Since 1952, when Belzona developed its first corrosion-resistant zinc coating, the Company has been pioneering corrosion protection methods for steel substrates.
Steel is even more integral to how we live than it appears at first glance due to its prevalence in manufacturing. Steel machinery is used in practically every form of production, from glass to paper, such is its importance. In 2017, so-called tool steels accounted for 15% of global steel use, according to worldsteel.org. Tool steels are specially constructed alloys with beneficial properties for manufacturing industries, such as heat resistance, strength, and improved corrosion resistance.
However, despite these properties, tool steels remain vulnerable to corrosion and so must be replaced or protected. Steel prices are rising due to a combination of the European energy crisis and the effects of the pandemic, with Global Times reporting that many Chinese steel factories were still operating at just 70% efficiency by summer 2021, contributing to extended lead times for new equipment.
Meanwhile, the drive towards a sustainable future has alerted asset-owners to the adverse environmental impact of steel manufacturing, with The World Counts reporting that steel production is the world’s most energy-consuming industry, adding over 3.3 million tonnes to global CO2 emission annually.
The cost, environmental impact and lead times of replacing steel ensures that steel corrosion protection methods such as industrial coatings are a more attractive option than replacing corroded steel machinery to maintain asset integrity and reduce downtime.
This guide details the properties of Belzona’s corrosion-resistant coatings for steel, with the aim of helping asset-owners to choose the most effective steel corrosion protection method.
Erosion-Corrosion Protection Methods for Steel
For environments where a high level of erosion takes place, such as fluid handling steel pumps and nozzles, Belzona’s industrial epoxy coatings provide superior erosion resistance and offer outstanding adhesion to steel.
Belzona 1321 (Ceramic S-Metal) achieves excellent adhesion to almost any rigid surface and, once fully cured, provides superb corrosion resistance, showing no visible signs of corrosion after 5,000 hours of exposure in the ASTM B117 salt spray cabinet. It is often used to overcoat Belzona 1311 (Ceramic R-Metal) to ensure long-lasting erosion-corrosion performance.
Meanwhile, the industrial coating, Belzona 1331, was specifically designed as a sprayable coating which provides erosion-corrosion resistance without causing undue wear on spray equipment. It is capable of high-build application in a single coating without sagging, high flexibility and toughness, and 24-hour overcoatability. Not only does Belzona 1331 possess good all-round chemical resistance to dilute acids, alkalis, hydrocarbons, solvents and amines, but it offers excellent erosion resistance, showing no signs of corrosion after salt spraying for 10,000 hours.
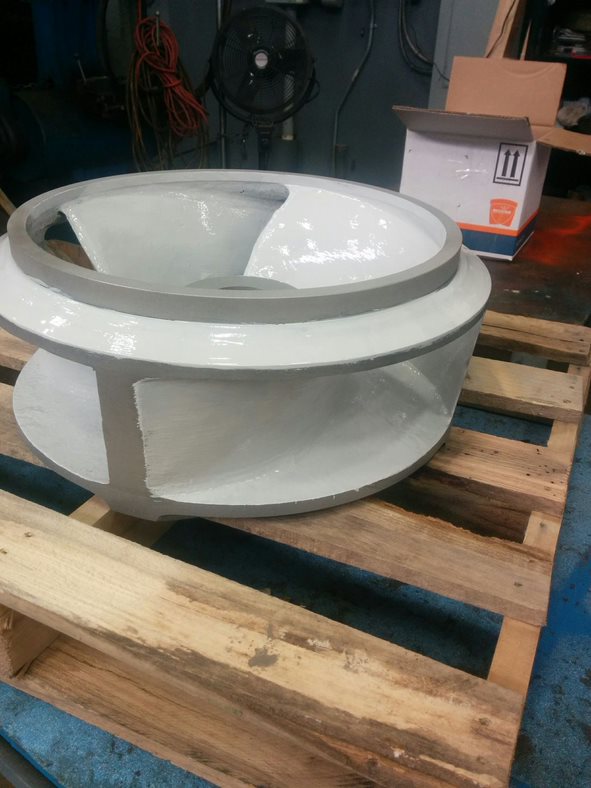
Temperature-Resistant Corrosion Protection Methods for Steel
Steel manufacturing equipment often functions in hot conditions, meaning that corrosion-resistant coatings must also be able to withstand high temperatures. Equipment such as heat exchangers, process vessels and pipelines, particularly in industries such as Oil and Gas, must often be protected against the effects of corrosion at high temperatures. Belzona’s heat resistant epoxy coatings provide these industries with corrosion protection for steel.
