Given the expected and necessary growth of the hydropower industry over the upcoming decades, it could be argued that polymeric technology has a valuable role to play in supporting this growth. Applications, such as the one identified below, demonstrate how hydro equipment that would otherwise be decommissioned or sent to landfill can be given a new lease of life thanks to a combination of epoxy repair composites.
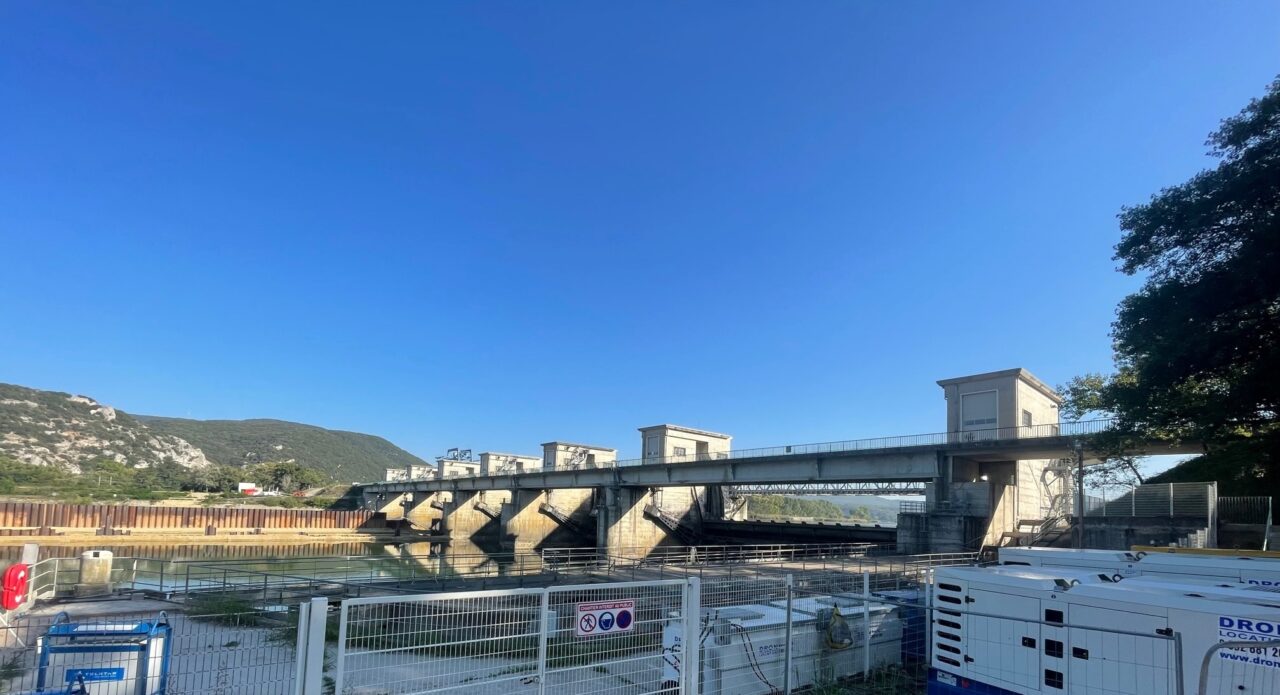
Hydropower Capacity Set to Double by 2050
According to the International Energy Association’s (IEA) ‘Net Zero by 2050’ Roadmap (revised version 2021), the hydropower industry needs to be the ‘third largest energy source in the electricity mix by 2050.’ – this involves a doubling of hydropower capacity by this date. This is in order to keep the planet aligned with a net zero by 2050 pathway.
To support this colossal scale-up of hydropower capacity, polymeric technology has an important part to play in terms of its role within hydropower plant maintenance. In order to keep a growing fleet of hydro plants running as efficiently as possible, systems such as epoxy repair composites and high-performance coatings can be deployed to repair and protect damaged assets.
Not only does this technology enable asset owners to make significant financial savings, but this circular economic business model is also extremely beneficial for the planet. It mitigates the carbon footprint that would otherwise be incurred through the process of replacing a damaged asset and sending it to landfill. In turn, by helping asset owners to avoid asset replacement, it could be argued that polymeric technology has an important part to play in supporting the transition to net zero by 2050.
