stress resistance, cathodic disbondment and application limitations, among others.
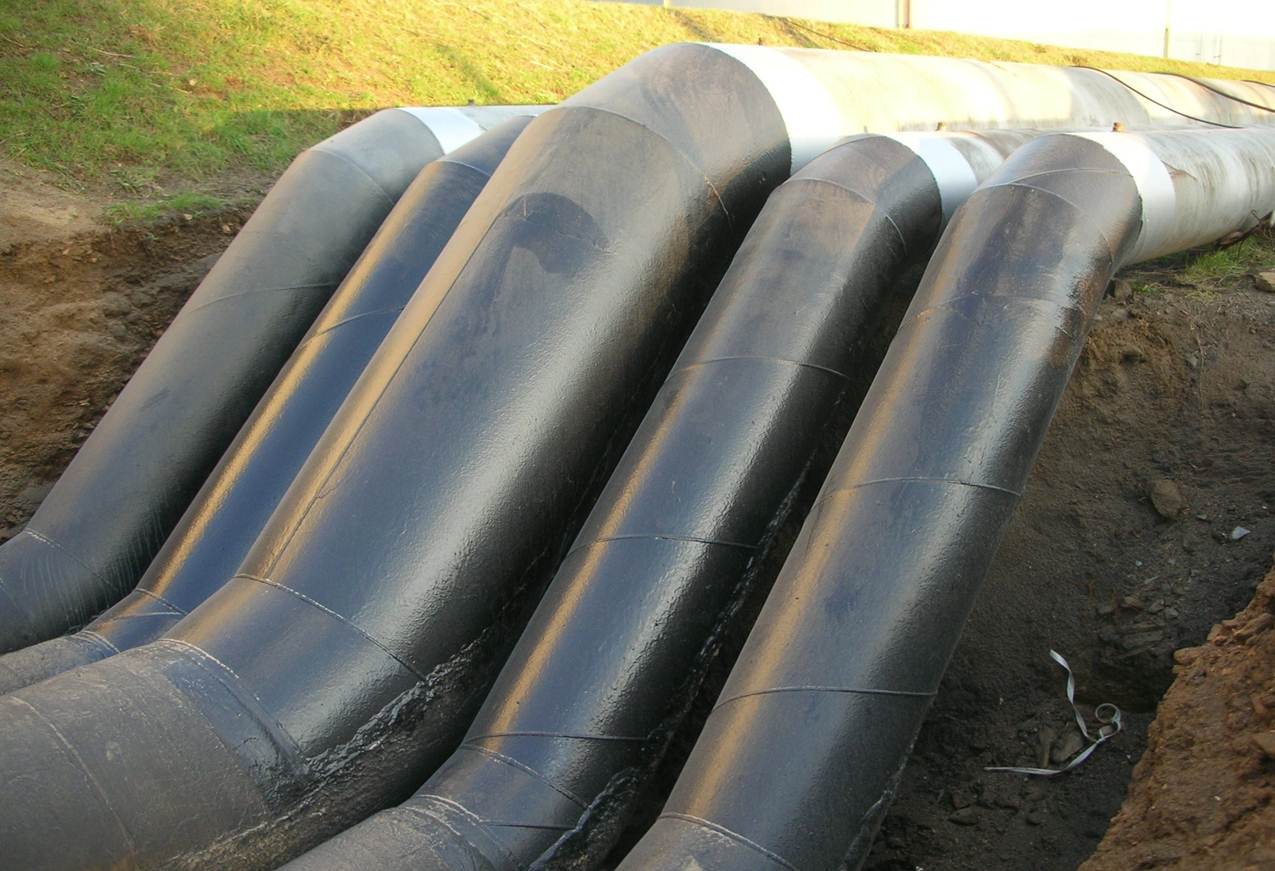
Material Testing
Coating resistance to immersion in liquids
As underground pipelines are exposed to water and dissolved salts, the chosen coating must be able to withstand continuous exposure to aqueous salt solutions. ISO 2812-2 specifies a method for determining the effects of full or partial water immersion on the coating. It involves immersing coated carbon steel panels in a seawater bath at 40˚C (104˚F) for six months. Upon test completion, a visual inspection for cracks, blisters or delamination determines whether the coating passes or fails.
Heat immersion resistance
It has been reported that the exterior of some pipelines can reach temperatures above 50˚C (120˚F). This is especially true in summer months when ambient air and soil temperature levels are the highest. Therefore, the coating must be able to endure elevated temperatures without exhibiting any significant signs of deterioration.