Belzona 5892 has been tested to prove its suitability for immersion in hydrocarbons and other aqueous solutions, protecting equipment from the effects of corrosion up to 95°C (203°F). Additionally, the two-part epoxy is approved by WRAS and NSF/ANSI 61, meaning that it is suitable for continuous immersion in hot potable water. This makes it the ideal corrosion protection method for steel in the Drinks Industry. Finally, its FDA 21 CFR 175.300 approval validates it for contact with a broad range of food types.
For even higher temperatures, Belzona 1593 provides excellent corrosion protection, with high performance in aggressive tests such as the Atlas Cell Cold Wall Immersion Testing (NACE TM0174 procedure A). Belzona 1593 shows no blistering or rusting after six months continuous immersion in water at 160°C (320°F). High performance at aggressive temperatures has led to the industrial coating’s use in extreme environments.
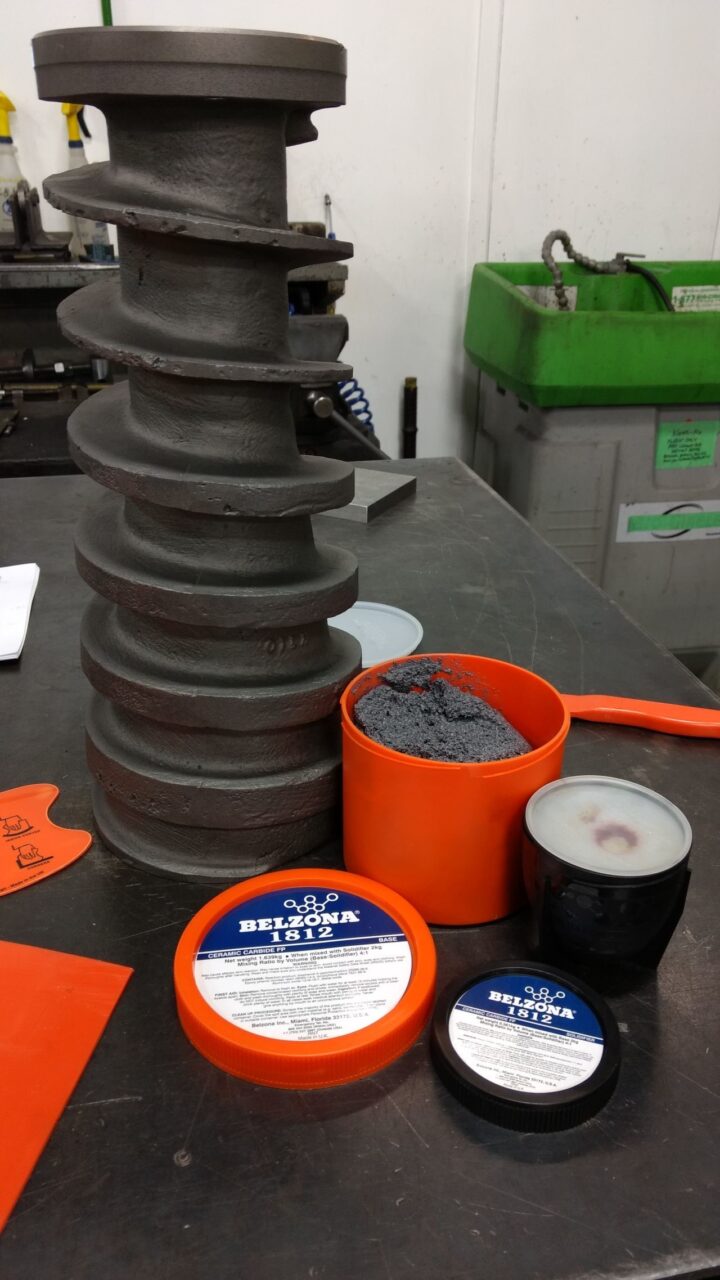
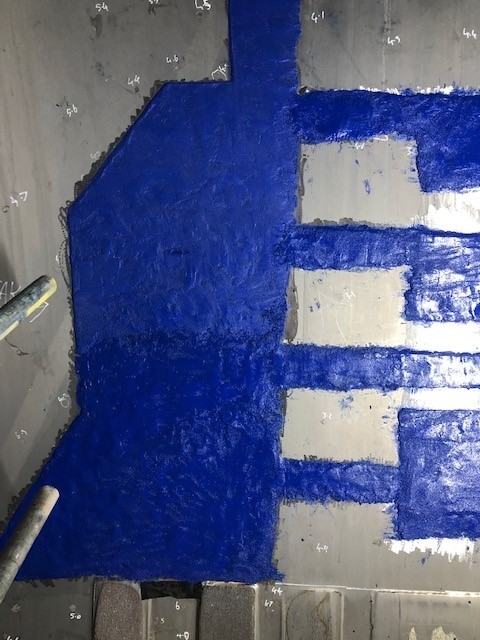
Heavy Abrasion Resistant Corrosion Protection Methods for Steel
Steel substrates can also face heavy abrasion, particularly solid-carrying equipment such as slurry pumps which transport large volumes of solid particles. Belzona’s 1800 series repair composite epoxy linings provide longstanding corrosion protection against heavy abrasion, with different products chosen depending on the working environment.
Belzona 1811 (Ceramic Carbide) offers corrosion protection for steel subjected to large particle abrasion, while Belzona 1812 (Ceramic Carbide FP) is suitable for finer particles. Meanwhile, Belzona 1814 is more cost-effective for larger application areas.
