- VIDEO: Pipe Wrap Repair | Belzona SuperWrap II
- How to Combat Corrosion with Pipe Wraps
- Material Selection in the Petroleum and Natural Gas Industries
- Repair Options for Pressure Equipment
- Step-by-Step Guide: How to Repair Pressure Equipment with Engineered Composite Pipe Wraps
- Ensuring an ASME PCC-2 or ISO 24817 Approved Pipe Wrap
- Frequently Asked Questions
VIDEO: Pipe Wrap Repair | Belzona SuperWrap II
How to Combat Corrosion with Pipe Wraps
Pipe wraps like Belzona SuperWrap II excel at repairing and reinforcing pressurised pipes. For pre-qualifying their system, manufacturers complete internationally recognised test standards such as ASTM G48 for corrosion resistance and ASTM D4541 for adhesion strength. Consequently, engineered composite pipe wraps provide a robust solution for corrosion protection, structural reinforcement, and leak sealing, effectively extending the lifespan of industrial piping systems.
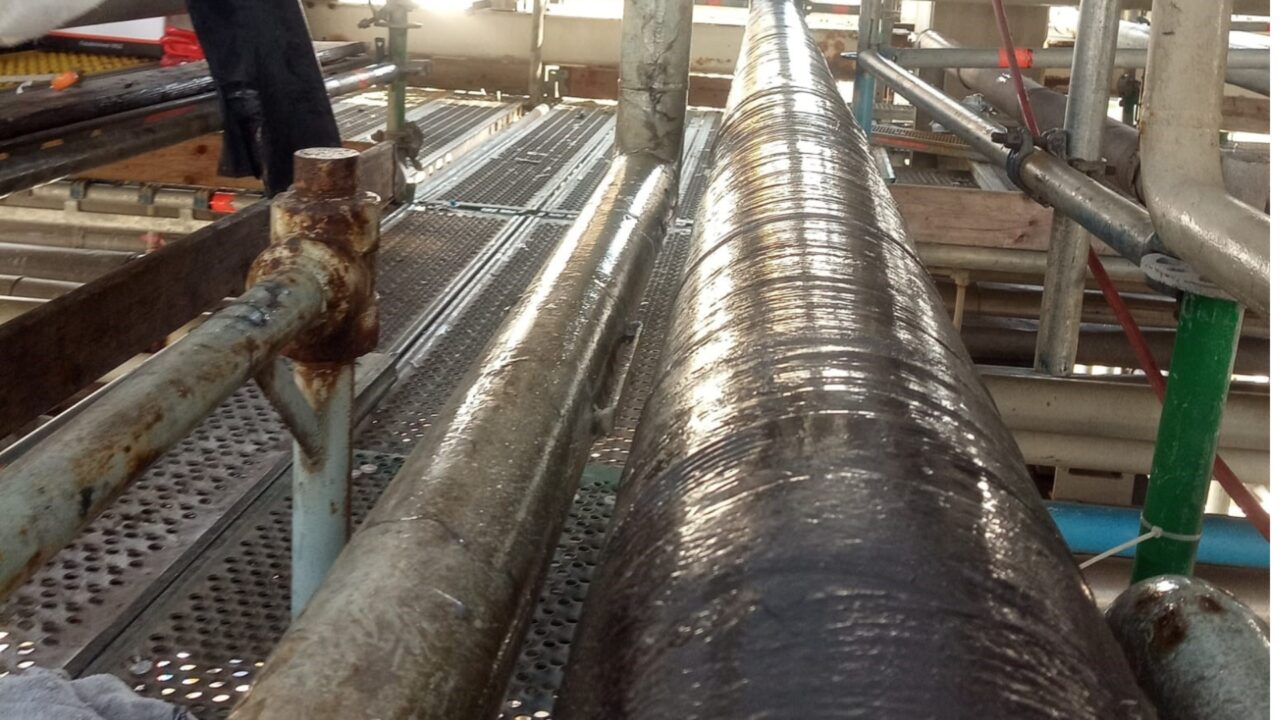
Material Selection in the Petroleum and Natural Gas Industries
In industries such as petroleum, petrochemical, and natural gas, manufacturers choose materials to fabricate flowlines, pipelines, and platform components based on their strength, corrosion resistance, and environmental suitability.
Subsequently, common choices include carbon steel for its cost-effectiveness and strength, stainless and duplex stainless steels, and corrosion-resistant alloys for superior corrosion resistance, along with alloy steel for high-temperature situations. Furthermore, manufacturers select each material according to the specific requirements for resistance to pressure, temperature, and corrosive conditions.
Even when using strong and durable materials, corrosion remains a prevalent issue in these critical sectors, therefore, addressing these issues is paramount for maintaining operational integrity.