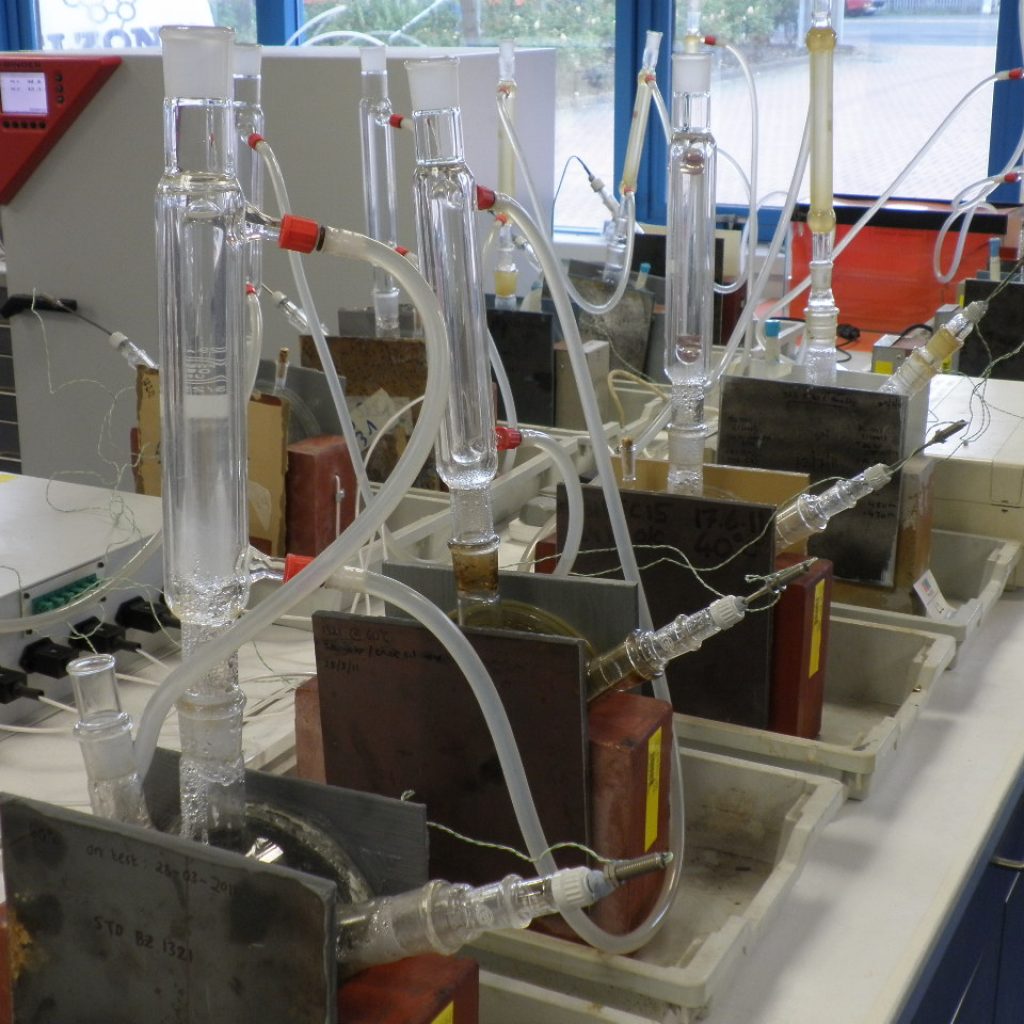
The heat resistance and permeability of a coating can be determined via Atlas cell testing in accordance with NACE TM0174. This technique is used to obtain the maximum temperature at which the coating can offer a suitable barrier of protection under immersed conditions.
The test involves immersing a coated panel in a chemical solution of nature and temperature comparable to the anticipated service environment.
Deionized water is typically used as a test solution since it provides the largest possible concentration gradient, promoting the permeation of water through the coating. The test is run for six months. The coatings are inspected after the first, third and sixth months of testing. The test is deemed a pass if no cracks, blisters or rusting are detected.
Electrochemical impedance spectroscopy (EIS) is a method of testing the impedance or resistance to the flow of electric current through the coating in agreement with ISO 16773-2. This technique can be used in conjunction with Atlas cell testing. Any water able to permeate the coating would decrease the coating’s impedance. By comparing values before and after Atlas cell testing, quantitative measurements of water permeation can be determined.
