This is a transcript of the Belzona “Solve it Session” webinar – Understanding the Challenges of Mitigating Abrasion and Wear. You can watch the webinar recording below:
Introducing Abrasion
Abrasion is one of the most common forms of wear. It is ultimately a process, one which cannot be completely stopped. Everything will wear down with time, but there are methods to slow this process enough to allow equipment to maintain a good service life. But before we can talk about solutions, we need to understand the problem.
Abrasion is caused by foreign bodies moving over a surface. In most cases these are mineral particles, which can be harder or softer than the metal surface undergoing the abrasion wear.
There are many forms of abrasion, with many different names such as gouging, grinding and scratching. These names mainly describe the cause of the abrasion, and how the wear took place. Scratching abrasion could be due to small particles flowing through a pump; grinding abrasion could be a process involving particles under a compressive load.
Understanding Abrasion
There are many factors which affect the severity of abrasion. The abrasive media will have a huge effect; with the size, hardness and shape causing the rate of wear to vary massively.
These include:
- Media type – Is it a liquid or solid?
- Media size – Are we looking at small, fine particles or something much bigger?
- Is there any moisture involved? – A wet surface will generally degrade faster than a dry one.
- What temperature is the involved media? – A higher temperature will normally mean a more aggressive environment.
Once we have most of this information, we can begin to agree on a solution. However, the most important question of all isn’t on this list. In order to correctly specify a repair method for damaged equipment, we should know how long it has been in service. This gives an indication as to the relative aggression of the media involved.
