Mechanical damage, corrosion and erosion are only some of the maintenance problems that pipelines can experience. Several solutions exist to solve this problem including welding and bonding which usually require hot work. In this podcast episode, we focus on a different industrial repair method which involves the use of composite wrap systems.
To discuss this topic, two guests joined us, Thomas Martin, Senior Business Development Engineer and Osmay Oharriz, ASME Board Member and Oil & Gas Industry Manager at Belzona.
An introduction to Composite Wraps
The first part of the episode involves a conversation with Thomas Martin. Thomas has been working at Belzona for the past five years and is an expert of Belzona’s composite wrap system, SuperWrap II. He participated in the early stages of the qualification system for the SuperWrap II system that Belzona has developed.
Today he is a certified trained, designer, applicator and supervisor for the Belzona SuperWrap II system and is the best person to give us an introduction on composite wraps.
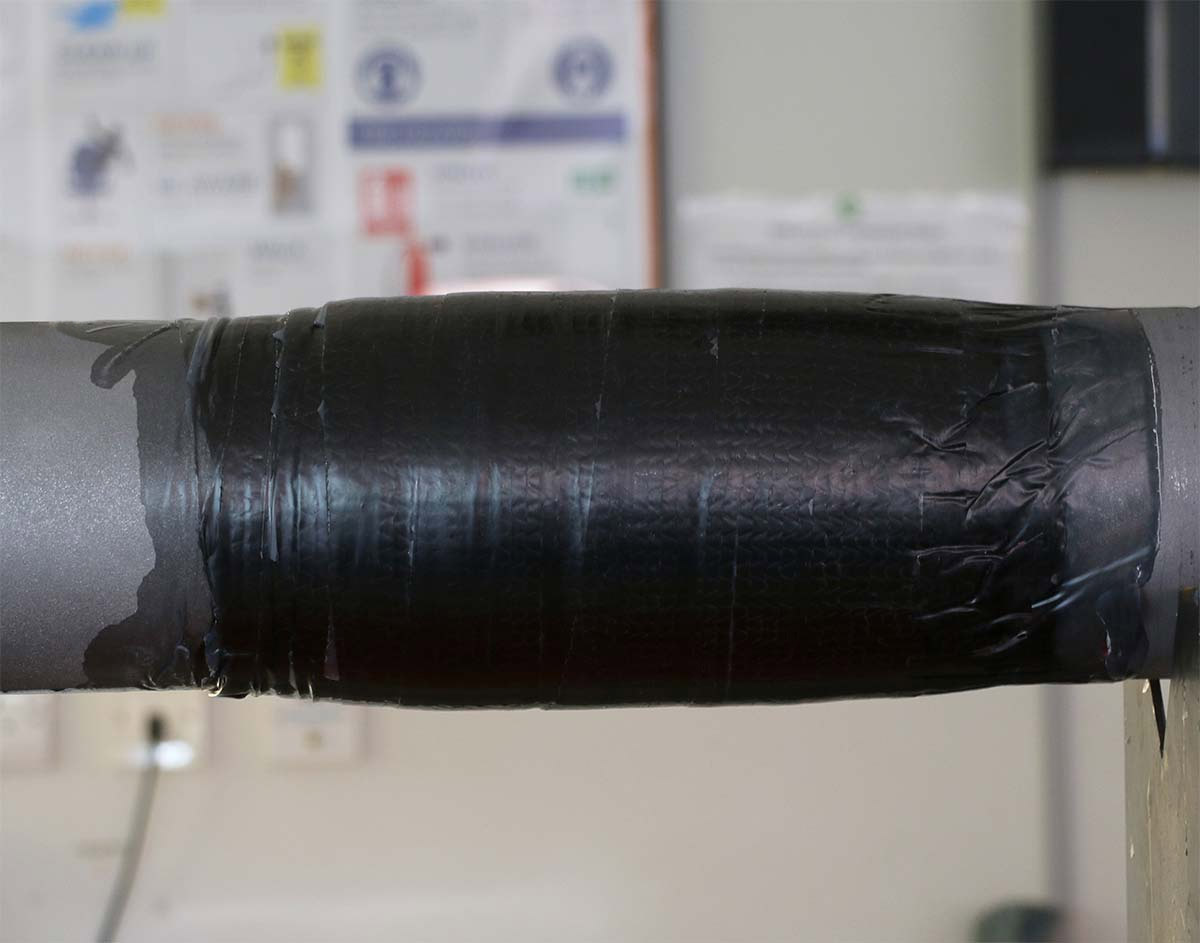
The word composite means that more than one material is used to repair or improve a piece of equipment, he explains. Here at Belzona, we use a reinforcement sheet with a resin or a paste grade material. The resin or paste grade material wet is used to out the reinforcement sheet, and together they wrap the pipe. Once it cures, it forms a reinforcing protection system on the pipe to repair leaks, corrosion damage, thin and through wall defects.
