Challenges in Containment Areas
Concrete is commonly used to construct containment areas and bunds in various industries. These structures are essential for containing chemical spills, recovering products, and protecting the environment. However, concrete is porous and vulnerable to cracking, corrosion, and chemical attack, especially without proper protection.
Even with bunds in place, leaks can still contaminate surrounding areas and groundwater. Thermal expansion and contraction also contribute to structural issues if not properly accounted for with expansion joints.
To address these challenges, asset owners often rely on containment area protective coatings. Belzona offers tailored solutions for chemical resistance coatings: Belzona 4361 provides high chemical resistance and flexibility, Belzona 5811 (Immersion Grade) is ideal for general protection, and Belzona 5815 offers a cost-effective, flexible solution for less aggressive environments.
Belzona Coatings for Containment Areas
Belzona 4361
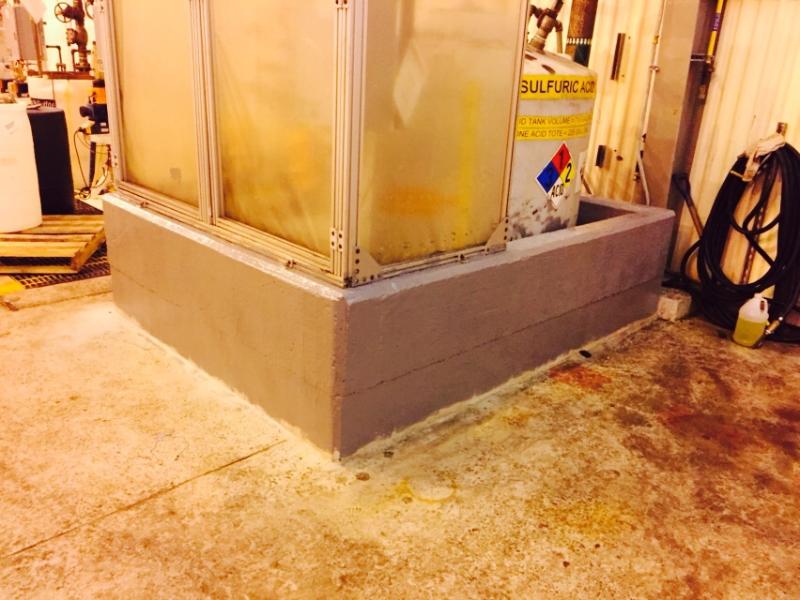
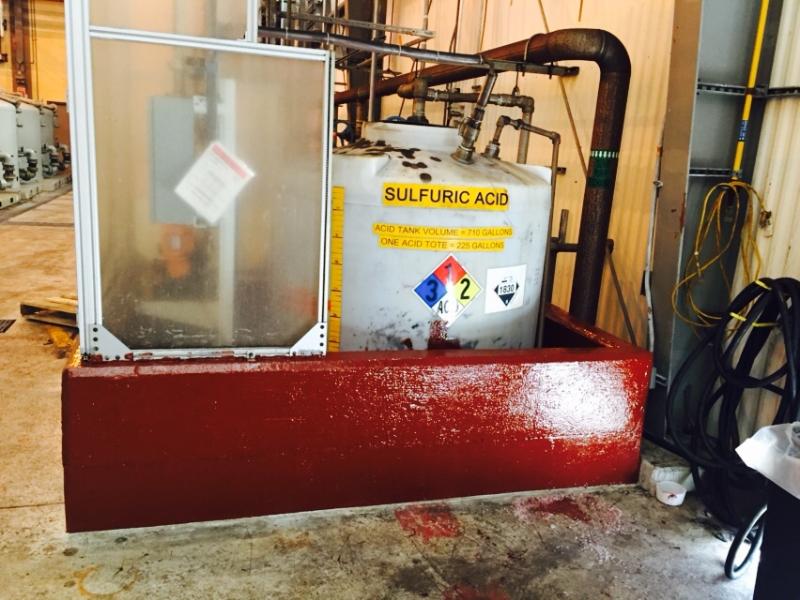
Belzona 4361 is a flexible coating for the long-term protection of chemical containment areas from harsh chemical attacks. The product adapts to the movement or cracking in the material beneath without deteriorating; the crack-bridging technology safeguards against any loss of containment.
