In this post, we will take a look at how to repair pitting corrosion using Belzona’s epoxy solutions. Corrosion is the gradual destruction and degradation of materials through chemical and/or electrochemical reactions with their environment. There are several different types of corrosion that can occur and, in this post, we take a look at one specific type of corrosion – pitting corrosion – through two case studies from different industries. Corrosion is a dangerous and extremely costly problem across a wide range of industries. In the most serious of cases, it can cause buildings and bridges to collapse, oil pipelines to break and chemical plants to leak. So how do we repair pitting corrosion
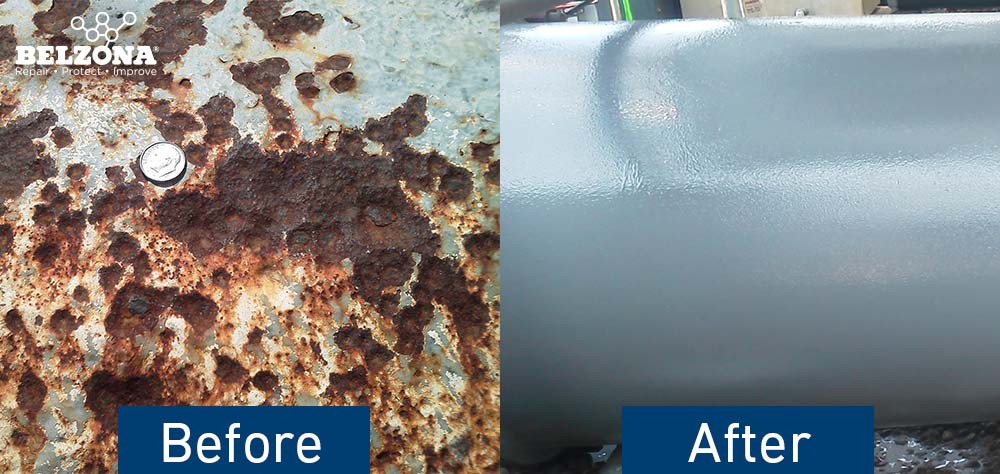
How to repair pitting corrosion (step by step)
- Surface Preparation
Brush away any loose contamination and clean the area with Belzona 9111 (Cleaner Degreaser) or any other effective cleaner which does not leave a residue. If applicable, use a flame to sweat out oils from permeated surfaces. Then, roughen the surface by blast cleaning, deeply scoring, or grinding and clean again.
- Mix your epoxy metal repair paste (Belzona 1111)
Transfer the entire contents of the Base and Solidifier modules onto the Belzona Working Surface. Mix thoroughly together to achieve a uniform material without streakiness
- Apply epoxy metal repair paste to the pitting corrosion
Apply the Belzona 1111 directly onto the prepared surface with the plastic applicator provided. Then, firmly press down to fill in all cracks, remove entrapped air, and ensure maximum contact with the surface. Finally, contour the Belzona 1111 to the correct profile or allow it to cure then machine it down (refer to the Belzona 1111 IFU for cure times).
- Cure and prepare Belzona 1111 for overcoating
Allow the Belzona 1111 to reach the “machining or light loading” level of cure. After this time, the surface must be roughened by abrading or grit blasting to achieve a surface profile of 40 microns before overcoating with Belzona 1321.
- Mix corrosion-resistant coating (Belzona 1321
Begin by combining the entire contents of the Solidifier can into the Base module. Mix thoroughly together to achieve a uniform material without streakiness.
- Apply corrosion-resistant overcoat (Belzona 1321)
Apply the Belzona 1321 directly onto the prepared surface with a stiff-bristled brush or the plastic applicator provided. As soon as the first coat is applied, apply a further coat of Belzona 1321 (refer to the Belzona 1321 IFU for coverage rates and cure times). Afterwards, visually inspect for pinholes and misses and immediately brush out where detected.
Below we take a look at a case study which demonstrates how not implementing a corrosion prevention solution resulted in severe pitting corrosion.
Severe pitting corrosion at a petrochemical plant
At a petrochemical plant in Southeast Texas, USA, multiple areas of carbon steel pipework were suffering from heavy corrosion which had resulted in major pitting.