Composite wrap as a valid and standardised repair alternative to welding
As mentioned previously, the traditional repairing solution for equipment such as pipes and tanks is welding.
This method is appropriate for most situations, however, certain situations exist where using composite wraps would be advantageous as an alternative of welding:
“One of the major drawbacks that you find with welding is hot work. It requires hot work in order to be implemented and in many situations, especially if we have flammable substances, this can be very problematic. Equipment will need to be shut down and areas need to be safe for hot work. Belzona saw this opportunity and developed the composite wrapping system, originally using our paste grade materials and a reinforcement sheet, which could be used instead of welding in some cases and avoid the need for hot work.”
Thomas Martin, Senior Business Development Engineer, Belzona Polymerics, Harrogate, UK
Even if recognised as a valid alternative, composite wraps were seen more as temporary repair solutions in the past. No standards, codes or a unified way recognised by the industry were in place to help engineers take into account key information such as the pressure of the pipe, the defect size, the depth of the pitting and the temperature in which the pipe was operating while executing the repair.
Over the years however, composite wraps systems have been constantly improved and, as a result, proved to be a permanent and cost-effective repair system.
Due to the benefits that composite wraps were providing, the industry worked to put into place official standards to make them fit for purpose on more equipment and pipes, especially higher pressure and safety critical lines.
These standards were ASME PCC – 02 and ISO 24817. ISO stands for International Organisation for Standardisation while ASME stands the American Society of Mechanical Engineers.
Development of Belzona SuperWrap II system
Belzona was aware of these standards when developing its own compliant system which the public todays knows as Belzona SuperWrap. As time progressed and new technologies became available, Belzona has then updated this system into the Belzona SuperWrap II system.
The Belzona SuperWrap II material has been prequalified to the international composite repair standards ASME PCC-2 Article 4.1 and ISO 24817. It is suitable where there are requirements for engineered calculations and documentation including quality control records are needed.
The Belzona SuperWrap II compliant system enables applicators to input all the key information about the equipment that needs repairing, run them through the calculation system to offer a bespoke solution for the repair.
Belzona SuperWrap II applied only by trained applicators
To apply this composite wrap according to these ISO and ASME standard and ensure a high standard of application, applicators should be trained. Belzona runs training courses in its offices around the world to teach the right application and inspection techniques for the Belzona SuperWrap system.
The Belzona SuperWrap II training course provides specific theoretical knowledge and practical skills to design, supervise or apply Belzona’s ISO and ASME compliant composite repair system.