Belzona 5811 (Immersion Grade)
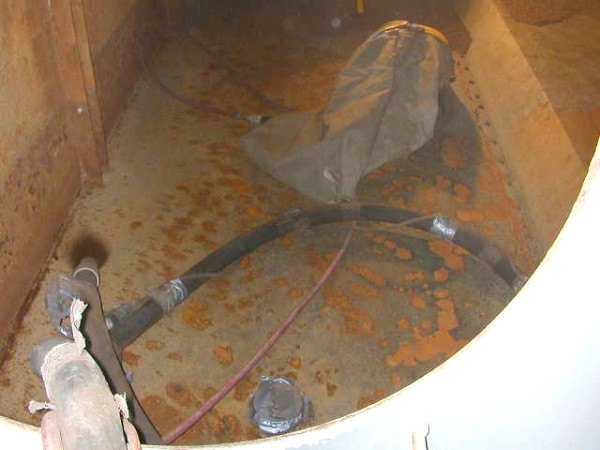
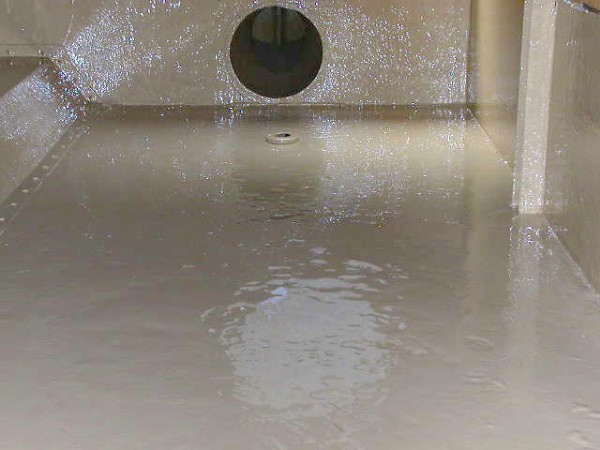
Belzona 5811 (Immersion Grade) stands out among the other containment area coatings because it is engineered to provide chemical resistance (saltwater, acids, alkalis, alcohol, hydrocarbons, etc.) and protect assets operating under immersion in aqueous solutions. The coating can endure temperatures up to 122°F (50°C) in continuous immersion to protect assets from corrosion.
Belzona 5815
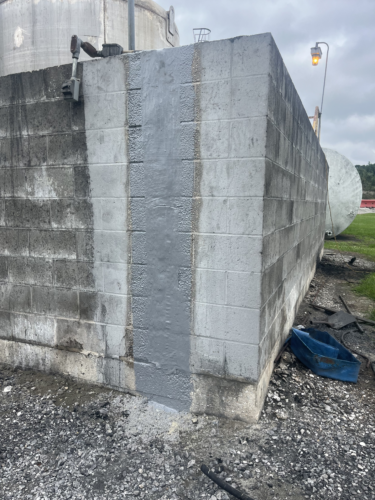
Belzona 5815 is a concrete protection coating system designed for protecting non-metallic and metallic surfaces. This barrier coating provides a cost-effective solution for substrates exposed to short-term chemical immersion or accidental spillages. Being a flexible coating, Belzona 5815 can accommodate anticipated movement in building materials such as concrete and carbon steel.