Compressive resistance
Underground pipelines are exposed to significant compressive stresses associated with the load exerted by the weight of the soil, pipeline and pipeline contents. Testing in accordance with ASTM D695 indicates a coating’s ability to resist failure when axially stressed under compression. This process consists of using a 25 kN (5620 lb-f) tensometer to exert a load onto a cast sample until failure is observed.
Shear stress resistance
Changes in temperature and pressure due to varying operating conditions result in expansions and contractions of the carbon steel pipeline. The relative movement between the pipeline and soil will subject the coating to shear stresses. If the lap shear adhesion of the coating cannot overcome the shear stresses exerted by the pipeline, disbondment can occur.
Testing via ASTM D1002 can be employed in order to determine the adhesive strength of a material. In this method, the adhesive material is bonded between two rigid metallic substrates. Once the adhesive material is fully cured, a 25 kN (5620 lb-f) tensometer applies tensile loading to both plates in opposite directions until there is a bond failure.
Flexibility and crack resistance
Coatings applied onto underground pipelines can elongate when the substrate becomes bent or deformed due to unexpected loads. This is the reason why pipeline coatings are commonly tested for their ability to resist cracking when the substrate is placed under stresses. ASTM D522 is a test method that employs cylindrical mandrels for such a purpose. A coated panel is placed onto cylindrical mandrels of various diameters with the uncoated side of the panel in contact with the mandrel. Then, the panel is bent 180˚ at a fixed velocity and immediately inspected for signs of cracking, delamination or any other failure modes.