Stainless steel – corrosion resistance Carbon steel – cost effective Alloy steel – high temperatures
Repair Options for Pressure Equipment
You can apply Belzona composite wrap systems in situ, with no need for a shutdown. This method ensures safe operations while minimising downtime, and it provides cost savings and environmental benefits.
The Belzona SuperWrap II pipe wrap meets industry standards ISO 24817 and ASME PCC-2, making it a reliable choice for various applications.
You might also consider alternative solutions such as welding, mechanical clamps and reinforcement sleeves, epoxy coatings, or replacing damaged sections, depending on specific repair needs. For effective and durable industrial pipeline wrapping, Belzona SuperWrap II offers an optimum solution.
Step-by-Step Guide: How to Repair Pressure Equipment with Engineered Composite Pipe Wraps
This guide provides step-by-step instructions on pipeline wrapping, specifically to repair pressure equipment and piping with ASME PCC-2 compliant engineered composite repair systems.
STEP 1: Pre-surface preparation
Use masking tape to mark the repair area, including at least 7.6 cm (3 in) on either side, covering the defect, the total overlay, and the taper length.
Step 2: Surface preparation
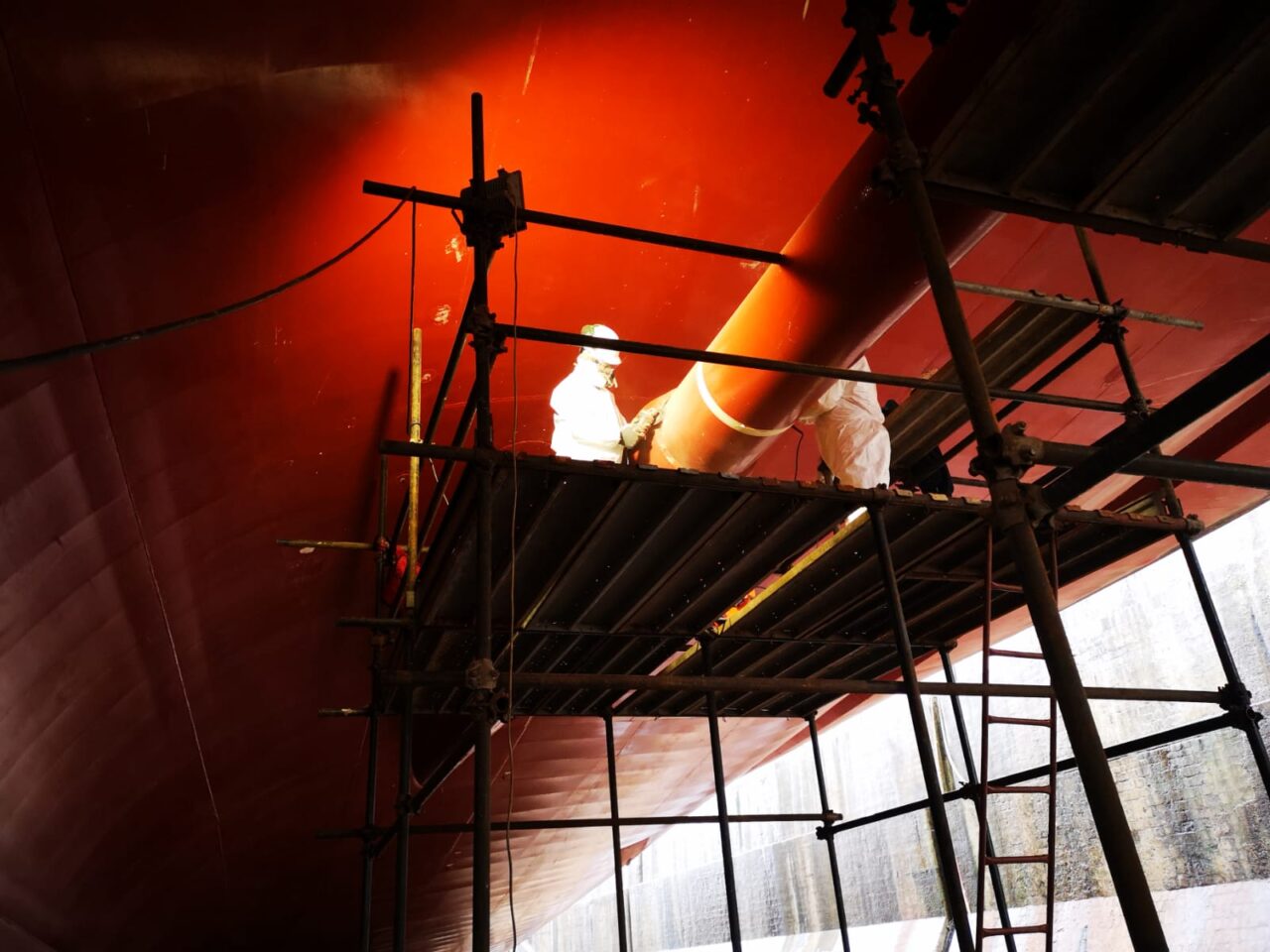
Begin by cleaning the pipe to remove any dirt, grease, or debris. Use a wire brush or sandblasting to achieve a rough surface profile, which helps the wrap adhere better.
