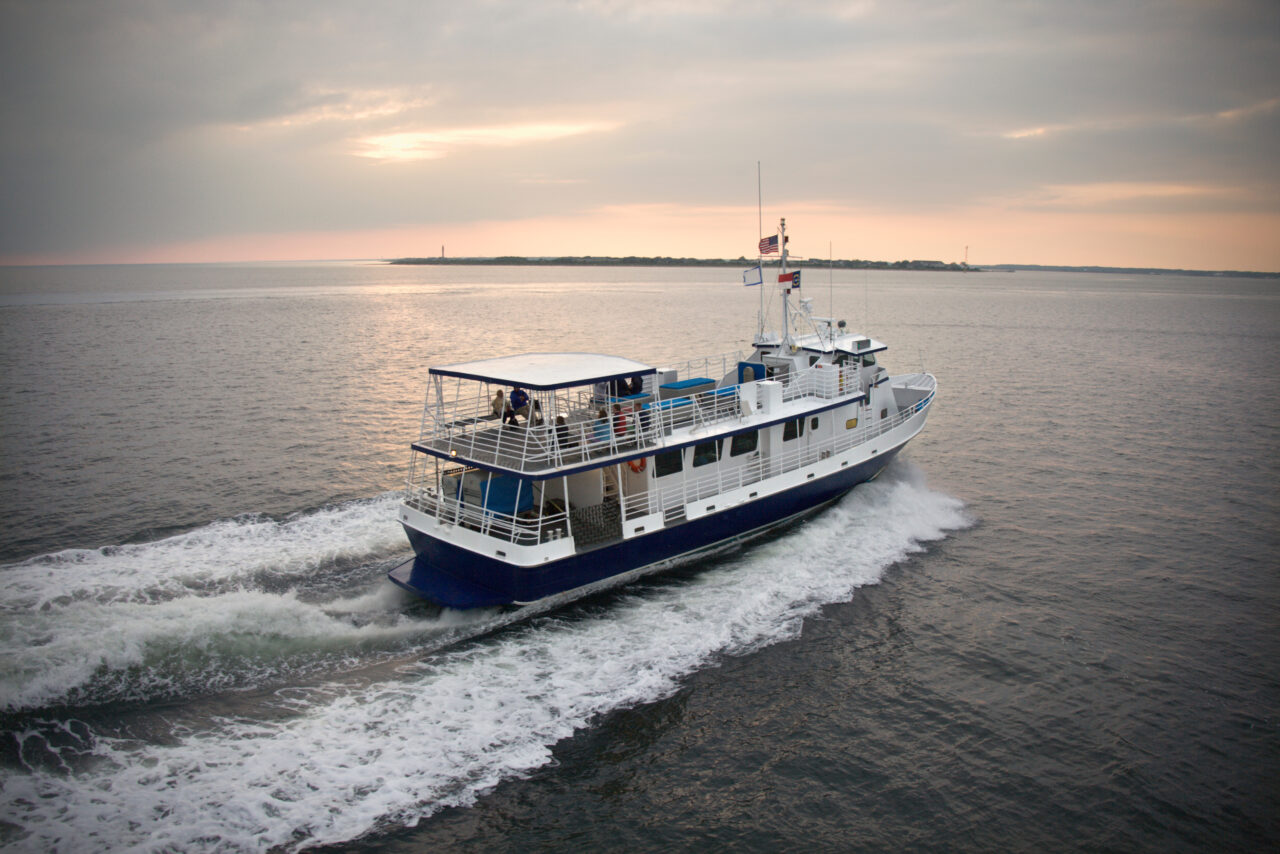
Diesel engines play critical roles across various industries, from marine vessels to heavy equipment in the agriculture and mining industries. When engine blocks become worn or cracked, performance issues such as reduced power and increased oil consumption commonly occur, potentially causing costly downtime and the need for expensive replacements.
In this Belzona case study, we demonstrate a diesel engine repair using a Belzona solution to repair a Caterpillar engine block suffering cavitation. Following an inspection from Belzona representatives, a combination of the repair composite, Belzona 1311 (Ceramic-R Metal) and the anti-corrosion coating, Belzona 1391T, was selected to provide a durable, efficient alternative to expensive replacements.
Diesel Engine Repair Method:
During a routine maintenance inspection, extensive cavitation damage was visible on the port outer of the main Caterpillar diesel engine block on a passenger ferry.
