This technical article was written by Ian Wade, Senior Technical Services Manager, Belzona.
An edited version of this article was published on the Hydrocarbon Processing website.
Strengthening the Bond with Reliable Structural Adhesives
Abstract
When identifying solutions that can offer assurance and longevity, the maintenance and reliability of assets repairs can be challenging, this white paper will look into the use of structural adhesives as the first-choice solution.
Structural adhesives can be used for affixing metal substrates or components as they provide high modulus and high strength. However, they are not currently internationally recognised like the traditional methods even though adhesives are already used in a wide range of industries, such as aerospace, rail, and construction.
Traditional practice such as welding, riveting, nuts and bolts and mechanical fixing are perceived as the go to method. However, they all have their inherent inadequacies. Welding can be hazardous to health, riveting, nuts and bolts concentrate the stress locally while mechanical fasteners can concentrate stress.
This paper introduces a novel, two-component, solvent-free toughened epoxy adhesive material that provides high adhesion to metallic substrates while also being able to withstand high movement or cyclic fatigue in comparison to general epoxy materials.
As well as potential application areas, the article also discusses a number of benefits, including ease of use, load bearing and impact resistance properties.
Introduction
Most industrial maintenance or repair procedures can either involve welding or use of mechanical fasteners as these can be perceived as easy and quicker, however, these procedures might initially seem to correct the issue but may cause more harm than good. Depending on the repair situation for instance welding or drilling to connect mechanical fasteners on a storage tank containing flammable liquid is not recommended for obvious reasons this is where a structural adhesive can really offer a solution for that maintenance repair.
There are many structural fixings used across a whole range of industries that may be part of any maintenance or repair these include support brackets such as cable trays, antennas, heating coils filter pans or any other internal fixtures in vessels that suffer from corrosion, impact or vibration damage. Within construction there are fire water deluge systems, nozzles connections, facades panels and signs which can require maintenance overtime or adverse weather conditions.
Process equipment or piping can suffer from thinning or the steel or even through wall defects which will need either monitoring or repairing depending on whether the integrity of the equipment has been lost.
Structural fittings are generally for fixing of static members but may be subjected to forces unbeknown at time of installation this could include thermal cycling of the joints, cyclic loading or vibration due to fatigue of a component.
If there are repairs due to the above, the contractor may be in a situation where a choice of solution can be made, then the strengths and weaknesses need identifying.
Welding is regularly used for repairs as it is widely available while being well regulated with high customer confidence and high strength of the repair it does come with its inherent risks both the use, the material by heat stressing and the user as welding can cause both acute and chronic health risks [1]. Application of welding repairs onto live piping sections, storage tanks or process systems and equipment should not be undertaken due to the high temperatures involved and not forgetting the combustible nature of the process fluid or gas running through or being stored in these components.
Bolted joints are seen as simple and low cost due to the ease of disassembly and reassembly and these can be dissimilar metals, but the use of dissimilar metals will contribute to galvanic corrosion, add weight to the joint, requiring routine inspection and tensioning while the drilled holes in the support material, stress distribution is not uniform and concentrated at the holes.
Structural adhesives have high bond strength whilst being lightweight, adhesive applied to cover the entire joint, resulting in uniform stress distribution, reducing metal distortion under strain.
Importance of a strong bond
Adhesive bonding is the joining of similar or dissimilar members together while creating permanent high strength bonds which can transfer structural stress without loss of structural integrity.
Regardless of the joint type used, it is important to understand the different stresses that are imparted onto a bonded assembly. Adhesives perform the best when the stress is two-dimensional to the adhesive, allowing the force to be applied over the entire bond area.
Joints that are well designed for adhesives place most of the stress into compression or shear modes, adhesives perform the worst when stress is one-dimensional to the adhesive, concentrating the load onto the leading edge of the bond line. Joints placing stress into cleavage or peel concentrate the stress onto the leading edge, which may lead to premature bond failures, especially if subjected to vibration, impact or fatigue
Bonds of high strength are obtained after cleaning of the substrate by removal of any contaminants followed by the roughening of the substrate generally in the form of grit blasting to international recognised standards [2], this is why surface preparation is critical to success regardless of what type of adhesive is used.