Belzona 5815 Application Process
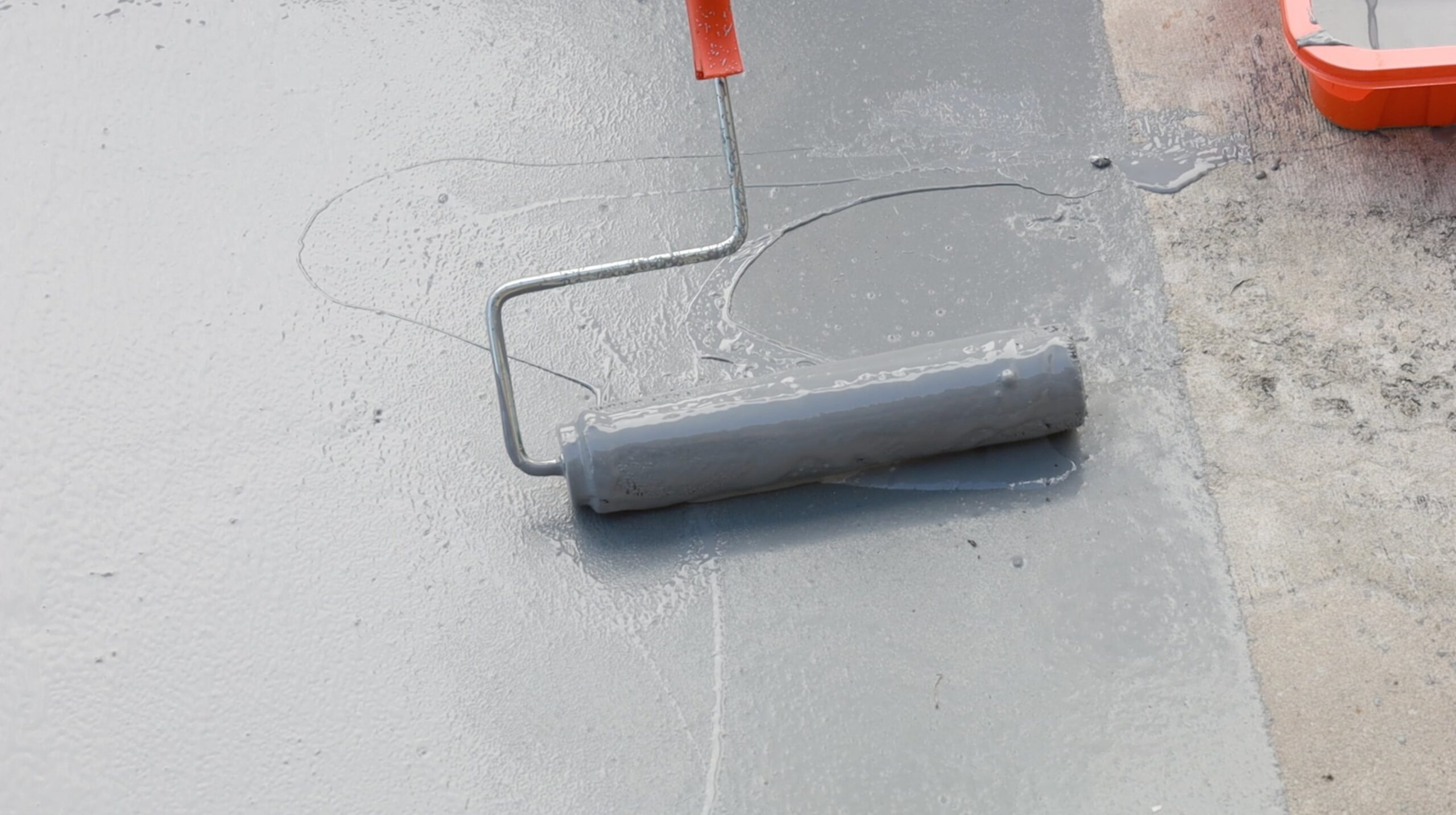
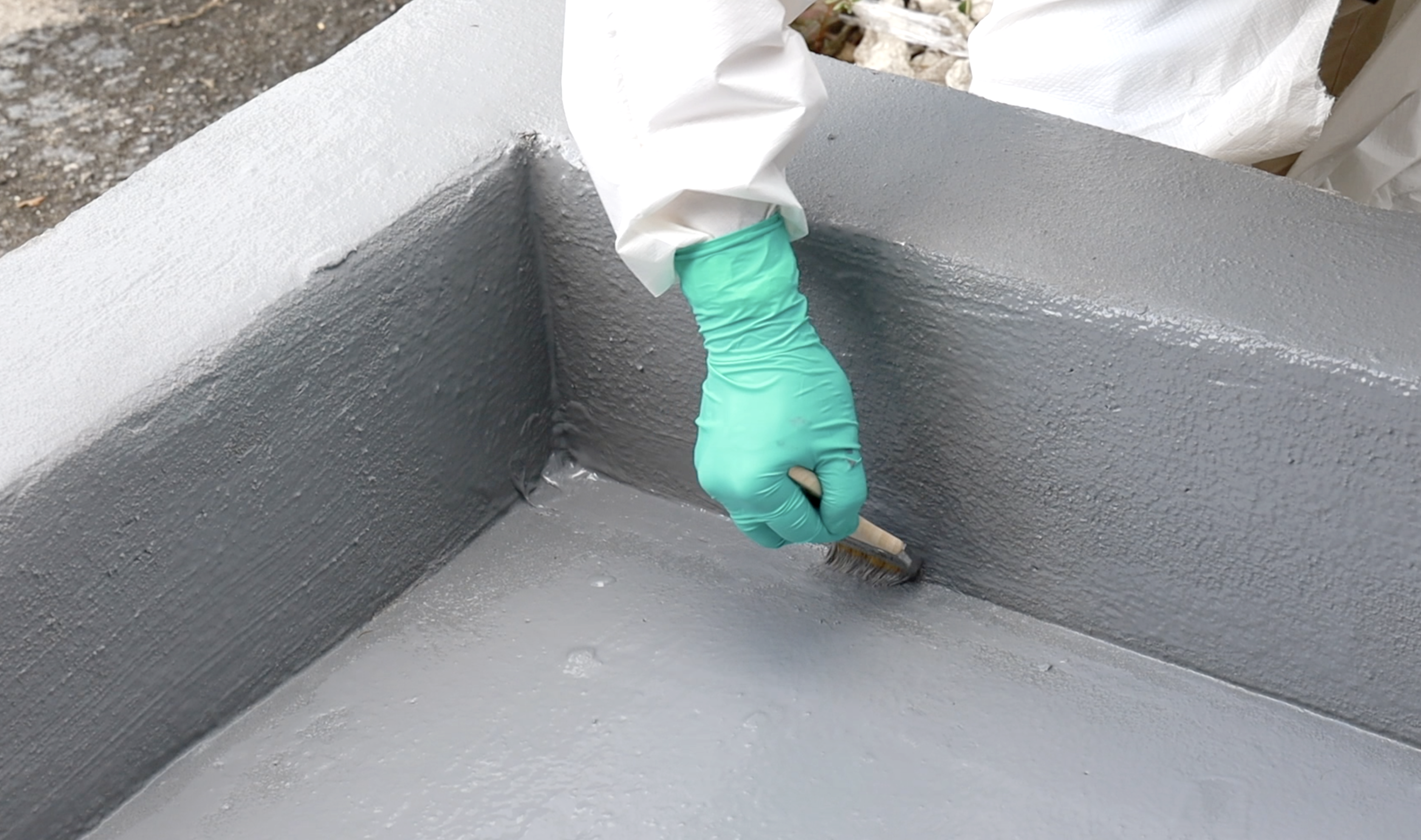
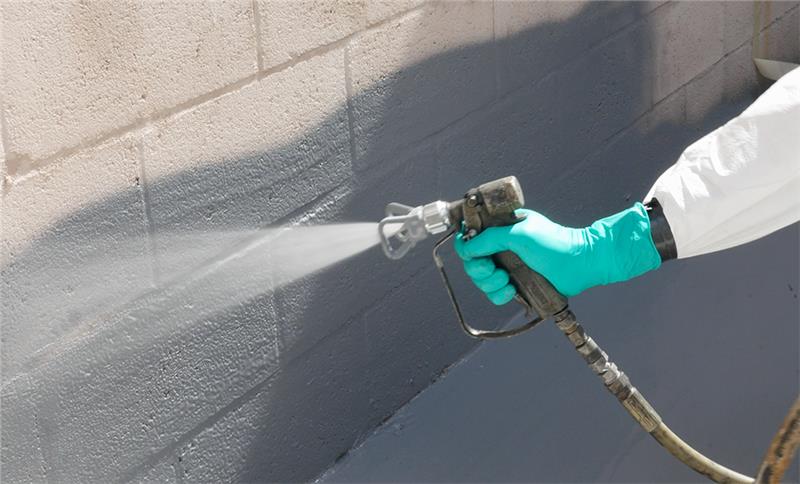
In this blog, we’ll walk you through the steps for properly mixing and applying Belzona 5815 onto concrete secondary containment areas. Belzona 5815 is a solvent-free, flexible coating that can be applied using a brush, roller, or airless spray, depending on the size and type of application.
Step 1: Containment Area Surface Preparation
Thoroughly clean the concrete surface using a mechanical preparation method, such as grit blasting or grinding. This step removes contaminants and opens the pores of the concrete for optimal adhesion.
Step 2: Mix the Product
Open the Belzona 5815 Base and scrape the sides to reincorporate any settled material.