Cathodic disbondment resilience
As mentioned earlier, CP can be concurrently used with a coating system. Holidays or discontinuities can form in the coating and expose the pipe to the soil environment. Applied CP can cause further loosening of the coating and creep corrosion. ASTM G8 provides a test method for simulating this scenario. A coated specimen is intentionally perforated to produce a fixed size defect or holiday. The sample is then exposed to an electrolyte and electrically stresses at ambient or elevated temperatures (ASTM G42). Testing takes place for a period of 30 days. Following the exposure, the sample is visually examined for any evidence of unintentional holidays and loosening of coating at the edge of the intentional holiday, as well as any other signs of deterioration such as blisters, cracking or crazing. The lesser the loosening of the intentional holiday, the more resistant the coating is to cathodic disbondment.
To be a feasible solution for external corrosion of underground pipelines, a coating must manifest excellent results in the testing mentioned above. The coating should also be environmentally friendly, economical and have a straightforward and practical application procedure.
Case Study
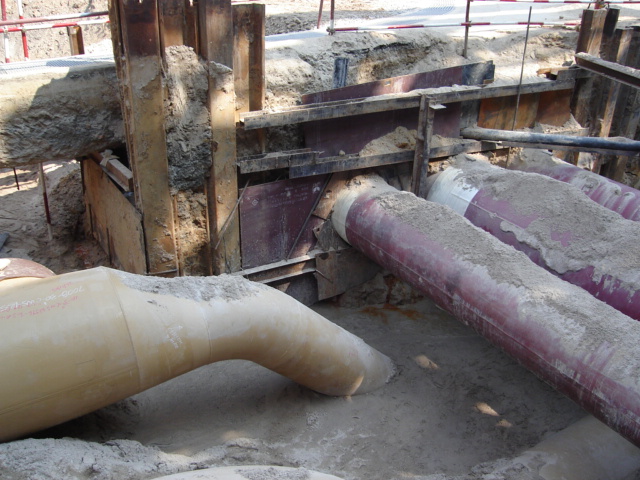
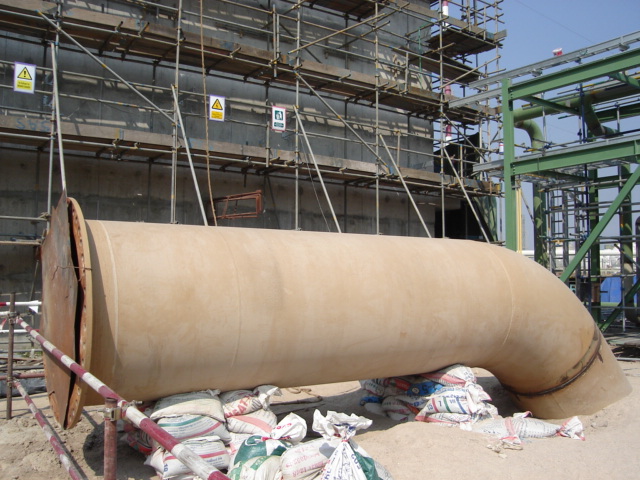
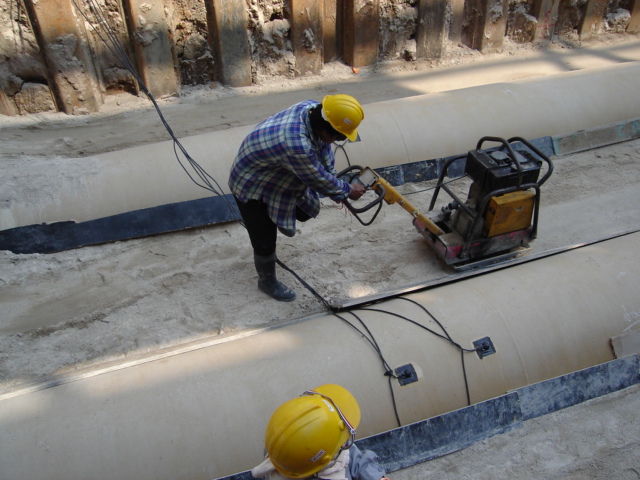