The high temperature abrasion resistant lining solution, Belzona 1813, is the best abrasion resistant corrosion protection method for steel at high temperatures, with suitability up to 190°C (374°F) when subjected to wet (slurry) conditions. Meanwhile, Belzona 1818 is most appropriate for emergency corrosion protection due to its fast curing and surface tolerant properties, minimising downtime.
Chemical Resistant Corrosion Protection Methods for Steel
For steel substrates at risk of chemical attack, particularly equipment such as pump impellers and tanks, the two-part epoxy coating, Belzona 4311 (Magma CR1), is the principle chemical resistant coating for aggressive chemical attack. It adheres very well to rigid substrates and has provided excellent resistance against concentrated inorganic acids and alkalis, approved in accordance with ISO 2812-1.
Surface Tolerant Corrosion Protection Methods for Steel
In industries such as Oil & Gas and Petrochemical, steel equipment can be exposed to water or oil contamination. To provide corrosion protection, contaminated surfaces which cannot be cleaned and dried must be coated with a surface tolerant epoxy coating which can displace contaminants, such as Belzona 5831 (ST-Barrier).
The ability of the coating to be applied and cured underwater ensures that it can be applied in-situ, drastically reducing downtime. Alternatively, Belzona 5831LT can be applied to steel substrates at temperatures as low as 5°C (41°F), which is particularly beneficial for the Marine Industry.
Corrosion is a fundamental problem for steel assets, but fortunately Belzona’s epoxy coatings provide corrosion protection for a wide variety of circumstances to increase output, drive sustainability and cut replacement costs.
