The polymer coatings industry is huge! In fact, I doubt if there is anyone who understands all the subtle differences of any one coating over another. However, if you are not a chemist working in the field of coatings formulation and like me, are merely specifying or applying coatings, the question is –
“Do you need to?”
Perhaps a better question would be –
“Are you aware of the different types and what it is about them that makes them fit for purpose?”
Throughout my working life my mantra has always been – keep it simple. Distil the important facts and you will have enough knowledge to hold confident discussion and make recommendations based on the expected service conditions that the chosen coating or lining will be exposed to.
So, what are the main facts that you need to be aware of? Let’s start at the very beginning…
The function of a binder in polymer coatings
The binder (or resin) is the main constituent of a coating or lining (product) and is the film-forming element of the product. It provides adhesion to a substrate, binds pigments and other additives together, and determines important properties such as durability, flexibility and hardness.
Most coatings available on the market today are known by the names of their binder resin and you will be aware of most of the well-known types such as:
Most coatings available on the market today are known by the names of their binder resin and you will be aware of most of the well-known types such as:
Epoxy
Polyester
Vinyl-ester
Acrylic
Poly Urea
Urethane
Alkyd
Ethyl Silicate
These are all binder resins and they all have very different physical properties some good some not so good dependent upon how they are applied, cured and what they are exposed to under in-service conditions.
In terms of the binder resin the most important factor, with regards to performance, is adhesion. As indicated above, the resin binder is responsible for other physical properties all of which are irrelevant if the product is not going to stay where it is applied.
SOLVENTS
The function of a solvent in a polymer coating
Solvents are used to liquify the binder resin, so that it can be applied in a thin film to the substrate. Once the coating has been applied, the solvent becomes completely redundant. The importance of the solvent other than liquification of the binder is related to the application method. Should it evaporate away too quickly, there would not be enough time to spread the coating to the correct thickness. Too slow and the cure time would increase to unacceptable lengths, resulting in an increased possibility of solvent entrapment within the cured coating.
Therefore, the evaporation rate of the solvent, known as volatility, is carefully chosen to match the application method. For example, slower evaporation for hand-applied coatings and fast evaporation for spray application.
Solvent volatility
Volatility of the solvent is usually compared against a standard solvent, normally N-Butyl Acetate, which is given an evaporation rate of 1. Solvents with evaporation rates higher than 1 evaporate faster and those less than 1 evaporate slower than N Butyl Acetate.
Solvents and the rate at which they leave the applied coating film have a marked effect on surface wet out and coating penetration, (of the surface profile), film levelling, flow rate, sagging and gloss.
The binder resin together with the liquifying solvent is know within the coatings industry as the Vehicle – into which the other constituents are added.
see more on Pigments , Additives & Filters
Mention pigments to anyone and they will immediately think colour, but the pigment added to provide colour is only one of the properties it can impart. There are many different pigments that can be added to a coating and they determine many different properties – not just colour.
Pigments are added to a coating to…
- Impart colour
- Protect the binder from weathering (UV exposure for example)
- Provide corrosion inhibition
- Control and reduce liquid permeation
- Provide a form of cathodic protection
- Modify mechanical or electrical properties
Pigments are largely solids (powder form) with particles of varying shape and size which remain as solid particles and do not dissolve in the vehicle.
- Improve stability (shelf life)
- Minimise settling (of the different components)
- Reduce foaming during mixing
- Improving the flow out and wetting
- Increase pot life
- Enhance UV resistance
- Increase or decrease gloss
Additives
Additives are most commonly liquid components added to the coating. Typically they are added in small amounts to perform a specific function such as:
Putting all of these components together in order to formulate a coating which will do what is expected of it is not an easy exercise. Imagine, all of the different binders, solvents, pigments and additives and the millions of different combinations that are possible!
Fillers
Fillers can be included to bulk out the final product and reduce costs, but many “functional fillers” are used to modify the rheology of the coating, (how it flows) and impart covering power, increase storage stability and modify application behavior.
Before we discuss the curing mechanisms of the major coating types it is perhaps prudent to eliminate a couple of misconceptions about coating cure.
Whether a coating is dry does not give a true indication of whether it has cured
Some coatings take longer to dry than others, but for full cure to be achieved it must also have developed the physical properties required to cope with the operating environment. Therefore, a generally accepted method of determining full cure of a coating would be to measure its hardness value.
