Where are the Problems in a Warehouse?
Right now, thousands of packages are being delivered to homes globally. These thousands of packages add up to the nearly 500 million the largest online retailer and distribution company delivers yearly in addition to the packages other logistic services deliver. This boom is due to the expansion of e-commerce, the exchange of goods and services through an electronic network or online platform. Over recent years, consumers have been purchasing more frequently en masse from online retailers, and it has led to an increase in the need for warehouses to keep up with the proximity and demand of consumers.
A warehouse is a distribution center of at least 200,000 square feet. Currently, there are around 11,000 warehouses in North America which equate to 4.7 billion square feet of industrial space. Yet, there is a space shortage in logistics real estate. 96% of all industrial space is currently leased in the United States, and preleasing rates have skyrocketed, meaning warehouses are being leased even before construction is finished. The scarcity has led to companies fighting over warehouses for rent and for sale.
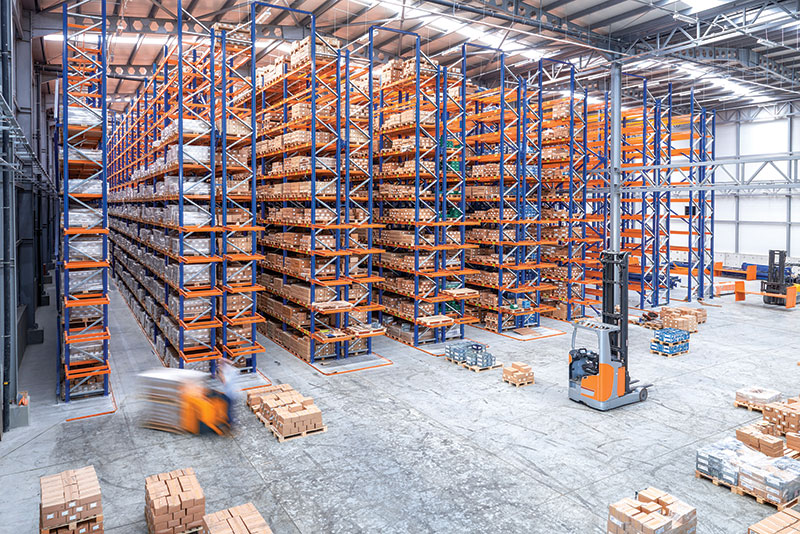
Modern warehouses take three times as much space as brick-and-mortar establishments to fit the amount of stored merchandise and in combination with the fact that warehouses are being leased at an increased rate, is creating an environment where land is becoming scarce to warehouse developers. It is estimated that 1 billion square feet of new industrial space will be constructed, including 100 million square feet of cold storage space by 2025 to satiate the real estate shortage.
The warehouses that we do have and those that are going to be built must be protected and maintained. The structures include loading docks, roofs, walls, floors, HVAC systems, refrigeration systems, conveyor belts, curbside appeal, etc. A warehouse cannot afford to have any of these assets or equipment fail or it will cause a period of downtime that will lead to operations backing up and package delays costing money, time, and unhappy customers.
Finding Solutions for Warehouses!
While there are repair methods that will take care of the common problems, many of them are costly, tedious, and require specialized tools and people to repair. For instance, welding is an optional repair method for metal. However, a specialized person is needed to operate the hot tools, creating a dangerous environment. These injuries are caused by gases and fumes, sparks, fires and explosions, optical and auditory injuries, and extreme heat conditions.