If we have two systems (one which transports granite, and another which transports chalk) which would suffer from a greater amount of wear?
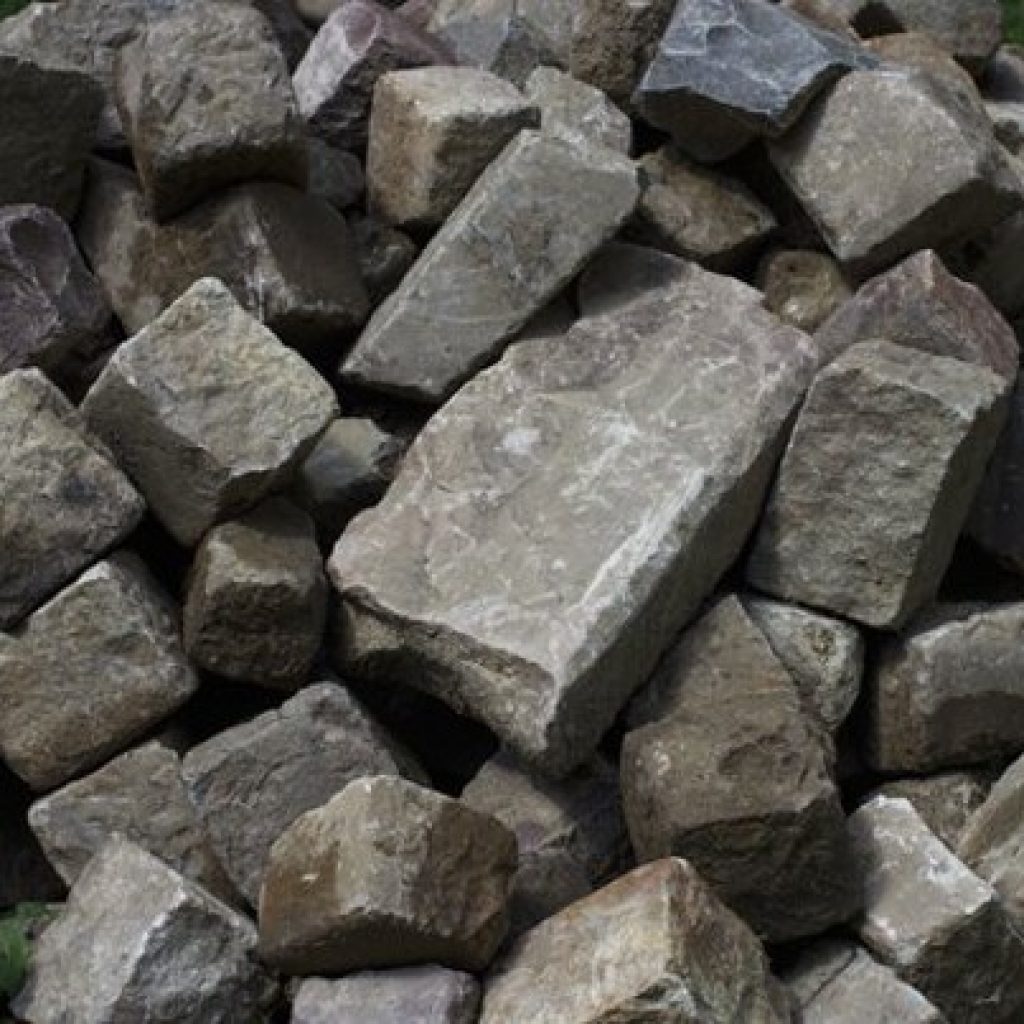
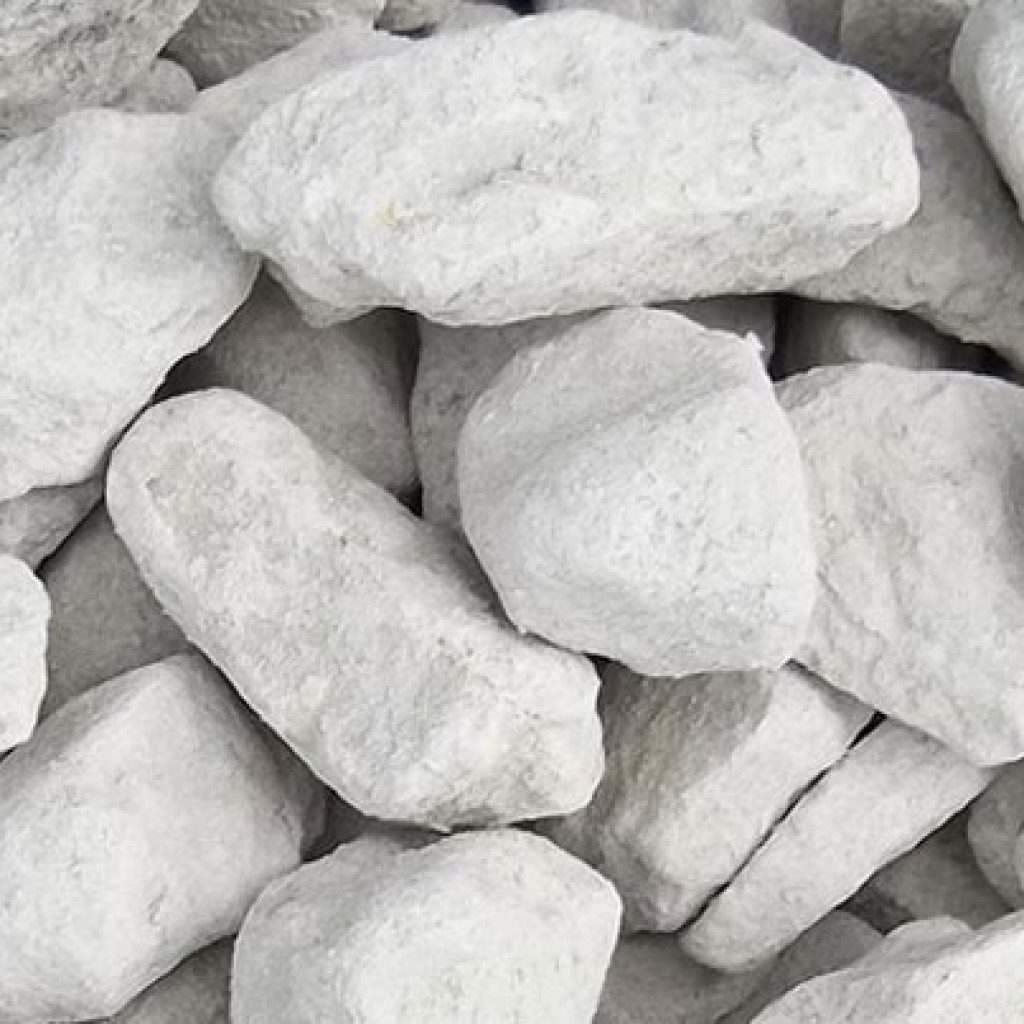
Many would suppose that granite is a harder material, so should cause more damage! Whilst this is true, we must remember all those other factors. What we don’t know about this hypothetical situation is the size, quantity, velocity or any other useful information about the process. Over time, chalk could quite easily cause a similar amount of damage to mechanical equipment. One of the biggest struggles for companies who specify repair and protection materials is having enough information to give a reliable solution. The more information we have, the easier it will be to specify!
Common Abrasive Environments
All equipment in contact with foreign bodies will be subjected to abrasion. Solids handling equipment primarily, including de-barkers, hoppers, screw conveyors, conveyor belts and drive rollers, are especially susceptible to abrasion and wear due to the nature of the materials they process.
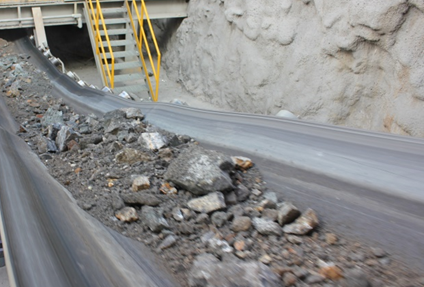
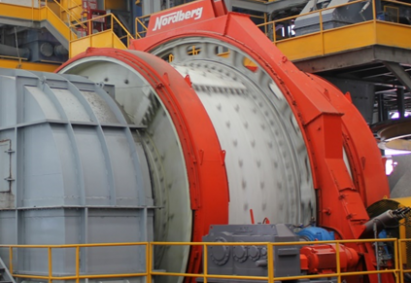
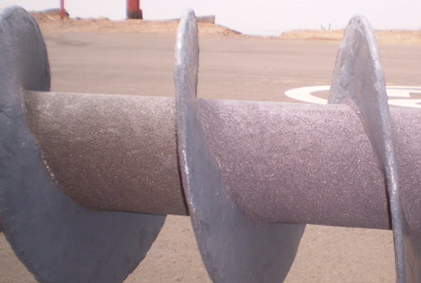
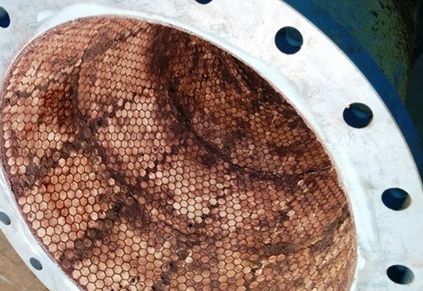
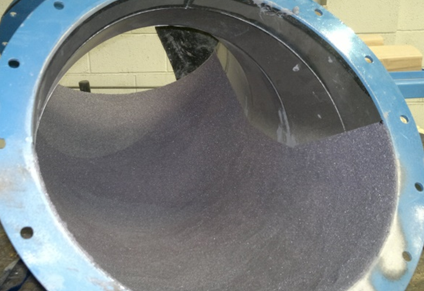
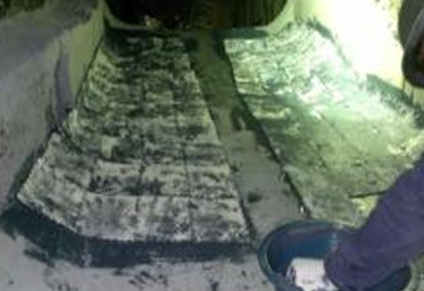
Solution Selection
Selection of the correct repair product is dependent on the type of abrasion which is occurring – specifically the angle that the wearing material has when impacting the substrate. This can be defined as the angle of incidence.