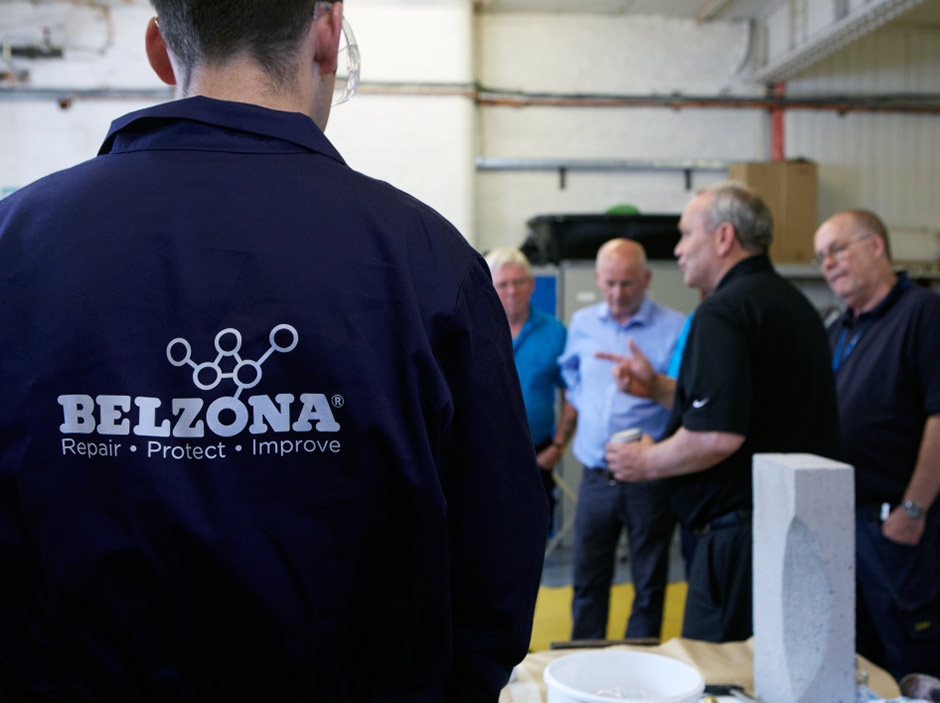
A conversation with Osmay Oharriz, ASME Committee Member
For the second part of the episode, Osmay, Oil and Gas Industry Manager and also member of the ASME committee joins our host.
Some of you may remember him from Episode 2 of the Belzona Podcast where he talked about the benefits of high temperature coatings.
In this episode, he joined our host to give us a more detailed insight into the standards that dictate the use of our Belzona composite wrap system.
What is the ASME committee?
ASME is a is an organisation that helps the global engineering community develop solutions to real world challenges.
It offers a continuously evolving collection of standards across a wide variety of topics such as construction equipment, piping, nuclear component, pressure technology and many more.
ASME PCC- 2 has existed since the early 2000s to develop standards for repair and inspection of pressure equipment, piping, pipelines after the equipment has been in service.
Members of different background are part of this committee which represent all the stakeholder of the industry. In fact, some members represent the manufacturer, others represent the asset owner or the contracting companies which enables all to look at different problems from different angles and perspectives.
The ASME PPC – 2 committee holds regular meetings to assess the equations in the standards, the procedures of inspection and repairs they follow to refine some of the approaches they previously took to reflect any new advancement in the industry.
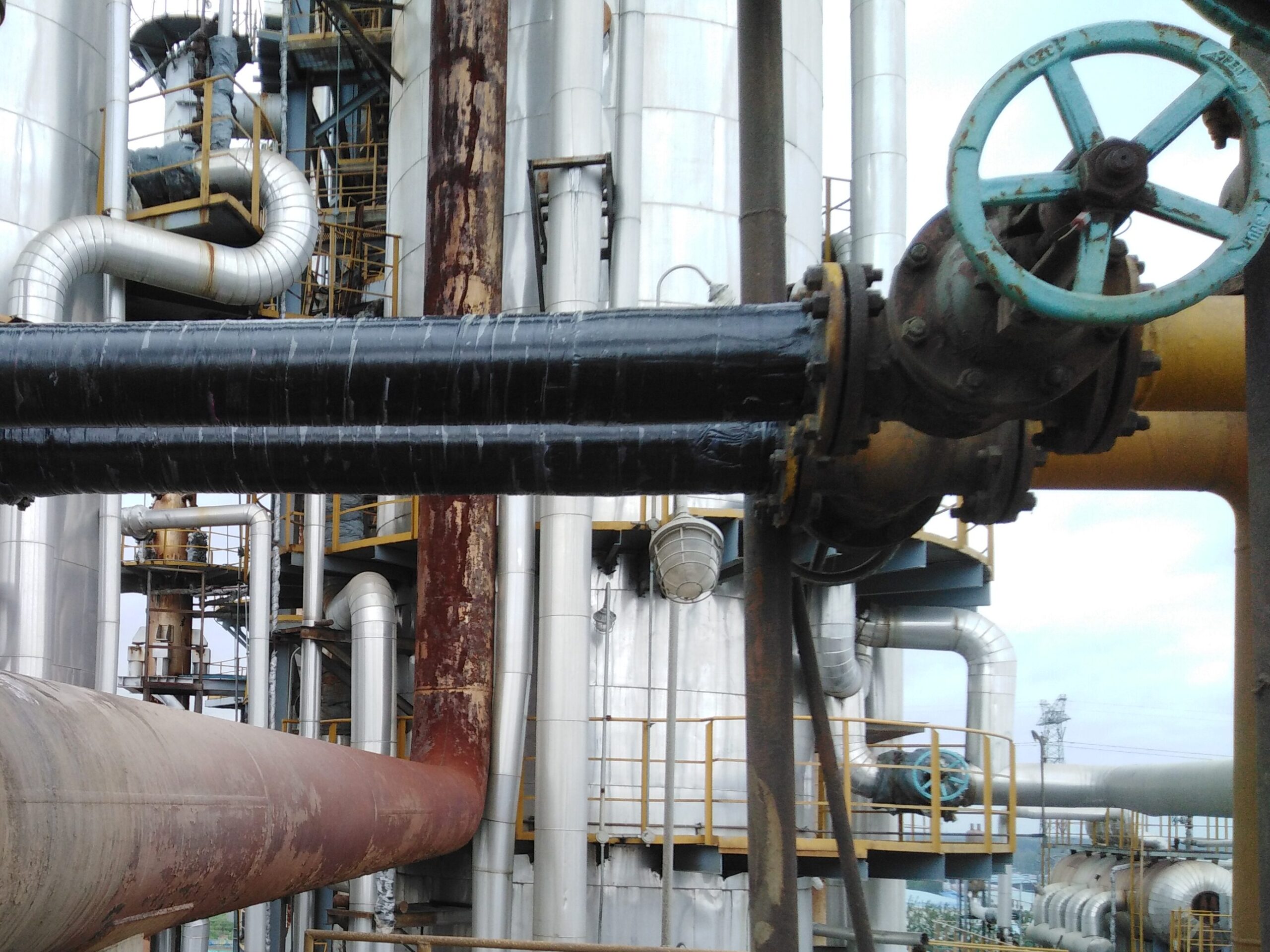
Future implementation of composite wraps repairing methods in construction standards
As mentioned by Thomas Martin, the industry did not always recognise composite wraps as permanent repair methods but this view is steadily changing.
The ASME – 02 committee sees a lot of progress being made as composite wrap systems are starting to receive the recognition they deserve by different construction standards as an effective and permanent solution.
