Chocks and shims have traditionally played an important role in the alignment and installation of heavy machinery and equipment. Metal chocks and mortar-based pourable chocking systems have been widely used by industries for many years. But do they offer an ideal fit-for-all solution?
In this episode we are joined by Barry Nisill, CEO of Belzona Inc., to discuss the reasons behind the increasing popularity of epoxy resin chocking systems. Barry walks us through the technology and application of resin chocking systems, and how they can benefit asset owners in various industrial settings.
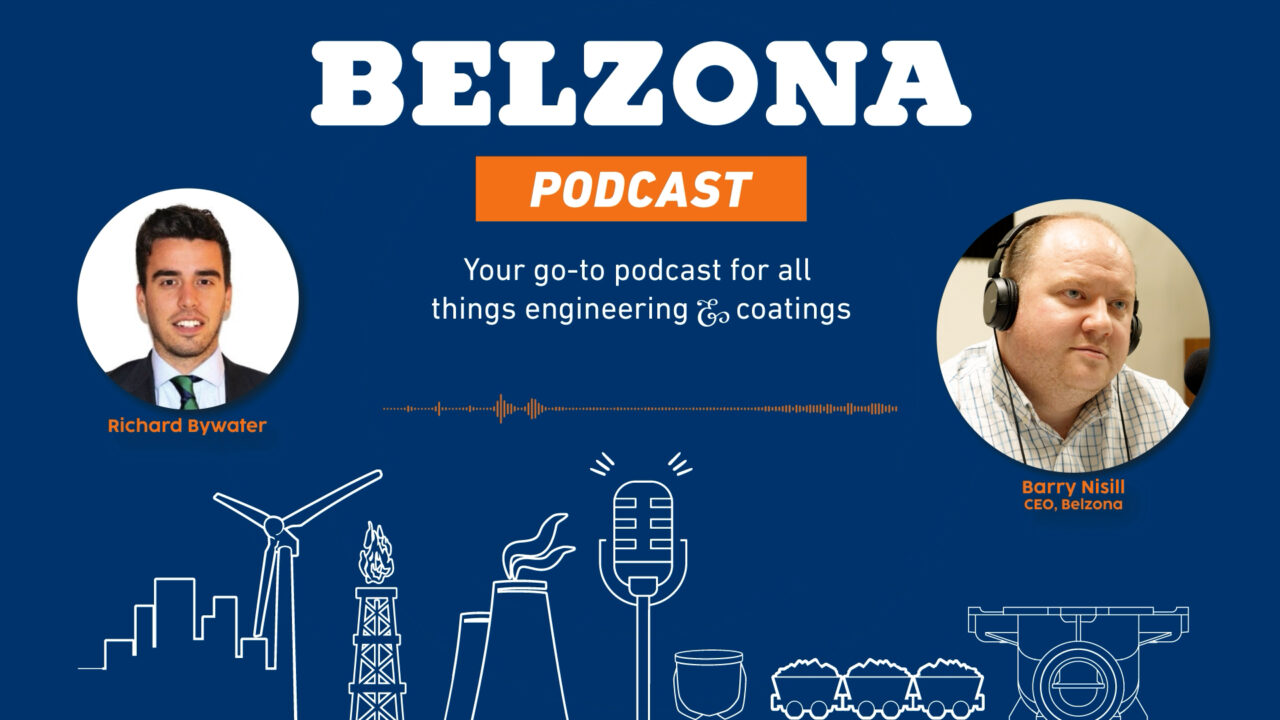
Chocking systems help create an interface between a piece of equipment and its foundation or base. Almost all machinery and equipment must have an intimate contact with the surface it is mounted to. This interface between the equipment and its structure traditionally has been accomplished by several different processes and products.
Metal chocks and shims have been used for many years to adjust the height and alignment of machinery and equipment. This typically requires much time and a skilled workforce to carry out. Metallic chocks are great technical solution, but the process is costly and unique for every new install and every time you need to make an adjustment.
Conventional chocking systems
Metal chocks and shims have been used for many years to adjust the height and alignment of machinery and equipment. This typically requires much time and a skilled workforce to carry out. Metallic chocks are great technical solution, but the process is costly and unique for every new install and every time you need to make an adjustment.
Cement based pourable mortars are very simple to use but the mechanical and physical properties tend not to provide precise alignment due to shrinkage of the chocking. They also take a long time to cure meaning the full physical properties are not available for a quick return to service.