The different mechanisms of abrasion are divided into brittle and ductile behaviour. Ductile erosion deals with material removal due to cutting or ploughing via sliding abrasion. Here the angle of impact is typically less than 30° with respect to the target surface.
Brittle abrasion is material removal due to crack formation and wearing via impact. This tends to occur when the angle of impingement is perpendicular to the affected surface, so closer to 90°.
VIDEO: HOW TO CREATE ABRASION-RESISTANT SYSTEM WITH BELZONA
Protection of Screw Conveyor Against Abrasion
In this application, the screw conveyor at a water treatment plant in Romania was suffering from significant metal loss. As part of its operation in a treatment plant’s slurry clarifier, the screw conveyor was transporting dehydrated slurries. The hard particles in the slurry were causing abrasion of the conveyor blades.
Due to the particles being incredibly small, Belzona 1812 was specified as it can deal with finer materials. The blades were prepared and coated in accordance with the instructions, and this allowed the conveyor to continue operating in such a harsh environment, with minimal wear to the base material of the blades.
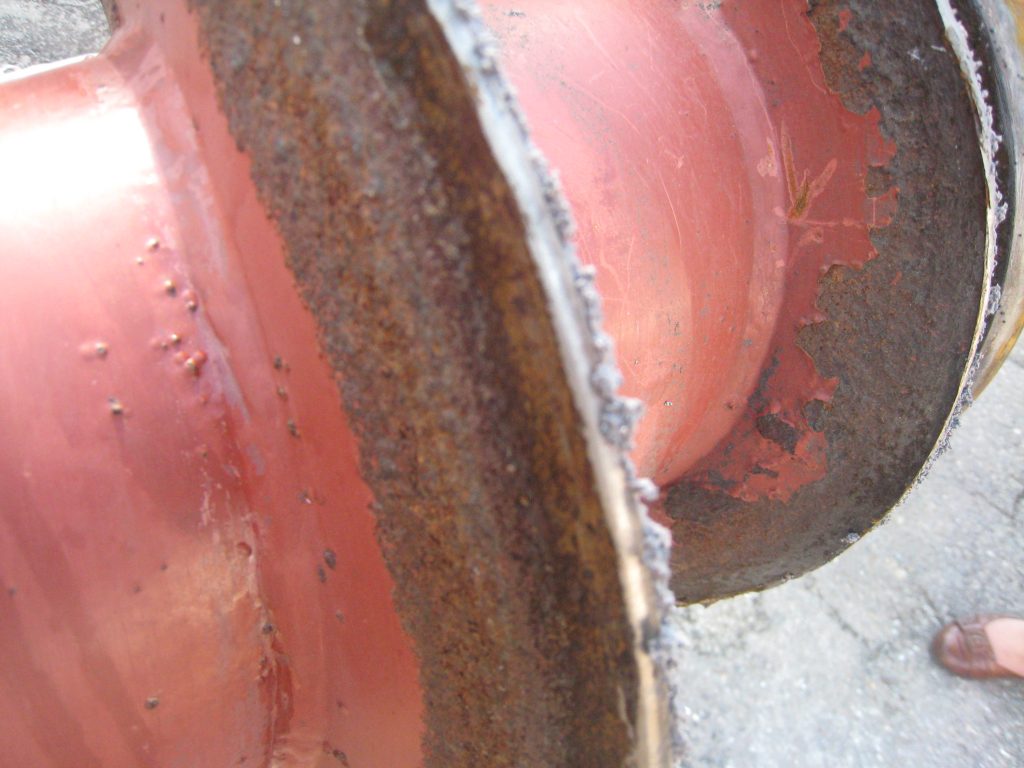
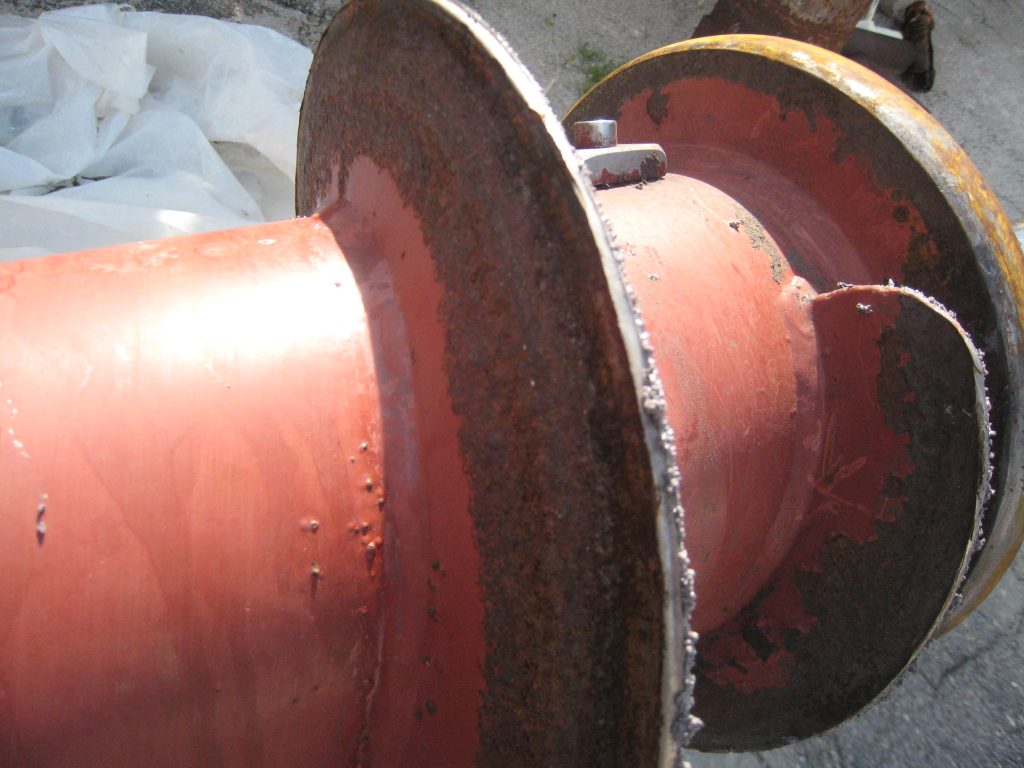
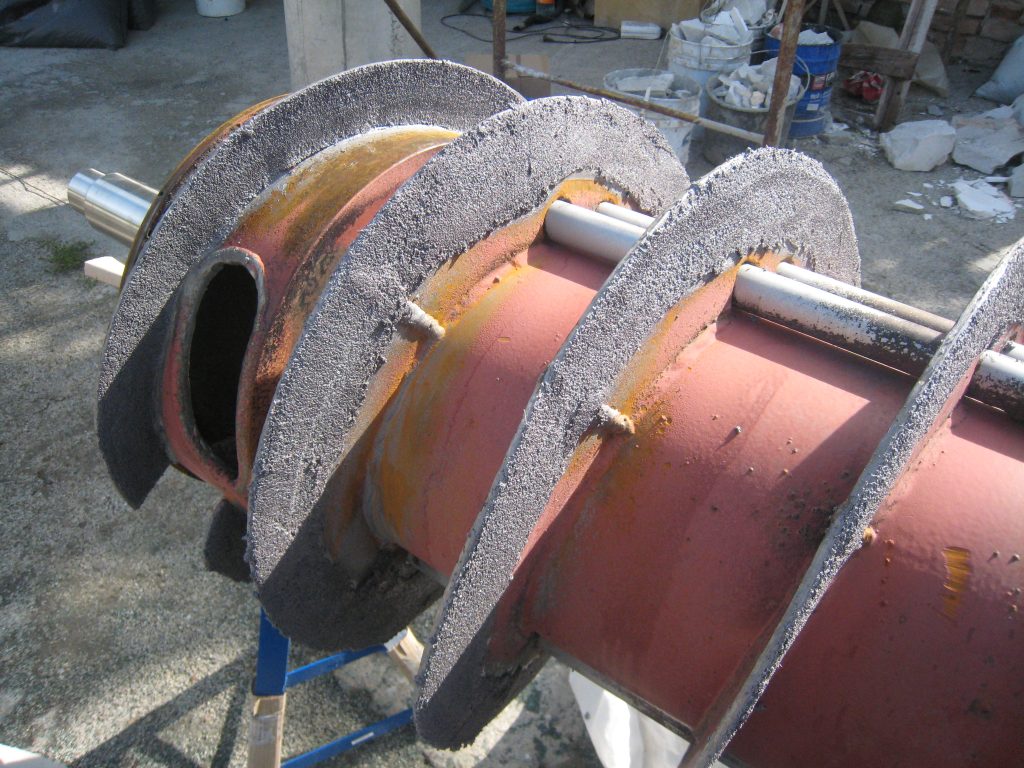
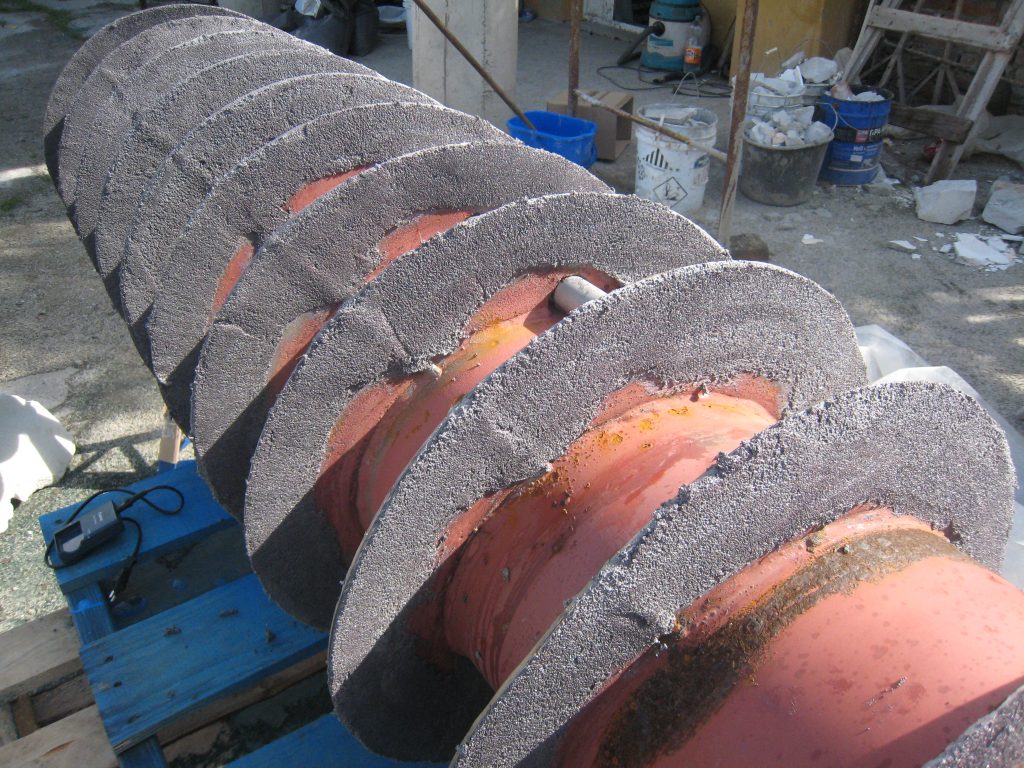
Protection of Mixer Blades From Abrasion
For this case study, we are looking back to September 2007. This was a crystallization tank in Kansas, and the mixer blades exhibited serious damage due to abrasion. This is part of a flue gas desulphurisation system, which is a key component in power plants all across the world.