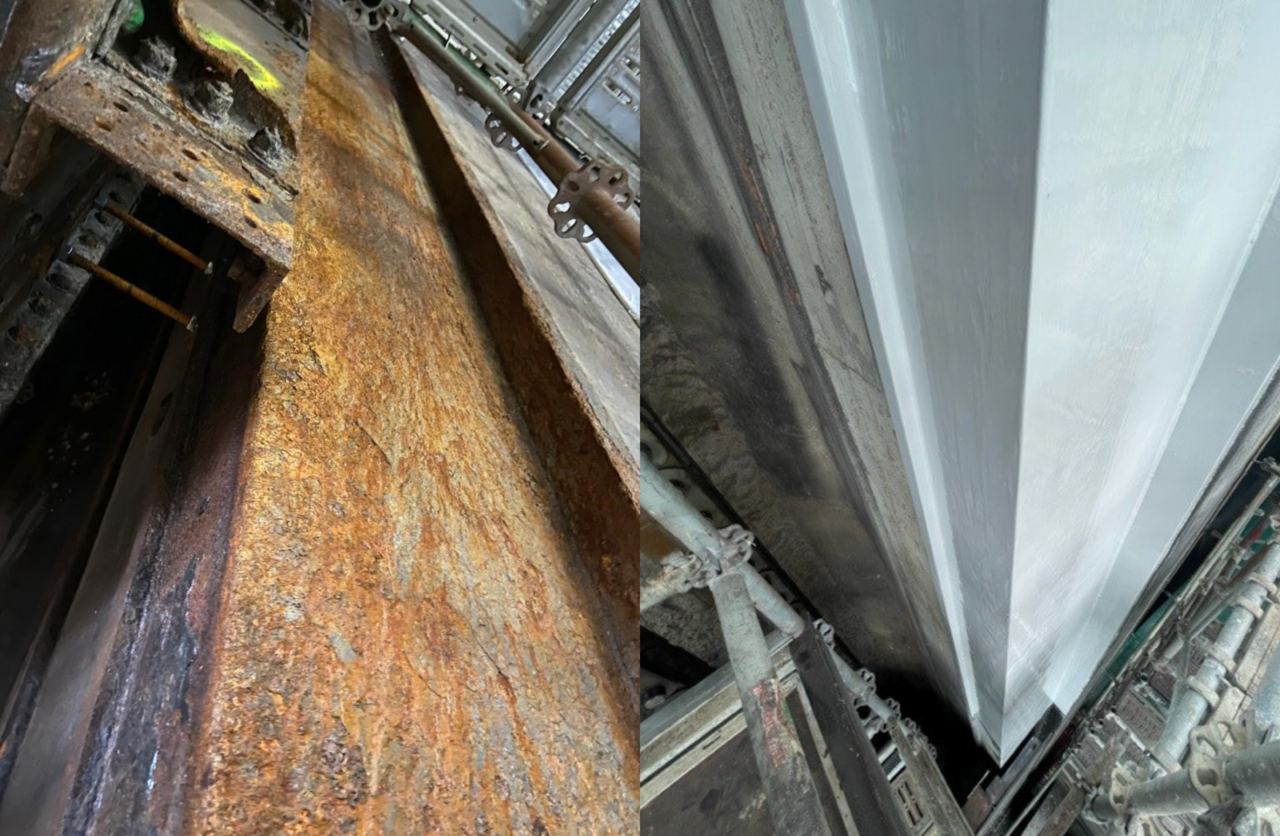
Rebuilding Sealing Faces of Hydro Equipment
A common application area where polymeric technology can be deployed in hydropower plants is dam or lock gates. These gates are highly susceptible to substantial erosion at their sealing surfaces. Factors such as pressure, water flow and consistent friction contribute to compromised seals over time. Over the years, authorised Belzona Distributor, Protecmo, has conducted a series of applications designed to repair and protect the sealing faces of hydro equipment for the long term.
For rebuilding the damaged substrate, Protecmo specify the 2-part epoxy paste, Belzona 1111 (Super Metal). As this system is specially designed for metal repair and resurfacing, it is perfectly optimised to rebuild damaged metal substrates in dam or lock gates. A solvent-free epoxy resin reinforced with silicon steel alloy, this composite repair material is corrosion-resistant, and also resists a wide range of chemicals. Thanks to its cold-curing properties, this successfully mitigates the need for hot work. The ceramic polymer, Belzona 1311 (Ceramic R-Metal), is also specified for metal rebuilding, but for situations where additional erosion resistance is required.
In order to provide long-term protection to the lock gates, Protecmo specifies the metal repair composite, Belzona 1321 (Ceramic S-Metal). This system provides excellent corrosion-erosion resistance for applications up to 60°C (140°F). This solvent-free epoxy coating also has outstanding chemical resistance and will bond to almost any rigid surface. Belzona 1331 is also used to protect assets against the effects of corrosion-erosion for temperatures up to 50°C (122°F). In addition, as Belzona 1331 can be spray applied, this makes it a practical choice for larger applications.