Epoxy resin chocking systems
Epoxy resin chocks can be used for the same purpose. They do not need the same amount of time or skilled labor force to install, and yet they offer improved performance over metallic chocks. Barry adds,
An epoxy resin chock is an engineered product which is poured and cast-in-place to form a permanent chock. Resin chocks are cost effective and convenient for new equipment or for repairs, primarily because there is no need for machining. Installation time is measured in hours instead of days and weeks that are typically required for metal chocking and shimming.
Barry Nisill, CEO, Belzona Inc.
Resin chocks are often used within the marine industry with applications such as engines, auxiliaries, steering gear, deck machinery and crane rails.
Chocking systems in general industries
It is however common to see resin chocks in general industry where they are used for pumps, motors, generators, compressors, crushers, and a range of other grouting applications. General industry can make use of the same features and benefits as the marine industry. A resin chocking system can be utilized to provide key benefits such as pressure, impact and vibration resistance. They provide precise equipment alignment, dampen machine noise and vibration, prevent loosening of threaded bolts. A high load-bearing capacity is achieved for the structure, reduced installation times and does not require heat or special tools.
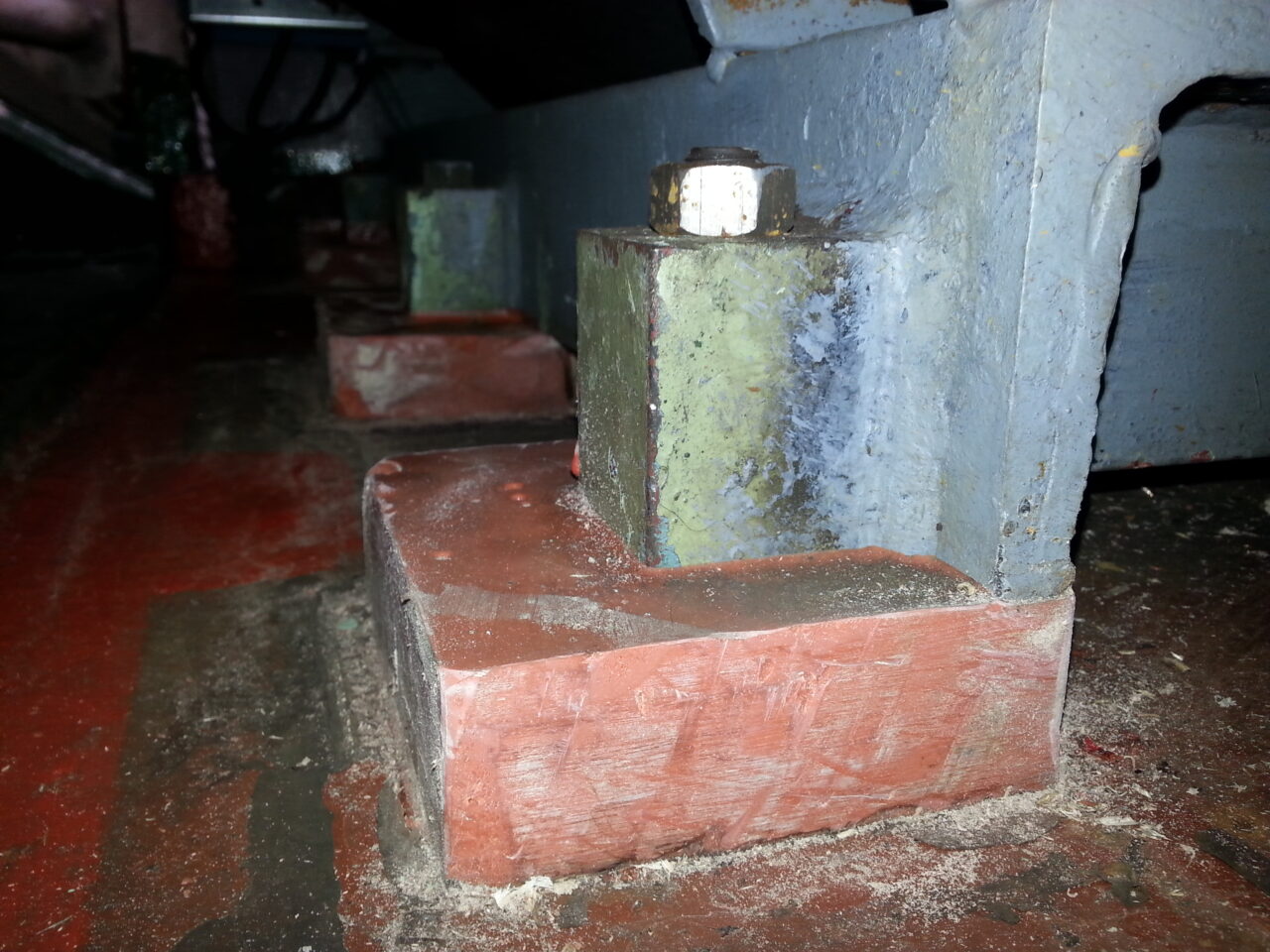
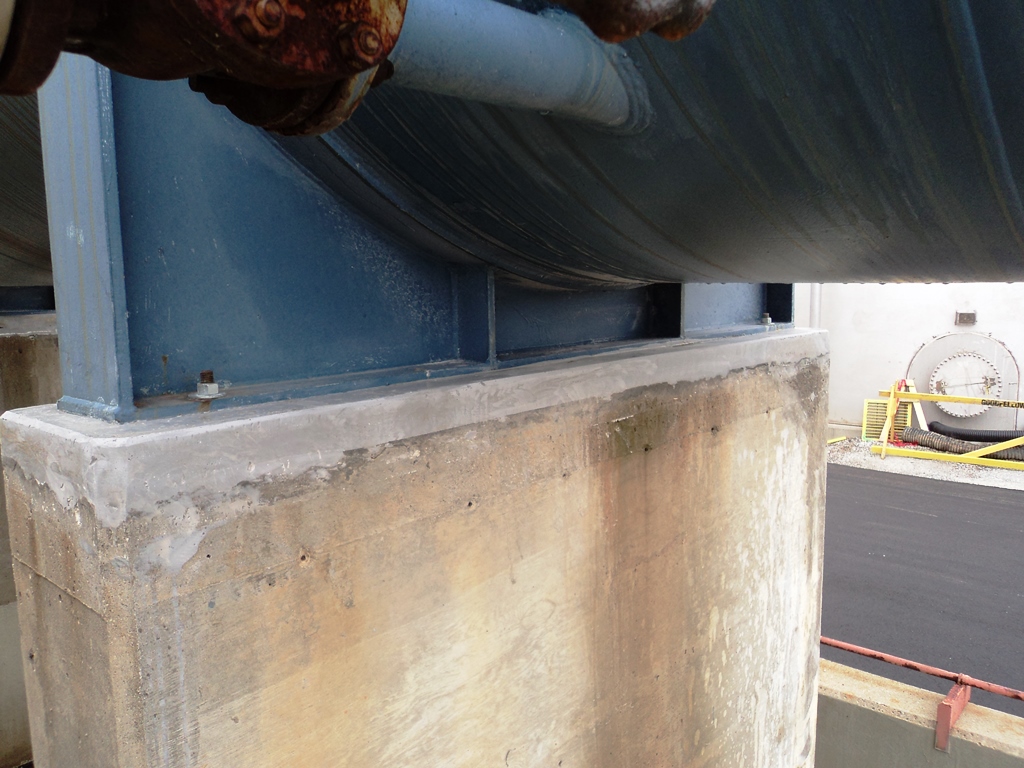
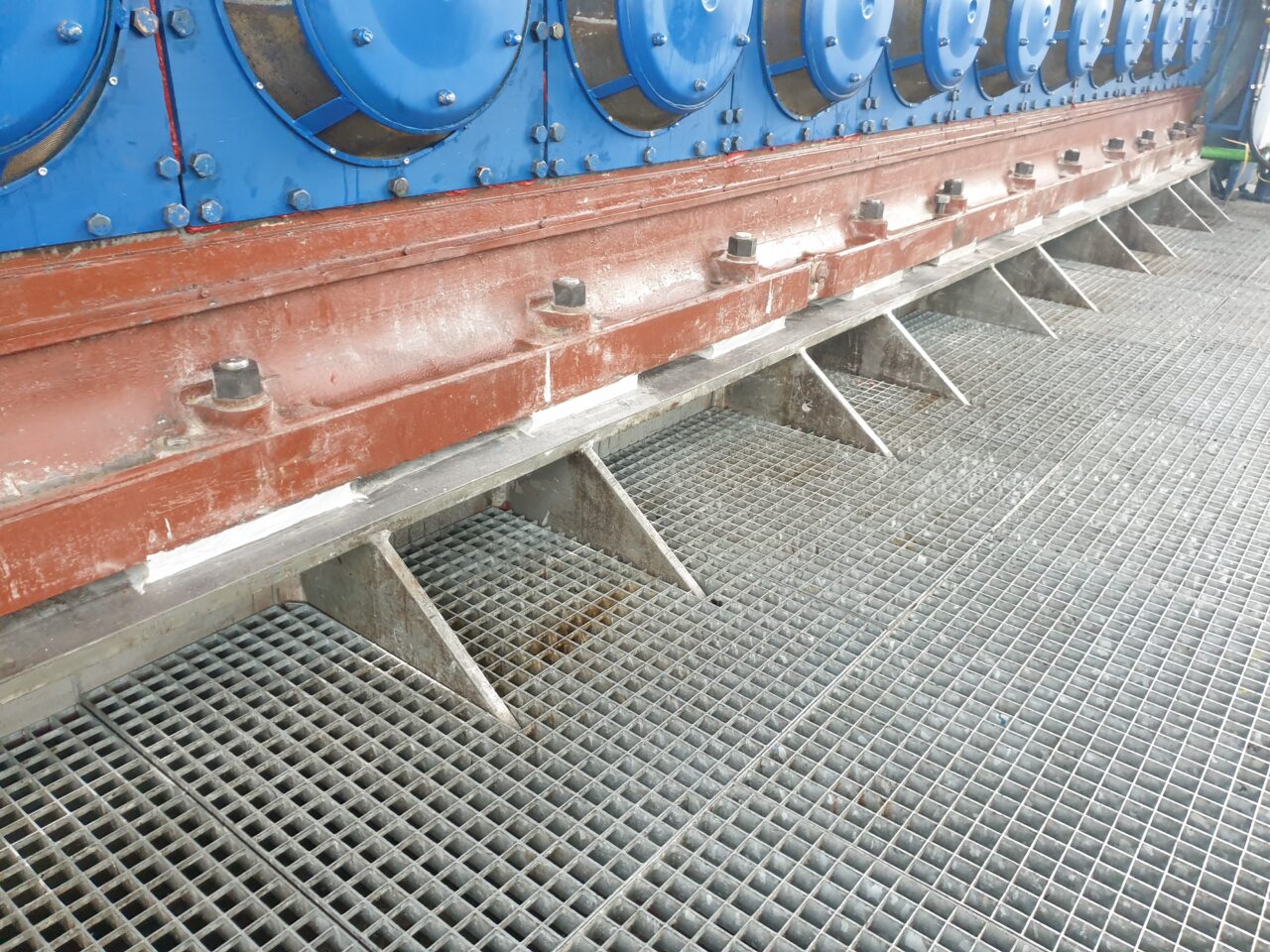