Preparing the Surface for Repair
The team prepared the surface of the diesel engine block to maximise the adhesion and ensure the longevity of the Belzona repair:
- The damaged area was thoroughly degreased with Belzona 9111 (Cleaner/Degreaser) to remove all grease, dirt and surface contaminants
- Technicians roughened the damaged areas of the diesel engine block were roughened using vacuum blasting to achieve a suitable surface profile, to enhance the Belzona epoxy’s bonding capability
Repairing the Marine Diesel Engine Block
Belzona 1311 (Ceramic R-Metal), a 100% solids repair composite, was selected due to high resistance to cavitation/erosion, combined with durability and compatibility with marine diesel engine blocks. The epoxy coating, Belzona 1391T, was chosen due to its excellent corrosion resistance properties, providing long-term protection to the diesel engine. Belzona 1391T is a fluid grade system for protecting immersed surfaces suffering from erosion-corrosion at operating temperatures up to 266 °F (130 °C) and suitable for steam-out up to 410 °F (210 °C).
- Mixing: Belzona 1311 (Ceramic R-Metal) was mixed at a ratio of 3:1 parts base to solidifier by volume, as recommended on the instructions for use sheet
- Rebuilding Application: The product was applied in a thin, even film over the area using a stiff-bristled brush. Additional layers were built up to restore the areas of deep pitting. The team used a former to recreate the cylinder skirt geometry to ensure accuracy of the diesel engine repair
- Coating Application: After the cavitation damage was repaired, the Belzona coating, Belzona 1391T, was mixed at a ratio of 4:1 parts base to solidifier by volume. It was then applied to the overall area to prevent further erosion-corrosion and cavitation damage
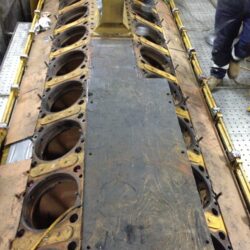
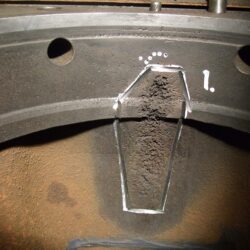
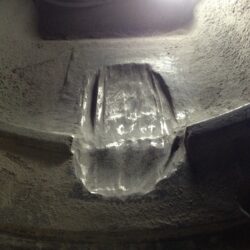
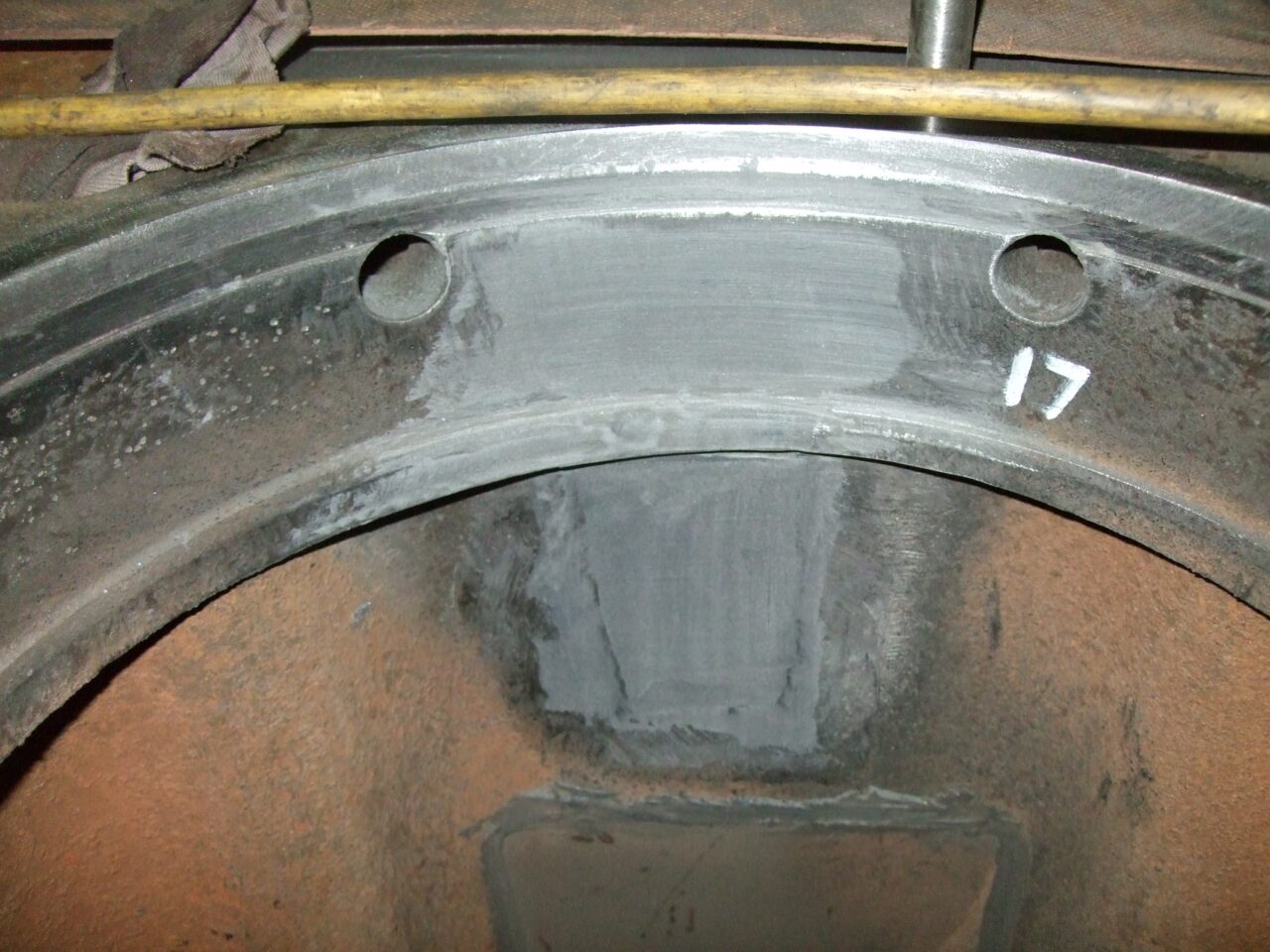
Benefits of Using Belzona for Diesel Engine Repair
Fast, Cold-Curing Repairs
- Cold-curing composites eliminate welding or hot-work, enabling diesel engines to return to service in hours – not days
- Long-term protection against high temperatures, erosion, and corrosion, making it ideal for equipment operating in demanding industrial environments such as diesel engines
Durable and Long-Term Protection
- Belzona metal adhesives and industrial coatings are 100% solids formulas which reduce VOCs and health risks, making them safer for confined-space applications
Minimised Downtime and Cost Savings
- Quick application using no specialist tools, combined with fast curing times reduce repair time and costly downtime, ideal in a marine environment