Grit blast the repair area to achieve cleanliness levels in accordance with SSPC-SP- 10/ NACE 2/ Sa 2 ½ (Near White Metal) and an average minimum angular profile of 75 µm (3 mil). Use the Testex tape method to measure the substrate profile.
Apply a degreasing agent to the pipe surface to eliminate any remaining oils or contaminants.
Step 3: Measuring and cutting
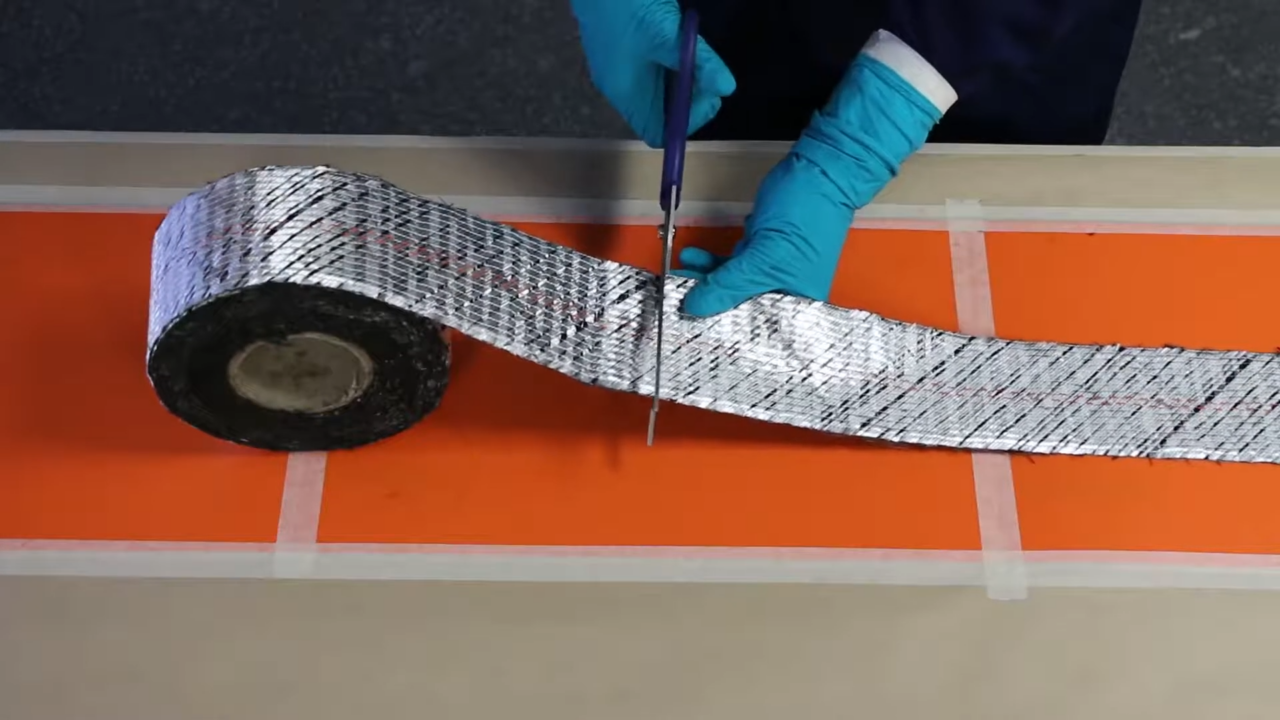
Accurately measure the length and circumference of the pipe section to be wrapped, including bends, straights, and tees.
Cut the composite wrap to the required dimensions. Ensure you have enough material to overlap by at least 50% for each layer.
