In this podcast episode, along with our dynamic host, Richard Bywater, we explore with Dinis Castro, Quality Control Manager, and Isaac Atkinson, Technical Coordinator at Belzona, what are the internal and external quality control standards Belzona complies with, and the approval certificates that attest to them.
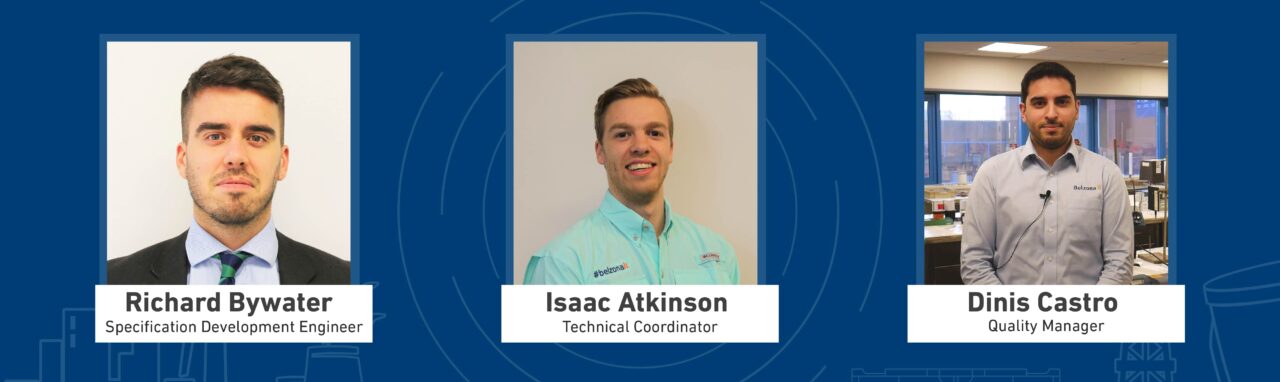
From Product Development to Quality Control
As a continuation from episode 3, where we had an insight into Belzona’s Research and Development Department, we now move from product development, through to the procedures and standards that are undertaken to ensure that consumer satisfaction is achieved, and high standards are met.
In this episode, Dinis explains a little more about the work that his team carries out internally as part of adhering to these standards.
“As Quality Manager, I oversee the quality control team in both in Laboratory and Factory who test the raw materials and finished products to ensure quality consistency. My team, along with our operations staff, capture and analyze issues that could be raised throughout several stages of the manufacturing process, looking for common factors and trends to avoid these recurring. Customer feedback is also a big part of the role, through from the investigation of complaints to maintaining the database where all this information is kept. Overall, the key part of the role is to ensure that the quality management system is up to date so we can work to improve areas or specific processes.”
Dinis Castro, Quality Manager, Belzona Polymerics, UK, Harrogate
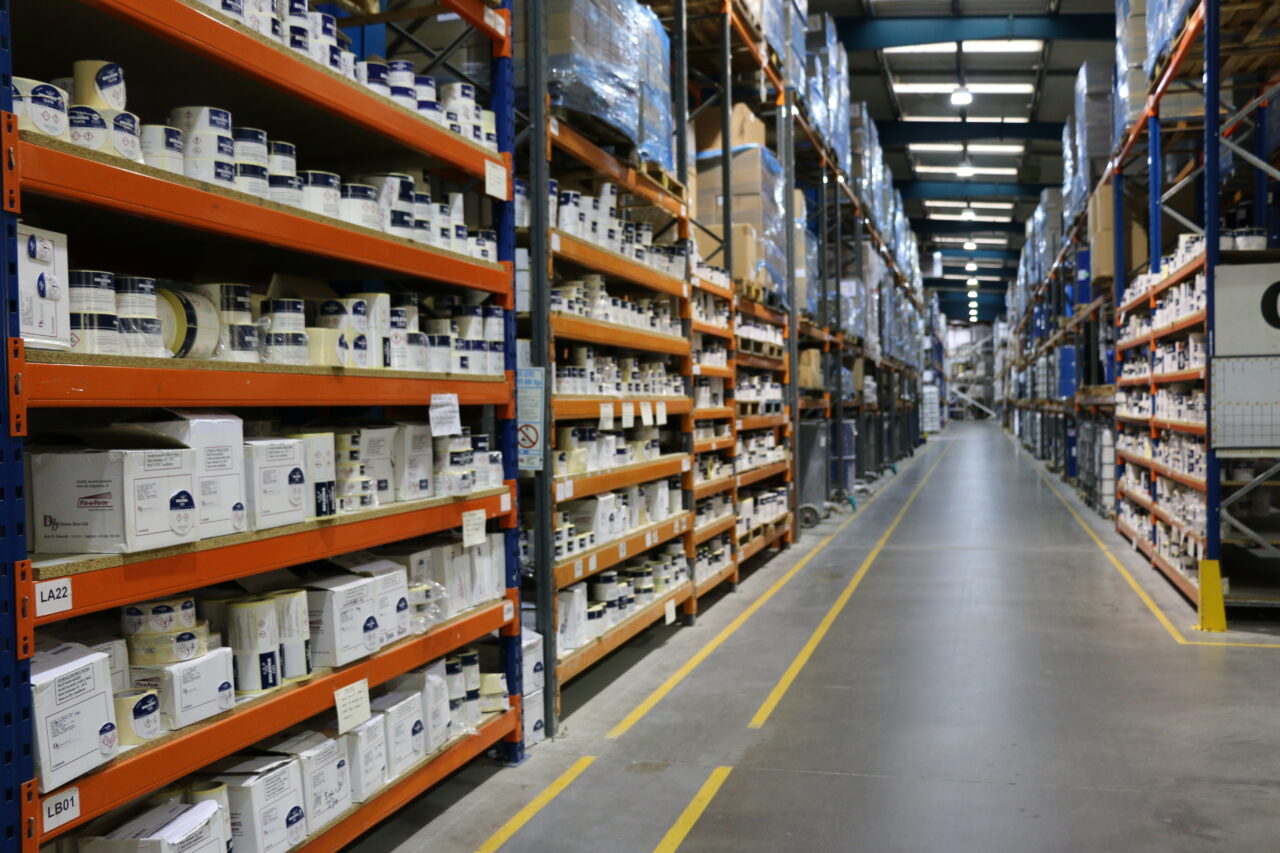
So why is it important to have these systems in place? Dinis goes on to explain the importance of being able to control outcomes, and how it defines consistency in the quality of products. It is essential to have these processes, and this is why we are certified by The British Standards Institution (BSI) against the standards ISO 9001 for quality and ISO 14001 for environmental. These standards provide us with a framework and guideline to help us continually improve.