- Cold-applied solutions avoid expensive diesel engine block replacements
Proven solutions such as this one can help engineers and maintenance managers maintain the integrity of diesel engines across many industries such as heavy machinery, transportation and mining, ensuring minimal downtime and avoiding expensive replacement.
Frequently Asked Questions
Is Belzona 1391T suitable for use on diesel engine components?
Yes, Belzona 1391T is an excellent choice for diesel engine applications. Diesel engines typically operate with:
- Coolant temperatures between 195°F and 200°F (90°C–93°C)
- Oil temperatures between 210°F and 230°F (99°C–110°C)
Belzona 1391T is well-suited for these conditions, as it comfortably operates at temperatures up to 266°F (130°C) and is even suitable for steam-out conditions up to 410°F (210°C). This makes it an ideal protective coating for components exposed to the elevated temperatures and aggressive fluids found in diesel engines.
Are diesel engines expensive to repair?
Diesel engine repairs can be expensive, especially if traditional repair methods like welding or replacing entire engine components is required. However, using Belzona’s cold-curing epoxy solutions significantly reduces repair costs. Belzona solutions minimise downtime, avoid expensive part replacements, and eliminate the need for hot work or specialised tools.
Is it worth rebuilding a diesel engine?
Rebuilding a diesel engine with Belzona’s advanced epoxy composites and protective coatings is not only cost-effective, but also extends the engine’s lifespan. This method saves significant capital compared to full replacement, reduces downtime, and ensures reliable performance across diverse industrial environments.
How long will a rebuilt diesel engine last?
The lifespan of a rebuilt diesel engine depends on the quality of the repair and how well it is maintained. With Belzona’s proven metal repair techniques, rebuilt engines can perform just as well as new engines, offering durable and reliable service for years, even under demanding industrial conditions. See more Belzona repair success stories.
Why choose Belzona over a traditional diesel engine repair service?
Choosing Belzona offers significant advantages over traditional diesel engine repair services. Our cold-applied, epoxy-based solutions enable quick, safe, and cost-effective repairs without the need for welding or extensive dismantling. This minimises downtime, reduces repair costs, and extends the longevity and performance of your engine, all while maintaining structural integrity and reliability.
