What is a Microporous Membrane?
Microporous membranes are permeable membranes, designed to prevent water ingress whilst also allowing trapped moisture underneath to escape. They protect interiors and structures from leaks, safeguard people and equipment as well as prevent damages in industrial facilities.
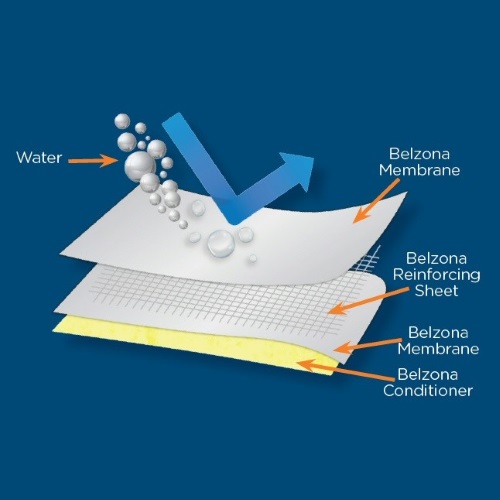
Belzona adopts microporous membranes in the development of waterproof and weatherproof coatings for emergency roof repair, insulation protection, tank base sealing, and concrete waterproof coating. These membrane coatings help mitigate maintenance issues in buildings and structures by providing strong adhesion and ensuring a long-term protection against adverse temperatures, sunlight, rainwater, and other atmospheric factors.
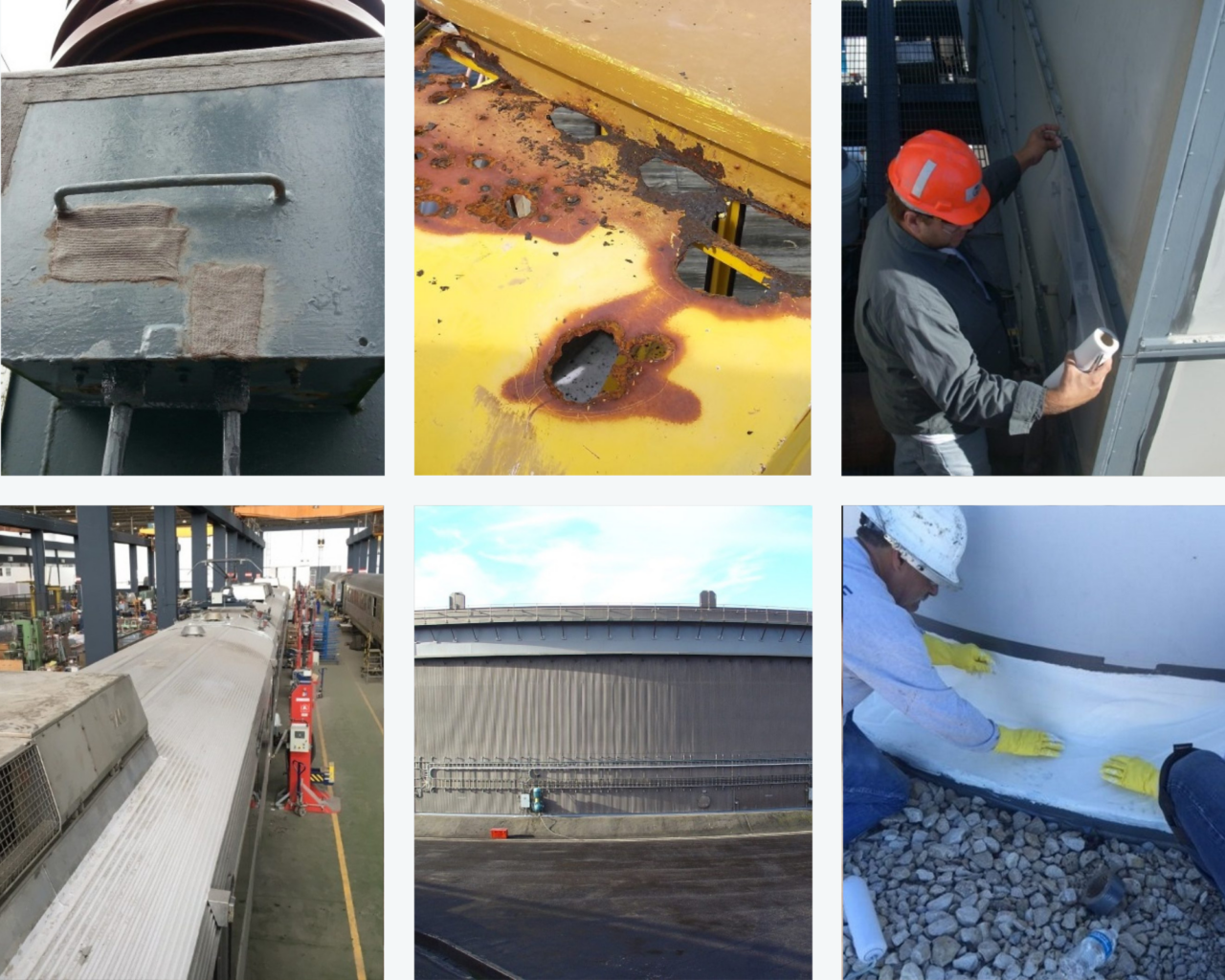
Benefits of Belzona Microporous Membranes
- Low odor systems: Their low odor properties enable applications during working hours without any disruptions to operations.