Ambient temperature does not always increase cure speed
It is also a misconception that you can always decrease the cure time of a coating by increasing the ambient temperature to speed up the curing process. Whether this is possible or not is very dependent upon the type of coating and its curing mechanism.
Coating Types
The Key Differences between Polymer coatings
Generally, there are two distinct coating groups:
Inorganic – Coatings that are made using naturally occurring minerals but contain no carbon atoms.
Organic – These coatings, on the other hand, do contain carbon molecules and are generally formulated from ingredients that were once part of living organisms, plants, animal and vegetable oils.
The major difference between the two types is that inorganic coatings have a higher resistance to heat than organic coatings. But by no means is this the only difference.
However, regardless of whether a coating is organic or inorganic their curing chemistry is the same and would fall into two major categories.
- Non-Convertible coatings
- Convertible coatings
Non-Convertible Coatings Work
How Non-Convertible Coatings Work
Non-Convertible coatings are made from resins that are dissolved in solvents and cure or solidify once that solvent has evaporated. However, if exposed to that specific solvent or one with comparable solvency power, the cured coating will re-dissolve. In other words, the coating has not undergone any chemical change or conversion – simply the solvent evaporated and the applied film dried.
Since these types can be re-dissolved after full cure they are sometimes termed “Thermoplastic Coatings”. Typical examples of these coating types would be those based on Vinyl and Chlorinated rubber resins.
These types of coatings are extremely useful for maintenance applications as little surface preparation needs to be carried out. Essentially, the solvent attacks and softens the existing coating and ensures that the two layers fuse together. In effect, they cure as one thicker layer. Yet, these highly solvented coatings have fallen out of favour in most parts of the world as a consequence of the environmental damage from the volatile solvents.
There is a subclass of coatings which cure via evaporation known as Coalescent coatings. Here, the resin particles are usually dispersed in water (emulsion). As the water evaporates and dries, the particles of resin join (coalesce) to form the coating film.
Convertible Coatings
How Convertible Coatings Work
These coating types may be solvented or 100% solids and undergo a chemical change during cure, such that they cannot be re-dissolved afterwards. Consequently, they are sometimes called “Thermosetting Coatings”
These coatings cure by polymerisation and this process is induced by several different chemical reactions. However, the major curing mechanisms in this class of coating are:
- Co reaction
- Oxidation
- Hydration
- Fusion
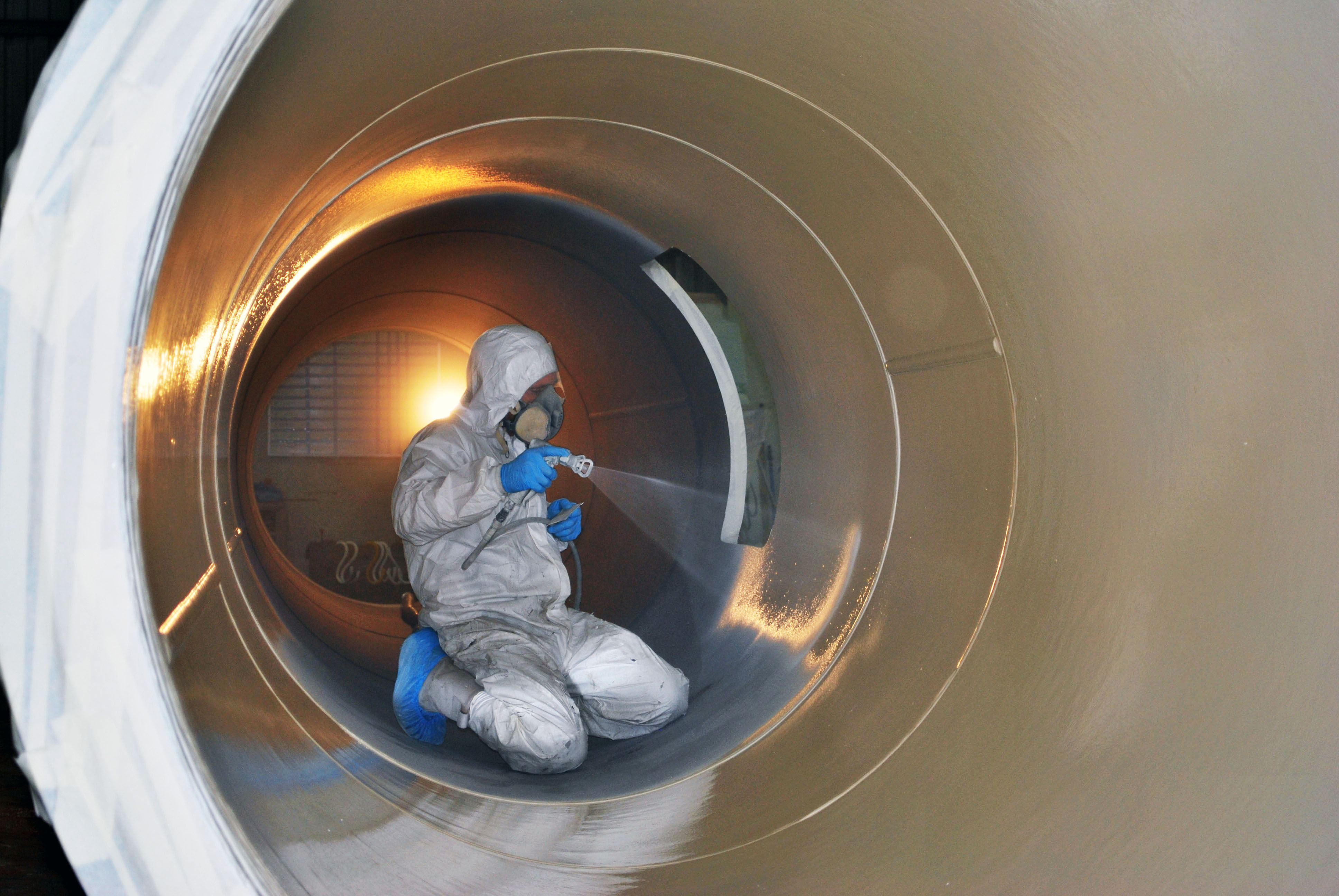
Co-Reaction
These coatings typically cure (polymerise) via a chemical reaction by at least two separate chemical groups. They are typically supplied in two separate containers known as a base and a hardener, solidifier or catalyst. Once these two components are mixed in the correct ratio the chemical reaction begins and heat is produced. This promotes the cross linking of the monomer molecules in the base material in order to produce the polymer. By modifying the chemistry of these types, they can be engineered to polymerise into either two or three-dimensional polymer matrices.
This form of polymerisation can be applied to many different chemistries such as: Epoxies, Polyurea’s, Polyaspartics, Urethanes and others.
Oxidation
These are coatings that cure by reaction with oxygen from the air. However, this reaction does not begin in earnest until any solvents have evaporated, leaving the coating film behind. Because the reaction itself is a surface effect it should be noted that these types of coatings cannot be applied in very thick layers or the surface will be fully cured and prevent oxygen from reaching the liquid coating below
I am sure that you have all applied one of these coatings in your home, only to find that a thick skin has formed with still liquid beneath? So, if your coating has wrinkled on the surface it is a sure sign of over thickness during application.
These types of coating are based on modified oils (vegetable or fish oil) an example of which would be an Alkyd. They should not be used in immersed service and should also not be used in alkaline conditions. In alkaline conditions a saponification reaction takes place; (the coating bond layer is turned into soap). How many times have you walked past galvanised street furniture where the paint system is peeling off? This is a prime example of saponification due to a reaction between the drying oil used in the coating and the galvanised, alkaline, substrate.
Hydration
Hydration cured coatings require some quantity of moisture to achieve their full cure. This level of moisture varies with coating type but without it, no cure would take place. Examples of this type of coating would be a moisture-cured Polyurethane or an inorganic zinc rich coating based on ethyl silicate resin. Even concrete cures in this way but generally requires much more water than “conventional coatings”.
Fusion
Finally, the fusion-cured coatings are generally baked in heat ovens to obtain full cure. Typical examples would be Fusion-Bonded Epoxies, Enamels, Polyethylene, and thermal sprayed metals. They can be single or two component but require a particular temperature regime which must be carefully monitored to ensure full cure.
Henry Smith
Senior Technical Service Engineer
Belzona Polymerics Ltd