Chocking systems have been widely used in industries including lumber, mining, food and beverage, aggregate and chemical industry.
Barry recounts the details of a project he was involved with a couple of years ago at a coal mine in Montana. The mine was replacing six old conveyor belt drives with new units that achieve volume throughout with almost half the footprint. These drives had to be precisely aligned according to the alignment requirements from the manufacturer.
A number of reasons, primarily it was used to meet the requirements of the gearbox manufacturer, with the number of chocks and dimensions all in accordance with the design specification. An added benefit was the ability to replace the drives within the scheduled shutdown period of the mine. The mine was only stopped for 36 hours before the gearboxes were aligned and put back in service.
The gearboxes and motors drive the main conveyor belt of the plant, so without the conveyor the powerplant would not receive the coal from the mine, meaning no power being generated and threatening the generation capacity of the power plant.
Belzona epoxy resin chocking systems
Belzona 7111 was specified to replace the existing chocking materials, it is a cost-effective, two-part, 100% solids chocking/grouting material designed to endure the physical and thermal shock common in such industrial environments as the plant. This pourable compound is engineered to spread out evenly across irregular surfaces and ideal for creating foundations for heavy equipment where alignment and anchorage are essential.
This was Belzona’s first product in the 7000 series range of products. We have used many of our other products over the last five decades to create irregular shims, chocking and grouting. We see Belzona 1321 and Belzona 4111 used frequently for such applications, but Belzona 7111 is different it exhibits excellent non-shrinking properties, high impact strength, and compression strength along with having been specifically tested for this type of application.
This material is designed for use as a chocking or grouting material to support precise alignment under machinery and equipment ensuring effective bearing underneath, where alignment and operating reliability are critical. The product carries independent approvals from American Bureau of Shipping (ABS), Lloyds Register, DNV-GL and many more. These approvals along with our ISO9001 certified manufacturing process should help customers comfort level.
For more information about Belzona’s epoxy resin chocking systems, go to www.belzona.com.
Click the buttons below to listen to the full episode of The Belzona Podcast , and find out more about epoxy resin chocking systems and their benefits.
Subscribe and listen to the full episode on your favorite podcast platform
What is an epoxy resin epoxy?
Resin chocks are cost effective and convenient for new equipment or for repairs, primarily because there is no need for machining. Installation time is measured in hours instead of days and weeks that are typically required for metal chocking and shimming.
What are chocking systems used for?
What is a chocking system?
Interested in purchasing Belzona’s repair composites and protective coatings?
Yulia Burova, Marketing Director, Belzona Inc., Miami FL, USA