Step 4: Mixing the resin
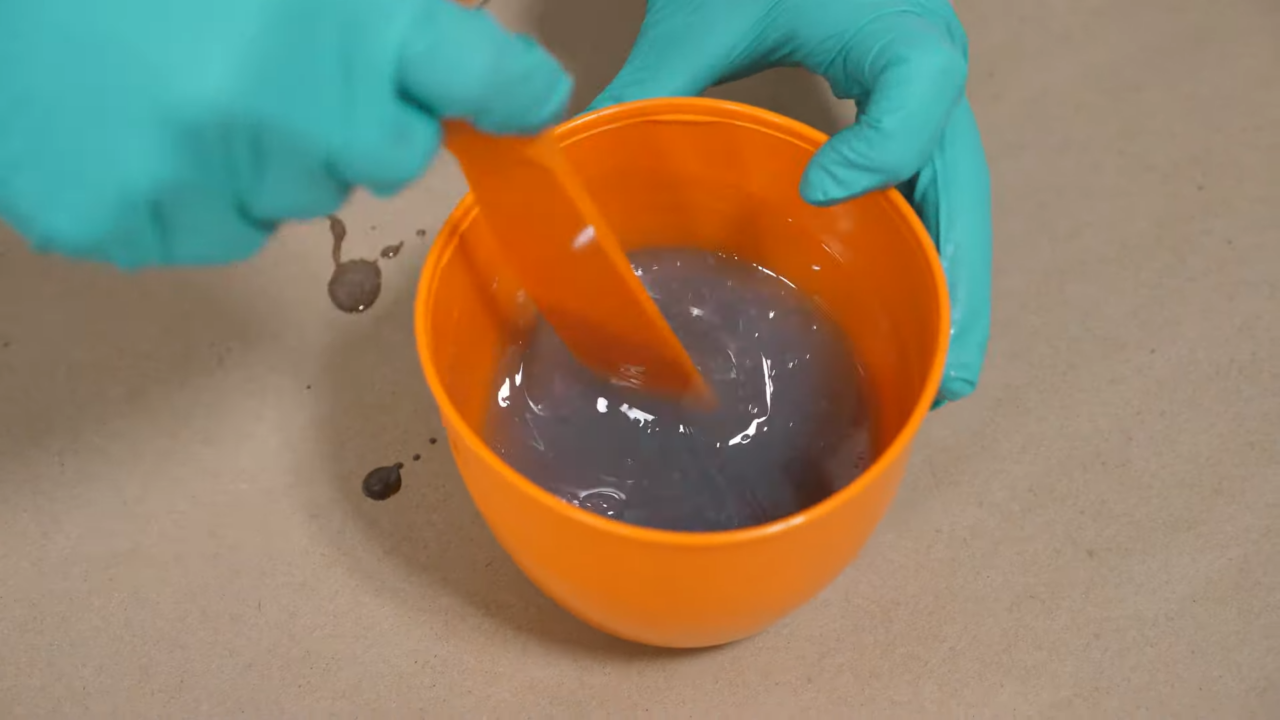
Mix the Belzona SuperWrap II resin according to the manufacturer’s Information for Use sheet.
Step 5: Wetting out
Apply Belzona SuperWrap II resin to the repair substrate. Make sure that all the repair area is wetted out. As the resin is fluid, it will spread quite easily and can be brushed in.
Using an applicator, brush, roller, or rubber squeegee, saturate the hybrid reinforcement sheet (carbon fibre/glass fibre) with resin.
Step 6: Application
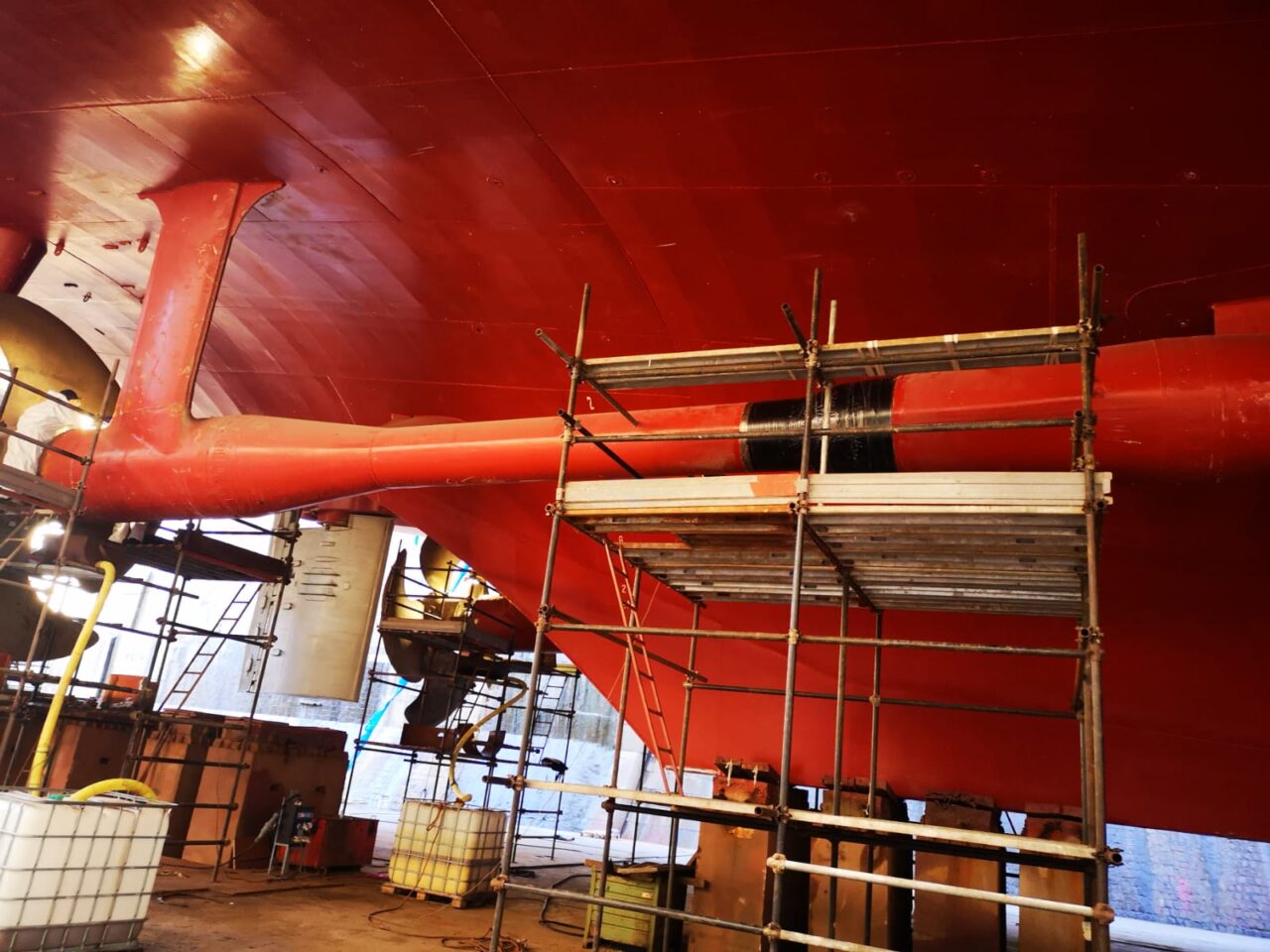
Starting from either end of the repair area, apply the composite wrap sheet onto the substrate applying tension. There should be resin exuding through the fibers.
Continue the pipe wrap with at least 50% overlap until the other end of the repair area is reached.
Step 7: Release film
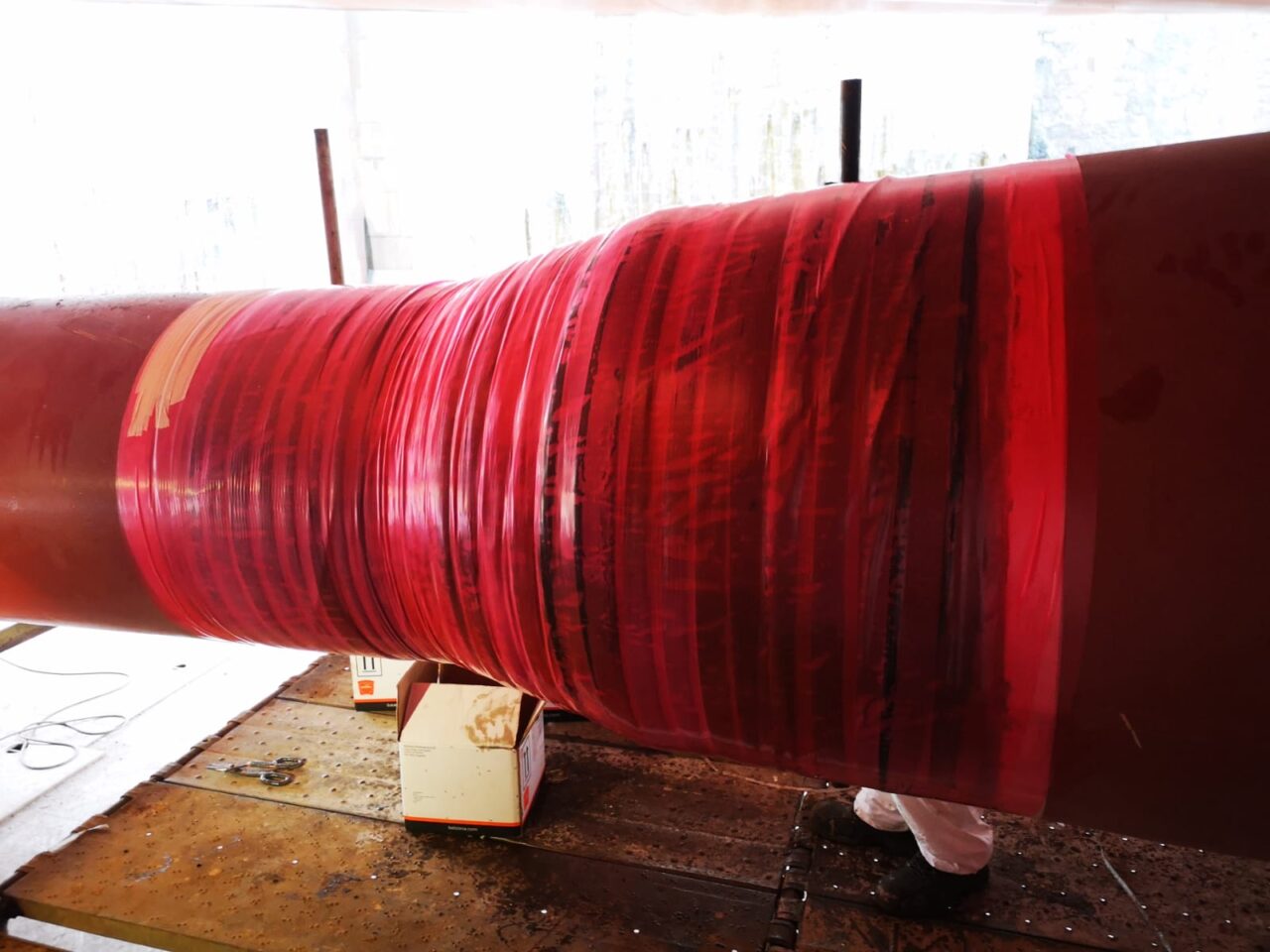