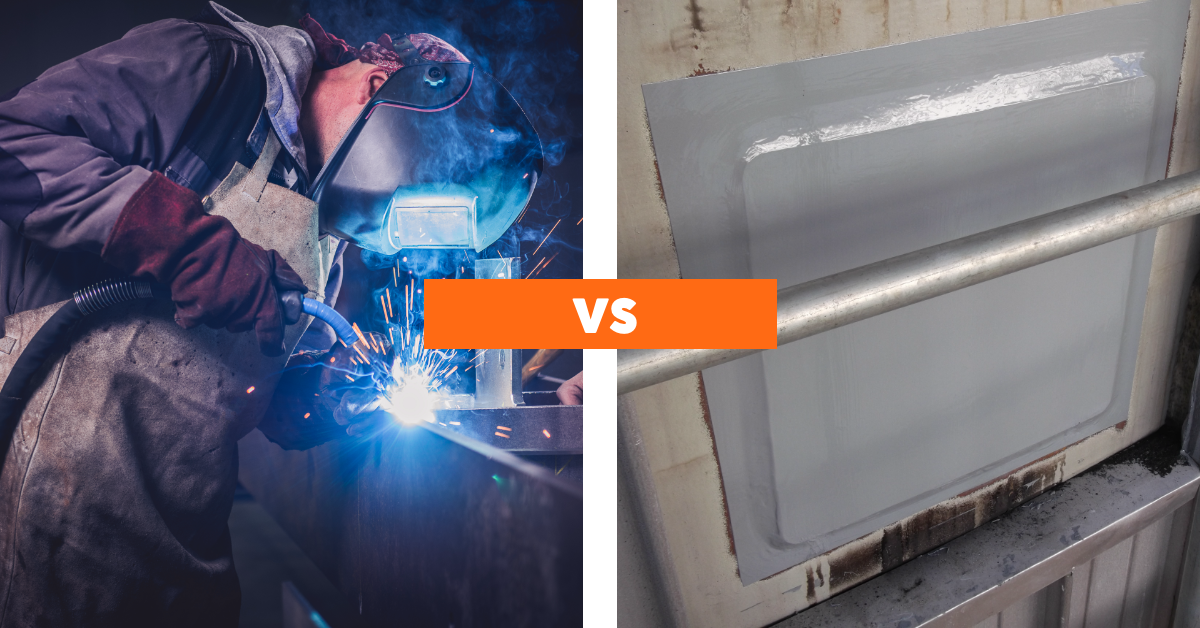
On the other hand, Belzona’s epoxy repair composite solutions can be used in place for a quicker and user-friendly application that is less expensive than a replacement or specialized repair. For example, a sump tank was leaking on the engine room floor of a frozen food warehouse, creating hazardous conditions. Corrosion and holes had developed on the weld seams of the tank. The warehouse had considered replacing the equipment. They priced out the cost of purchasing a new tank with the associated piping and labor. The estimated delivery time for the tank would take months. Additionally, the cost would make the replacement a capital budget item, which required corporate approval. The outcome did not seem possible since the frozen food warehouse operates 24/7, 365 days per year, with millions of dollars of inventory meaning the freezer’s building could not be shut down. The warehouse decided to choose Belzona 1111 (Super Metal) and Belzona 5811 (Immersion Grade) to repair the corrosion and holes and give the equipment proper maintenance rather than going through the hassle of replacing it. In the end, the Belzona repair was completed in 2 days.
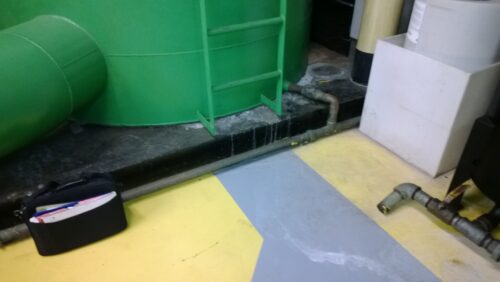
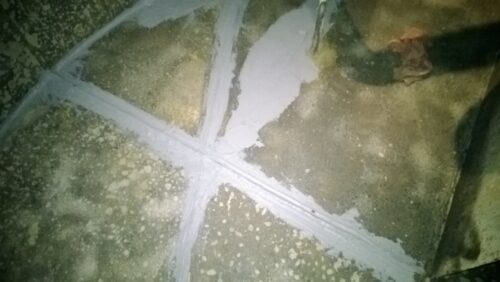
Keeping Warehouses Safe
With new warehouses popping up it means that they will also need to meet safety compliance. For instance, a facility identified a potential slip hazard on a metal staircase leading to a mezzanine floor area. They had to solve the issue quickly and Belzona was chosen for its anti-slip epoxy products. Belzona 4411 (Granogrip) gave a quick and easy solution to removing a slip hazard from a busy set of stairs. After preparing the area with an MBX Bristle Blaster, stripes of Belzona 4411 (Granogrip) red and yellow safety colors incorporating Belzona 9221 aggregate were applied. The non-slip properties of the Belzona Grip system are ideal for this dusty environment and safety colors aid in both identifying the step edges and in highlighting the potential hazard, all while complying with safety regulations.