There are three types of bonding that are important to achieve to ensure good adhesion. These are adhesive, chemical, and Mechanical.
Adhesive relies on surface energy to generate adhesion to the substrate. While chemical relies on chemical bond formation and electronic bonding to produce adhesion. Mechanical adhesion is due to the creation of an irregular profile that allows a deeper profile to be produced.
The types of structural adhesives available have been summarised in Table 1
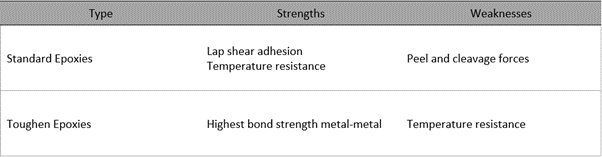
There are two types of failure mechanisms associated with structural adhesives:
1. Cohesive failure occurs in the bulk layer of the adhesive material. This failure mode is limited by the strength of the adhesive material and can be caused by insufficient curing of the adhesive and applications at a greater thickness than that recommended among others.
2. Adhesive failure occurs when the mechanical adhesion between the adhesive and the parts being joined is overcome by the loading. This failure mode is associated with inadequate surface preparation, presence of contaminants, or insufficient curing of the adhesive among others.
Background
Design considerations for Belzona 7311 were based on both technical target requirements and a practicality approach, as summarised in Table 2.
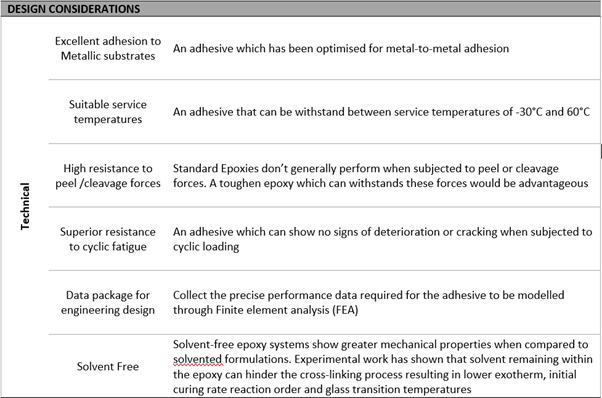
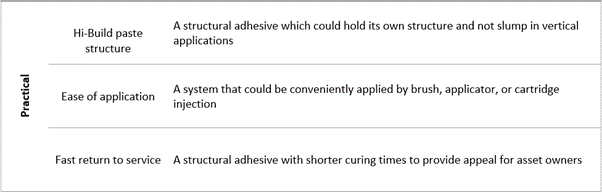
Belzona 7311 was subjected to at least the following tests and evaluation protocols in to ensure that it met the design criteria previously discussed. Where possible, internationally recognised standards were used.
- Cleavage Adhesion – ASTM D1062 [3]
- Tensile Shear Adhesion – ASTM – D1002 [4]
- Tensile Fatigue Resistance – ISO 9664 [5]
- Impact Resistance – ASTM D256 [6]
Bibliography
1. https://www.hse.gov.uk/welding/health-risks-welding.htm
2. ISO 17212:2012 Structural adhesives — Guidelines for the surface preparation of metals and plastics prior to adhesive bonding
3. 3. ASTM D1062-08(2015) Standard Test Method for Cleavage Strength of Metal-to-Metal Adhesive Bonds
4. ASTM D1002-10(2019) Standard Test Method for Apparent Shear Strength of Single-Lap-Joint Adhesively Bonded Metal Specimens by Tension Loading (Metal-to-Metal)
5. ISO 9664:1993
6. Adhesives — Test methods for fatigue properties of structural adhesives in tensile shear
7. ASTM D256-10(2018) Standard Test Methods for Determining the Izod Pendulum Impact Resistance of Plastics
Click on the following link to read PART TWO of the technical article.
Interested in Purchasing the Epoxy Structural Adhesive, Belzona 7311?