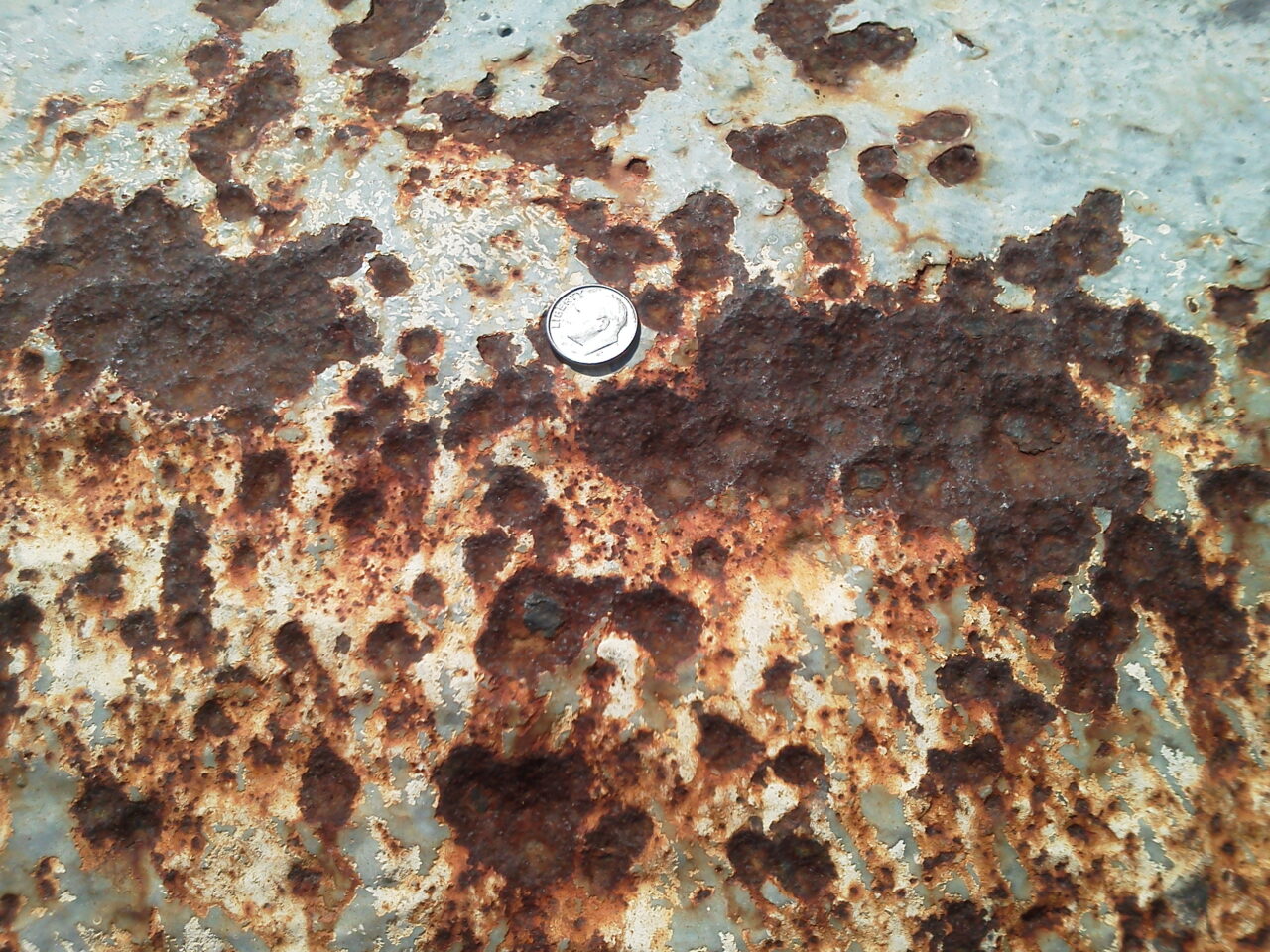
The severity of this pitting had caused the pipe walls to thin in many areas and completely through the wall in one spot, which resulted in a leak.
