Arguably, concrete is the most important building block of human history. Although the mix has evolved significantly to get to today’s typical formulation, its presence throughout time has brought us a wealth of architecture – from the Roman Colosseum to the Burj Khalifa. Going forward, the importance of this material and concrete repair is unlikely to diminish. It has 5000 years of history, but some predict it can last for up to 50,000 years.
However, that does not mean that concrete is without its flaws. This article summarizes some of its common failures, issues associated with like-for-like repairs and will explore some alternative technologies used to restore concrete.
Damage mechanisms affecting concrete
Concrete is highly water dependent to fully cure. However, in hot, dry or windy climates it can be difficult to maintain moisture levels. In these biomes, concrete dries out and is therefore likely to shrink and lose compressive strength.
Water
But too much water can be just as detrimental, as concrete is a porous surface. Although having high levels of absorption helps during the curing process and in maintaining concrete’s strength throughout its lifespan, in environments where the temperature drops below 0°C (32°F), freeze-thaw cycle damage can occur. Upon freezing, any absorbed water will expand by up to 9% , putting the concrete pores under stress. They can then rupture, causing it to crack.
Thermal contraction and expansion
Additionally, thermal contraction and expansion can affect the concrete’s volume. Although there are common solutions to compensate for volume change within concrete, such as expansion joints, these can be expensive to install, plus it adds another component which can potentially experience failure.
Low flexural strength
Beyond these factors, fully cured concrete can still experience damage due to mechanical faults. Despite its high compressive strength, concrete’s comparatively low flexural strength means that excessive loading often leads to cracking.
One method for allowing the concrete to bear a heavier load is to use reinforcement – steel rebar. Steel complements concrete’s compressive strength (as a more tensile construction material) and makes it more versatile and low cost. As well as this, the steel used for rebar does not readily corrode due to its natural passivating layer.
Carbonation
However, when reinforced concrete comes into contact with moisture, carbonation can occur, due to carbon dioxide reacting with the cement binder. Although concrete is a naturally alkaline material, the addition of moisture allows further CO2 to enter it, which lowers its pH over time. This in turn, makes it more acidic, negating the steel’s passivating layer and allowing it to corrode. Consequently, the rebar can distort or increase in volume, in turn causing it to crack and spall from the inside.
Aside from this, should the concrete be experiencing expansion or detraction anyway, steel structures restrain it, causing significant tensile stresses to occur and lead to cracking.
Problems of like-for-like repairs
With so many damage mechanisms affecting concrete, it is necessary to be able to easily restore it. One of the most popular methods to rebuild a degraded substrate is to use more concrete.
However, without addressing the root issue of the problem, the repair will still be vulnerable to the same damage.
Another issue with like-for-like repairs is that new concrete does not always adhere well to the original substrate. This is particularly the case in small repair areas, where the new concrete maybe thinly applied or a feather-edging technique used. Damage occurs at the weakest point – the bond between the existing substrate and the new concrete – meaning that, even if the original could bear it, a lesser amount of pressure could now result in failure.
Finally, one of the most critical characteristics of this material is that it requires many days to fully cure and achieve adequate strength. This may halt operations or result in having to close off areas for long periods of time.
Advantages and disadvantages of polymeric materials
An alternative concrete repair option, which can provide advantages throughout the lifecycle of the restoration, is to use polymeric composite materials. Manufacturers design them to provide a superior substitute to concrete in many ways and tackle some of the frequent issues associated with this material.
Polymeric materials are designed to be easy to use by the customer. They can be simple to mix and often do not require specialist tools for application. Unlike typical concrete, polymeric materials provide excellent adhesion to any existing cementitious substrate. On average, concrete experiences 2 – 3 x 10-4 drying shrinkage , whereas polymeric materials (which increasingly do not incorporate solvents) experience little to none.