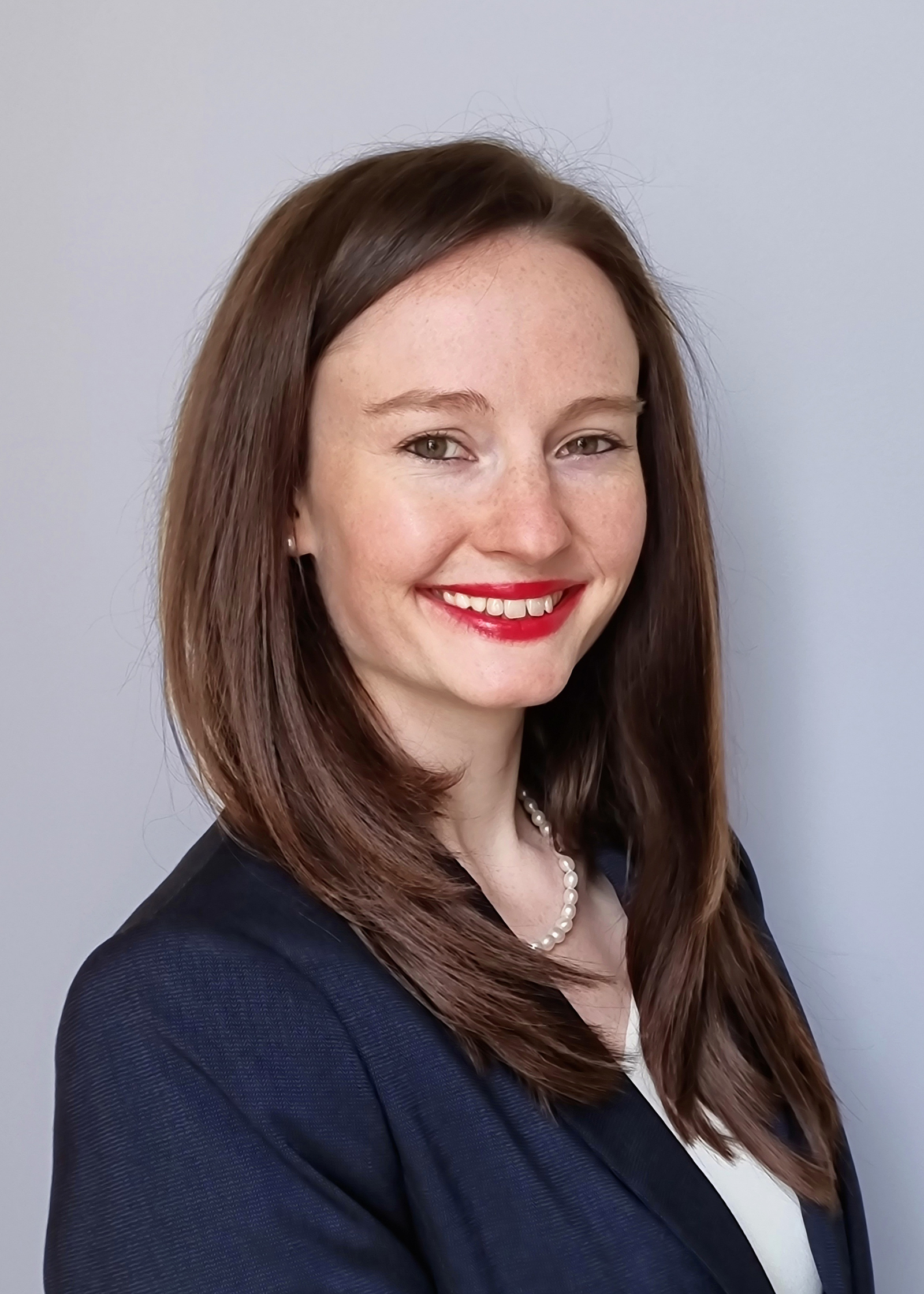
Chloe Hirst is the Senior Copywriter at Belzona Limited and is based in Harrogate, England. She gained a Bachelor’s Degree (with Hons.) in Media and Communications (specialising in Journalism) at Goldsmiths College, University of London. Chloe regularly writes case studies and thought leadership content featuring a variety of different industries, with a special focus on the renewables sector. In both 2023 and 2024, she won the Best Manufacturing Content Creation Specialist (UK) Award as part of Acquisition International’s Influential Businesswoman Awards.