A chemical company in Thailand decides to protect the external surface of an underground pipeline. The pipeline was previously coated with a polyethylene coating and was suffering from severe external corrosion. Highly salty underground water affected the pipeline and accelerated the deterioration and disbondment of the previous coating in certain areas. The asset owner planned to implement an alternative coating solution. The customer assessed all of the testing data and selected Belzona 5811 to coat the pipeline.
The pipeline was abrasive blasted to the cleanliness requirements of SSPC-SP 10 (near white metal) prior to the application of the protective coating system. The substrate profile was measured by Testex tape in accordance with NACE SP0287 to ensure a 75 μm (3 mil) average profile. The surface was cleaned and degreased utilizing appropriate cleaning and degreasing chemicals in accordance with the requirements stated in SSPC-SP10. The application crew used a single component Hasco sprayer to apply Belzona 5811. The system was applied in two coats of contrasting colors and achieved a minimum dry film thickness of 400 μm (16 mil).
The coating was allowed to cure in accordance with Belzona’s Instructions for Use (IFU). Once the epoxy material was cured, the pipeline system was transported to the application site and buried in fine sand together with CP.
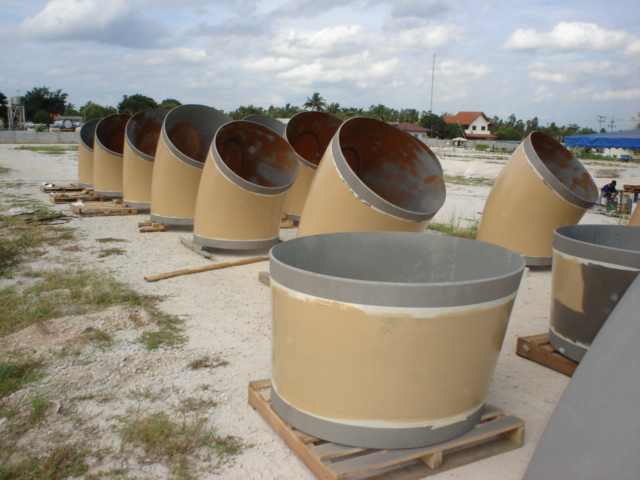
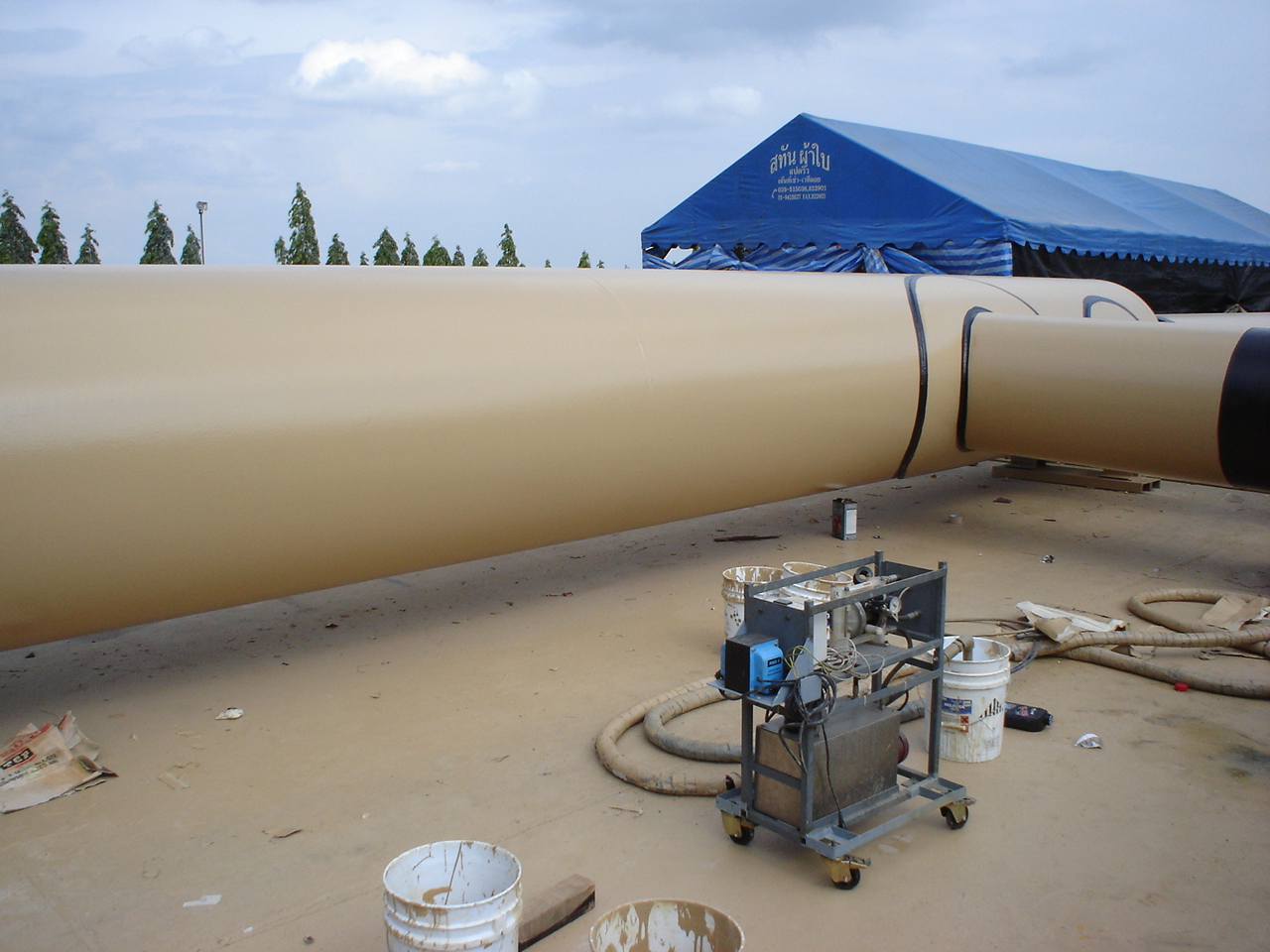
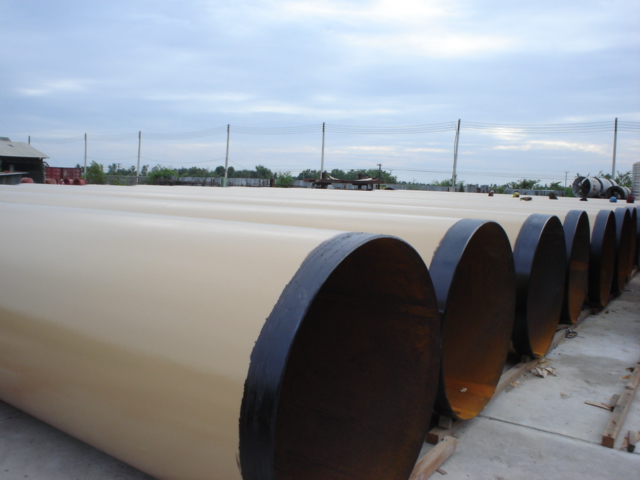
For more information about epoxy based solutions for pipes and pipelines, visit www.belzona.com.
Interested in purchasing Belzona’s repair composites and protective coatings?
Yulia Burova, Marketing Director, Belzona Inc., Miami FL, USA