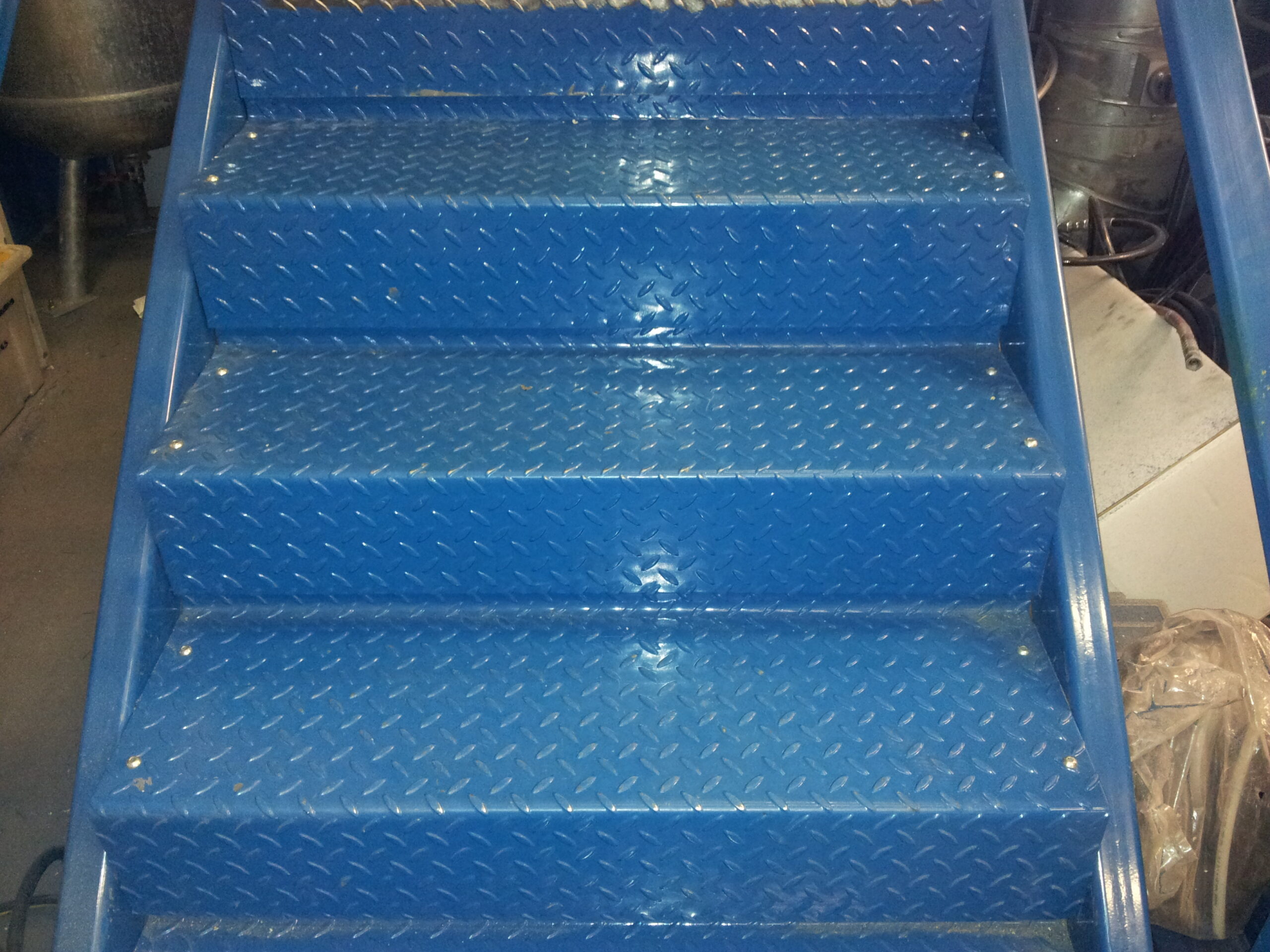
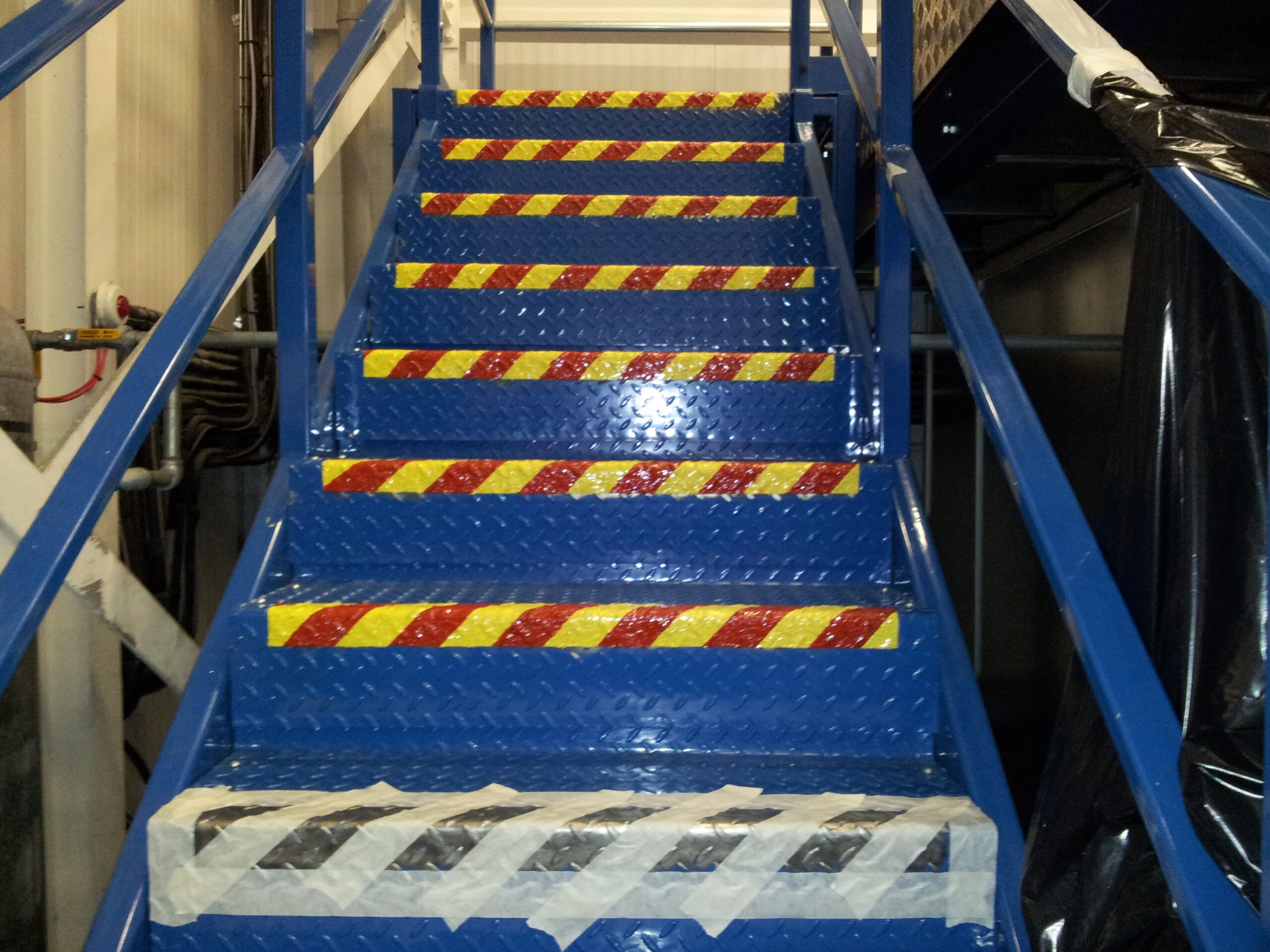
It is a critical time in the logistics and retailing industry to maintain the overworked and damaged equipment that they might encounter during their overwhelming production. Belzona can always step in to offer solutions where a full replacement is costly and