- Excellent adhesion: Belzona microporous membrane coatings can adhere to a wide range of substrates including felt, asphalt, lead, zinc, copper, glass, concrete, brick and metal.
- Weatherproofing and UV protection: The range of Belzona microporous membranes provides outstanding weatherproofing and waterproofing properties, along with solar-reflectance properties to enhance energy efficiency.
- Breathable membranes: The membranes prevent water ingress under substrates while allowing trapped water to escape.
- Corrosion resistance: Belzona vapor-permeable flexible membranes allow vapor to escape, reducing moisture accumulation and mitigating corrosion. Our solutions help prevent stress corrosion cracking at tank base sealing. Plus, our fire-resistant membrane coating can enhance the protection of thermal insulation components, preventing corrosion under insulation (CUI).
- Ease of application: Belzona membranes, including spray-applied waterproofing, can be applied easily by spray or hand, making them ideal for covering both small and large areas.
How to Use Microporous Membranes
Belzona membranes, applicable on complex geometries, can seal deteriorated sections on buildings and structures, and ensure protection for the long term. Additionally, Belzona recommends using suitable reinforcement sheets in conjunction with the membranes as they bond with the substrate beneath for a stronger and durable protection.
Belzona membranes, including Belzona 3111 (Flexible Membrane), Belzona 3121 (MR7) and Belzona 3131 (WG Membrane) can provide water resistance, shielding roof surfaces and structures from atmospheric change.
Unlike traditional solutions, Belzona 3121 (MR7) offers superior properties. It resists rain wash immediately after the application, allowing it to cure even in wet conditions.
Belzona 3211 (Lagseal), fire-resistant membrane, is an ideal solution for thermal insulation protection, cladding protection, and preventing damages on insulation components. The system is a single component water- based coating allowing the application to be easy and simple.
In the below video, we put these membranes to the test and demonstrate their fast-curing and waterproof properties, as well as their adhesion and elongation capabilities.
Learn More About Belzona Microporous Membranes
Roof Repair and Maintenance with Belzona 3111 (Flexible Membrane)
How to Use Belzona 3211 (Lagseal) for Thermal Insulation Coatings
How to Use Microporous Membranes for Tank Base Sealing
FAQ
How can an asset owner select the most appropriate Belzona microporous membrane for facility and equipment protection?
Belzona microporous membranes, including Belzona 3111 (Flexible Membrane), Belzona 3121 (MR7), Belzona 3131 (WG Membrane), and Belzona 3211 (Lagseal), are breathable membranes designed to prevent water ingress while allowing trapped moisture to escape. Each system serves specific purposes. The following table provides guidance on selecting the most suitable membranes for your needs.
Guide | Belzona 3111 (Flexible Membrane) | Belzona 3121 (MR7) | Belzona 3131 (WG Membrane) | Belzona 3211 (Lagseal) |
Roof repair | ● | ● | ● | |
CUI protection | ● | |||
Rain or washout resistance | ● | ● | ||
Leak sealing / Emergency repair | ● | |||
Single-component | ● | ● | ● | |
Water-based | ● | ● | ||
Solvent-based | ● | ● | ||
Sprayable | ● | ● | ||
Fire resistance | ● | |||
BBA/ETA approved | ● | |||
Microporous/ breathable | ● | ● | ● | ● |
Is it necessary to apply a reinforcement sheet before applying a Belzona microporous membrane?
Belzona recommends using reinforcement sheets to add durability and control film thickness. The suitable reinforcement sheet for each system is as follows:
- Belzona 3111 (Flexible Membrane) used in conjunction with Belzona 9311
- Belzona 3121 (MR7) used in conjunction with Belzona 9331
- Belzona 3131 (WG Membrane) used in conjunction with Belzona 9351
- Belzona 3211 (Lagseal) used in conjunction with Belzona 9321
Is there any testing data that can confirm the solar-reflectance properties of Belzona membrane coatings?
In addition to waterproof properties, Belzona 3111 (Flexible Membrane), exhibited high solar reflectance properties with an average SRI of 99.4% in Solar Reflectance Index (SRI) testing. The testing followed ASTM E1980-11 standards.