The mix of abrasive media was enough to wear the edges of the blades down considerably.
The Belzona trained contractor mechanically prepared each blade prior to rebuilding to the original contour with Belzona 2111. Then, the blade circumferences were further protected with multiple coats of Belzona 2131. By choosing to repair the blades in-situ instead of replacement, tremendous financial savings were realized. This allowed the maintenance planners to have an additional budget to repair even more blades in an additive tank during the same scheduled outage.
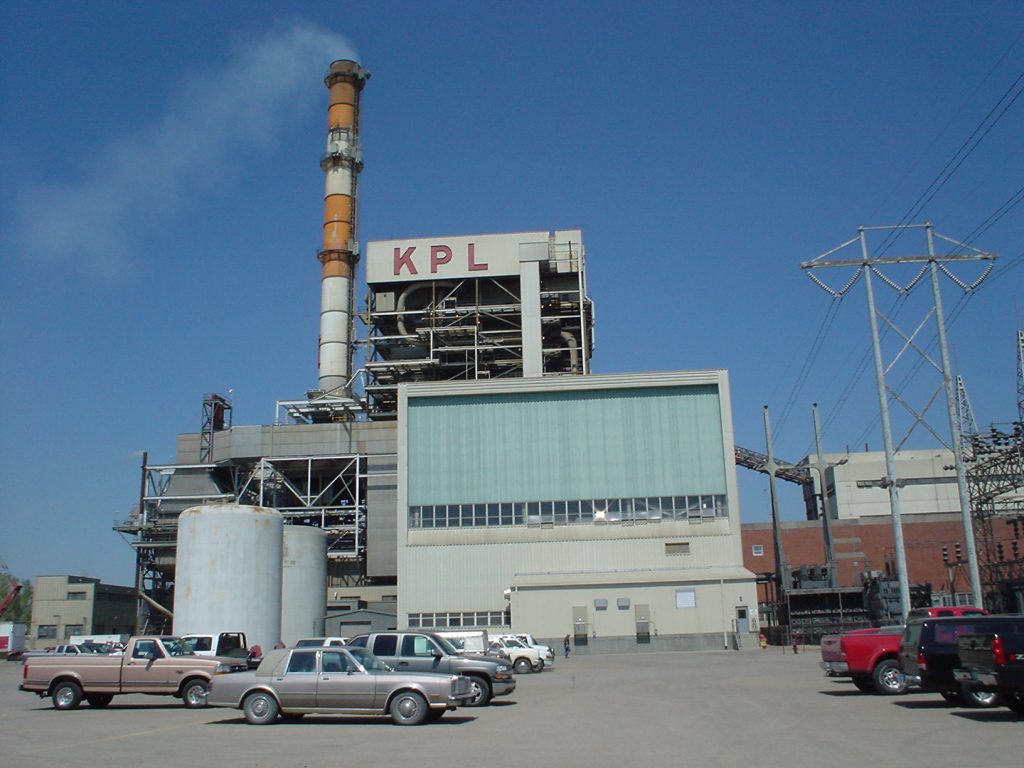
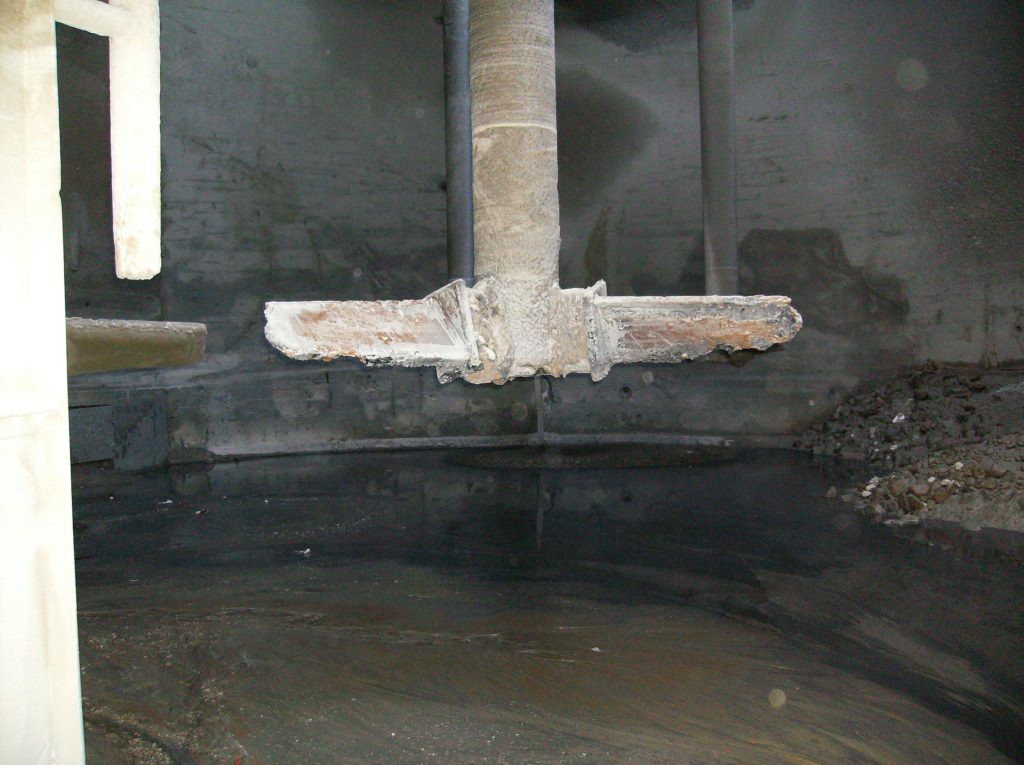
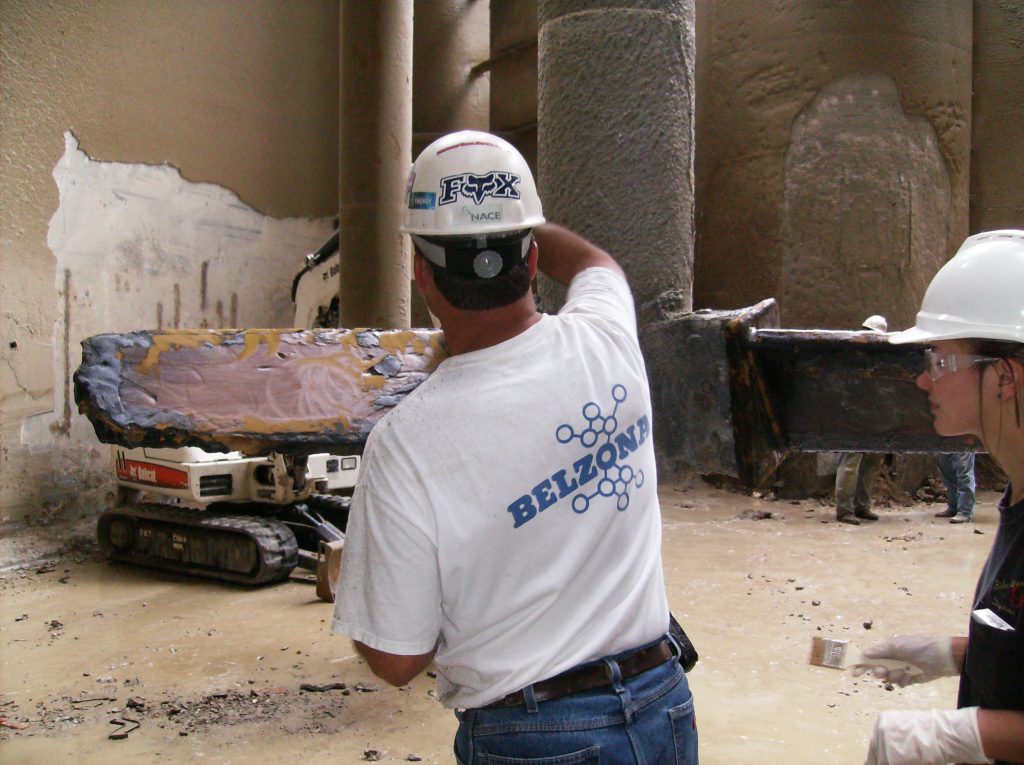
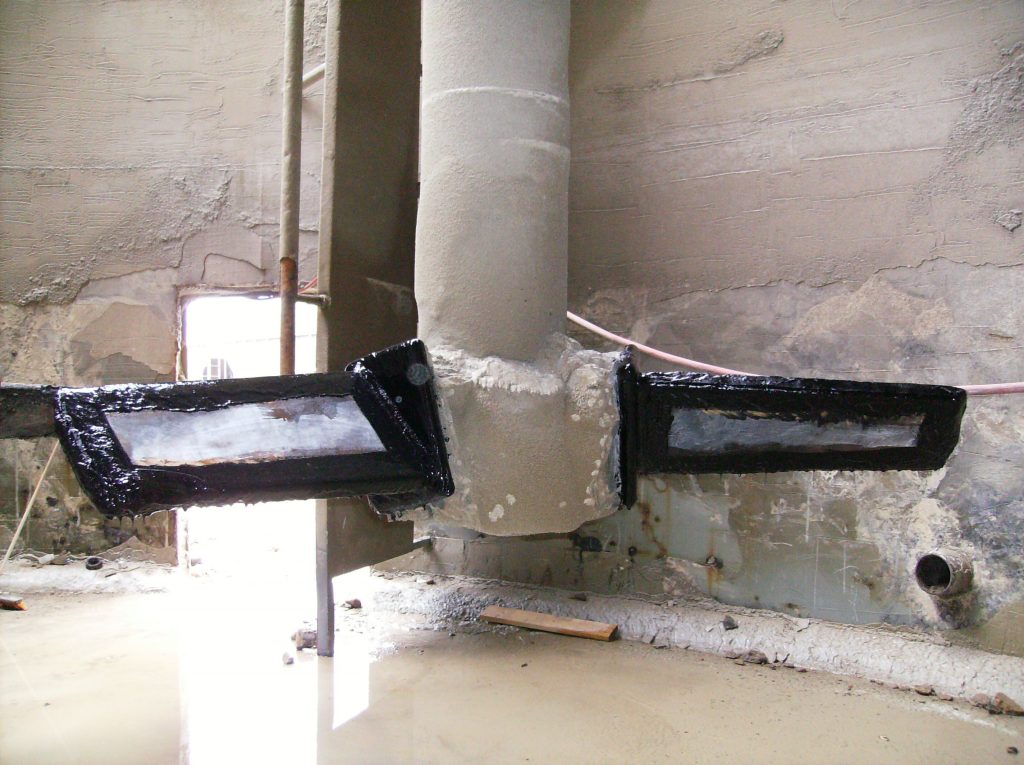
Protection of Hoppers from Dual-action Abrasion
A Manufacturer of asphalt shingles, Canada had hoppers that handle abrasive solid material in the production of asphalt shingles. The unloading of solids, composed of fine stone approximately 1/32″ diameter, was creating high abrasion on the inside surface of the hoppers. So here we are looking at a case of combination of brittle and ductile abrasion.
Belzona 1812 was applied to profile the hopper before overcoating with Belzona 2111. Both mild steel hopper and Belzona 1812 were grit blasted before coating.
- Hopper volume : 22.5 tons of material per hour 24 hours a day /7 days a week.
- Production shut down 40 days per year.
Originally the hopper had a life expectancy of 1 month. Other solutions lasted 7 months. With the Belzona solution, the equipment now operates for a period of 18 to 24 months maintenance free. They even carry 1 or 2 hoppers in stock. Client approved the Belzona 1812 as an inventory product and which is also used in other applications.