Engineers around the world are starting to accept that metal repairing methods such as welding experience corrosion, contrary to non-metallic solutions which do not when designed and applied correctly. A lot more users are in fact embracing non-metallic solutions as a way to retrofit damaged equipment.
Very often composite repairs are originally implemented as temporary solutions, with the plan to eventually replace for a more permanent solution. In reality, after a year or two, they are not replaced as they are proved to be effective and a permanent repair.
“The positive thing is that most regulatory agencies or standard generating entities are looking for solutions implemented by methods proven by reliable engineering testing and analysis and can permanently restore the serviceability of the damaged substrate.”
Osmay Oharriz, Oil & Gas Industry Manager at Belzona and ASME Board Member
There are already some construction standards that mention the use of composite wraps as a method of repair which are:
- ASME B31.4 which covers pipelines which transport liquids and slurries.
- ASME B31.8 which covers pipelines transporting gases.
The committee is confident that an increasing number of construction standards will soon include non-metallic composite wraps systems as a way to permanently repair a piece of equipment.
What is positive is that regulatory agencies are looking for solutions that can be implemented by methods that have been proven engineering testing and analysis, the maths is the evidence that it works.
Here at Belzona, as part of our on-going product development we are always working on improving our current standards, making the products easy to use and that they also align with technological development.
This, in hand with the opportunity to carry out in-service inspection, and supported by training will certainly ensure successful applications which is the end goal.