- Measure three parts of the Base and pour it into your mixing container.
- Measure one part of the Solidifier and add it to the same container.
- Mix thoroughly using a mechanical mixer until a uniform color and consistency is achieved. For smaller quantities, mixing paddles or spatulas can be used.
Step 3: Application
- Apply Belzona 5815 directly onto the prepared surface with a short-bristled brush, rubber squeegee, or lint-free NAP white woven roller.
- Suitable areas may be coated by spray using heated airless equipment. Use either a single airless pump or plural equipment capable of metering accurately and mixing the two components.
- Use a brush or roller on edges and vertical surfaces for precision and complete coverage.
Step 4: Apply the Second Coat
Once the first coat has firmed up (but not fully cured), apply a second coat following the same method to build up the required thickness and protection.
Step 5: Allow to Cure
Let the coating cure according to the product’s instructions before placing the area back into service.
Why Belzona 5815 Is a Smart Choice for Protecting Containment Areas
Properly protecting containment areas is essential for maintaining structural integrity and preventing environmental contamination. With leak prevention and control solutions like Belzona 5815, asset owners can safeguard concrete surfaces using a cost-effective, flexible coating system that’s easy to apply and built to last. Whether you’re dealing with aggressive chemicals or general industrial environments, Belzona is a reliable containment area maintenance product.