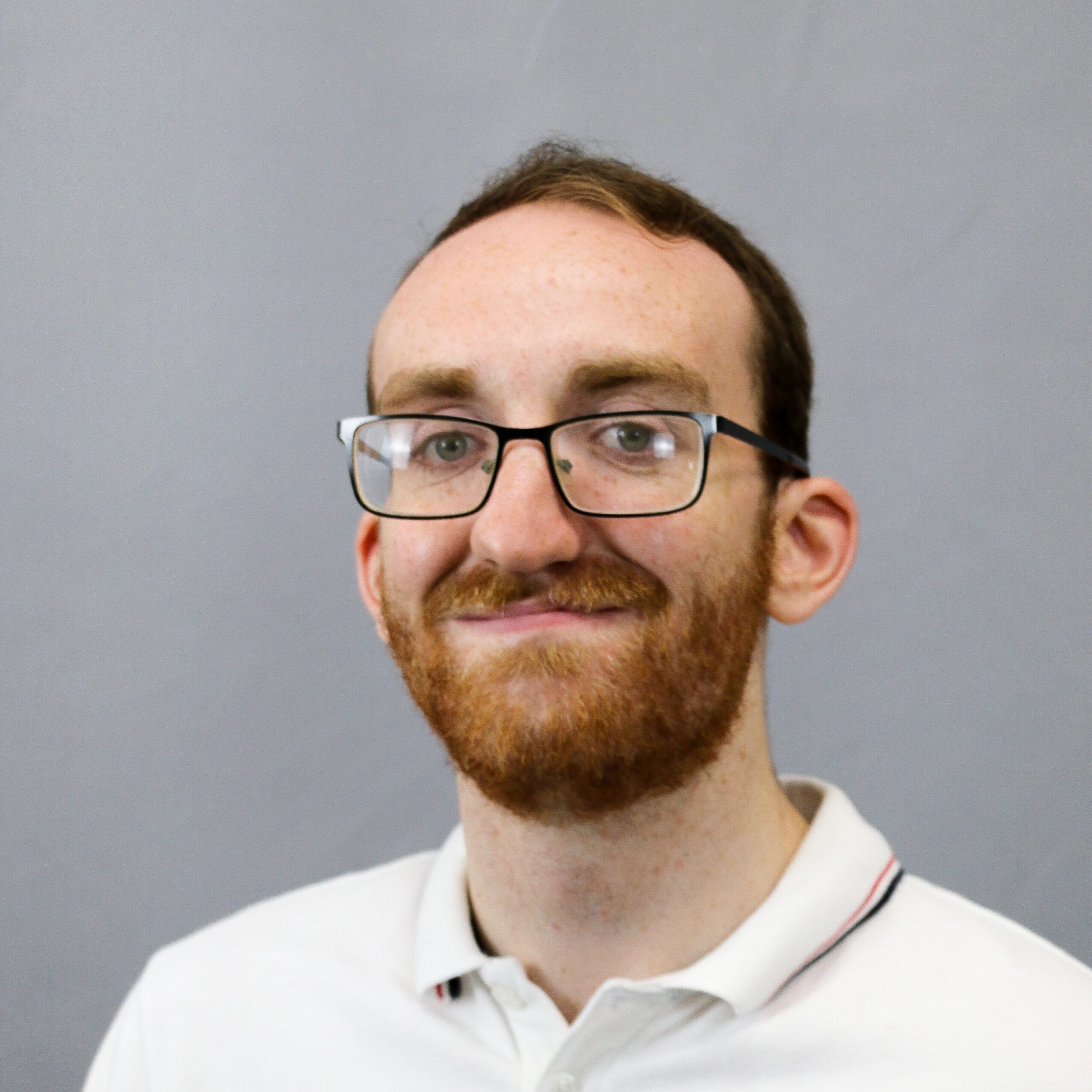
Content Creator, Belzona Polymerics Limited
Question,
I have a question on a 10 ‘ long cylinder that has a 7 7/8 bore . The ID of the cylinder is scarred and scratched up and I cannot see how far far it goes back from the end. Then you have the piston issue they will be sliding into it . On our discussion today, there was a discussion that Belzona could have a product to repair the 10’ long cylinder, instead of honing it setting it up in a lathe to get the dimensions correct. The piston would have to be machined also with new rings. The tolerance from cylinder n piston is only .005 to .015 . I was in a machine shop for over 40 years and each time we had to hone the cylinder. My question to you is , is there any other way to repair this using a product from Belzona . Someone said that they saw it done before , but I disagree . Mainly because keeping everything straight and in tolerance . What’s your opinion ?
Hello Todd, thank you for your comment. For more information about this solution and to receive a technical answer to your question, please use the following link to contact your local Distributor – https://belzona.com/en/about/disfinder.aspx. Best regards, Belzona Team.