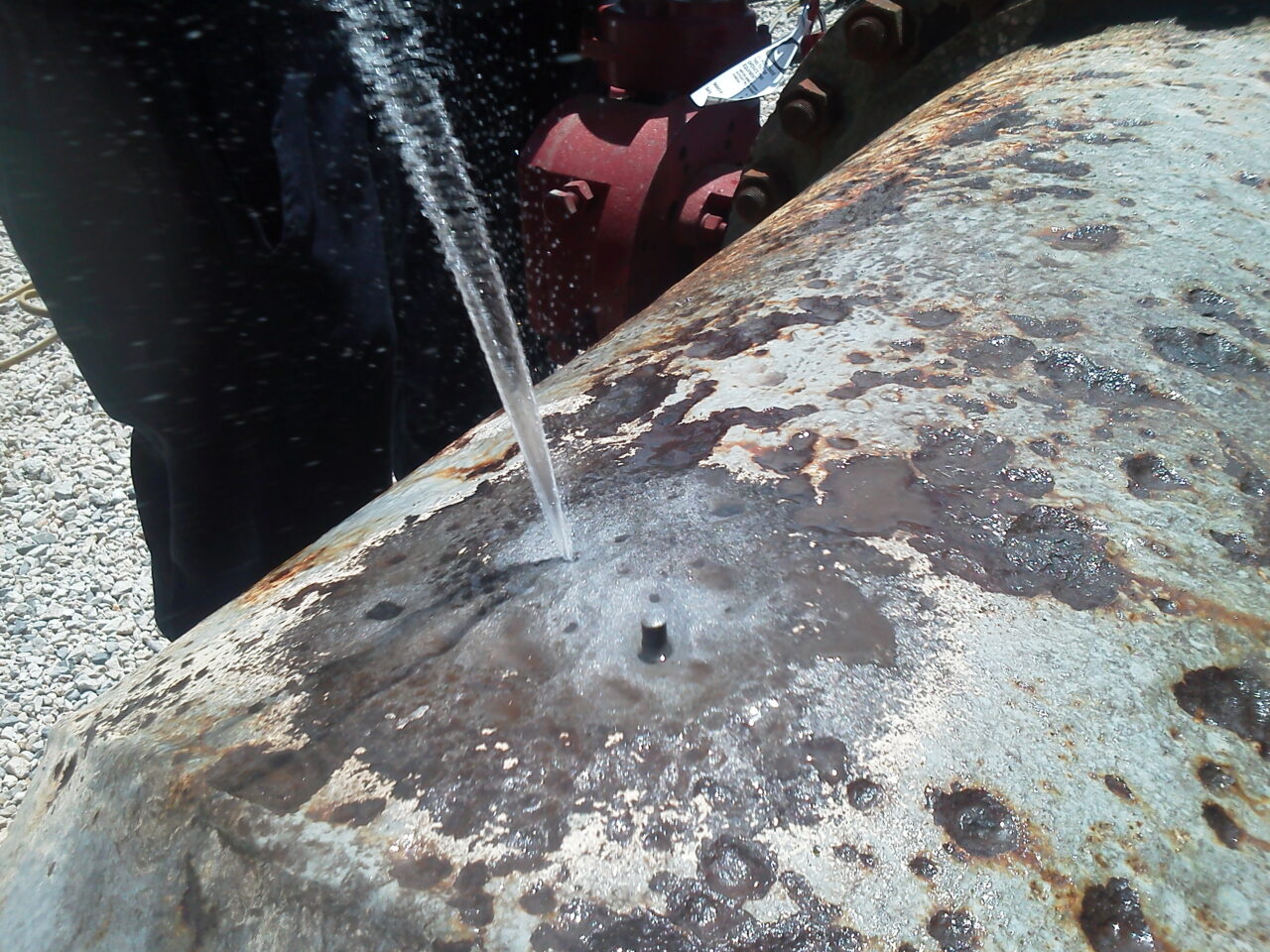
Firstly, a solution was needed to fix the live leak. A fast curing epoxy-based metal repair composite (Belzona 1211) was used to fix the live leak. This solution can be used for both permanent and emergency repairs, and cures at room temperature with no hot work involved.
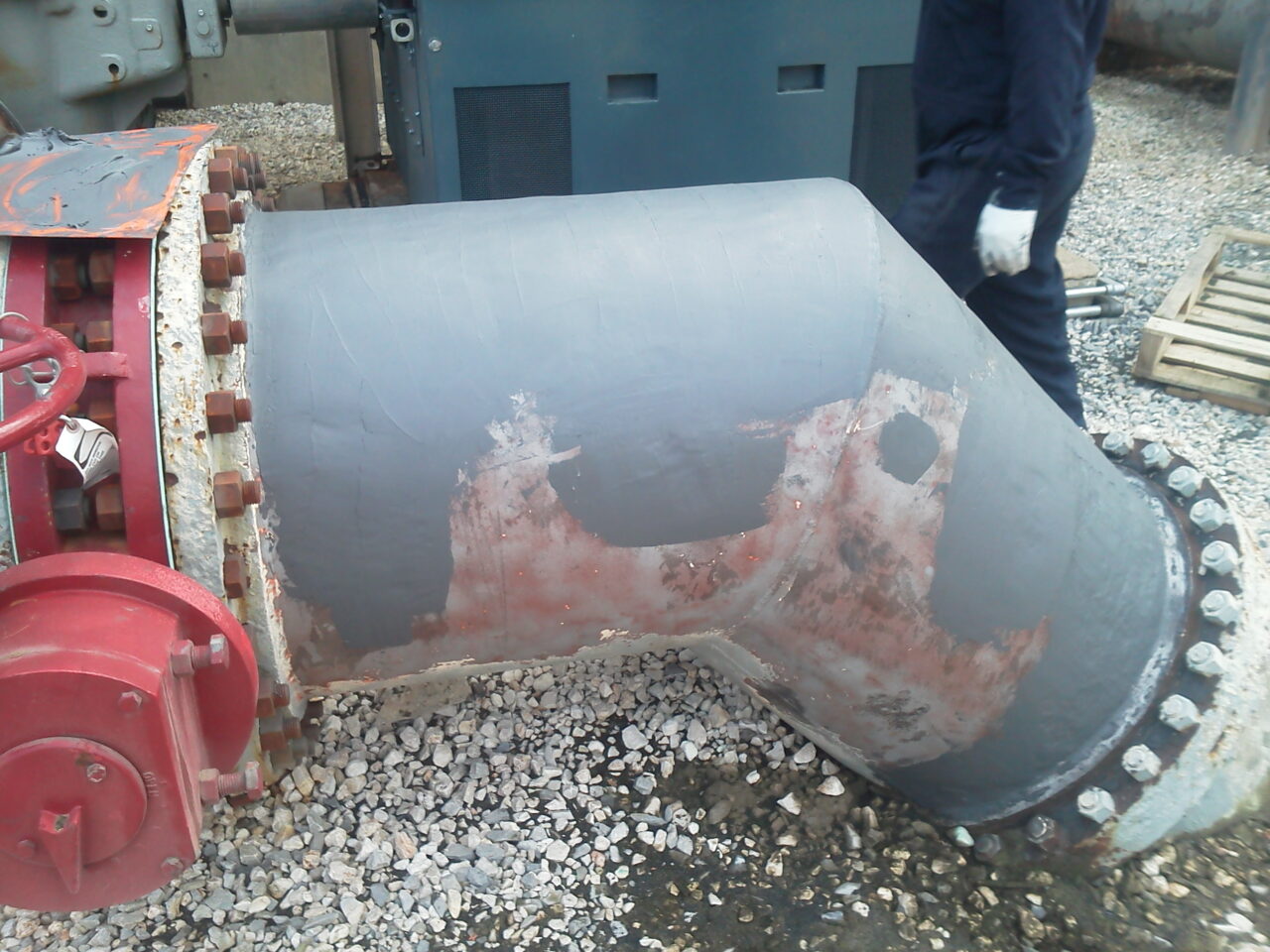
Once the live leak had been sealed, the heavy pitting on the pipes was filled with an epoxy-based composite (Belzona 1111). This solution cures at room temperature, so no hot work is involved, and also it offers reduced health and safety risks due to being solvent-free.
Find out more about this application, read the case study below:
Pitting corrosion and bi-metallic corrosion in the HVAC industry
Heat exchangers are commonplace in the Heating, Ventilation and Air Conditioning (HVAC) industry. They work by transferring heat from one place to another. Heat