To consolidate the pipe wrap with two wraps of Belzona 9382 release film with a minimum 75% overlap.
Step 8: Curing
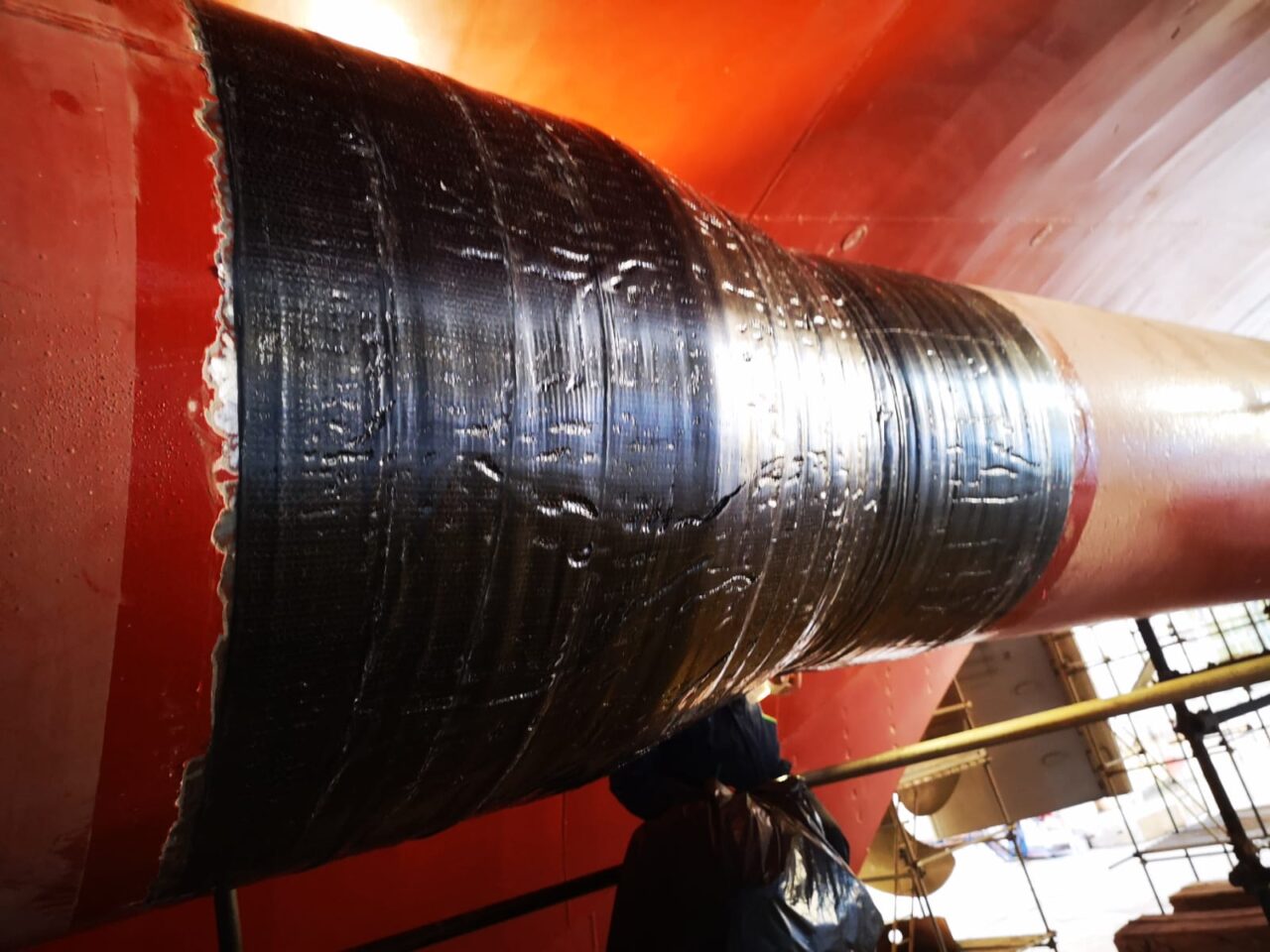
Allow the pipe wrap to cure according to the manufacturer’s Information for Use sheet. This typically involves letting the resin cure for a specific period under ambient conditions. Once cured, remove the Belzona 9382 release film.
Ensuring an ASME PCC-2 or ISO 24817 Approved Pipe Wrap
Wrapping pressure equipment and piping with engineered composite repair systems like Belzona SuperWrap II offers a durable and reliable method for repairing and reinforcing pipes.
These step-by-step instructions aim to show you how to achieve a secure and long-lasting pipe wrap that adheres to industry standards.
To ensure your repair meets ISO 24817 and ASME PCC-2 standards, a trained and validated Belzona SuperWrap II designer must design the composite repair solution. Only Belzona-trained and certified Belzona SuperWrap II Installers and Supervisors should carry out the application of the pipeline wrapping.