Product Approvals Providing Assurance to Customers
On the external side, Isaac Atkinson, Belzona’s Technical Coordinator, coordinates the process of preparing new product developments for the field alongside our R&D, Technical, and Marketing Teams, as well as managing our existing product portfolio. Similar to Dinis’s role, Isaac ensures consistency in the quality of information we output. A key factor as part of this process is gathering feedback from the field, which is then fed back into the product development stage and so the cycle begins again.
“At Belzona, we don’t just provide the product, we provide a solution, so, although we supply the product initially, we are also there to provide any technical support throughout an application, and even post-application. So, because of that, we need quality products to ensure we provide a long-term solution”.
Isaac Atkinson, Technical Coordinator, Belzona Polymerics, UK, Harrogate
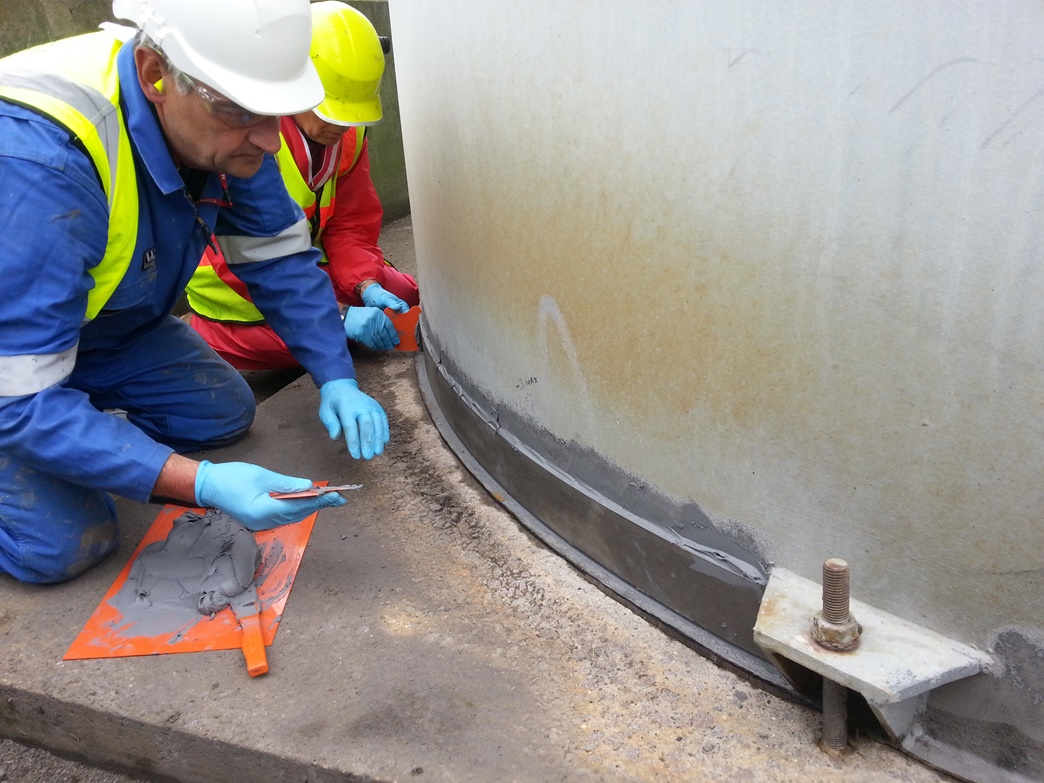
In addition, Isaac also coordinates Belzona’s product approvals, which provide assurance to the end-user that we have standards in place. Belzona has obtained a range of product approvals across various different industries. For example, Belzona holds marine approvals from DNV, ABS, and BV classification societies. Additionally, specific approvals are gained for different regions such as NSF or WRAS potable water approvals for the U.S and UK markets. These approvals need to be maintained and part of Isaac’s role is to ensure that these are renewed which is done through audits.
Importance of Auditing- Internally and Externally
The purpose of an audit is to determine if the procedures and controls that are in place are efficient, valid to the business needs, and conform to the standards. Through both audit feedback and constructive criticism, this then gives us the opportunity to further improve our quality management system.
“It’s absolutely vital that Belzona meets and exceeds the expectations of the customers. Feedback from the customer is the best way we can measure our success.”
Dinis Castro, Quality Manager, Belzona Polymerics, UK, Harrogate
It’s clear from this podcast, that quality control standards are something that needs to be rooted in all processes and procedures. It not only ensures that we conform to our quality processes, but it also ensures that continual improvements are made to further enhance the value of solutions and services, as well as customer satisfaction. Overall, the dedication to sourcing consistent raw materials, the combination of in-depth testing and manufacturing checkpoints, aids the transition from science through to solution.