exchangers can be found in many different places, usually working to heat or cool buildings or helping engines and machines to work more efficiently.
In a facility in Ontario, Canada operating in the HVAC Industry, a heat exchanger (HEX) was suffering from pitting corrosion and bi-metallic corrosion, which was resulting in leakage.
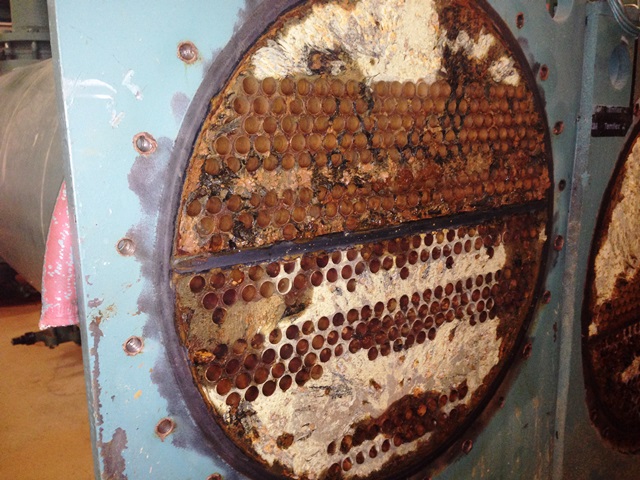
An epoxy-based composite for metal repair (Belzona 1111) was applied to the surfaces of the tube sheets and end covers to fill any pitting and damage. Next, a ceramic filled epoxy coating designed to provide erosion and corrosion resistance of metal surfaces (Belzona 1321), was applied to the surfaces using a brush. These non-metallic composite materials also stop the galvanic corrosion issues commonly seen in heat exchangers. Due to the solution chosen, the application was able to be carried out without the need for specialist tools.