time-consuming. Belzona products can slim down the shutdown time of a facility and ensure that damages are limited in the future. See what other industries Belzona can help with here.
Interested in purchasing Belzona’s repair composites and protective coatings?
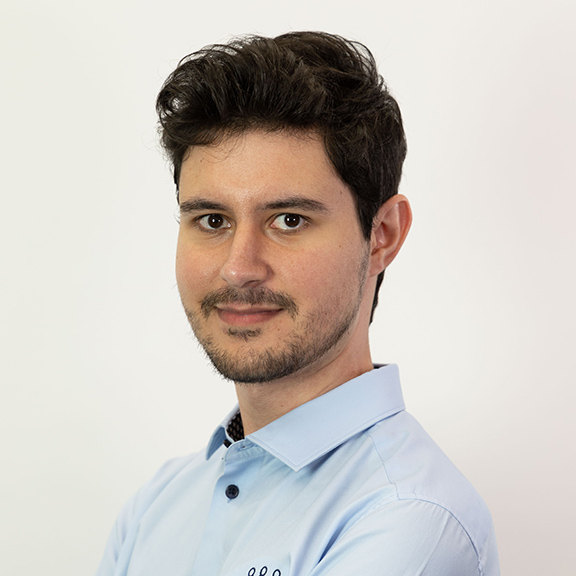
Digital Content Creator, Belzona Inc., Miami, Florida