Additional notable advantages include:
- Cure time – polymeric materials can often experience foot traffic in a matter of hours, as opposed to concrete’s 28 days
- Porosity – certain polymeric materials are non-porous, which means that moisture cannot absorb into the material, resulting in freeze-thaw issues or carbonation
- Performance – polymeric materials provide high compressive and flexural strength meaning they are less likely to experience the same excessive loading damage mechanisms as concrete
However, the cost of these materials is often notably higher than that of concrete’s. This is because in part, concrete is so readily available and cheap to produce. For those who don’t need specialist capabilities it performs a more than satisfactory job. Whereas researching, designing and producing specific polymeric materials results in a premium price for manufacturers. As well as this are the costs of manufacturing specialist products and distributing them around the world.
This often leaves Building Managers and Engineers with a difficult decision of how to repair larger areas of deteriorated concrete. If the substrate has already experienced damage, a concrete-based replacement may suffer from the same mechanisms, therefore not providing a long-lasting result. However, the high price of certain polymeric materials can result in them not being cost effective despite the repair being of a superior quality.
Is there an alternative solution?
To address this issue, manufacturers are increasingly producing polymeric formulations for the repair of large areas of damaged concrete and stonework. A new example of this is Belzona 4154 (Bulkfill Resin).This resin is easily combined with locally sourced aggregates to create a cost-effective system for large-scale concrete repairs. Examples of usage include:
- Repair large floor areas
- Horizontal surfaces to fill holes and cracks
- Raise and level uneven surfaces
- Vertical structures with the use of formers
Contractors can use this system with other materials such as Belzona 4111 and Belzona 4131. The combination of Belzona 4154 and an aggregate fills the void, before being over-coated with a thin layer of an additional material for added protection.The resin itself bonds exceptionally well to most surfaces including concrete, brick, marble and natural stone.
Example: Belzona 4154 Bulk Fill Solution for a Meat Freezer Concrete Floor
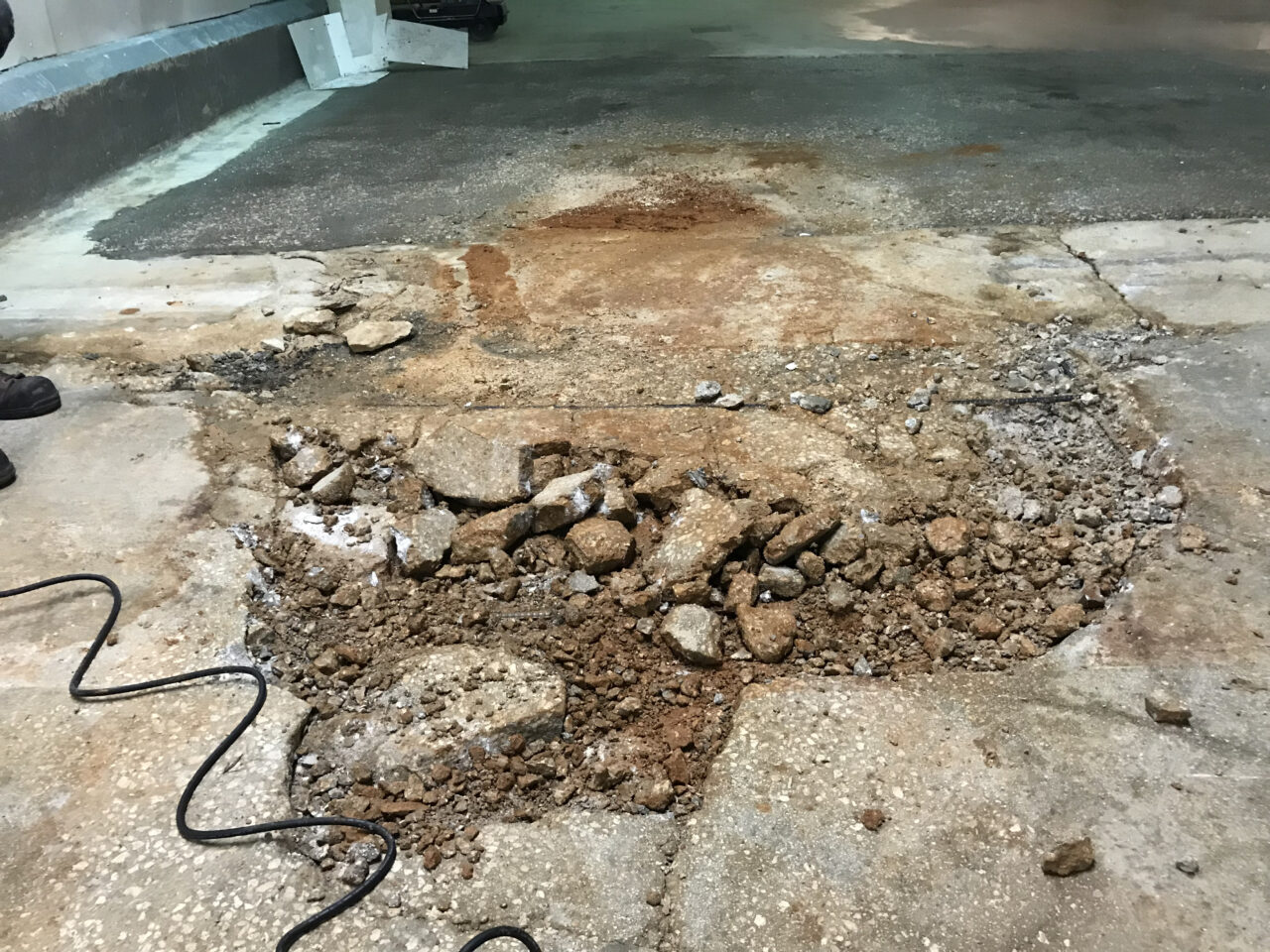
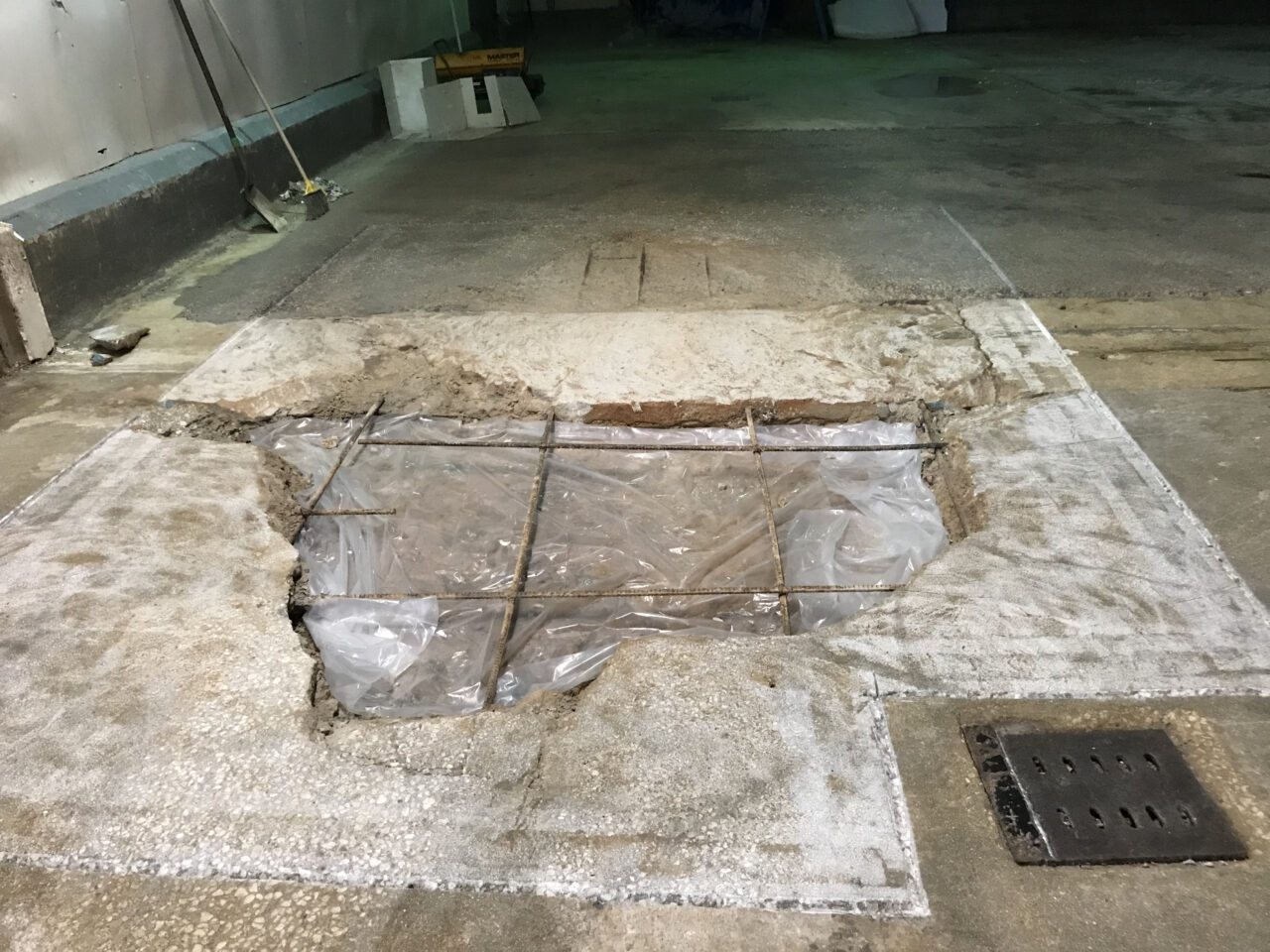

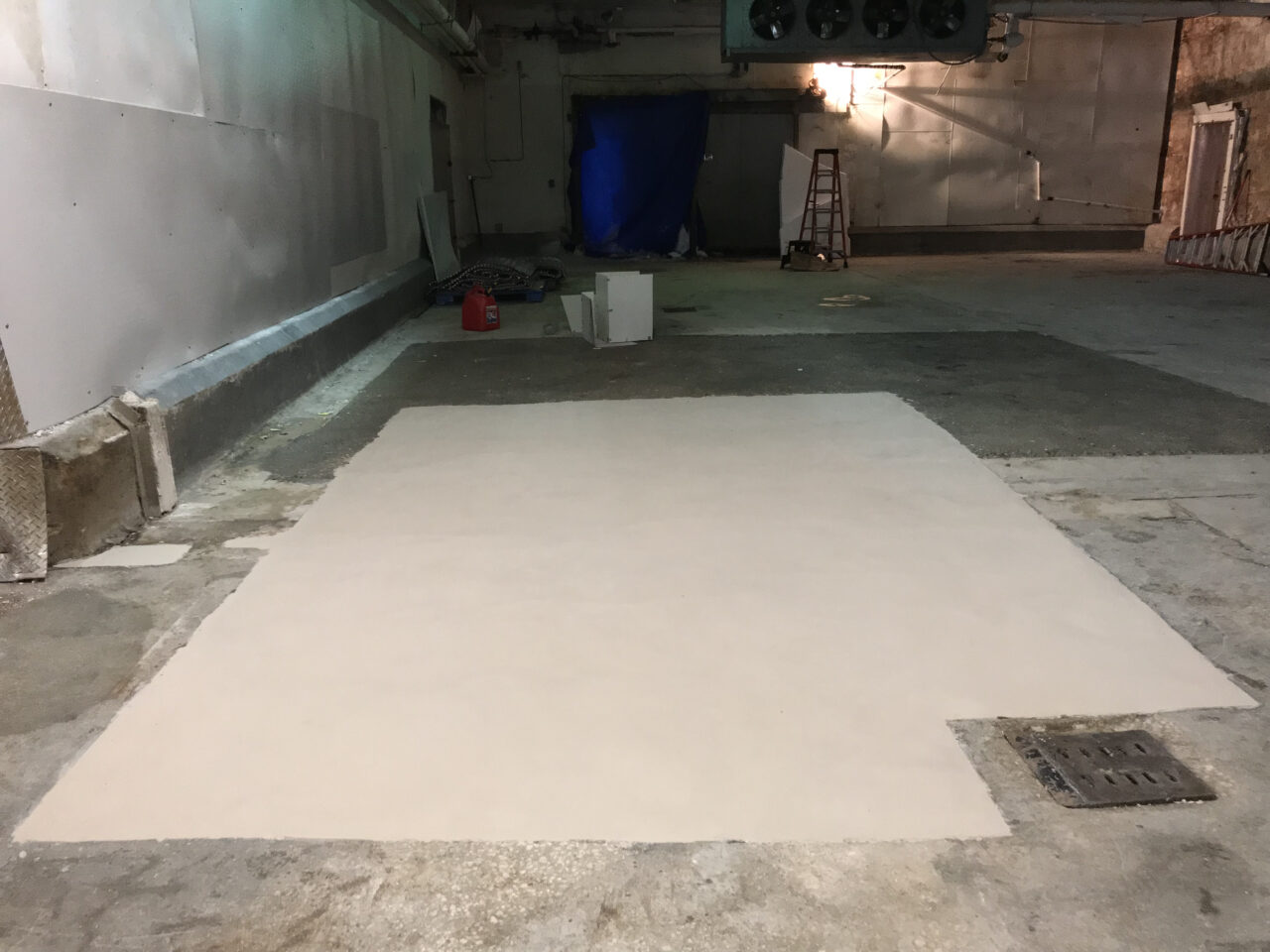
In order to measure the properties of Belzona 4154 in comparison to concrete, Belzona carried out a number of internal tests on them both. Belzona 4154 resin was mixed with kiln-dried sand before being put to the test.
Compressive Strength (ASTM D695) –