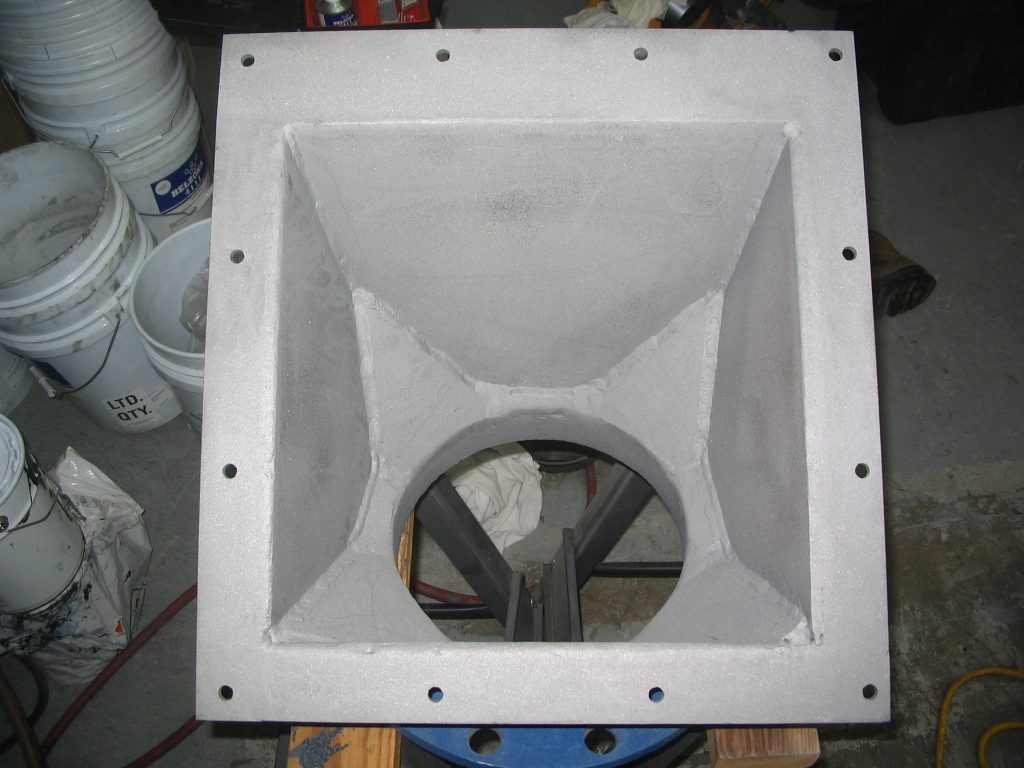
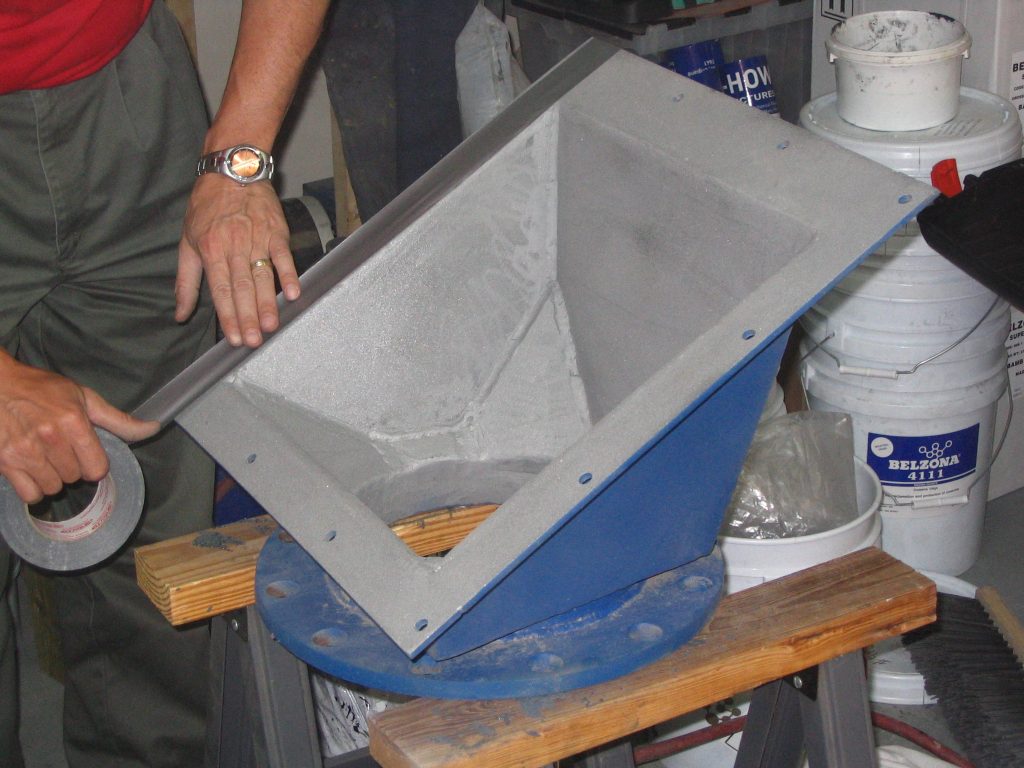
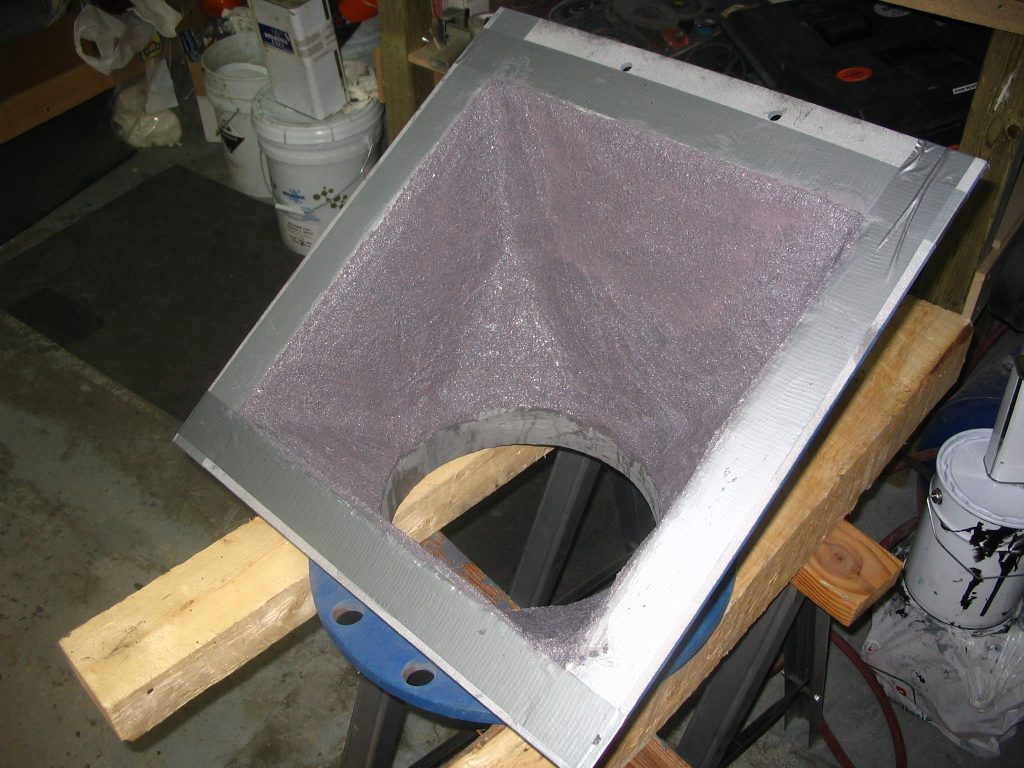
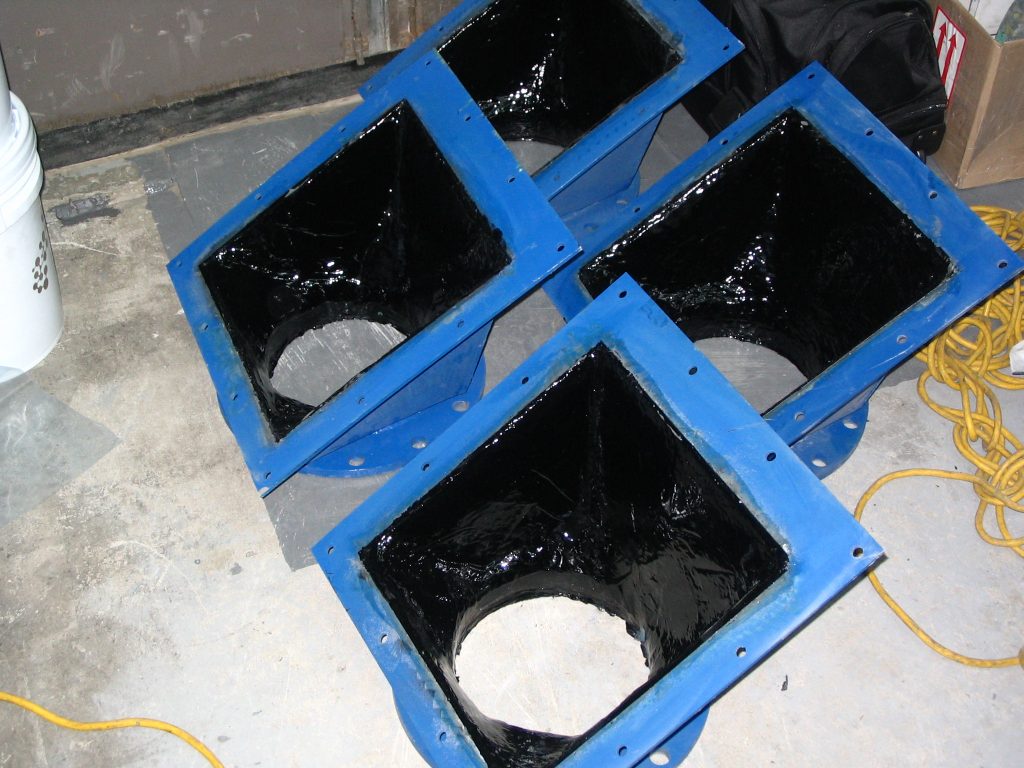
Testing of Abrasion Resistant Materials
There are numerous test methods available to determine this.
Some are standardised tests, such as the taber abrasion or slurry drum methods; whilst others are used to give an indication of performance in relation to real life situations, and these are usually much more aggressive.
The taber abrasion test involves two wheels which are run over the sample of material for a set period of time. The samples are weighed before and after the testing has been completed. The volume loss is then calculated in order to show the average amount lost for both a wet and dry sample.
The slurry abrasion testing is much more indicative of real life scenarios. Rods coated with the chosen material are inserted into a rotating drum, which is then set for a pre-determined period of time. The volume loss is measured and from this a determination of the abrasion resistance can be given.
All the test results can be found on the product specification sheets for each individual product.
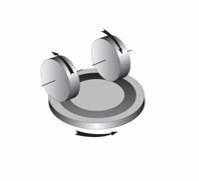
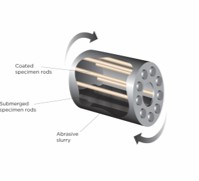
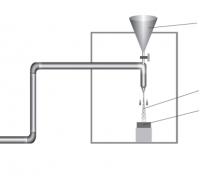
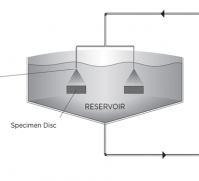
Alternatively, contact us to discuss your maintenance requirements.
WANT MORE INFORMATION?
Discover Belzona’s full range of abrasion resistant solutions.