Contact Your Local Distributor to Learn More About How Diesel Engine Repairs
Learn More
Marine Coatings and Composites: Six Key Maintenance Areas
How to Repair and Protect Ship Bilges: A Complete Guide
How to Use Engineered Pipe Wraps for Pressure Equipment Repair
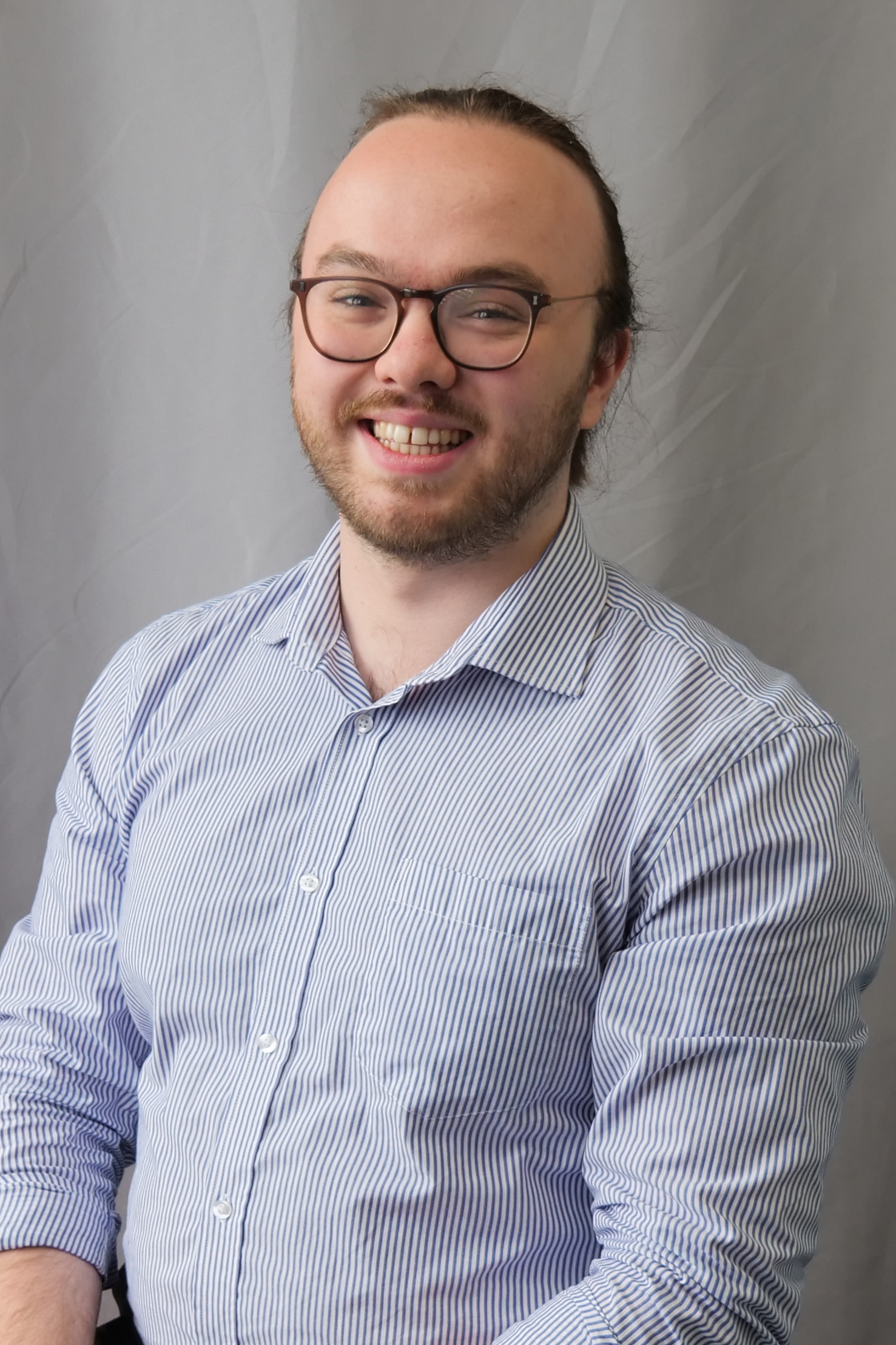
Based in the Company’s Headquarters in Harrogate, Angus Jackson joined Belzona Ltd in 2024 as a Chemical Engineer. Specialising in repair composites and protective coatings, Angus works closely with Belzona’s authorised Distributor Network, providing technical support and training.
He plays a key role in helping select and apply advanced polymeric materials for asset protection, ensuring long-term performance and reliability. In addition to delivering product training, Angus is actively involved in troubleshooting and optimising solutions for corrosion, erosion, and mechanical damage in industrial systems.
Holding an MEng in Chemical Engineering from Newcastle University, Angus has a background in pipeline engineering and simulation, with expertise in hydraulic analysis for Oil & Gas, water, and wastewater systems. His experience in flow dynamics and system optimisation provides a strong technical foundation for his current work in materials engineering. Passionate about innovation and knowledge sharing, he is dedicated to enhancing infrastructure longevity through advanced engineering solutions.