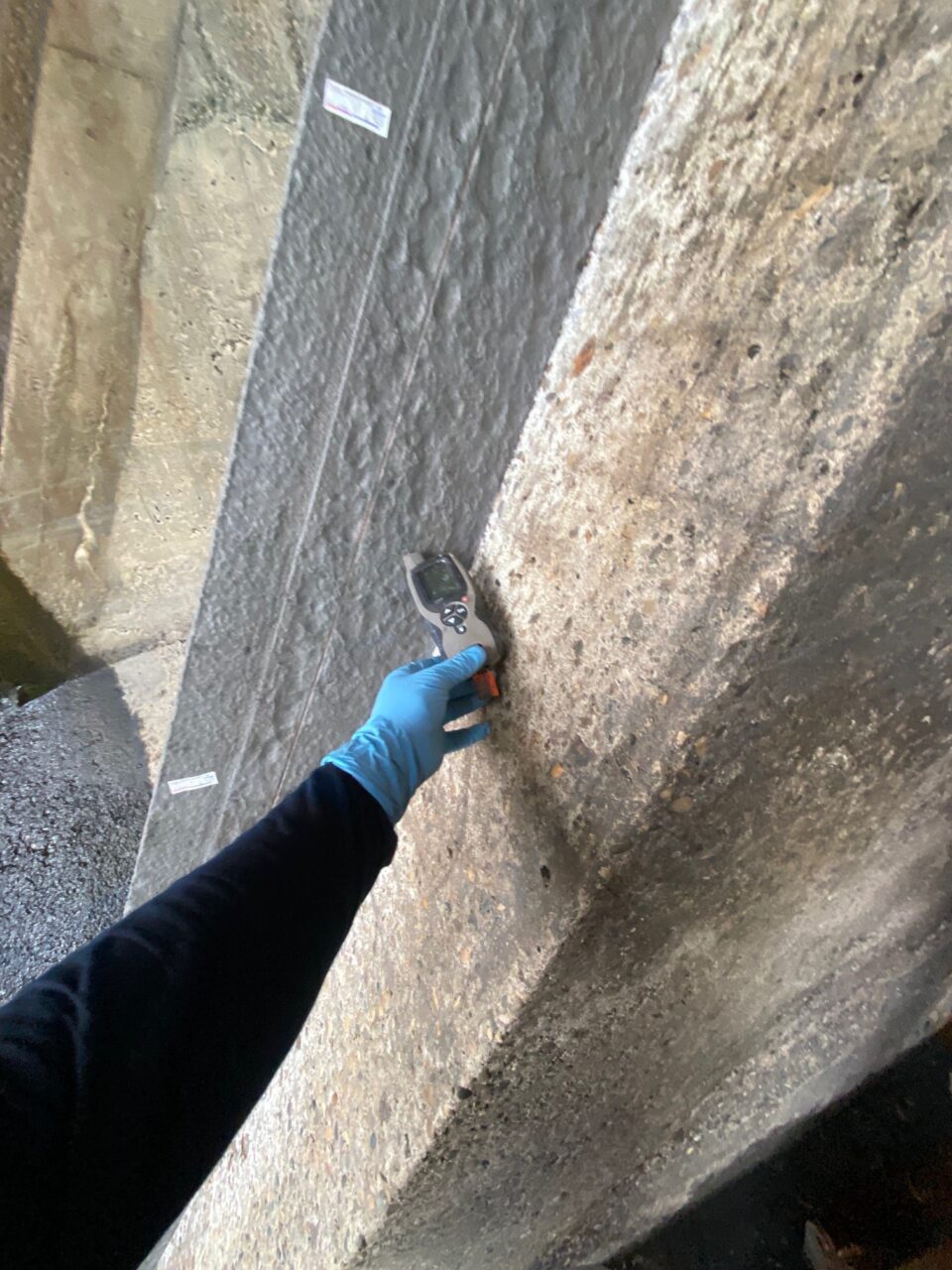
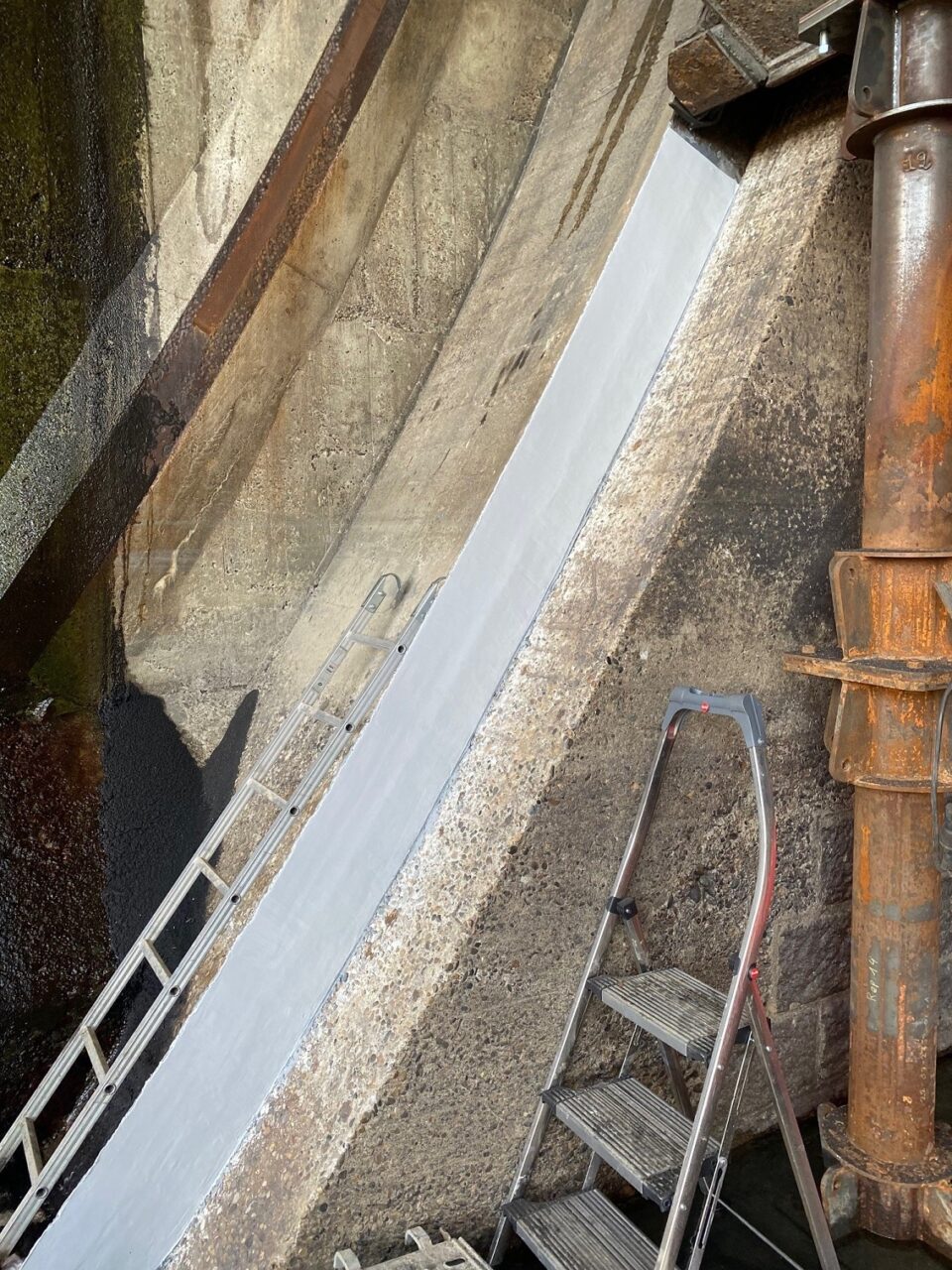
Polymeric Technology Supports the Transition to Net Zero
Considering the expected growth of the hydropower industry, it is critical that vital assets are safeguarded against damage and degradation for the long term. Polymeric technology has an important role to play in facilitating this. By repairing and protecting a damaged asset instead of replacing it, epoxy repair composites and high-performance coatings are key drivers in supporting the transition to net zero.
About Protecmo:
From power generation to paper production, steel mills to petrochemical plants, Protecmo, the Belzona Exclusive Authorised Distributor for the South of France, provides epoxy repair composites and high-performance coatings to solve a myriad of maintenance issues. The Distributorship provides local, 24-hour technical support and on-site assistance.
Want to learn more about Protecmo?
More information about how Belzona repair and protection technology can be used in the hydropower industry can be found in the following blog posts:
Can Polymeric Technology Help To “Accelerate Decarbonization” Across Multiple Industries?