Contact Belzona to Learn More About Solutions for Containment Areas
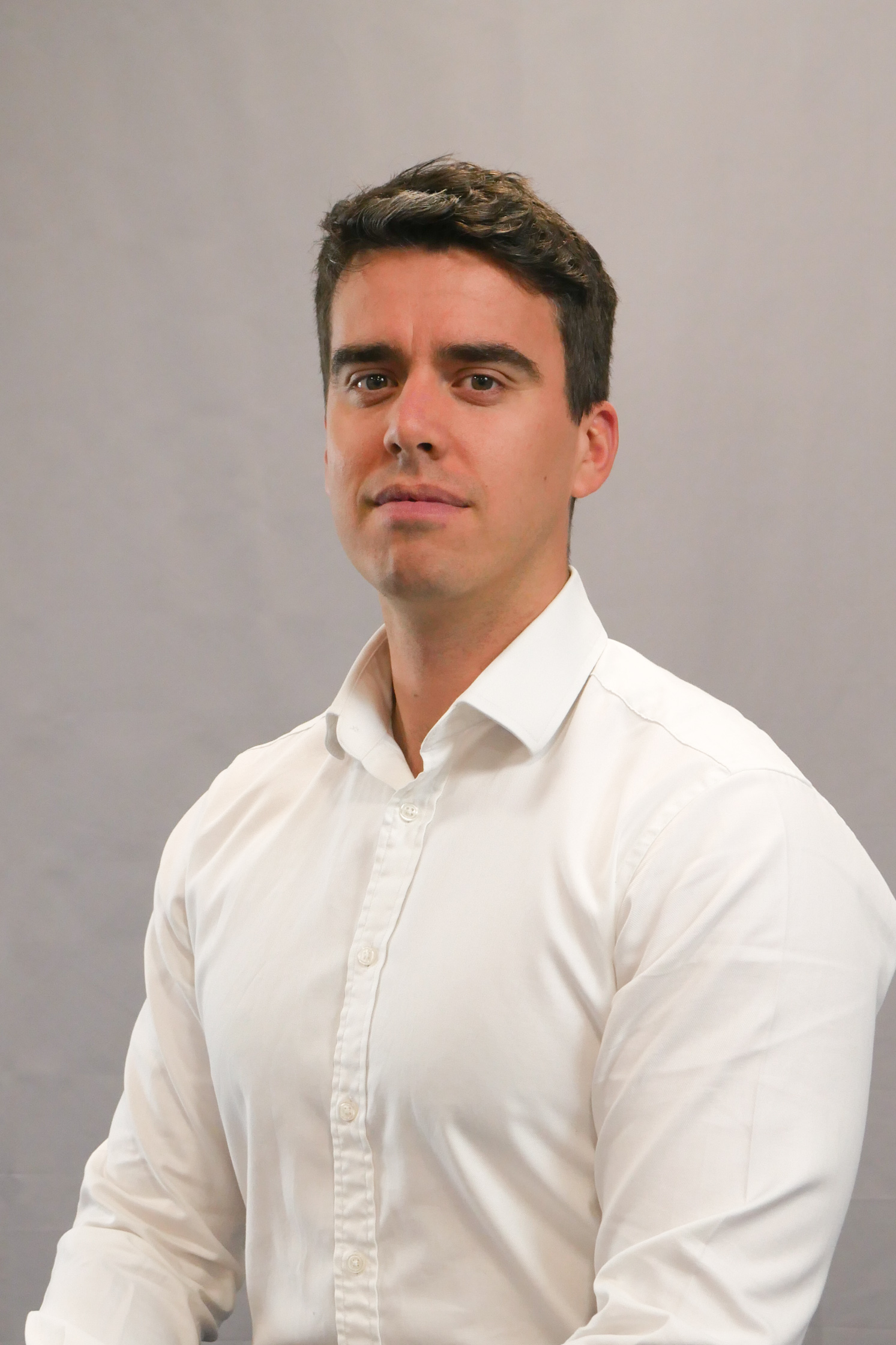
Richard Bywater is a Key Account Engineer at Belzona Ltd, one of the most established manufacturers of asset integrity solutions. With a Bachelor’s degree from the University of Leeds, Richard brings a unique blend of commercial insight and engineering expertise to his role.
His career at Belzona, beginning in 2018, has taken him around the globe, delivering talks, leading training seminars, and providing hands-on support to some of the world’s largest energy companies. His work focuses on implementing Belzona’s simple, safe, and effective solutions, ensuring optimal performance and longevity of critical assets. Over the years, Richard has been responsible for securing specifications for Belzona products with major energy suppliers, promoting a sustainable maintenance ethos within these companies.
Richard’s extensive travel and on-site experience have made him a highly sought-after expert in asset integrity, particularly in mitigating erosion and corrosion issues.