Cured concrete’s compressive strength varies from 3000-6000 psi (20-40MPa), depending on the aggregate used and overall mix. Belzona 4154 was tested in accordance with ASTM D695 to assess its compressive strength. After 24 hours at 22°C (72°F) it recorded 9500 psi (65.5 MPa) which rose to 13,000 psi (89.63 MPa) after seven days at the same temperature.
Flexural Strength (ASTM D790) –
Concrete’s flexural strength ranges between 400-700 psi (3-5MPa) whereas Belzona 4154’s is significantly higher, allowing it to bear heavier loads than traditional concrete. When tested in accordance to ASTM D790, the polymeric material recorded 7,500 psi (51.71 MPa) after 24 hours at 22°C (72°F) and 11,800 psi (81.36 MPa) after 7 days at 22°C (72°F).
Tensile Strength
In house testing using a hydraulic puller was used to evaluate the tensile strength of Belzona polymeric materials in comparison to concrete. The materials were bonded onto concrete cylinders and left to cure before being separated using a Clark Strong-Arm hydraulic puller. This resulted in pressure readings which were then converted into measurements of force. The maximum force recorded of a polymeric material was 50kN by the Belzona 4154 system, whereas, when the test was performed on concrete alone, the measurement was only 28kN.
Concrete repairs going forward
Concrete gained its reputation from hundreds of years’ worth of applications. Its popularity as a building and repair material is unlikely to diminish anytime soon. As well as this, concrete simply cannot be beaten in terms of price, often the most important factor in any business.
However, upon the degradation of concrete, the growing trend is for asset owners to invest once into an alternative repair method which can then be maintenance free for many years without suffering from the same damage mechanisms. Although there are many alternatives available at different price points, for larger areas of concrete it is often systems such as Belzona 4154 which are favored. Their effectiveness stems from both their cost and their long-term and durable performance, ultimately providing the best of both worlds.
To learn more about Belzona solutions for concrete surfaces and structures, read our previous post Concrete Solutions form Floor to Ceiling.
Yulia Burova, Marketing Director, Belzona Inc., Miami FL, USA
I appreciate how this article delves into the innovative solutions filling gaps in the concrete repair market.Thank you for sharing!!
I really appreciate that you shared this amazing post with us, thanks for sharing and keep up the amazing work.
I really appreciate that you shared this amazing post with us, thanks for sharing and keep up the amazing work.
Dear Barry,
Thank you for your feedback! We’re delighted to hear that you found the post informative.
Many thanks,
Belzona Team
Thank you for your feedback! We’re glad that you found the article informative.
– Belzona Marketing
Nice Blog!! The content you have shared is very elaborative and informative. Thanks a lot for sharing such a great piece of knowledge with us.