Contact Belzona to Learn More About Microporous Membranes
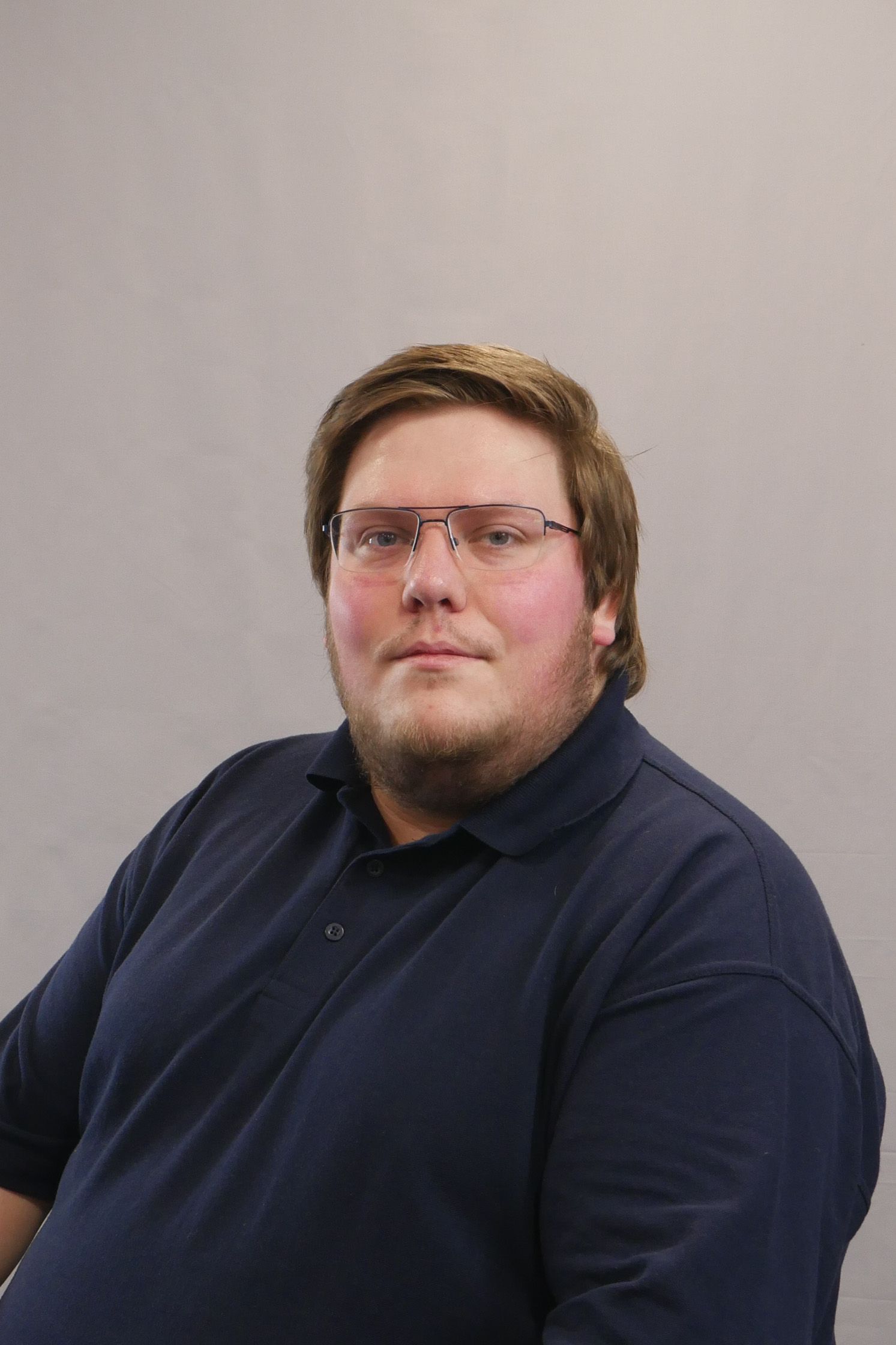
Jake Stephenson originally joined Belzona in 2014 as a Service Support Technician and has since been promoted to Training Facilitator, based at the Company’s Headquarters in Harrogate. With over a decade of experience, Jake plays a key role in leading training workshops and demonstrating the correct application of Belzona repair composites and protective coatings. In addition to leading training courses, he contributes to the creation of sales aids, exhibition materials and product testing.
Jake has been actively involved in the development of many Belzona solutions, including Belzona 4141FR, Belzona 5711, Belzona 5721 and Belzona 1984. This involved testing formulations, refining application methods and assessing product performance in various climates and conditions. He has also participated in live demonstrations at open days in numerous locations including Harrogate, Poland and Germany; showcasing Belzona’s industrial repair and protection solutions.
Holding an AMPP (NACE) Certified Coatings Inspector Level 1, Jake ensures that Belzona’s training aligns with industry standards, providing Belzona’s authorised Distributor Network with expert guidance on surface preparation, application techniques and coating inspections. His technical expertise and hands-on experience make him an invaluable asset to Belzona’s global support network.