Frequently Asked Questions
How do you wrap a pipe?
Use a versatile, long-term composite repair system such as Belzona SuperWrap II for practical and cost-effective repair of damaged pipework, pipelines, and structural components.
What is the difference between the Belzona SuperWrap II resin grades?
https://belzona.com/en/products/applied/superwrap2.aspx
Belzona SuperWrap II Selection Guide | Belzona 1981 Winter Grade | Belzona 1982 Tropical Grade | Belzona 1983 High Temperature Grade | Belzona 1984 Surface Tolerant Grade |
---|---|---|---|---|
Application Temperature Range | 5 °C – 20 °C (41 °F – 68 °F) | 20 °C – 40 °C (68 °F – 104 °F) | 5 °C – 40 °C (41 °F – 104 °F) | 5 °C – 40 °C (41 °F – 104 °F) |
Minimum Service Temperature | -60 °C (-76 °F) | -60 °C (-76 °F) | -60 °C (-76 °F) | -60 °C (-76 °F) |
Maximum Service Temperature | 60 °C (140 °F) | 80 °C (176 °F) | 150 °C (302 °F) | 50 °C (122 °F) |
Surface Preparation Requirements | Grit Blast – ISO 8501-1/SSPC SP 10 Power Tool – SSPC SP 11 | Grit Blast – ISO 8501-1/SSPC SP 10 Power Tool – SSPC SP 11 | Grit Blast – ISO 8501-1/SSPC SP 10 | Power Tool – SSPC SP 11 |
Surface Cleanliness | Clean/Dry | Clean/Dry | Clean/Dry | Damp/Wet/Underwater |
ISO/ASME Complaint | ✓ | ✓ | ✓ | ✓ |
What types of defects can Belzona SuperWrap II address?
Belzona SuperWrap II is designed to address various defect types, including thin wall defects, internal and external corrosion, and through-wall defects. It can be engineered for service temperatures up to 150 °C (302 °F).
Can Belzona SuperWrap II be applied to live systems without shutdowns?
Yes, it can be applied to live areas without the need for shutdowns, supporting safe operations while optimising production uptime and delivering cost savings and environmental benefits.