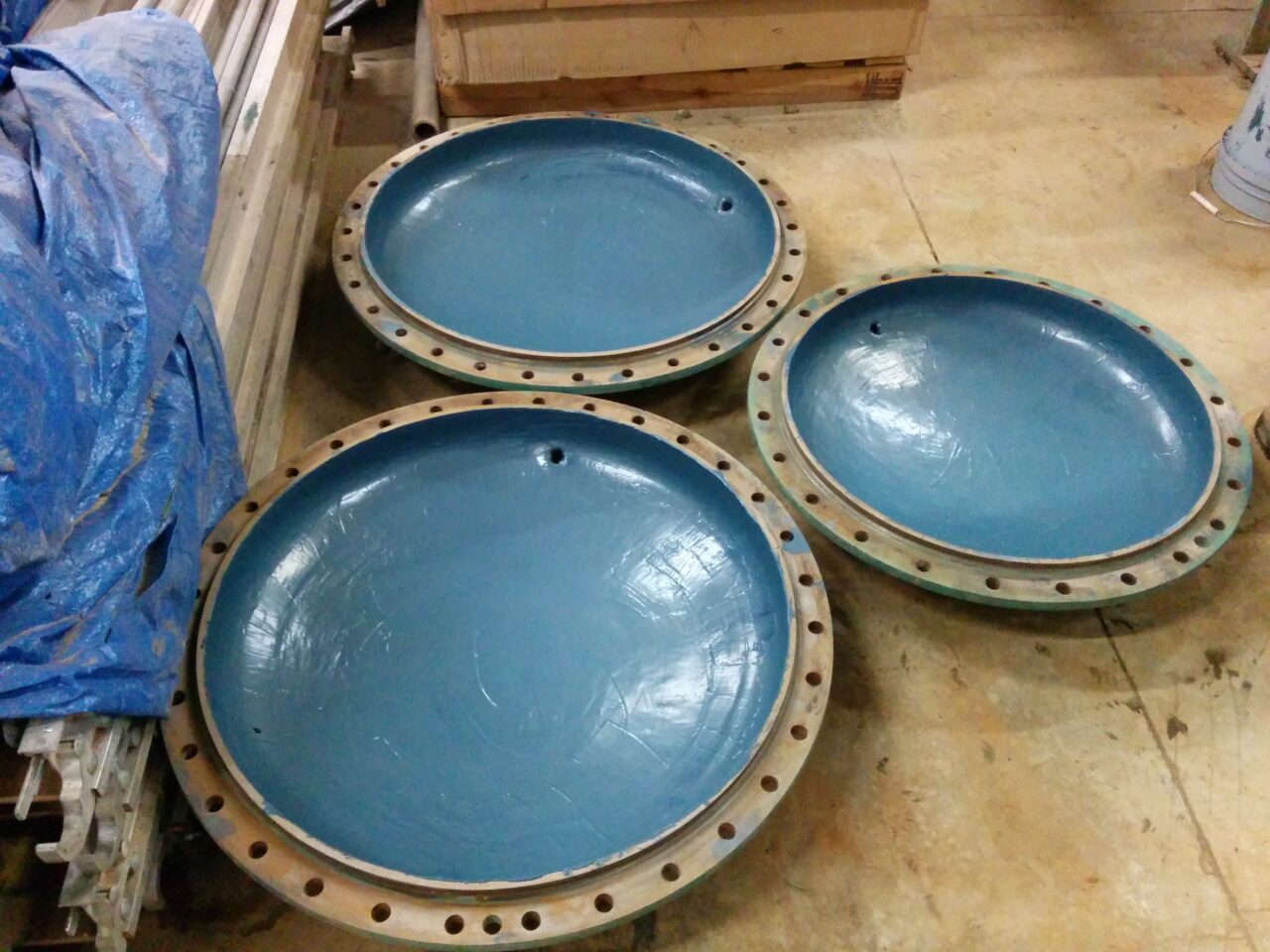
The multipurpose polymeric coating used in this application will protect the heat exchanger from bi-metallic and pitting corrosion, whilst also providing resistance to a wide range of chemicals.
Belzona’s epoxy solutions repair corroded metals and can also be used as a preventative measure to protect against future corrosion.
Good day, I have a consult about this application.
Is posibble to applicate this product in a surface with pittings of one tail shaft of one submarine unity?
Perhaps I wish you response this answer
Best Regards.
Hello Augusto, thank you for your comment. For more information about this solution, please use the following link to contact your local Distributor – https://belzona.com/en/about/disfinder.aspx. Best regards, Belzona Team.