How To Decarbonise The Hydropower Industry
The Hydropower Industry And Epoxy Coatings
The Hydropower Industry And Epoxy Coatings
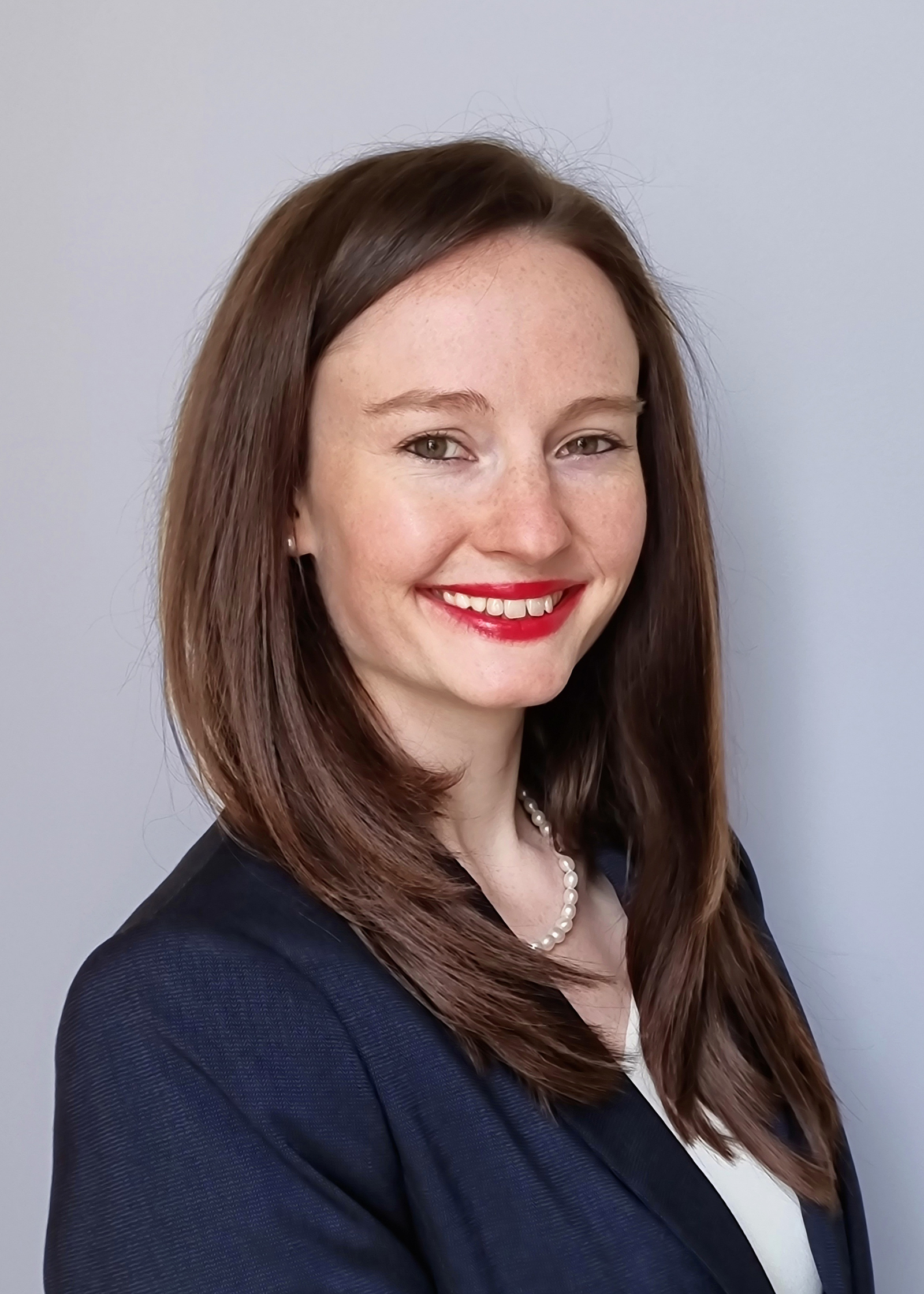
Chloe Hirst is the Senior Copywriter at Belzona Limited and is based in Harrogate, England. She gained a Bachelor’s Degree (with Hons.) in Media and Communications (specialising in Journalism) at Goldsmiths College, University of London. Chloe regularly writes case studies and thought leadership content featuring a variety of different industries, with a special focus on the renewables sector. In both 2023 and 2024, she won the Best Manufacturing Content Creation Specialist (UK) Award as part of Acquisition International’s Influential Businesswoman Awards.