Contact Your Local Distributor to Learn More About Belzona Solutions for Process Vessels
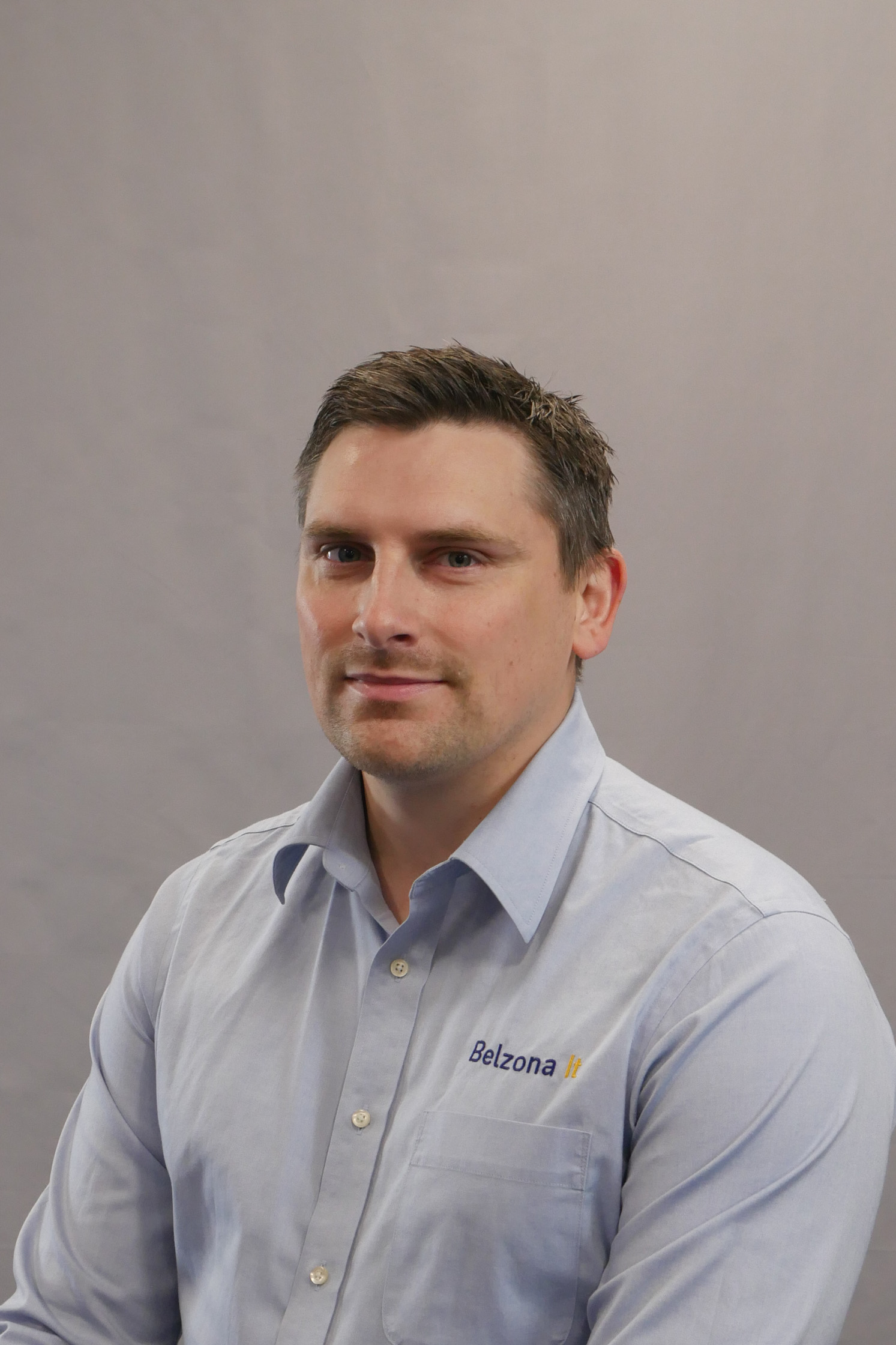
Having joined Belzona in 2010, Ian Wade has cultivated a deep expertise in corrosion, coatings, and inspection services. Currently serving as the Technical Services Manager at Belzona’s headquarters in Harrogate, Ian has held various roles. These include Technical Services Engineer and Training Facility Team Leader, where he managed the day-to-day operations of the training facility and collaborated closely with technical and business development teams.
Ian’s professional journey has taken him across the UK and international waters, including stints in South Korea, China, the North Sea, and the Caspian Sea, performing both supervisory and hands-on inspection work. His practical experience extends to on-site applications using Graco spray pumps and hand-applied coatings, directly enhancing operational standards and safety.
Ian is an AMPP (NACE) Certified Coating Inspector Level 2 and is currently advancing his knowledge by pursuing a Bachelor of Engineering in Mechanical Engineering part-time at The Open University, expected to complete in 2027. He has written a number of technical articles including: Strengthening the Bond with Reliable Structural Adhesives and The Benefits of Protecting Storage Tanks with Sprayable, Polymeric Coatings. His commitment to technical excellence and his robust experience make him a valued leader and innovator in his field.